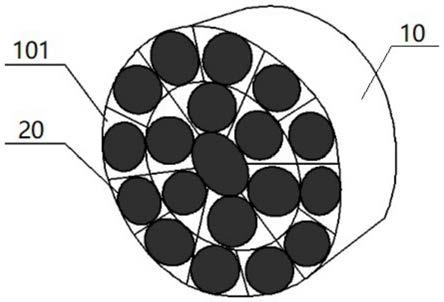
1.本发明涉及废水处理技术领域,特别地,涉及一种多孔塑性体内嵌粒子复合电极。此外,本发明还涉及一种用于制备多孔塑性体内嵌粒子复合电极的制备方法。
背景技术:
2.难降解有机废水是当前工业废水处理的热点和难点,电催化技术不产生污泥,无二次污染,反应条件温和,运行操作简单,反应过程易控制,极具应用前景,但因催化效率低、传质效率低、运行能耗高等问题限制了应用。三维电催化技术在传统二维电催化反应器内填充粒子电极,粒子电极在通电情况下被极化而带电,形成无数的微电池参与电化学反应,污染物在其表面被降解。由于增大了电极比表面积,大大缩小了阴阳极间距,相比传统的二维电极,提高了电能效率和传质效率,进而提高污染物的降解速率并降低能耗。
3.粒子电极的形式及其充填方式的优劣很大程度上决定了三维电催化系统的处理效果及能耗。传统的三维电催化技术将粒子电极填充在阴阳极板之间,粒子电极与极板直接接触形成短路电流,造成了电能的浪费。
4.现有技术201510967304.x采用带孔隙的绝缘筐内填充粒子电极,避免了粒子电极直接接触极板从而减少短路电流,绝缘框内粒子电极自然堆积,彼此接触形成串联,在一定程度上影响粒子电极效能发挥,此外也减少了反应器有效容积。
5.现有技术201310182361.8采用表面开长方形孔的多孔瓷环粒子与活性炭颗粒按一定质量比例混合组成复合粒子电极。该粒子电极瓷环表面开长方形孔,孔尺寸大于活性炭粒子粒径,通过搅拌自然混合的方式来负载活性炭粒子,通过搅拌自然混合的方式存在“混合均匀性、孔内活性炭粒子数量、粒子嵌入的牢固性等均很难控制”的技术问题,无法实现活性炭粒子彼此分散,且活性炭粒子嵌固不牢易脱落,最终导致复合粒子电极分离,影响反应效果。
技术实现要素:
6.本发明提供了一种多孔塑性体内嵌粒子复合电极及其制备方法,以解决现有的粒子电极存在的易与极板接触产生短路电流、复合粒子电极易分离的技术问题。
7.本发明采用的技术方案如下:
8.一种多孔塑性体内嵌粒子复合电极,包括:由塑性材料制备形成起安装支撑作用的塑性体,塑性体的外表面间隔设有内凹延伸的安装通道;安装通道内嵌安装有柱状的粒子电极,以使粒子电极间相互分散,并与塑性体连接形成复合粒子电极。
9.进一步地,安装通道的截面呈多边形;安装通道的最小孔径与对应安装的粒子电极的外径相适应,以使粒子电极稳定内嵌安装于安装通道中,且粒子电极与安装通道间具有供粒子电极与废水传质的反应间隙。
10.进一步地,相邻两条安装通道之间的壁面上开设有连通两者的连通缝或连通孔,以连通相邻两条安装通道。
11.进一步地,塑性体呈球状;安装通道沿塑性体的径向延伸贯穿塑性体;或者安装通道沿塑性体的径向内凹延伸成盲孔。
12.进一步地,塑性体呈多面体状;安装通道在塑性体的外平面上均匀间隔或非均匀间隔布设,且各安装通道内凹延伸贯穿塑性体,或内凹延伸成盲孔。
13.进一步地,塑性体呈柱状;安装通道沿塑性体端面的同心圆线均匀间隔或非均匀间隔布设,或在塑性体的端面上均匀间隔或非均匀间隔布设;安装通道沿塑性体的轴向贯穿塑性体,或沿塑性体的轴向内凹延伸成盲孔。
14.进一步地,塑性体的最大外径为10~40mm。
15.进一步地,塑性体的开孔率为90%以上;塑性材料为共聚塑料材料,不限于聚乙烯、聚丙烯、聚氯乙烯、聚苯乙烯,且塑性材料的密度为(0.85~0.95)g/cm3。
16.进一步地,粒子电极负载金属活性组分或催化剂。
17.根据本发明的另一方面,还提供了一种复合粒子电极的制备方法,用于制备出如上述中任一项的多孔塑性体内嵌粒子复合电极,包括以下步骤:将塑性材料、改性助剂置于混合机中充分混合均匀以得到混合料;将混合料置于挤压成型设备中挤压成型出塑性体;将粒子电极浸入含金属活性组分或催化剂的涂覆液中,浸渍完成后干燥;将粒子电极分别插入塑性体的安装通道中以得到复合粒子电极。
18.本发明具有以下有益效果:
19.本发明为三维电催化提供了一种新型的复合粒子电极,使用时将该复合粒子电极直接投入电催化反应器电场内,无需固定,操作简单;本发明的多孔塑性体内嵌粒子复合电极,立体结构且多安装通道的塑性体的电阻高、机械强度高、耐磨性好、耐酸碱性强、性能稳定,其支撑作用有助于防止粒子电极因受压摩擦而粉碎;通过塑性体的设置,可有效防止粒子电极与反应器电场内的阴阳极板直接接触,每颗粒子电极卡在单独的安装通道内,粒子电极之间相互分散、彼此绝缘,每一颗粒子电极均能充分发挥微电池的效能,进而避免短路电流,提高电流效率及废水处理效率,且粒子电极卡在安装通道中,嵌固牢固不易脱落,耐冲击性强,复合粒子电极不易分离,大大减少粒子电极的流失,便于回收,且废水处理效果良好;本发明中塑性体的外径、开孔数量、安装通道的孔径等参数可根据实际需要选择,内嵌粒子电极的数量也可根据实际需要调整,以适应于不同废水水质、不同处理需求,适用性广;本发明的复合粒子电极构造简单,利于大规模生产制造,对于三维电催化系统而言,是理想的粒子电极;
20.采用本发明的制备方法制备如上述中任一项的多孔塑性体内嵌粒子复合电极时操作简单、容易实施;采用塑性材料和改性助剂制备的塑性体结构稳定、机械强度高、耐磨性好、耐酸碱性强,适应于绝大部分的废水处理场合;制备塑性体时,只需根据目标塑性体的结构形式,提前制备出相应的成型模具即可,从而可轻松获取所需结构形式的塑性体,以满足不同结构形态、不同外形尺寸的粒子电极的内嵌安装需求,适应性强;将粒子电极浸入含金属活性组分或催化剂的涂覆液中,涂覆均匀,进而提高粒子电极的改性质量;将粒子电极通过外力方式插入塑性体的安装通道中,粒子电极嵌固牢固,不易脱落,耐冲击性强,复合粒子电极不易分离,大大减少粒子电极的流失,便于回收,且废水处理效果良好。
21.除了上面所描述的目的、特征和优点之外,本发明还有其它的目的、特征和优点。下面将参照图,对本发明作进一步详细的说明。
附图说明
22.构成本技术的一部分的附图用来提供对本发明的进一步理解,本发明的示意性实施例及其说明用于解释本发明,并不构成对本发明的不当限定。在附图中:
23.图1是本发明优选实施例的多孔塑性体内嵌粒子复合电极的结构示意图。
24.图例说明
25.10、塑性体;101、安装通道;20、粒子电极。
具体实施方式
26.以下结合附图对本发明的实施例进行详细说明,但是本发明可以由下述所限定和覆盖的多种不同方式实施。
27.参照图1,本发明的优选实施例提供了一种多孔塑性体内嵌粒子复合电极,包括:由塑性材料制备形成起安装支撑作用的塑性体10,塑性体10的外表面间隔设有内凹延伸的安装通道101;安装通道101内嵌安装有柱状的粒子电极20,以使粒子电极20间相互分散,并与塑性体10连接形成复合粒子电极。
28.本发明为三维电催化提供了一种新型的复合粒子电极,使用时将该复合粒子电极直接投入电催化反应器电场内,无需固定,操作简单;本发明的多孔塑性体内嵌粒子复合电极,立体结构且多安装通道101的塑性体10的电阻高、机械强度高、耐磨性好、耐酸碱性强、性能稳定,其支撑作用有助于防止粒子电极20因受压摩擦而粉碎;通过塑性体10的设置,可有效防止粒子电极20与反应器电场内的阴阳极板直接接触,每颗粒子电极20卡在单独的安装通道101内,粒子电极之间相互分散、彼此绝缘,每一颗粒子电极20均能充分发挥微电池的效能,进而避免短路电流,提高电流效率及废水处理效率,且粒子电极20卡在安装通道101中,嵌固牢固不易脱落,耐冲击性强,复合粒子电极不易分离,大大减少粒子电极的流失,便于回收,且废水处理效果良好;本发明中塑性体10的外径、开孔数量、安装通道的孔径等参数可根据实际需要选择,内嵌粒子电极的数量也可根据实际需要调整,以适应于不同废水水质、不同处理需求,适用性广;本发明的复合粒子电极构造简单,利于大规模生产制造,对于三维电催化系统而言,是理想的粒子电极。
29.可选地,如图1所示,安装通道101的截面呈多边形,该多边形可以是规则的正多边形,也可以是不规则的任意多边形,且多边形的边可以是直线,也可以是任意曲线,只需围设出的多边形结构能够稳定卡持相应设置的粒子电极,且与粒子电极之间具有废水进入进行反应的空间即可。安装通道101的最小孔径与对应安装的粒子电极20的外径相适应,以使粒子电极20稳定内嵌安装于安装通道101中,进而提高复合粒子电极的耐冲击性,使复合粒子电极不易分离;且粒子电极20与安装通道101间具有供粒子电极20与废水传质的反应间隙,以使废水能够进入安装通道101与粒子电极20之间,提高两者之间的传质效率及废水处理效果。
30.可选地,图未示,相邻两条安装通道101之间的壁面上开设有连通两者的连通缝或连通孔,以连通相邻两条安装通道101。连通缝可以仅开设于相邻两条安装通道101之间的壁面上,连通缝也可以向外延伸至与塑性体10的外表面连通;开设连通缝或连通孔时,应在保证塑性体10具有足够的支撑强度的前提下进行,防止塑性体强度不够导致受压变形后压碎粒子电极,连通缝和连通孔用于增大粒子电极20与废水的接触面积,进而提高传质效率
及废水处理效果。
31.可选地,塑性体10的第一实施例,图未示,塑性体10呈球状。安装通道101沿塑性体10的径向延伸贯穿塑性体10,安装柱状的粒子电极20时,在安装通道101的两端分别嵌入安装一颗粒子电极20,且塑性体10内所有安装的粒子电极20的嵌入端不相互接触,以避免产生短路电流。或者,安装通道101沿塑性体10的径向内凹延伸成盲孔,粒子电极20嵌入安装至安装通道101时,可有效防止粒子电极间相互接触短路。塑性体的该结构设置方式,使其结构简单、容易制备成型,且有效防止粒子电极间相互接触,避免短路电流产生。
32.可选地,塑性体10的第二实施例,图未示,塑性体10呈多面体状。安装通道101在塑性体10的外平面上均匀间隔布设,且各安装通道101内凹延伸贯穿塑性体10,安装柱状的粒子电极20时,在安装通道101的两端分别嵌入安装一颗粒子电极20,且塑性体10内所有安装的粒子电极20的嵌入端不相互接触,以避免产生短路电流。或者,安装通道101内凹延伸成盲孔,粒子电极20嵌入安装至安装通道101时,可有效防止粒子电极间相互接触短路。塑性体的该结构设置方式,使其结构简单、容易制备成型,且有效防止粒子电极间相互接触,避免短路电流产生。
33.可选地,塑性体10的第三实施例,如图1所示,塑性体10呈柱状。安装通道101沿塑性体10端面的同心圆线均匀间隔布设,即如图1所示,塑性体10的端面具有多层同心环,每层同心环内分隔出沿周向依次间隔设置的多个安装通道101;或者,安装通道101在塑性体10的端面上均匀间隔布设,如呈蜂窝煤状布设;或者,安装通道101在塑性体10的端面上无规则间隔布设。无论多条安装通道101在塑性体10上如何布设,各安装通道101沿塑性体10的轴向贯穿塑性体10,安装柱状的粒子电极20时,在安装通道101的两端分别嵌入安装一颗粒子电极20,且塑性体10内所有安装的粒子电极20的嵌入端不相互接触,以避免产生短路电流;或者,在塑性体10的两端分别布设安装通道,且使各安装通道101沿塑性体10的轴向内凹延伸成盲孔,粒子电极20嵌入安装至安装通道101时,可有效防止粒子电极间相互接触短路,也可以使塑性体10两端的安装通道彼此错位布设后连通,有效防止粒子电极间相互接触短路时,还可增大粒子电极20与废水的接触面积,进而提高传质效率及废水处理效果。塑性体的该结构设置方式,使其结构简单、容易制备成型,且有效防止粒子电极间相互接触,避免短路电流产生,并可有效增大粒子电极20与废水的接触面积,进而提高传质效率及废水处理效果。
34.可选地,塑性体10的第一、第二、第三实施例中,塑性体10的最大外径为10~40mm,防止塑性体10体积过大,占用较大的反应器空间,进而减少粒子电极的数量,且塑性体10体积过大时,将使形成的复合粒子电极失去微电池的作用效果,进而弱化废水处理效果。
35.可选地,塑性体10的第一、第二、第三实施例中,塑性体10的开孔率为90%以上,使其在保证整体结构稳定性前提下,尽可能搭载更多的粒子电极,提高单位体积内,粒子电极的数量,进而提高传质效率及废水处理效果。塑性材料为共聚塑料材料,不限于聚乙烯、聚丙烯、聚氯乙烯、聚苯乙烯,材料获取简单、制作成本低。且塑性材料的密度为(0.85~0.95)g/cm3,当该塑性体10搭载粒子电极形成复合粒子电极时,该复合粒子电极的密度将大于废水的密度,故而复合粒子电极可在反应器内堆叠,并填充整个阴阳极板之间的区域,减少旁路电流的产生,提高电流效率,且使粒子电极在该整个极板区域间均匀、分散填充,进而提高传质效率及废水处理效率。
36.可选地,塑性体10和/或粒子电极20负载金属活性组分或催化剂进行改性,进而提高催化效能。本可选方案中,粒子电极20为活性炭基粒子、金属基粒子、无机矿物质基粒子等低阻抗、高比表面积粒子的一种或多种,且柱状粒子的粒径为1~5mm。
37.参照图1,本发明的优选实施例还提供了一种复合粒子电极的制备方法,用于制备出如上述中任一项的多孔塑性体内嵌粒子复合电极,包括以下步骤:
38.将塑性材料、改性助剂置于混合机中充分混合均匀以得到混合料;
39.将混合料置于挤压成型设备中挤压成型出塑性体10;
40.将粒子电极20浸入含金属活性组分或催化剂的涂覆液中,浸渍完成后干燥;
41.将粒子电极20分别插入塑性体10的安装通道101中以得到复合粒子电极。
42.采用本发明的制备方法制备如上述中任一项的多孔塑性体内嵌粒子复合电极时操作简单、容易实施;采用塑性材料和改性助剂制备的塑性体10结构稳定、机械强度高、耐磨性好、耐酸碱性强,适应于绝大部分的废水处理场合;制备塑性体10时,只需根据目标塑性体10的结构形式,提前制备出相应的成型模具即可,从而可轻松获取所需结构形式的塑性体10,以满足不同结构形态、不同外形尺寸的粒子电极20的内嵌安装需求,适应性强;将粒子电极20浸入含金属活性组分或催化剂的涂覆液中,涂覆均匀,进而提高粒子电极20的改性质量;将粒子电极20通过外力方式插入塑性体10的安装通道101中,粒子电极20嵌固牢固,不易脱落,耐冲击性强,复合粒子电极不易分离,大大减少粒子电极的流失,便于回收,且废水处理效果良好。
43.具体地,首先,将100份聚乙烯、0.5~1份硬脂酸钙、0.5~1份聚乙烯蜡置于混合机中充分混合均匀以得到混合料;然后,将混合料置于双螺杆挤出机中熔融挤出,并通过相应模具按压成相应形状以得到具有安装通道101的塑性体10;接着,将粒子电极20浸入sncl4·
5h2o(0.5mol/l)和sbcl3(0.05mol/l)的乙醇溶液中,浸渍2~4h后在100~105℃下干燥;最后,将粒子电极20分别插入塑性体10的安装通道101中以得到复合粒子电极。
44.本发明具体实施例中,如图1所示,塑性体10为立体多孔塑料环,其材质为聚乙烯;立体多孔塑料环的结构为圆柱状,其端面设有内外3层同心环,各同心环内分隔出16~32个通孔,即安装通道101;立体多孔塑料环沿轴向的厚度为8~12mm,外径为10~15mm;立体多孔塑料环的开孔率为90%以上;立体多孔塑料环的比重为0.92~0.98g/cm3;立体多孔塑料环开孔的等效孔径为3~5mm;柱状粒子为活性炭基粒子,柱状活性炭基粒子的粒径为3~5mm;柱状活性炭基粒子以分散方式嵌入立体多孔塑料环的开孔内;柱状活性炭负载pbo2、sno2、sb2o3等金属氧化物。
45.以上所述仅为本发明的优选实施例而已,并不用于限制本发明,对于本领域的技术人员来说,本发明可以有各种更改和变化。凡在本发明的精神和原则之内,所作的任何修改、等同替换、改进等,均应包含在本发明的保护范围之内。