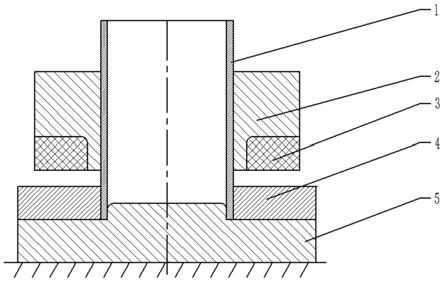
1.本发明属于金属板材与管材连接技术领域,具体涉及一种基于金属管材端部与板材径向挤压连接的方法及装置。
背景技术:
2.近些年来,随着轻量化板材管材的使用,板管连接在汽车方面得到了巨大的应用和发展。新的板材连接工艺需求逐渐增加,再传统的连接工艺中,焊接存在污染环境、不适应于异种材料的连接等问题;螺钉、螺栓连接存在需要增加辅助零件、连接过程需要辅助设备、成本较高等问题;胶接存在粘结接头易受环境影响强度降低等问题。
3.板管塑性连接不仅满足轻量化设计需求和异种材料的连接,同时易实现流水线自动化生产,而且也可以实现板材在管材任意部位进行的连接,但板管塑性连接工艺需要的连接力较大,同时对特定的挤压模具寿命有一定的损伤,而且连接接头的板材表面质量不好。
技术实现要素:
4.为了解决上述问题,本发明提供了一种基于金属管材端部与板材径向挤压连接的方法及装置,结构简单,满足轻量化设计需求,连接力小,制造成本低,易实现流水线自动化生产,不会造成环境污染。
5.本发明是通过以下技术方案来实现:
6.本发明公开了一种基于金属管材端部与板材径向挤压连接的方法,包括以下步骤:
7.s1:将待连接的管材1与板材4进行装配后整体放置在下模5上,下模5上设有圆柱凸台,管材1套在圆柱凸台上;上模2套在管材1上,上模2下端内侧设有环形的挤压凸起,挤压凸起外侧套有弹性套圈3;
8.s2:下模5固定不动,上模2以速度v1下行直至挤压凸起与板材4接触,上模2继续以速度v2下行挤压板材4,弹性套圈3受到上模挤压发生弹性变形,并对板材4产生压边作用,使板材4与弹性套圈3接触的部位不发生形变;板材4与管材1接触的孔口边缘的下部受到下模5上圆柱凸台的约束不产生变形,孔口边缘的上部受到局部挤压,产生向管材1径向的塑性变形,对管材1的局部施加径向压力从而产生向内的颈缩;当上模2下行至预设位置时停止,管材1与板材4的连接部位形成机械锁扣;
9.s3:上模2以速度v3上行回到初始位置,完成管材1与板材4的连接。
10.优选地,板材4和管材1的材质为碳钢、不锈钢或铝合金。
11.优选地,板材4的厚度为3~10mm,管材1的壁厚为0.5~3mm。
12.优选地,v1为0.5~3mm/s,v2为0.02~0.5mm/s,v3为0.1~1mm/s。
13.本发明公开了实现上述基于金属管材端部与板材径向挤压连接的方法的装置,包括上模2和下模5,上模2下端内侧设有环形的挤压凸起,挤压凸起外侧套设有弹性套圈3;下
模5上设有圆柱凸台,圆柱凸台的外径与待连接的管材1的内径匹配。
14.优选地,下模5上圆柱凸台的高度为待连接的板材4厚度的0.3~0.7倍。
15.优选地,下模5上圆柱凸台的边缘为圆角。
16.优选地,弹性套圈3为聚氨酯橡胶圈。
17.与现有技术相比,本发明具有以下有益的技术效果:
18.本发明公开的基于金属管材端部与板材径向挤压连接的方法,通过上模对板材的孔口边缘进行挤压,同时通过下模上的圆柱凸台进行约束,产生向管材径向流动的塑性变形,从而对管材的局部施加径向压力从而产生向内的颈缩,形成机械锁扣,实现二者的可靠连接。由于板材局部嵌入在颈缩的管材中,若要破坏必须使相邻部位也发生颈缩失稳,因此接头的抗拉脱强度高。该方法制造成本低,生产效率高。连接过程中对设备的要求不高,模具加工简单,连接过程便捷,生产效率高,易实现流水线生产。同时,整个连接过程在室温下进行,不需要加热,不会产生有害气体或粉尘,对环境友好;连接前后不会改变母材的性能,便于材料回收利用。
19.进一步地,板材和管材的材质为碳钢、不锈钢或铝合金,应用范围广。
20.进一步地,板材的厚度为3~10mm,管材的壁厚为0.5~3mm,该尺寸范围内板材与管材的连接通过挤压板材向径向方向形成的颈缩实现。合适的板材厚度即能保证足够的挤压变形空间,也不会对模具产生过大的磨损;合适的管材厚度能够保证其在板材塑性流动下发生失稳,形成可靠的连接,同时不发生破裂。
21.进一步地,v1为0.5~3mm/s,该速度为模具空行速度,较大的速度能够缩短运行时间,减小连接周期;v2为0.02~0.5mm/s,该速度为上模挤压凸起对板材进行挤压的速度,较小的速度并与连接过程中进行监控,预防缺陷的发生;v3为0.1~1mm/s,该速度为上模脱离板材时的速度,由于板材材料仍对模具有一定的挤压作用,当速度较大时,对模具的挤压凸起磨损较大,易损伤模具,过小的速度则增大连接时间。
22.本发明公开的实现上述利用管材塑性变形实现管材与板材连接方法的装置,结构简单,设计合理,安装便捷,与常规设备兼容性好,适合大批量生产。
23.进一步地,下模上圆柱凸台的高度为待连接的板材厚度的0.3~0.7倍,下模上圆柱凸台高度为保证管材套装上,并产生板材塑性变形时对板材局部产生约束作用。当高度较大时,则对板材竖直方向上的约束过多,导致模具对板材挤压的可行位移较小,形成的接头质量较差,当高度较小时,不能起到良好的约束作用。
24.进一步地,下模上圆柱凸台的边缘为圆角,能够避免挤压使对连接部位造成机械损伤。
25.进一步地,弹性套圈采用聚氨酯橡胶圈,强度和弹性性能高,回弹性好。
附图说明
26.图1为本发明板材与管材安装后的示意图;
27.图2为本发明上模挤压板材后的示意图;
28.图3为本发明上模向上运动去除挤压力的示意图;
29.图4为本发明完成板材与管材连接后的示意图。
30.图中:1为管材,2为上模,3为弹性套圈,4为板材,5为下模。
具体实施方式
31.下面结合附图和一个具体实施例对本发明做进一步的详细说明,所述是对本发明的解释而不是限定。
32.如图1,为实现本发明的一套具体装置,以此为例对本发明的基于金属管材端部与板材径向挤压连接的方法进行具体解释,不构成对本发明的限定,本发明的方法能够利用任何能够实现其分步功能的现有装置来实现。
33.待连接的板材4和管材1的材质为碳钢、不锈钢或铝合金。
34.该装置包括包括上模2和下模5,其特征在于,上模2下端内侧设有环形的挤压凸起,挤压凸起外侧套设有弹性套圈3;下模5上设有圆柱凸台,圆柱凸台的外径与待连接的管材1的内径匹配。
35.在本发明的一个较优的实施例中,下模5上圆柱凸台的高度为待连接的板材4厚度的0.3~0.7倍。
36.在本发明的一个较优的实施例中,下模5上圆柱凸台的边缘为圆角。
37.在本发明的一个较优的实施例中,弹性套圈3采用聚氨酯橡胶圈。
38.本发明的具体步骤为:
39.s1:在板材4上加工与管材1装配的通孔,如图1,将待连接的管材1与板材4进行装配后整体放置在下模5上,下模5上设有圆柱凸台,管材1套在圆柱凸台上;上模2套在管材1上,上模2下端内侧设有环形的挤压凸起,挤压凸起外侧套有弹性套圈3;
40.s2:如图2,下模5固定不动,上模2以速度v1下行直至挤压凸起与板材4接触,上模2继续以速度v2下行挤压板材4,弹性套圈3受到上模挤压发生弹性变形,并对板材4产生压边作用,使板材4与弹性套圈3接触的部位不发生形变;板材4与管材1接触的孔口边缘的下部受到下模5上圆柱凸台的约束不产生变形,孔口边缘的上部受到局部挤压,产生向管材1径向的塑性变形,对管材1的局部施加径向压力从而产生向内的颈缩;当上模2下行至预设位置时停止,管材1与板材4的连接部位形成机械锁扣;
41.s3:如图3,上模2以速度v3上行回到初始位置,完成管材1与板材4的连接,如图4。
42.在本发明的一个较优的实施例中,板材4的厚度为3~10mm,管材1的壁厚为0.5~3mm。
43.在本发明的一个较优的实施例中,v1为0.5~3mm/s,v2为0.02~0.5mm/s,v3为0.1~1mm/s。
44.下面以一个具体实施例来对本发明进行进一步地解释说明:
45.根据待连接管材1外径对厚度为5mm的板材4进行加工通孔,并将壁厚为1mm的管材1与板材4装配在一起,然后放置在下模5上直径为25mm的圆柱凸台上,下模5固定不动,聚氨酯橡胶材质的弹性套圈3安装在上模2下方的挤压凸起外侧,上模2套装在管材1外部。
46.上模2以速度v1=1.0mm/s向下运动,挤压板材4,板材4材料发生塑性流动,由于下模5上圆柱凸台的约束,受挤压材料向管材1径向发生颈缩,随着上模2以速度v2=0.2mm/s不断向下运动,颈缩逐渐增大,形成板材4与管材1塑性连接接头。
47.上模2运动到预定位置后,以速度v3=0.8mm/s向上运动,与板材4分离,并取出连接完成后板材4与管材1,完成板管塑性连接过程。
48.需要注意的是,本发明不限于上述实施方式,本领域技术人员所做出的对上述实
施方式任何显而易见的改进或变更,都不会超出本发明的构思和所附权利要求的保护范围。