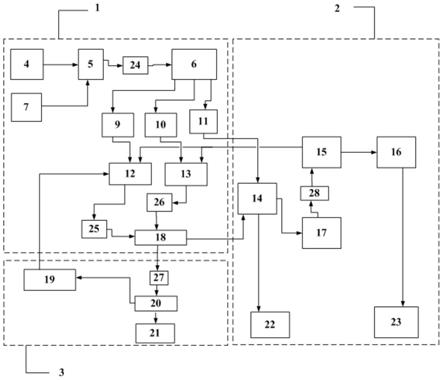
1.本发明涉及一种含油污泥无害化资源化处理系统,特别涉及一种氧化-萃取联合法处理含油污泥的系统。该系统能够实现含油污泥满足国家相关标准要求,达到无害化、减量化及资源化目标,属于含油污泥除油环保技术领域。
背景技术:
2.当前油田含油污泥和炼化“三泥”年产量超过300万吨,为危险废物。其主要来源于石油开采、运输、炼制及含油污水处理。研究发现,含油污泥因含有一些对人体有毒、有害物质等,已被列入国家危险废物名单(hw-08)。当前处理含油污泥的主要方法有:掩埋法、调质-分离法、焚烧法、热处理法、焦化法、生物法、溶剂萃取法及氧化法。
3.含油污泥组成复杂,来源不同,但经过处理后,含油污泥油含量需满足《gb4284-2018农用污泥污染物控制标准》中净化后含油污泥油含量小于等于0.3%的要求。掩埋法仅能处理那些油含量、重金属元素含量及水含量较低的含油污泥,对于绝大部分含油污泥,无法满足掩埋要求,同时容易产生二次污染;调质-分离法能够实现含油污泥减量化目标,但仍达不到净化后含油污泥油含量小于0.3%的要求;焚烧法对含油污泥的处理量较大、较彻底,处理后的残渣能够达到掩埋要求,但该方法一次性投资较大,处理产生的废气容易产生二次废气污染;热处理法是一种无害化的处理方法,该方法在无氧条件下逐步提升温度使含油污泥中的有机物裂解,裂解产生的气体进行冷凝回收,剩余残渣满足掩埋要求,但该方法需要热裂解的温度较高(>500℃),工艺条件苛刻,投资较大,易产生二次废气污染;焦化法能够促进含油污泥的资源化利用,但对于含油污泥的固含量有要求,且影响焦炭品质,油田企业的含油污泥及炼化企业的“三泥”均无法采用此种方法。生物法处理含油污泥的方式多样,对含油污泥的选择性较低,工艺操作较简单,但该方法对生物菌的选择要求高,同时处理周期较长。
4.溶剂萃取法利用“相似相溶”原理,是一种使用有机溶剂将含油污泥的中有机物溶解,并回收利用的方法,当前存在的溶剂萃取法,萃取剂组成及制备工艺复杂且需要多次萃取,导致萃取剂用量较大,溶剂的回收率低,成本较高昂,限制了该方法工业化应用。氧化法是一种化学法,利用氧化剂将含油污泥的中有机物大分子、胶质沥青质及胞外聚合物进行部分氧化分解,使细小的含泥颗粒或者碳粉从油中脱附,达到含油污泥分离的目的,当前行业使用的氧化剂氧化效率低,导致氧化剂用量大,反应周期长,处理成本高,对于罐底含油污泥除油也不彻底,普适性差,难以快速高效的处理含油污泥。
5.专利cn111606531a公开了一种含油污泥低温强化分离方法,该方法主要通过浮选分离、离心分离、芬顿氧化和重力沉降四个步骤对含油污泥进行净化处理。该方法对油田罐底含油污泥具有一定效果,但对经过长时间放置的炼厂罐底含油污泥,净化后的含油污泥油含量仍达不到0.3%的标准,且回收的油中因固含量(>2%)和水含量(>2%)超标达不到直接掺炼电脱盐的要求。
6.专利cn111718105a公开一种基于臭氧氧化和双氧水氧化联合降解含油污泥的处
理装置和方法,该方法通过添加表面活性剂降低油-泥-水三相表面张力,辅以曝气和氧化作用对含油污泥进行降解,降解后的污泥作为植物的肥料。但该方法处理周期(仅曝气流程需要6小时以上)较长,导致处理规模不大,且处理后的污泥油含量达不到国家标准,该方法对油含量低的剩余活性污泥,有一定效果,但对油含量高的罐底含油污泥,没有明显效果。
7.专利cn103693824b公开了一种含油污泥的深度萃取焦化工艺,该方法先是通过离心法脱除含油污泥的固相,固相经溶剂萃取分离出含油液相,含油液相进焦化装置。经萃取后的固相与煤掺烧。该方法处理含油污泥较为彻底,但需要多次萃取,且萃取剂不能循环利用,成本较高。回收的油进了焦化装置而不是电脱盐装置,造成资源浪费。
8.专利cn110845101a公开了一种含油污泥无害化处理系统及其处理方法,该方法处理含油污泥较彻底,但对于老化罐底油污泥需要多次萃取,造成溶剂损耗加大,且设备占地面积较大,处理成本较高,对含油污泥的普适性不好。
9.专利cn 113003922 a公开了一种种一体式高效热洗-高级氧化联合处理含油污泥的系统及含油污泥处理方法,该方法使用过硫酸盐和四氧化三铁作为氧化剂,表面活性剂作为洗涤剂,该方法对非老化的落地含油污泥有一定除油效果,但对老化含油污泥罐底含油污泥和污水处理厂含油污泥效果不佳,处理后的含油污泥油含量远达不到国家标准,且处理周期更长(大于48小时),不利于大规模处理。
10.本发明提供一种含油污泥无害化资源化处理方系统及处理方法,该方法使用氧化-萃取联合工艺处理含油污泥,在具有氧化法和萃取法的双重优点同时,又具有协同作用。所使用的氧化药剂氧化效率高,氧化剂用量少,对不同种类的含油污泥具有普适性,且工艺简单,经过氧化药剂处理后的含油污泥,再次用萃取法处理含油污泥,萃取剂不仅用量少,而且萃取次数低。整个工艺过程,可以实现含油污泥大规模处理高效处理,处理成本低。经处理后,含油污泥中的油含量满足国家相关标准要求(油含量<0.3%),除油率大于99%。回收的油可直接掺炼电脱盐,产生了明显的经济效益,实现了含油污泥无害化资源化目标。
技术实现要素:
11.为了解决上述问题,本发明的目的在于提供一种无害化资源化处理含油污泥系统。
12.一种无害化资源化处理含油污泥系统,包括氧化萃取系统、萃取溶剂发生系统、污泥干化系统,氧化萃取系统与污泥干化系统相连通、污泥干化系统与萃取溶剂发生系统相连通、氧化萃取系统与萃取剂发生系统相连通,其特征在于:氧化萃取系统的三相分离器液相出口与萃取溶剂发生系统的油水分离器连接,氧化萃取系统的两相分离器的固相出口与螺旋输送器连接,螺旋输送器与污泥干化系统的干化设备连接、两相分离器的液相引出口与萃取溶剂发生系统的油水分离器连接;污泥干化系统的冷凝器与氧化萃取系统的固相除油搅拌槽连接;萃取溶剂发生系统的溶剂发生塔轻质组分出口分别与氧化萃取系统固相除油搅拌槽和重相除油搅拌槽连接。
13.所述的氧化萃取系统:含油污泥管道与含油污泥调质槽连接,含油污泥调质槽设有搅拌装置,并设有氧化药剂加入口,与氧化药剂加料泵连接,含油污泥调质槽混合液出口连接含油污泥调质槽输出泵,含油污泥调质槽输出泵出口与三相分离器连接,三相分离器
固相出口与固相除油搅拌槽连接、三相分离器重相出口与重相除油搅拌槽连接、三相分离器液相出口与萃取溶剂发生系统的油水分离器连接;
14.固相除油搅拌槽物料出口与固相除油搅拌槽出料泵连接,固相除油搅拌槽出料泵出口与两相分离器连接;重相除油搅拌槽物料出口与重相除油搅拌槽出料泵连接,重相除油搅拌槽出料泵出口与两相分离器连接,两相分离器的固相出口与污泥干化系统的干化设备连接、两相分离器的液相引出口与萃取溶剂发生系统的油水分离器连接。
15.所述的污泥干化系统:与氧化萃取系统两相分离器连接的固相螺旋输送器与干化设备连接,干化设备气相出口与冷凝器连接,冷凝器与氧化萃取系统的固相除油搅拌槽连接,干化设备设有固相出口。
16.所述的萃取溶剂发生系统:油水分离器水相出口与污水处理装置22连接,油相出口与原油罐连接,原油罐设有原油罐输送泵,原油罐输送泵出口与溶剂发生塔连接,溶剂发生塔轻质组分出口分别与固相除油搅拌槽和重相除油搅拌槽连接,溶剂发生塔的剩余组分出口与换热器连接,换热器后产品送炼油装置。
17.所述的溶剂发生塔是由常压塔和/或减压塔组成。
18.一种无害化资源化处理含油污泥处理方法,包括以下步骤:
19.(1)含油污泥原料自界区外管线,引入原料调质槽,用氧化药剂进料泵向调质槽中加入氧化药剂,并持续搅拌,用含油污泥调质槽输出泵输送至三相离心机,进行油水、重相、固相分离;
20.(2)步骤(1)中分离出的油水相输送至油水分离器,进行油、水分离,分离出的油相进入原油缓冲槽,分离出的水相进入气浮,进行气浮除油,除完油后的水外排至界区外;
21.(3)步骤(2)分离出的原油经原油缓冲槽输送至萃取剂发生系统的溶剂发生塔,溶剂发生塔蒸馏出的萃取剂分别进入重相除油槽和固相除油槽,溶剂发生塔的塔底油,经换热器换热至60℃送至炼油装置;
22.(4)步骤(1)分离出的重相进入重相除油槽,向重相除油槽加入氧化药剂和萃取剂,进行氧化—萃取除油,然后将混合液用重相除油搅拌槽出料泵输送至两相离心机,进行油水、固分离;
23.(5)步骤(1)分离出的固相进入固相除油槽,向固相除油槽加入氧化药剂和萃取剂,进行氧化—萃取除油,然后将混合液用固相除油搅拌槽出料泵输至两相离心机,进行油水、固分离;
24.(6)步骤(4)和步骤(5)中分离出的油水进入油水分离器;
25.(7)步骤(4)和步骤(5)中分离出的固相输送至污泥干化设备,干化后的污泥输送至界区外;干化过程回收的萃取剂返回至重相除油槽和固相除油槽。
26.所述的步骤(1)中所述的氧化药剂有氧化剂、氧化助剂、表面活性剂和分散剂,其中氧化剂为双氧水、浓硫酸、高锰酸钾、浓硝酸中的一种或两种,氧化剂添加量为待处理含油污泥质量的0.05%~0.5%;氧化助剂为金属氧化物(优选mno2、fe2o3、tio2、cuo)、亚铁盐(优选feso4、fecl2、fe(no3)2)中的一种或一种以上,氧化助剂的添加量为氧化剂添加量的0.03%~0.06%;表面活性剂为有机磺酸盐类(优选十二烷基苯磺酸盐、十六烷基苯磺酸盐)、有机硫酸盐类(优选十二烷基硫酸盐、十六烷基硫酸盐)、有机卤化铵(优选十二烷基三甲基溴化铵、十四烷基三甲基氯化铵)中的一种或一种以上,表面活性剂添加量为待处理含
油污泥质量的0.01%~0.4%;分散剂为三聚磷酸钠、偏硅酸钠、六偏磷酸钠中的一种或两种,分散剂添加量为待处理含油污泥质量的0.03%~0.1%。
27.所述的剂发生塔产生的轻质组分,萃取剂质量:含油污泥质量=0.5~1.0:1。
28.所述的一种含油污泥无害化资源化处理系统及处理方法,其特征在步骤(3)所述的溶剂发生塔是由常压塔和减压塔组成。
29.所述的污泥干化是在于经两相分离器分离出的污泥需经过干化,干化的温度为130~180℃,干化过程产生的气体经冷凝回收,用于重相除油槽和固相除油槽中萃取剂的补充剂。
30.与现有技术相比,本发明的有益效果是:
31.1、本发明对不同种类的含油污泥具有优异的普适性。
32.2、本发明所使用的萃取剂来源于含油污泥除油后的回收原油经精馏装置蒸馏出的轻质组分,不需要从外界采购新的萃取剂,显著降低了装置的运行成本。
33.3、本发明将调质后的含油污泥进行三相分离,形成油水、重相、固相,提高了处理能力。
34.4、本发明使用的氧化-萃取联合工艺使处理后的含油污泥指标不仅满足国家现有环保标准,而且可以回收含油污泥中的原油,产生经济效益。实现含油污泥资源化无害化目标。
附图说明
35.图1为本发明的无害化资源化处理含油污泥系统示意图。
36.图1:1-氧化萃取系统,2-萃取溶剂发生系统,3-污泥干化系统,4-含油污泥管道,5-含油污泥调质槽,6-三相分离器,7-氧化药剂进料泵,9-三相分离器固相出口,10-三相分离器重相出口,11-三相分离器液相出口,12-固相除油搅拌槽,13-重相除油搅拌槽,14-油水分离器,15-溶剂发生塔,16-换热器,17-原油罐,18-两相分离器,19-冷凝器,20-干化设备,21-干化设备固相出口,22-污水处理装置,23-炼油装置,24-含油污泥调质槽输出泵,25-固相除油搅拌槽出料泵,26-重相除油搅拌槽出料泵,27-固相螺旋输送器,28-原油罐输送泵。
具体实施方式
37.下面结合具体实施例,并参照数据进一步详细的描述本发明。以下实施例只是为了举例说明本发明,而非以任何方式限制本发明的范围。
38.应用本发明中所述的含油污泥除油减量化的处理方法处理含油污泥后的油含量百分数均表示质量百分数,其中含油污泥中的水含量和含油污泥中的油含量按如下方法进行。
39.含油污泥中水含量测试按照gb/t 212—2008所述方法进行。
40.含油污泥中油含量测试按照gb/t 6504—2008所述方法进行。
41.以下实施例中所述的除油率表示含油污泥经本发明提供的方法处理后,总有机物的去除率。
[0042][0043]
参阅图1,一种含油污泥无害化资源化处理系统及其处理方法,包括以下步骤:
[0044]
(1)氧化萃取系统
[0045]
含油污泥自界区外引入含油污泥调质槽5,向含油污泥调质槽5中加入氧化药剂,并持续搅拌,进行氧化除油。用泵24将含油污泥调制槽5中的混合液输送至三相分离器6,进行固相(大颗粒底泥)分离、重相(小颗粒浮泥)、液相。经三相分离器6分离出的固相引入固相除油搅拌槽12、分离出的重相引入重相除油搅拌槽13、分离出的液相引入油水分离器14。
[0046]
用泵25和泵26将固相除油搅拌槽12中的物料和重相除油搅拌槽13中的物料分别输送至两相分离器18,进行固液分离。两相分离器18分离出的固相经螺旋输送器27引入干化设备20、分离出的液相引入油水分离器14。
[0047]
(2)污泥干化系统
[0048]
将两相分离器18分离出的固相用螺旋输送器27输送至干化设备20,干化设备20干化后的污泥用于掩埋、园林肥料或者建筑材料。干化设备20干化污泥的过程中,产生的蒸汽经冷凝器19冷凝,产生的液相被引入固相除油搅拌槽12,用于萃取除油。
[0049]
(3)萃取溶剂发生系统
[0050]
三相分离器6分离出的液相和两相分离器18分离出的液相分别被引入油水分离器14,在油水分离器14的作用下,水相引入污水处理装置22,油相引入原油罐17,用泵28将原油罐17中的油输送至溶剂发生塔15,溶剂发生塔15产生的轻质组分被引入固相除油搅拌槽12和重相除油搅拌槽12,用于萃取除油。溶剂发生塔15的剩余组分经换热器16降温后,引入炼油装置23。
[0051]
所述的氧化药剂有氧化剂、氧化助剂、表面活性剂和分散剂,其中氧化剂为双氧水、浓硫酸、高锰酸钾、浓硝酸中的一种或两种,氧化剂添加量为待处理含油污泥质量的0.05%~0.5%;氧化助剂为金属氧化物(优选mno2、fe2o3、tio2、cuo)、亚铁盐(优选feso4、fecl2、fe(no3)2)中的一种或一种以上,氧化助剂的添加量为氧化剂添加量的0.03%~0.06%;表面活性剂为有机磺酸盐类(优选十二烷基苯磺酸盐、十六烷基苯磺酸盐)、有机硫酸盐类(优选十二烷基硫酸盐、十六烷基硫酸盐)、有机卤化铵(优选十二烷基三甲基溴化铵、十四烷基三甲基氯化铵)中的一种或一种以上,表面活性剂添加量为待处理含油污泥质量的0.01%~0.4%;分散剂为三聚磷酸钠、偏硅酸钠、六偏磷酸钠中的一种或两种,分散剂添加量为待处理含油污泥质量的0.03%~0.1%。
[0052]
步骤(2)和步骤(3)中所述的萃取剂,为含油污泥净化过程中回收的原油经溶剂发生塔15产生的轻质组分,萃取剂质量:含油污泥质量=0.5~1.0:1。
[0053]
步骤(3)所述的溶剂发生塔15是由常压塔和减压塔组成。
[0054]
经两相分离器分离出的污泥需经过干化,干化的温度为130~180℃,干化过程产生的气体经冷凝回收,用于重相除油槽和固相除油槽中萃取剂的补充剂。
[0055]
实施例1
[0056]
以某炼化公司清罐含油污泥(油含量为27.2%、水含量38.3%)为原料进行试验,以双氧水为氧化剂,添加量为0.5%;以mno2氧化助剂,添加量为0.03%,十二烷基硫酸钠为表面活性剂,添加量为0.01%;偏硅酸钠添加量为0.03%;萃取剂与含油污泥按着质量比
0.5:1,按照上述步骤进行实施,处理后含油污泥油含量为0.15%,除油率为99.44%。
[0057]
实施例2
[0058]
以某炼化公司清罐含油污泥(油含量为27.2%、水含量38.3%)为原料进行试验,以高锰酸钾为氧化剂,添加量为0.10%;以fe2o3为氧化助剂,添加量为0.05%,十六烷苯磺酸钠为表面活性剂,添加量为0.15%;三聚磷酸钠添加量为0.05%;萃取剂与含油污泥按着质量比1.0:1,按照上述步骤进行实施,处理后含油污泥油含量为0.19%,除油率为99.30%。
[0059]
实施例3
[0060]
以某石化公司污油池含油污泥(油含量为41.4%、水含量55.6%)为原料进行试验,以浓硫酸为氧化剂,添加量为0.4%;以cuo为氧化助剂,添加量为0.06%十二烷基三甲基溴化铵为表面活性剂,添加量为0.05%;六偏磷酸钠添加量为0.1%;萃取剂与含油污泥按着质量比0.6:1,按照上述步骤进行实施,处理后含油污泥油含量为0.27%,除油率为99.34%。
[0061]
实施例4
[0062]
以某石化公司污油池含油污泥(油含量为41.4%、水含量55.6%)为原料进行试验,以浓硝酸为氧化剂,添加量为0.30%;以tio2为氧化助剂,添加量为0.05%,十四烷基三甲基氯化铵为表面活性剂,添加量为0.05%;偏硅酸钠添加量为0.05%;萃取剂与含油污泥按着质量比0.6:1,按照上述步骤进行实施,处理后含油污泥油含量为0.25%,除油率为99.39%。
[0063]
实施例5
[0064]
以某炼化公司剩余活性含油污泥(油含量为18.4%、含水量27.4%)为原料进行试验,以双氧水为氧化剂,添加量为0.2%;以feso4为氧化助剂,添加量为0.05%,十六烷基硫酸钠为表面活性剂,添加量为0.2%;偏硅酸钠添加量为0.05%;萃取剂与含油污泥按着质量比1:1,按照上述步骤进行实施,处理后含油污泥油含量为0.11%,除油率为99.40%。
[0065]
实施例6
[0066]
以某炼化公司剩余活性含油污泥(油含量为18.4%、含水量27.4%)为原料进行试验,以高锰酸钾为氧化剂,添加量为0.4%;以fecl2为氧化助剂,添加量为0.03%,十六烷基硫酸钠为表面活性剂,添加量为0.2%;偏硅酸钠添加量为0.1%;萃取剂与含油污泥按着质量比0.5:1,按照上述步骤进行实施,处理后含油污泥油含量为0.12%,除油率为99.34%。
[0067]
实施例7
[0068]
以某炼化公司清罐含油污泥(油含量为27.2%、水含量38.3%)为原料进行试验,以浓硝酸为氧化剂,添加量为0.3%;以fe(no3)2为氧化助剂,添加量为0.03%,十二烷基硫酸钠为表面活性剂,添加量为0.2%;偏硅酸钠添加量为0.08%;萃取剂与含油污泥按着质量比0.7:1,按照上述步骤进行实施,处理后含油污泥油含量为0.22%,除油率为99.19%。
[0069]
实施例8
[0070]
以某炼化公司清罐含油污泥(油含量为27.2%、水含量38.3%)为原料进行试验,以浓硫酸和高锰酸钾为氧化剂,添加量为0.5%(浓硫酸添加量为0.1%、高锰酸钾添加量为0.4%);以mno2为氧化助剂,添加量为0.03%,十二烷基硫酸钠为表面活性剂,添加量为0.3%;偏硅酸钠添加量为0.03%;萃取剂与含油污泥按着质量比0.6:1,按照上述步骤进行
实施,处理后含油污泥油含量为0.17%,除油率为99.37%。
[0071]
实施例9
[0072]
以某炼化公司剩余活性含油污泥(油含量为18.4%、含水量27.4%)为原料进行试验,以双氧水为氧化剂,添加量为0.4%;以mno2和tio2为氧化助剂,添加量为0.04%(mno2添加量为0.02%、tio2添加量为0.02%),十二烷基三甲基溴化铵为表面活性剂,添加量为0.3%;偏硅酸钠添加量为0.07%;萃取剂与含油污泥按着质量比1:1,按照上述步骤进行实施,处理后含油污泥油含量为0.16%,除油率为99.13%。
[0073]
实施例10
[0074]
以某油田罐底含油污泥(油含量为22.6%、水含量72.3%)为原料进行试验,以高锰酸钾为氧化剂,添加量为0.4%;以feso4为氧化助剂,添加量为0.05%,十二烷基三甲基溴化铵和十二烷基苯磺酸钠为表面活性剂,添加量为0.15%(十二烷基三甲基溴化铵添加量为0.05%、十二烷基苯磺酸钠添加量为0.1%);六偏磷酸钠添加量为0.1%;萃取剂与含油污泥按着质量比1:1,按照上述步骤进行实施,处理后含油污泥油含量为0.19%,除油率为99.15%。
[0075]
实施例11
[0076]
以某炼化公司剩余活性含油污泥(油含量为18.4%、含水量27.4%)为原料进行试验,双氧水和浓硫酸为氧化剂,添加量为0.5%(其中双氧水添加量为0.3%,浓硫酸添加量为0.2%);以fecl2为氧化助剂添加量为0.03%,十二烷基硫酸钠为表面活性剂,添加量为0.15%;偏硅酸钠和三聚磷酸钠为分散剂,添加量为0.1%(偏硅酸钠添加量为0.08%、三聚磷酸钠添加量为0.02%);萃取剂与含油污泥按着质量比0.5:1,按照上述步骤进行实施,处理后含油污泥油含量为0.11%,除油率为99.40%。
[0077]
实施例12
[0078]
以某石化公司污油池含油污泥(油含量为41.4%、水含量55.6%)为原料进行试验,以高锰酸钾和浓硫酸为氧化剂,添加量为0.04%(其中高锰酸钾添加量为0.03%,浓硫酸添加量为0.01%);以fecl2和fe2o3为氧化助剂添加量为0.03%(fecl2添加量为0.01%、fe2o3添加量为0.02%),十二烷基三甲基溴化铵为表面活性剂,添加量为0.05%;三聚磷酸钠添加量为0.1%;萃取剂与含油污泥按着质量比0.6:1,按照上述步骤进行实施,处理后含油污泥油含量为0.22%,除油率为99.46%。
[0079]
上述所描述的实施例仅仅是本发明一部分实施例,而不是全部的实施例。基于本发明中的实施例,本领域普通技术人员在没有做出创造性劳动前提下所获得的所有其他实施例,都属于本发明保护的范围。