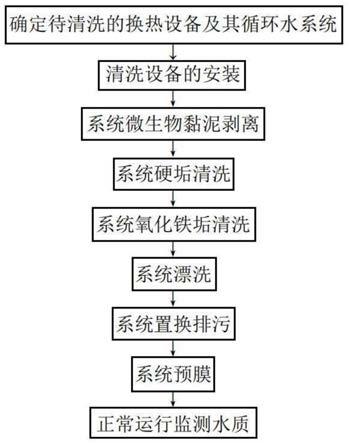
1.本发明涉及清洗领域,特别是涉及一种化工换热设备及循环水系统在线清洗方法。
背景技术:
2.化工生产过程一般囊括:化工原料
→
各种前处理(粉碎、除杂、混合等)
→
化学加工
→
各种后处理(提取、精馏等)
→
化工产品,在其生产装置配置中必不可少的涉及到加热或冷却的设备及其用于冷却的循环水装置,既化工换热设备及其循环水系统。由于循环水系统中的水散热蒸发,使水中各种矿物质和离子含量富集,并析出沉积在换热设备的表面上,使换热设备的换热效率降低,影响生产装置的正常运行并增加能耗,严重时须装置停运对其进行清洗;同时工业水中含有微量的微生物,在矿物离子浓度较高时营养充足,并在氧气的作用下,微生物在凉水塔填料上生长加快,致使凉水塔填料结垢严重,循环水管道上的氧化铁被微生物溶解吸蚀生成铁杆菌附着在管壁上,形成“锈瘤”,极大程度上降低了换热能力。
3.目前,行业上清洗基本采用高压水冲洗和强酸浸泡清洗,无论哪种清洗方式均存在如下的问题:
4.1、清洗时仅仅是对单台(套)设备进行清洗,无法对其所连接的管道、阀门、循环水系统的凉水塔等进行清洗,清洗范围窄且片面局部;
5.2、清洗时需将运行中的设备停止运行后才能进行,影响与其相连生产装置的产能发挥;
6.3、清洗时间短暂,清洗过程中人员作业劳动强度大且存在一定的安全风险;
7.4、清洗所使用的药剂浓度偏高,设备存在腐蚀风险和设备清洗泄漏风险。
技术实现要素:
8.本发明的目的在于:针对现有技术存在的问题,提供一种化工换热设备及循环水系统在线清洗方法。
9.为了实现上述目的,本发明采用的技术方案为:
10.一种化工换热设备及循环水系统在线清洗方法,包括:
11.a、微生物黏泥剥离阶段:向循环水池中依次投加ph调节剂、氧性杀生剂、黏泥剥离剂,ph值控制在1~7,其中,氧性杀生剂投加浓度为5~100mg/l,黏泥剥离剂投加浓度为50~500mg/l,连续运行时间为24~96h;
12.b、硬垢清洗阶段:向循环水池中同时投加除垢剂和缓蚀剂,ph值控制在1~6;
13.c、氧化铁垢清洗阶段:向循环水池中投加清洗剂,浊度、总铁含量基本平衡或呈下降趋势,两次测定值在0.1~1.0;
14.其清洗原理为硫酸与fe2o3反应,铁离子被还原成fe
2+
生成硫酸亚铁,溶解于循环水中,使氧化铁从换热器表面脱离,以达到清洗的目的;
15.d、漂洗阶段:向循环水池中投加漂洗剂,漂洗剂的投加浓度为10~200mg/l,ph值控制在7~14;
16.e、置换排污阶段:水质指标包括ph值4.5~9.5、浊度0~100、总铁含量0.1~5mg/l;
17.f、预膜阶段:在系统设备中投加预膜剂,在系统设备表面生成一层保护膜;
18.清洗后,系统设备的金属表面处于活化状态,容易被循环水里的游离氧和水中的ci-、so
4-、sio-等腐蚀,因此在系统中投加预膜剂,在系统设备表面生成一层保护膜,阻止循环水中有害物质对系统设备的腐蚀侵害。
19.采用本发明所述的一种化工换热设备及循环水系统在线清洗方法,能使换热设备在正常生产运行的状态下进行清洗,避免装置停车时间,提升装置利用效率;清洗干净彻底且清洗全面,不仅能对换热设备进行清洗,而且能对换热设备所连接的管道、阀门、循环水系统的凉水塔填料等进行清洗;只需作业人员按操作规定将涉及药品加入药剂桶中,作业人员劳动强度低且基本不存在安全风险隐患;清洗药剂浓度低,极大程度上减少甚至避免设备腐蚀风险和清洗泄漏风险;安全环保,不会对现场造成环境污染。
20.优选地,步骤a中,ph调节剂为硫酸、盐酸、硫酸氢钠、磷酸、碳酸中的一种或多种混合物。
21.进一步优选地,步骤a中,ph调节剂为工业硫酸,ph值控制在3~6。
22.优选地,步骤a中,ph调节剂投加方式包括一次性总量冲击式加入、缓慢连续滴加或分批间断投加。
23.进一步优选地,采用缓慢连续滴加方式,确保ph调节剂与循环水系统中的水充分混合,避免局部酸性过大造成腐蚀。
24.优选地,步骤a中,氧性杀生剂为次氯酸钠、二氧化氯、过氧化氢、次氯酸中的一种。
25.优选地,步骤a中,氧性杀生剂投加浓度为20~60mg/l,连续运行时间为36~60h。
26.优选地,步骤a中,黏泥剥离剂投加浓度为100~300mg/l,并一次性投加入循环水池中。
27.优选地,步骤b中,除垢剂和缓蚀剂采用滴加的投加方式,微量的投加到循环水池中并与循环水混合均匀。
28.优选地,步骤b中,ph值控制在2~4。
29.优选地,步骤c中,两次测定值在0.2~0.4,且在线清洗4~24h。
30.优选地,步骤d中,漂洗剂为氢氧化钠、氢氧化钙、氨水中的一种。
31.优选地,步骤d中,漂洗剂的投加浓度为30~70mg/l,ph值控制在11~13。
32.优选地,步骤e中,水质指标包括ph值5.5~8.5、浊度0~30、总铁含量0.1~3mg/l。
33.优选地,步骤f中,预膜剂为一水硫酸锌、三聚磷酸钠、六偏磷酸钠、有机磷一类的一种或多种。
34.进一步优选地,步骤f中,预膜剂选择为一水硫酸锌和三聚磷酸钠,一水硫酸锌的浓度为30~400mg/l、三聚磷酸钠的浓度为50~630mg/l。
35.综上所述,由于采用了上述技术方案,本发明的有益效果是:
36.本发明所述的一种化工换热设备及循环水系统在线清洗方法,能使换热设备在正常生产运行的状态下进行清洗,避免装置停车时间,提升装置利用效率;清洗干净彻底且清
洗全面,不仅能对换热设备进行清洗,而且能对换热设备所连接的管道、阀门、循环水系统的凉水塔填料等进行清洗;只需作业人员按操作规定将涉及药品加入药剂桶中,作业人员劳动强度低且基本不存在安全风险隐患;清洗药剂浓度低,极大程度上减少甚至避免设备腐蚀风险和清洗泄漏风险;安全环保,不会对现场造成环境污染。
附图说明
37.图1是实施例中在线清洗方法的流程示意图。
具体实施方式
38.下面结合附图,对本发明作详细的说明。
39.为了使本发明的目的、技术方案及优点更加清楚明白,以下结合附图及实施例,对本发明进行进一步详细说明。应当理解,此处所描述的具体实施例仅用以解释本发明,并不用于限定本发明。
40.实施例1
41.采用如图1所示的一种化工换热设备及循环水系统在线清洗方法,聚氯乙烯生产过程中使用的换热设备聚合釜及其循环水系统,系统循环水量4000m3/h;系统保有水量1500m3(含循环池、管道、设备水容量)。
42.安装清洗设备。
43.系统微生物黏泥剥离:先用滴加的方式向循环水池中加入ph调节剂工业硫酸600kg,将循环水的ph值调整到3~6,再采用一次性投加方式将氧性杀生剂次氯酸钠按投加浓度为20~60mg/l并连续运行时间为48h,最后加入黏泥剥离剂1500kg,不经置换排污,进入硬垢清洗。
44.系统硬垢清洗:向循环水池中同时投加除垢剂和缓蚀剂,除垢剂和缓蚀剂采用滴加的投加方式,微量的投加到循环水池中并与循环水混合均匀,ph值控制在2~4,不经置换排污,进入氧化铁垢清洗。
45.系统氧化铁垢清洗:向循环水池中投加清洗剂12000kg,并持续监测循环水的ph、浊度以及钙离子含量,两次测定值在0.2~0.4,且在线清洗4~24h,当基本维持不变后向循环水系统中再次加入工业硫酸以清除氧化铁的存在,不经置换排污,进入漂洗。
46.系统漂洗:向系统内加入漂洗剂氢氧化钠200kg,ph值控制在11~13,运行12h左右。
47.系统置换排污:进行置换排污,水质指标达到ph值5.5~8.5、浊度0~30、总铁含量0.1~3mg/l。
48.系统预膜:向系统中加入预膜剂三聚磷酸钠500kg、一水硫酸锌100kg,运行24h后转入正常运行状态。
49.正常运行监测水质。
50.通过上述在线清洗后,设备换热能力较清洗前提升60%以上,同样的反应条件下,通水量减少;循环水池凉水塔填料下水均匀;设备打开后表面光滑无锈瘤;达到清洗效果要求。
51.实施例2
52.采用如图1所示的一种化工换热设备及循环水系统在线清洗方法,氯乙烯生产过程中使用的制冷设备及其循环水系统,系统循环水量10000m3/h;系统保有水量3000m3(含循环池、管道、设备水容量)。
53.安装清洗设备。
54.系统微生物黏泥剥离:先用滴加的方式向循环水池中加入ph调节剂硫酸1600kg,将循环水的ph值调整到3.5~6,再采用一次性投加方式将氧性杀生剂次氯酸钠按投加浓度为20~60mg/l并连续运行时间为48h,最后加入黏泥剥离剂3600kg,不经置换排污,进入硬垢清洗。
55.系统硬垢清洗:向循环水池中同时投加除垢剂和缓蚀剂,除垢剂和缓蚀剂采用滴加的投加方式,微量的投加到循环水池中并与循环水混合均匀,ph值控制在2~4,不经置换排污,进入氧化铁垢清洗。
56.系统氧化铁垢清洗:向循环水池中投加清洗剂30000kg,并持续监测循环水的ph、浊度以及钙离子含量,两次测定值在0.2~0.4,且在线清洗4~24h,当基本维持不变后向循环水系统中再次加入硫酸以清除氧化铁的存在,不经置换排污,进入漂洗。
57.系统漂洗:向系统内加入漂洗剂氢氧化钠600kg,ph值控制在11~13,运行12h左右。
58.系统置换排污:进行置换排污,水质指标达到ph值5.5~8.5、浊度0~30、总铁含量0.1~3mg/l。
59.系统预膜:向系统中加入预膜剂三聚磷酸钠1300kg、一水硫酸锌360kg,运行24h后转入正常运行状态。
60.正常运行监测水质。
61.通过上述在线清洗后,设备换热能力较清洗前提升50%以上,同样的反应条件下,通水量减少;循环水池凉水塔填料基本无堵塞下水均匀;设备打开后表面光滑无锈瘤;达到清洗效果要求。
62.以上所述仅为本发明的较佳实施例而已,并不用以限制本发明,凡在本发明的精神和原则之内所作的任何修改、等同替换和改进等,均应包含在本发明的保护范围之内。