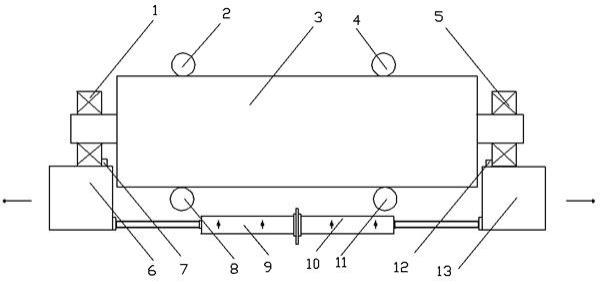
1.本实用新型涉及一种提高轧辊轴承箱装配精度的装置,属于工程设备领域。
背景技术:
2.轧制作业作为轧钢的一道主要工序,不仅要求操作人员的高技术水平,同时对辊系精度、辊系配比要求极高,这就要求轧辊轴承箱也必须满足高精度、高质量的装配要求,然而现实作业中,对于轧制宽度2100mm的宽幅轧机,其轧辊直径达到1250mm,单个轴承箱尺寸达到1500mm
×
1300mm
×
800mm,重量接近15吨,装配精度0.25mm—0.32mm的超高要求,面对如此体积大、质量重的轴承箱,一直以来仅仅依靠天车将导链吊起,导链钩挂轴承箱这种简单的装配方法,完全无法满足精度要求二三十道的技术要求,造成轴承箱在拆装过程中装配精度极低,轴承损坏率高,同时费事费力,还存在一定的安全隐患。
3.这种操作方法存在以下几个方面的弊端:1、装配精度低,误差大,由于需要天车配合装配,天车无法精准控制轴承箱二三十道的装配精度;2、轴承箱装配受力不均匀,由于轴承箱装配需要至少3—4人配合作业,装配过程中每个人的用力不同,造成轴承箱装配过程中受力不均匀;3、存在一定的安全隐患,轴承箱是利用天车钩挂导链的方式进行作业,每个轴承箱重量约15t左右,有时由于作业空间受限等其它原因存在一定的斜拉斜吊作业,安全危险性较高。
技术实现要素:
4.本实用新型提供一种提高轧辊轴承箱装配精度的装置,通过该装置对轴承箱定位拆装,使其满足拆卸或装配过程受力均匀,装配作业精度高的技术要求,同时减少人机接触,缩短作业时间,消除作业安全隐患。
5.本实用新型提供了一种提高轧辊轴承箱装配精度的装置,由四组托辊、两件拆装平台及左、右侧抱爪组成;拆装平台是长方体结构, 在拆装平台的台面上放置轴承箱;四组托辊分别位于轧辊的上、下、左、右位置,第一托辊位于轧辊上方左中部,第二托辊位于轧辊上方右中部,第三托辊位于轧辊下方左中部,第四托辊位于轧辊下方右中部;托辊可转动,分别分布在轧辊两侧,用于固定轧辊及轴承箱工位。在两个拆装平台上分别设置抱爪,抱爪最大外形尺寸为80
×
80
×
50mm,抱爪由拔块和抱爪销组成,用于抱住轴承箱外体,将轴承箱与轧辊分离或装配。
6.进一步地,所述四组托辊的尺寸为¢500
×
570mm。
7.进一步地,托辊是通过辊架平台固定的,辊架平台尺寸为3000mm
×
1500mm
×
500mm,然后在辊架平台上安装四组轴承座,轴承座内部含有轴承,轴承型号为6238,转动方式为自由旋转。
8.进一步地,拆装平台的移动可以是电动、液压或手动方式实现,优选地,拆装平台的移动是液压方式,由两个油缸分别驱动两个拆装平台实现。
9.所述拆装平台为长方体结构,其尺寸为1710
×
1350
×
560mm,该平台可实现位置移
动,用于拆装移动轴承箱。
10.本实用新型用于在拆、装轴承箱时,将轧辊放置在固定工位的托辊组上,经托辊组的转动和两侧拆装平台的升降、横移和纵向运动,进行拆、装轴承箱的作业。
11.本实用新型提供的提高轧辊轴承箱装配精度的装置,带来的有益效果:
12.(1)提高轧辊轴承箱装配精度,提高轴承利用率,轴承箱装配精度达到二三十道的技术要求;拆卸或装配轴承箱过程受力均匀;
13.(2)避免了原来斜拉斜吊的不安全作业方式,降低了维护成本,缩短了作业时间,减少了人机接触,消除了作业过程安全隐患。
14.下面结合附图和实施例对本实用新型做进一步说明。
附图说明
15.图1为轴承箱拆卸过程示意图。
16.图2为轴承箱装配过程示意图。
17.图3为抱爪的结构示意图。
18.图4为托辊与辊架平台的连接示意图。
19.图中:1—左轴承箱,2—第一托辊,3—轧辊,4—第二托辊,5—右轴承箱,6—左拆装平台,7—左侧抱爪,8—第三托辊,9—第一油缸,10—第二油缸,11—第四托辊,12—右侧抱爪,13—右拆装平台,14—拔块,15—抱爪销。
具体实施方式
20.实施例:
21.如图1和2所示,一种提高轧辊轴承箱装配精度的装置,由四组托辊、两件拆装平台及左、右侧抱爪组成;拆装平台是长方体结构, 在拆装平台的台面上放置轴承箱;四组托辊分别位于轧辊的上、下、左、右位置,第一托辊2位于轧辊3上方左中部,第二托辊4位于轧辊3上方右中部,第三托辊8位于轧辊3下方左中部,第四托辊11位于轧辊3下方右中部;托辊可转动,分别分布在轧辊3两侧,用于固定轧辊及轴承箱工位。在左拆装平台6和右拆装平台13上分别设置左侧抱爪7和右侧抱爪12,抱爪最大外形尺寸为80
×
80
×
50mm,抱爪由拔块14和抱爪销15组成(如图3所示),用于抱住轴承箱外体,将轴承箱与轧辊分离或装配。
22.托辊是通过辊架平台固定的,辊架平台尺寸为3000mm
×
1500mm
×
500mm,在辊架平台上设有四组轴承座,轴承座内部含有轴承,轴承型号为6238,转动方式为自由旋转。如图4所示。
23.所述四组托辊的尺寸:托辊尺寸为¢500
×
570mm。
24.所述拆装平台的移动采用液压方式,由两个油缸分别驱动两个拆装平台实现。所述拆装平台为长方体结构,其尺寸为1710
×
1350
×
560mm,该平台可实现位置移动,用于拆装移动轴承箱。
25.具体的使用方法如下:
26.如图1所示,轴承箱拆卸方法如下:
⑴
用天车将所要拆的轧辊3放置在托辊组上,即放置在第一托辊、第二托辊4、第三托辊8、第四托辊11的中间;
⑵
左拆装平台6和右拆装平台13分别运行到左轴承箱1、右轴承箱5下方,拆装平台升起,两个轴承箱底部与拆装平台6、13
接触后停止,
⑶
拆装平台上的左侧抱爪7、右侧抱爪12分别扣住左轴承箱1、右轴承箱5后,按图示箭头方向横向移动,使左轴承箱1、右轴承箱5脱离轧辊3。
27.如图2所示,轴承箱装配方法如下:
⑴
用天车将所要装配的轧辊3放置在托辊组上,即放置在第一托辊2、第二托辊4、第三托辊8、第四托辊11的中间;
⑵
左轴承箱1、右轴承箱5分别放置在左拆装平台6和右拆装平台13的台面上,通过两侧拆装平台的升降、横移,完成与轧辊3的中心线对中,
⑶
拆装平台上的左侧抱爪7、右侧抱爪12分别扣住左轴承箱1、右轴承箱5后,按图示箭头方向横向移动,实现左轴承箱1、右轴承箱5与轧辊3的装配。
28.在太钢冷轧10#轧机1250轧辊轴承箱拆卸装配上试用了本技术方案,轧辊直径¢1250mm,轧辊轴颈¢780mm,公差范围+0.25mm—+0.33mm,轴承箱尺寸1500mm
×
1300mm
×
800mm,重量接近15吨,四列轴承型号r540088+ l540088,轴承内套采购成本25万元/盘。选用了该轴承箱精度控制装置后,轴承箱与轧辊装配精度由以前的大于0.5mm优化为满足+0.25mm—+0.33mm公差范围,轴承损耗由平均10—12盘/年降低到2—3盘/年,成本降低了225万元,轴承箱拆装时间由原来的5—6h/个降低为1—2h/个,人机接触时间由原来5—6h/个降低为0.5h/个以内。
29.采用本实用新型提供的精度控制装置,达到了以下效果:轴承箱装配精度达到二三十道的技术要求;拆卸或装配轴承箱过程受力均匀;避免了原来斜拉斜吊的不安全作业方式,减少了人机接触,消除了安全隐患;缩短了作业时间;提高了轴承利用率,降低了维护成本。