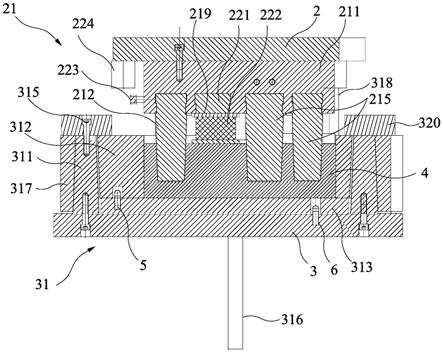
1.本发明金属材料塑性加工及成形技术领域,尤其是指一种大投影面积的异形箱体挤压成形方法。
背景技术:
2.随着工业时代的不断发展,具有轻量化、一体化、复杂化的异形箱体逐渐成为特种装备、大型复杂构件的首选。箱体,这种构件具有结构复杂、尺寸较大等特征,该类构件的成形难点之一是在于异形箱体内部型腔较多,且体积大小不一,型腔壁壁厚不均匀,较大的型腔面积导致在现有的实验条件下无法一次挤压成形,其中以成形载荷太大最为主要。传统的大尺寸(单边长度超过600mm且投影面积较大)箱体类零件结构复杂多样且制造方式多数为铸造+切削加工,铸造存在着铸件组织不致密、缩孔和气泡以及晶粒粗细不均匀等,机械加工生产效率低、原材料浪费严重并且耗时耗力;因此,该类构件的成形难点之二是在异形箱体挤压成形的过程中,如何精确的控制金属的流动方向,从而提高材料的利用率。这些方法存在的不足之处难以满足此零件服役要求。
技术实现要素:
3.本发明的目的在于提供一种大投影面积的异形箱体挤压成形方法,有效克服现有传统箱体结构加工制造所带来的问题,改善合金的成形性,提高成形件的综合力学性能,大大提高材料利用率和生产效率,节能减排。
4.为达成上述目的,本发明的解决方案为:一种大投影面积的异形箱体挤压成形方法,包括以下步骤:
5.(1)成形前准备:预热模具,该模具包括与压力机上工作台连接的上模板、拆卸安装于上模板的凸模组件、与压力机下工作台连接的下模板、拆卸安装在下模板上的凹模组件;凸模组件包括上垫板、左前凸模、左后凸模、右前凸模、右后凸模、中凸模、左前填充块、左后填充块、右前填充块、右后填充块、中填充块和橡胶块组;所述上模板下部连接所述上垫板,所述上垫板下部开设供所述左前凸模、左后凸模、右前凸模、右后凸模、中凸模连接的左前安装槽、左后安装槽、右前安装槽、右后安装槽、中安装槽;所述凹模组件包括内应力圈、分瓣式凹模、顶板、中间块、垫块、顶杆和外应力圈,所述内应力圈固定在下模板上,所述顶板、所述分瓣式凹模和中间块安装在内应力圈内部,且所述分瓣式凹模和中间块安装在所述顶板的上方,所述分瓣式凹模在凸模组件下方开设供坯料置入的内腔,所述橡胶块组下方的型腔内填装对应的所述垫块,内腔底部中间开有顶出孔,尺寸与顶杆相配合;所述外应力圈过盈配合套置在内应力圈的外部;
6.等预热完毕后,将分瓣式凹模、顶板及中间块放置到内应力圈内,然后将预热好的坯料放进内腔中,所述内应力圈上部的四周设置压板,压板伸入分瓣式凹模上方,压板的下表面与所述分瓣式凹模的上表面、外应力圈的上表面相抵接;在上垫板中安装预热好的左前凸模、右后凸模;在安装预热模具的过程中分别在分瓣式凹模和各个凸模的表面均匀的
涂抹水基石墨润滑剂;
7.(2)第一道次成形过程:在左前安装槽和右后安装槽以外的安装槽配合嵌入填充块、并在填充块下方堆叠橡胶块组;压力机开始带动左前凸模、右后凸模向下运动,坯料在凸模的作用下,先充满整个凹模内腔,与此同时,在坯料上成形出左前型腔和右后型腔,直到左前凸模、右后凸模下压到留有底厚,停止左前凸模和右后凸模的运动,然后左前凸模和右后凸模开始向上运动,脱离坯料;
8.(3)第二道次成形过程:移除第一道次成形的橡胶块组,取下挤压完毕的左前凸模、右后凸模,在刚刚成形的左前型腔、右后型腔内放置对应的加热好的垫块,在每个垫块上堆叠橡胶块组,橡胶块组上方的左前安装槽配合嵌入左前填充块、右后安装槽配合嵌入右后填充块,随后在上垫板安装左后凸模、右前凸模,压力机带动左后凸模、右前凸模向下运动,在坯料上进行左后型腔、右前型腔的成形;当橡胶块组压缩时,抽掉最上层的橡胶块,左后凸模和右前凸模继续向下运动,直到左后型腔、右前型腔成形,然后左后凸模和右前凸模向上运动,脱离坯料;
9.(4)第三道次成形过程:保留第二道次成形的橡胶块组,取下挤压完毕的左后凸模和右前凸模,安装中凸模,在刚刚成形的左后型腔和右前凸模内放置对应的加热好的垫块,在每个垫块上放置橡胶块组,橡胶块组上方的左后安装槽配合嵌入左后填充块、右前安装槽配合嵌入右前填充块;
10.中凸模向下运动,在坯料上进行中型腔的成形,当橡胶块组压缩时,抽掉最上层的橡胶块,然后中凸模继续下压,直到中型腔完全成形,得到成形箱体;
11.(5)挤压成形完成后:停止压力机上工作台的向下运动,压力机上工作台反向向上运动,带动中凸模上升并与成形箱体脱离,随后拆卸压板,顶杆升起,顶出分瓣式凹模、成形箱体、顶板。
12.进一步,所述成形箱体上的左前型腔和左后型腔之间、右前型腔和右后型腔之间通过机械加工去除,从而左型腔由左前型腔和左后型腔之间相互连通形成,右型腔由右前型腔和右后型腔之间相互连通形成。
13.采用上述方案后,本发明的增益效果在于:
14.对于第一个成形难点本发明申请采用局部加载和对角交错成形的挤压方式来克服实验室挤压机较低的额定载荷,对角交错是指根据异形箱体型腔的特点来进行划分、每道次成形的型腔都相互错开,这样就避免了传统单侧集中成形或整体一次成型带来的载荷不均匀问题,保护挤压机设备,并且保证了能在有限的道次内成形复杂型腔的箱体,大大提高材料利用率和生产效率,节能减排。
15.对于第二个成形难点本发明采用填装垫块和橡胶块组的方式来控制金属的流动。在每一道次挤压完成后,将与之形状一样的垫块放置到对应的刚挤压完毕的型腔中,在后续道次挤压其他型腔的过程中,在刚刚放置好的垫块上摞几层橡胶块组,随着凸模向下运动,当橡胶压缩量到达一定程度时,抽掉一层橡胶块,然后凸模继续运动。使用垫块可以有效的避免在后续型腔的挤压过程中发生已挤压成形的型腔发生变形;在垫块上放置橡胶块可以防止其他型腔在成形的过程中,坯料金属在对应凸模的作用下沿着与凸模运动垂直的方向流动,把已放置好的垫块顶起,使得已挤压好的型腔变形。该方法设计结构巧妙、可靠性好,成形精度高,改善合金的成形性,提高成形件的综合力学性能。
附图说明
16.图1是本发明坯料的结构示意图;
17.图2是本发明成形箱体的结构示意图;
18.图3是本发明第一道次挤压成形时模具工作状态的主视结构示意图;
19.图4是本发明第一道次挤压成形时模具工作状态的俯视结构示意图;
20.图5是本发明坯料第一道次成形的结构示意图;
21.图6是本发明第二道次挤压成形时模具工作状态的主视结构示意图一(左前型腔上放置橡胶块组);
22.图7是本发明第二道次挤压成形时模具工作状态的主视结构示意图二(右后型腔上放置橡胶块组);
23.图8是本发明第二道次挤压成形时模具工作状态的俯视结构示意图;
24.图9是本发明坯料第二道次成形的结构示意图;
25.图10是本发明第三道次挤压成形时模具工作状态的主视结构示意图;
26.图11是本发明第三道次挤压成形时模具工作状态的俯视结构示意图;
27.图12是本发明顶板的俯视结构示意图;
28.图13是本发明左前凸模的俯视结构示意图;
29.图14是本发明右后凸模的俯视结构示意图;
30.图15是本发明中凸模的俯视结构示意图。
31.标号说明:1、箱体;11、左型腔;111、左前型腔;112、左后型腔;12、中型腔;13、右型腔;131、右前型腔;132、右后型腔;14、凹槽;2、上模板;21、凸模组件;211、上垫板;212、左前凸模;213、左后凸模;214、右前凸模;215、右后凸模;216、中凸模;217、左前填充块;218、左后填充块;219、橡胶垫板;220、右后填充块;221、中填充块;222、橡胶块组;223、t形槽螺钉;224、导套;3、下模板;31、凹模组件;311、内应力圈;312、分瓣式凹模;313、顶板;314、中间块;315、螺钉;316、顶杆;317、外应力圈;318、导柱;319、刮料板;320、压板;4、坯料;5、第一定位销;6、第二定位销。
具体实施方式
32.以下结合附图及具体实施例对本发明做详细的说明。
33.如图2所示,本发明的箱体1的目标成形箱体为“π”字型形状,该箱体1结构分为左型腔11、中型腔12和右型腔13,所述左型腔11包括以箱体1结构的中心线对称的左前型腔111和左后型腔112,所述右型腔13包括以箱体1结构的中心线对称的右前型腔131和右后型腔132,所述中型腔12位于左型腔11和右型腔13之间,所述箱体1在右型腔13的中心线方向向内开设凹槽14,在该箱体1结构上成形多个型腔的难度较大,需合理控制成形载荷,本发明涉及一种大投影面积的异形箱体1挤压成形模具,如图3所示,该模具包括与压力机上工作台连接的上模板2、拆卸安装于上模板2的凸模组件21、导套224、与压力机下工作台连接的下模板3、拆卸安装在下模板3上的凹模组件31、刮料板319;所述的下模板3用紧固螺栓装配在压力机下工作台。
34.凸模组件21包括上垫板211、左前凸模212、左后凸模213、右前凸模214、右后凸模215、中凸模216、左前填充块217、左后填充块218、右前填充块、右后填充块220、中填充块
221和橡胶块组222;如图13所示的是左前凸模212的俯视结构示意图,同时也是左后凸模213的俯视结构示意图,左前凸模212和右前凸模214两者的结构相同,均呈t型,如图14所示的是右后凸模215的俯视结构示意图,同时也是右前凸模214的仰视结构示意图,右前凸模214、右后凸模215两者的结构相对称,均拆分为两个独立的部分,也可以根据实际需要大小进行拆分,如图15所示的是中凸模216的俯视结构示意图,中凸模216为长方形,中凸模216的面积大于左型腔11的面积,也大于右型腔13的面积,这也是中型腔12作为第三道次成形的原因。
35.所述上模板2下部连接所述上垫板211,所述上垫板211下部开设供所述左前凸模212、左后凸模213、右前凸模214、右后凸模215、中凸模216连接的左前安装槽、左后安装槽、右前安装槽、右后安装槽、中安装槽,左前凸模212、左后凸模213、右前凸模214、右后凸模215、中凸模216分别用以成形左前型腔111、左后型腔112、右前型腔131、右后型腔132、中型腔12,分别与左前型腔111、左后型腔112、右前型腔131、右后型腔132、中型腔12形状相配合。
36.上垫板211上设有t形槽螺钉223,上垫板211侧边开设t形槽用以放置t形槽螺钉223,t形槽螺钉223末端和凸模以螺纹配合方式连接,通过t形槽螺钉223连接来防止上垫板211内已放置好的凸模及填充块的相对滑动。所述的上模板2用紧固螺栓装配在压力机上工作台。
37.所述左前填充块217、左后填充块218、右前填充块、右后填充块220、中填充块221用于分别与左前安装槽、左后安装槽、右前安装槽、右后安装槽、中安装槽配合填装。
38.所述左前填充块217、左后填充块218、右前填充块、右后填充块220、中填充块221下方设置有一一对应或多个结合对应的橡胶块组222。在橡胶块组222下方的型腔内填装对应的所述垫块。
39.所述凹模组件31包括内应力圈311、分瓣式凹模312、顶板313、中间块314、垫块、顶杆316和外应力圈317,所述下模板3和内应力圈311底部以顶出孔为圆心向外发散均布安装孔,安装孔供螺栓安装以连接下模板3和内应力圈311,所述内应力圈311固定在下模板3上。
40.所述顶板313、所述分瓣式凹模312和中间块314安装在内应力圈311内部,且所述分瓣式凹模312和中间块314安装在所述顶板313的上方,所述分瓣式凹模312在凸模组件21下方开设供箱体坯料4置入的内腔。
41.如图12所示,所述顶板313在对应凹槽14的位置设置插槽供中间块314嵌入安装,内腔底部中间开有顶出孔,尺寸与顶杆316间隙配合;所述外应力圈317过盈配合套置在内应力圈311的外部。
42.本发明还设有导柱318导套224构成的导向组件,所述导套224采用紧固螺纹的方式装配在上模板2下部,所述导柱318采用间隙配合的方式装配在内应力圈311上部,导柱318和导套224相对配合滑动设置。所述的导柱318和导套224配合一起起到导程作用。
43.本发明提供一种大投影面积的异形箱体1挤压成形方法,包括以下步骤:
44.(1)成形前准备:将下模板3、内应力圈311、外应力圈317、顶杆316与导柱318按照上述装配关系安装到压力机下工作台上;将上模板2、上垫板211、导套224按照上述装配关系安装到压力机的工作台;挤压前利用已经安装好的导套224及导柱318对整个模具进行校正;将坯料4、各个凸模、分瓣式凹模312、垫块、顶板313及中间块314进行预热,等预热完毕
后,将分瓣式凹模312、顶板313及中间块314放置到内应力圈311内,所述顶板313和分瓣式凹模312之间设有第一定位销5,所述顶板313和下模板3之间设有第二定位销6。然后将预热好的坯料4放进内腔中,如图1所示的是原始坯料4的结构示意图,所述内应力圈311上部的四周设置压板320,压板320与内应力圈311通过之间的螺钉315连接,压板320伸入分瓣式凹模312上方,压板320的下表面与所述分瓣式凹模312的上表面、外应力圈317的上表面相抵接,刮料板319直接伸入压板320内;由于异形箱体1投影面积较大,型腔较多,所以采用型腔对角交错成形方案,采用这种方案的所有型腔成形可以分为三个道次完成,按照“先成形左前型腔111、右后型腔132,再成形左后型腔112、右前型腔131,最后成形中型腔12”的方式在上垫板211中安装预热好的左前凸模212、右后凸模215;在上垫板211侧边的t型槽拧入t形槽螺钉223(具体可以是内六角圆柱头螺钉),来预防各个凸模的滑动;在安装预热模具的过程中分别在分瓣式凹模312和各个凸模的表面均匀的涂抹水基石墨润滑剂;
45.(2)第一道次成形过程:如图3、图4和图5所示,在左前安装槽和右后安装槽以外的安装槽配合嵌入填充块、并在填充块下方堆叠两块橡胶块组222,橡胶块组222的上下两端分别设置上橡胶垫板219和下橡胶垫板分别与填充块和坯料4接触,上橡胶垫板和下橡胶垫板将橡胶块组222夹合在中间;压力机开始带动上模板2、上垫板211、左前凸模212、右后凸模215向下运动,坯料4在凸模的作用下,先慢慢的充满整个凹模内腔,与此同时,在坯料4上成形出左前型腔111和右后型腔132,直到凸模下压到既定深度、保留了一定的底厚后,停止左前凸模212和右后凸模215的运动,然后左前凸模212和右后凸模215开始反向的向上运动,慢慢地脱离坯料4,在左前型腔111、右后型腔132成形后,为了方便脱模,做了两点的设计:(1)挤压凸模带有2
°
的拔模斜度;(2)在压板320的下方安装刮料板319,防止凸模将坯料4带起;橡胶块组222防止在型腔成形的过程中,坯料4未流动的金属部分发生翘起;压板320的作用是,压板320压住分瓣式凹模312,预防在反挤压的过程中流动的金属将分瓣式凹模312带起来;
46.(3)第二道次成形过程:如图5、图6、图7和图8所示,移除第一道次成形的橡胶垫板219和橡胶块组222,拆除刮料板319,取下挤压完毕的左前凸模212、右后凸模215,在刚刚成形的型腔内(左前型腔111、右后型腔132)放置对应的加热好的垫块,在每个垫块上放置橡胶垫板219和多层橡胶块组222,橡胶垫板219和多层橡胶块组222上方的左前安装槽配合嵌入左前填充块217、右后安装槽配合嵌入右后填充块220,随后在上垫板211安装左后凸模213、右前凸模214,压力机上工作台带动左后凸模213、右前凸模214向下运动,进行左后型腔112、右前型腔131的成形;在成形的过程中,一部分金属会沿着凸模运动的反方向向上流动,部分金属在坯料4底部沿着垂直于凸模运动的方向流动,然后会将放置在已成形型腔内的垫块顶起,导致已成形的型腔发生变形,放置在对应型腔内的垫块上的橡胶块组222则有效地预防了这一现象,上垫板211会和橡胶垫板219接触,压缩橡胶块组222,从而预防垫块底部的流动金属将垫块顶起来,当最上层的橡胶块压缩量到达一定程度后,抽掉最上层的橡胶块及对应的橡胶垫板219,左后凸模213和右前凸模214继续向下运动,直到左后型腔112、右前型腔131成形,然后安装刮料板319,左后凸模213和右前凸模214向上运动,慢慢地脱离坯料4;
47.(4)第三道次成形过程:如图9和图10所示,保留第二道次成形的橡胶垫板219和橡胶块组222,拆除刮料板319,取下挤压完毕的左后凸模213和右前凸模214,安装中凸模216,
在刚刚成形的型腔内(左后型腔112和右前凸模214)放置对应的加热好的垫块,在每个垫块上放置橡胶垫板219和多层橡胶块组222,橡胶垫板219和多层橡胶块组222上方的左后安装槽配合嵌入左后填充块218、右前安装槽配合嵌入右前填充块;
48.中凸模216向下运动,慢慢成形中型腔12,在中型腔12成形的过程中,随着上垫板211和多层橡胶垫板219的接触,当橡胶块组222压缩量达到一定程度时,中凸模216稍微升起,将橡胶块一层层抽取,然后中凸模216继续下压,直到中型腔12完全成形,得到成形箱体;
49.(5)挤压成形完成后:停止压力机上工作台的向下运动,压力机上工作台反向向上运动,带动中凸模216上升并与成形箱体脱离,中凸模216下部工作部分所设计的拔模斜度有利于脱模。在中凸模216上升的过程中,在压板320下方放置刮料板319,防止中凸模216将成形箱体带起。随后拆卸压板320和刮料板319,顶杆316升起,顶出分瓣式凹模312、成形箱体、顶板313。
50.成形箱体上的左前型腔111和左后型腔112之间的余料、右前型腔131和右后型腔132之间的余料均可以通过切屑等机械加工的方式去除,从而异形的、难以成行的左型腔11可以由左前型腔111和左后型腔112之间相互连通形成,同理,异形的、难以成行的右型腔13也可以由右前型腔131和右后型腔132之间相互连通形成。
51.以上所述仅为本发明的较佳实施例,并非对本案设计的限制,凡依本案的设计关键所做的等同变化,均落入本案的保护范围。