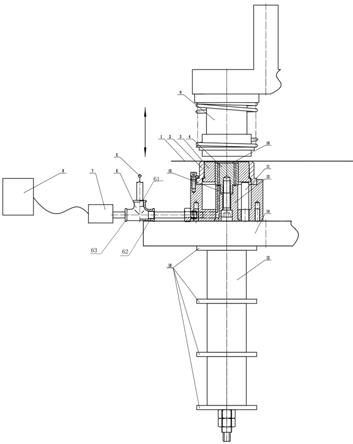
1.本实用新型属于铝板拉伸设备技术领域,具体地说涉及一种铝板冲压拉伸模具碎片自动检测装置。
背景技术:
2.在包装制盖领域,铝质瓶盖是通过模具对铝板的冲压成型生产的。铝板在冲压拉伸过程中,由于受铝板材质、拉伸油、温度以及模具质量等因素影响,在冲压时会出现铝片拉伸破损现象。由于不能及时发现停车,非正常冲压导致破损铝片塞模、损伤模具,既延长了模具维护时间,又影响冲压生产效率。
技术实现要素:
3.本实用新型提供了一种铝板冲压拉伸模具碎片自动检测装置,解决了背景技术中的冲压模具不能及时发现铝片拉伸破损停车,非正常冲压导致破损铝片塞模、损伤模具的缺点。
4.本实用新型的技术方案是这样实现的:一种铝板冲压拉伸模具碎片自动检测装置,包括固定在模具冲床主轴上的上冲头,所述上冲头下方设有下模板,所述下模板下方设有胶皮柱,所述胶皮柱上设有多个压力盘,所述下模板上设有下模,所述下模包括芯座,所述芯座内设有凸模,所述凸模外侧设有压料环,所述压料环外侧设有凹模,所述压料环下方设有顶杆,所述顶杆下部与下模板相连接,铝板位于上冲头下方的下模上,所述凸模上设有气道,所述气道上端通达凸模端面,所述气道下端穿过芯座与三通接头的接头二相通,所述三通接头的接头一上设有单向阀,所述三通接头的接头三与压力传感器相连接,所述压力传感器与控制系统相连接,所述压料环、凸模和铝板冲压后的圆形铝片三者之间形成气体预留空间,所述气体预留空间与气道相连通。
5.本实用新型的有益效果是:本实用新型铝板冲压拉伸模具碎片自动检测装置,根据冲压模具结构及工艺,利用压料环、凸模和铝板在拉伸过程中所形成的气体预留空间的空气压力变化作为检测信号,实现铝板在冲压过程中破碎的自动检测,自动化程度高,检测稳定可靠。通过对冲压铝板碎片进行自动检测,可自动实现铝板碎片及时停车,大大节省生产维护成本,提高生产效率。
附图说明
6.图1为本实用新型的结构示意图。
7.零件说明:1、铝板,2、凹模,3、压料环,4、凸模,5、单向阀,6、三通接头,61、接头一,62、接头二,63、接头三,7、压力传感器,8、控制系统,9、上冲头,10、气体预留空间,11、顶杆,12、胶皮柱,13、芯座,14、下模板,15、气道,16、压力盘。
具体实施方式
8.下面将结合本实用新型实施例中的附图,对本实用新型实施例中的技术方案进行清楚、完整地描述,显然,所描述的实施例仅仅是本实用新型一部分实施例,而不是全部的实施例。
9.在本实用新型的描述中,需要理解的是,术语“上”、“下”、“前”、“后”、“左”、“右”、“顶”、“底”、“内”、“外”等指示的方位或位置关系为基于附图所示的方位或位置关系,仅是为了便于描述本实用新型和简化描述,而不是指示或暗示所指的装置或元件必须具有特定的方位、以特定的方位构造和操作,因此不能理解为对本实用新型的限制。
10.参照附图1,一种铝板冲压拉伸模具碎片自动检测装置,包括固定在模具冲床主轴上的上冲头9,上冲头9下方设有下模板14,下模板14下方设有胶皮柱12,胶皮柱12与下模板14之间设有1个压力盘16,胶皮柱12下部均匀设有3个压力盘16,下模板14上设有下模,所述下模包括芯座13,芯座13内设有凸模4,凸模4外侧设有压料环3,所述压料环3外侧设有凹模2,压料环3可在凹模2内上下移动,压料环3下方设有顶杆11,顶杆11可顶压压力盘16,压力盘16挤压胶皮柱12。压力盘16使顶杆11顶力均衡作用于胶皮柱12上。
11.铝板1位于上冲头9下方的下模上,凸模4上设有气道15,所述气道15上端通达凸模4端面,气道15下端穿过芯座13与三通接头6的接头二62相通,三通接头6的接头一61上设有单向阀5,单向阀5只能从外面进入空气,不能排出空气,三通接头6的接头三63与压力传感器7相连接,压力传感器7与控制系统8相连接,控制系统8带动上冲头9做上下往复运动。压料环3、凸模4和铝板冲压后的圆形铝片三者之间形成气体预留空间10,气体预留空间10与气道15相连。
12.具体地,当铝板1板材经过控制系统输送到由凸模4、凹模2、压料环3等组成的下模表面时,上冲头9向下运动,与凹模2共同环切铝板1,冲切成凹模2直径面积大小的圆形铝片,上冲头9随着冲床继续向下运动,压着冲切成的圆形铝片,铝片压着压料环3向下进行拉伸成型,同时,由铝片、压料环3、凸模4等组成的气体预留空间10里的空气,在铝片拉伸过程中被压缩,进入气道15,连通三通接头6,压力传感器7检测到压缩空气的压力信号,冲压正常情况下,在冲床驱动下,上冲头9每次冲切拉伸形成的压缩空气,经过气道15,由压力传感器7采集到正常压力,由压力传感器输出一信号给控制系统8,控制系统8控制冲床进行正常冲压拉伸。由于板材质量等方面原因,圆形铝片在环切拉伸过程中若出现破损,由铝片、压料环3、凸模4等组成的气体预留空间10里的空气,在拉伸过程中被泄放掉,无法被压缩进入气道15,压力传感器7因检测不到正常压力信号,输出另一信号给控制系统8,控制系统8控制冲床及时自动停止冲压拉伸。
13.以上所述,仅为本实用新型较佳的具体实施方式,但本实用新型的保护范围并不局限于此,任何熟悉本技术领域的技术人员在本实用新型揭露的技术范围内,根据本实用新型的技术方案及其实用新型构思加以等同替换或改变,都应涵盖在本实用新型的保护范围之内。
技术特征:
1.一种铝板冲压拉伸模具碎片自动检测装置,包括固定在模具冲床主轴上的上冲头(9),所述上冲头(9)下方设有下模板(14),所述下模板(14)下方设有胶皮柱(12),所述胶皮柱(12)上设有多个压力盘(16),所述下模板(14)上设有下模,所述下模包括芯座(13),所述芯座(13)内设有凸模(4),所述凸模(4)外侧设有压料环(3),所述压料环(3)外侧设有凹模(2),所述压料环(3)下方设有顶杆(11),所述顶杆(11)下部与下模板(14)相连接,铝板(1)位于上冲头(9)下方的下模上,其特征在于所述凸模(4)上设有气道(15),所述气道(15)上端通达凸模(4)端面,所述气道(15)下端穿过芯座(13)与三通接头(6)的接头二(62)相通,所述三通接头(6)的接头一(61)上设有单向阀(5),所述三通接头(6)的接头三(63)与压力传感器(7)相连接,所述压力传感器(7)与控制系统(8)相连接,所述压料环(3)、凸模(4)和铝板冲压后的圆形铝片三者之间形成气体预留空间(10),所述气体预留空间(10)与气道(15)相连通。
技术总结
本实用新型提供了一种铝板冲压拉伸模具碎片自动检测装置,包括固定在模具冲床主轴上的上冲头,所述上冲头下方设有下模板,所述下模板上设有下模,所述下模包括芯座,所述芯座内设有凸模,所述凸模上设有气道,所述气道下端穿过芯座与三通接头的接头二相通,所述三通接头的接头一上设有单向阀,所述三通接头的接头三与压力传感器相连接,所述压力传感器与控制系统相连接,所述压料环、凸模和铝板冲压后的圆形铝片三者之间形成气体预留空间。本实用新型利用压料环、凸模和铝板在拉伸过程中所形成的气体预留空间的空气压力变化作为检测信号,实现铝板在冲压过程中破碎的自动检测,自动化程度高,检测稳定可靠,大大节省生产维护成本,提高生产效率。提高生产效率。提高生产效率。
技术研发人员:刘久平 苏允涛 李波 都业成 曲鲁宁
受保护的技术使用者:山东中锐产业发展股份有限公司
技术研发日:2021.09.24
技术公布日:2022/2/11