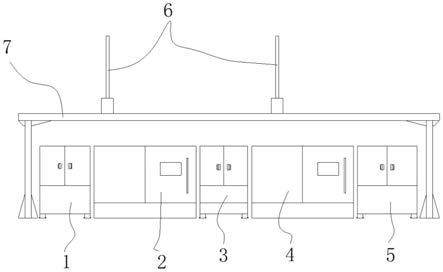
1.本发明涉及一种模块组合生产工艺,尤其涉及一种实轴制造自动化的模块组合生产工艺。
背景技术:
2.在现有的加工技术中一般是采用人工对通过数控车床加工后的实轴产品进行机械式的测量来判定尺寸精度,从而挑选出正品和次品,属于事后控制模式,存在批量不良风险。在大批量的生产实际中,人工测量存在:工作量大、劳动强度高、遗漏测量、测量失误等问题。并且,由于实轴产品对尺寸精度要求高,如果测量人员手法不当或检测操作不当,就无法做到准确的检测出产品是否真实地达到所要求的尺寸规范,因此,也就无法保证每一根实轴的检测结果可靠性,导致始终无法规避不良品流出的风险。
技术实现要素:
3.本发明主要是解决现有技术中存在的不足,提供一种结构紧凑,以解决传统实轴先制造后检测的批量质量风险,并避免人工手动检测精度不高、检测效率低下等问题的一种实轴制造自动化的模块组合生产工艺。
4.本发明的上述技术问题主要是通过下述技术方案得以解决的:
5.一种实轴制造自动化的模块组合生产工艺,按以下步骤进行:
6.(一)、结构组成:
7.从左至右依次设有上料仓、数控车床ⅰ、视觉检测系统、数控车床ⅱ和下料输送线,待加工产品通过机械手进行抓取位移,机械手通过桁架进行滑动;
8.(二)、上料仓操作:
9.将待加工实轴产品放入上料仓的储料仓中,上料仓通过自动抬升定位装置将储料仓中的产品一根一根举升至检具定位台,当传感器感应到产品已进入定位台并正确定位以后,产品总长度测笔及中心孔检具启动,对产品总长度和两端面中心孔尺寸进行自动检测和合格判定;
10.(三)、机械手操作:
11.机械手末端分别安装有2个夹爪能一次性分别抓取2根实轴产品,并且该末端手爪机构安装有旋转气缸可以180
°
旋转,可对实轴产品进行方向旋转调整操作;
12.上料仓完成上料及产品总长度和两端面中心孔检测以后,通知机械手移动至上料仓上方,将检测结果不合格的产品分选抓取至指定的不合格品放置区;检测结果合格的产品抓取并送料至数控车床ⅰ设备上方待加工;
13.(四)、数控车床ⅰ操作:
14.数控车床ⅰ天窗自动打开,机械手将待加工产品送料至数控车床ⅰ的拔料器上;拔料器设置有可上下伸缩调节和轴向前后调节的v型支架,并且v型支架与产品接触的部位有滚杆支撑,防止拔料时造成磕碰划伤产品表面;
15.数控车床ⅰ尾座顶尖启动将v型支架及上面的产品推入数控车床ⅰ夹头套中并顶紧产品,安装在数控车床ⅰ刀盘上的长度位置检测探头启动检测出产品端面位置,并自动计算和补偿因产品总长度公差导致的车加工基准起点位置偏移问题,确保批量加工的每一支产品轴向位置尺寸的一致性;
16.数控车床ⅰ启动车削并完成加工后,拔料器自动启动将产品从数控车床ⅰ夹头套中取出放置在v型支架上并后退返回至送料位置;数控车床ⅰ天窗自动打开,机械手进行换料操作,取出已加工产品,送入待加工产品;
17.机械手完成换料操作后移出数控车床ⅰ,并且数控车床ⅰ天窗自动关闭启动下一支产品的车削加工循环;
18.(五)、视觉检测系统操作:
19.机械手将数控车床ⅰ加工完成的产品放置在视觉检测系统上进行进行外观检测,外观检测完成以后:合格的产品通知机械手自动抓取并换向后移动至数控车床ⅱ设备上方;如果检测不合格,机械手自动将不合格的产品放入待检区,并声光报警提示操作员进行人工确认处理,人工确认处理完成后放回原位,按下确认按钮,机械手启动并抓取产品再次放入视觉检测系统进行外观检测,合格后通知机械手自动抓取并换向后移动至数控车床ⅱ设备上方;
20.(六)、数控车床操作:
21.数控车床ⅱ天窗自动打开,机械手将待加工产品送料至数控车床ⅱ的拔料器上,拔料器设置有可上下伸缩调节和轴向前后调节的v型支架,并且v型支架与产品接触的部位有滚杆支撑,防止拔料时造成磕碰划伤;
22.数控车床ⅱ尾座顶尖启动将v型支架及上面的产品推入数控车床ⅱ夹头套中并顶紧产品,安装在数控车床ⅱ刀盘上的长度位置检测探头启动检测出产品端面位置,并自动计算和补偿因产品总长度公差导致的车加工基准起点位置偏移问题,确保批量加工的每一支产品轴向位置尺寸的一致性;
23.数控车床ⅱ启动车削并完成加工后,拔料器自动启动将产品从数控车床ⅱ夹头套中取出放置在v型支架上并后退返回至送料位置,数控车床ⅱ天窗自动打开,机械手进行换料操作,取出已加工产品,送入待加工产品;
24.机械手完成换料操作后移出数控车床ⅱ,并且数控车床ⅱ天窗自动关闭启动下一支产品的车削加工循环;
25.(七)、下料输送线操作:
26.机械手将数控车床ⅱ加工完成的产品抓取并通过吹气装置,对产品表面进行负压清洁后放置在下料输送线的检测定位台上;
27.下料输送线的检测系统对产品进行检测,合格的产品由机械手抓取并放置在下料输送线的成品输送线上;
28.检测不合格的产品,由机械手抓取放置于不合格区,并声光报警提示操作员进行人工确认处理;
29.下料输送线的检测系统具有对总数、合格品数、返修品数、废品数相关进行计数功能;检测系统预留与mes系统数据接口,并可以实现依据spc过程控制理论,提供xbarr控制图绘制及cp、cpk、pp、ppk、cmk相关一系列过程能力控制参数,对加工过程进行长期或短期
能力指数的监控。
30.作为优选,步骤(二)中,储料仓一次可存储80支产品,储料仓宽度可通过手轮两边调节,调节范围340-800mm,可满足不同的实轴产品长度需求;
31.定位台采用v型机构校正产品位置,确保检测定位准确及机械手抓取方便。
32.本模块组合生产工艺,可通过两组正反手(镜向)车床连线组合布置,实现1个工人轻松控制2条连线设备进行实轴总长度检测+两端面工艺中心孔检测+精车加工一端外表面+精车加工另一端外表面+100%遏制尺寸检测过程的自动生产,比传统的单功能、集群式机床布局方式减少3个工人。
33.本模块根据智能制造的需求,配置自动上料、识别、装夹、加工、自动检测、分拣、诊断、报警、保护、通信和呼叫等功能,真正实现了高精度实轴车削加工自动化和实时高效在线检测的全闭环控制。
34.本发明提供的一种实轴制造自动化的模块组合生产工艺,进一步提升产品质量,提高检测速度。
附图说明
35.图1是本发明的结构示意图。
具体实施方式
36.下面通过实施例,结构附图,对本发明的技术方案作进一步具体的说明。
37.实施例1:如图所示,一种实轴制造自动化的模块组合生产工艺,按以下步骤进行:
38.(一)、结构组成:
39.从左至右依次设有上料仓1、数控车床ⅰ2、视觉检测系统3、数控车床ⅱ4和下料输送线5,待加工产品通过机械手6进行抓取位移,机械手6通过桁架7进行滑动;
40.(二)、上料仓操作:
41.将待加工实轴产品放入上料仓的储料仓中,上料仓通过自动抬升定位装置将储料仓中的产品一根一根举升至检具定位台,当传感器感应到产品已进入定位台并正确定位以后,产品总长度测笔及中心孔检具启动,对产品总长度和两端面中心孔尺寸进行自动检测和合格判定;
42.(三)、机械手操作:
43.机械手末端分别安装有2个夹爪能一次性分别抓取2根实轴产品,并且该末端手爪机构安装有旋转气缸可以180
°
旋转,可对实轴产品进行方向旋转调整操作;
44.上料仓完成上料及产品总长度和两端面中心孔检测以后,通知机械手移动至上料仓上方,将检测结果不合格的产品分选抓取至指定的不合格品放置区;检测结果合格的产品抓取并送料至数控车床ⅰ设备上方待加工;
45.(四)、数控车床ⅰ操作:
46.数控车床ⅰ天窗自动打开,机械手将待加工产品送料至数控车床ⅰ的拔料器上;拔料器设置有可上下伸缩调节和轴向前后调节的v型支架,并且v型支架与产品接触的部位有滚杆支撑,防止拔料时造成磕碰划伤产品表面;
47.数控车床ⅰ尾座顶尖启动将v型支架及上面的产品推入数控车床ⅰ夹头套中并顶紧
产品,安装在数控车床ⅰ刀盘上的长度位置检测探头启动检测出产品端面位置,并自动计算和补偿因产品总长度公差导致的车加工基准起点位置偏移问题,确保批量加工的每一支产品轴向位置尺寸的一致性;
48.数控车床ⅰ启动车削并完成加工后,拔料器自动启动将产品从数控车床ⅰ夹头套中取出放置在v型支架上并后退返回至送料位置;数控车床ⅰ天窗自动打开,机械手进行换料操作,取出已加工产品,送入待加工产品;
49.机械手完成换料操作后移出数控车床ⅰ,并且数控车床ⅰ天窗自动关闭启动下一支产品的车削加工循环;
50.(五)、视觉检测系统操作:
51.机械手将数控车床ⅰ加工完成的产品放置在视觉检测系统上进行进行外观检测,外观检测完成以后:合格的产品通知机械手自动抓取并换向后移动至数控车床ⅱ设备上方;如果检测不合格,机械手自动将不合格的产品放入待检区,并声光报警提示操作员进行人工确认处理,人工确认处理完成后放回原位,按下确认按钮,机械手启动并抓取产品再次放入视觉检测系统进行外观检测,合格后通知机械手自动抓取并换向后移动至数控车床ⅱ设备上方;
52.(六)、数控车床操作:
53.数控车床ⅱ天窗自动打开,机械手将待加工产品送料至数控车床ⅱ的拔料器上,拔料器设置有可上下伸缩调节和轴向前后调节的v型支架,并且v型支架与产品接触的部位有滚杆支撑,防止拔料时造成磕碰划伤;
54.数控车床ⅱ尾座顶尖启动将v型支架及上面的产品推入数控车床ⅱ夹头套中并顶紧产品,安装在数控车床ⅱ刀盘上的长度位置检测探头启动检测出产品端面位置,并自动计算和补偿因产品总长度公差导致的车加工基准起点位置偏移问题,确保批量加工的每一支产品轴向位置尺寸的一致性;
55.数控车床ⅱ启动车削并完成加工后,拔料器自动启动将产品从数控车床ⅱ夹头套中取出放置在v型支架上并后退返回至送料位置,数控车床ⅱ天窗自动打开,机械手进行换料操作,取出已加工产品,送入待加工产品;
56.机械手完成换料操作后移出数控车床ⅱ,并且数控车床ⅱ天窗自动关闭启动下一支产品的车削加工循环;
57.(七)、下料输送线操作:
58.机械手将数控车床ⅱ加工完成的产品抓取并通过吹气装置,对产品表面进行负压清洁后放置在下料输送线的检测定位台上;
59.下料输送线的检测系统对产品进行检测,合格的产品由机械手抓取并放置在下料输送线的成品输送线上;
60.检测不合格的产品,由机械手抓取放置于不合格区,并声光报警提示操作员进行人工确认处理;
61.下料输送线的检测系统具有对总数、合格品数、返修品数、废品数相关进行计数功能;检测系统预留与mes系统数据接口,并可以实现依据spc过程控制理论,提供xbarr控制图绘制及cp、cpk、pp、ppk、cmk相关一系列过程能力控制参数,对加工过程进行长期或短期能力指数的监控。
62.步骤(二)中,储料仓一次可存储80支产品,储料仓宽度可通过手轮两边调节,调节范围340-800mm,可满足不同的实轴产品长度需求;
63.定位台采用v型机构校正产品位置,确保检测定位准确及机械手抓取方便。