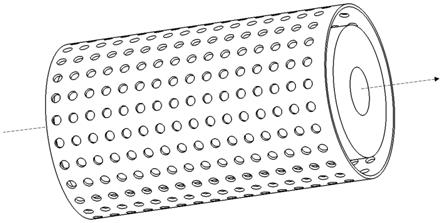
1.本发明涉及一种提高吸声能力的背腔穿孔隔板喷嘴,通过在隔板喷嘴周围安装一层穿孔板,使得隔板喷嘴的安装更易操作,同时实现更大的吸声效果,此发明为液体火箭发动机燃烧不稳定的抑制提供了有效手段。
背景技术:
2.在生产实践中,为了抑制压力波动并降低噪声,经常使用穿孔板对声波进行吸收。穿孔板是在一块薄板上进行穿孔形成的,通过在孔内的热粘性作用和孔边界处的涡脱落作用,实现对声波能量的耗散。由于其结构简单并且吸声能力强,穿孔板作为一种吸声手段被广泛地用于建筑、交通、声乐等领域。
3.一直以来,燃烧不稳定问题是制约液体火箭发动机发展的一个重要问题。燃烧不稳定是由燃料燃烧和燃烧室声学特性的耦合形成的,因此燃烧室声学特性是影响燃烧稳定性的重要因素。为了抑制液体火箭发动机横向不稳定,一般采用隔板或隔板喷嘴两种方式。目前用于液体火箭发动机不稳定燃烧抑制的隔板喷嘴的最佳吸声间隙为0.1
‑
0.2mm,在工程实践中很难精确控制,而本发明提出的背腔穿孔隔板喷嘴能够使得相邻隔板喷嘴之间的距离没有严格的要求,同时能够实现更大的对声能的耗散作用,因此该发明具有吸声能力强、易操作等优点。
技术实现要素:
4.针对上述背景,本发明提供一种提高吸声能力的背腔穿孔隔板喷嘴,在隔板喷嘴周围安装一层穿孔板,通过孔内的热粘性作用和孔边界处的涡脱落作用,实现对声波能量的耗散效果。通过商用软件comsol仿真,得出了孔隙率、孔径、板厚等因素对背腔穿孔隔板喷嘴吸声能力的影响规律,并提出了最大吸声效果的最佳设计方案。
5.本发明采用的技术方案如下:
6.一种提高吸声能力的背腔穿孔隔板喷嘴,其特征在于,在隔板喷嘴周围安装一层穿孔板,通过孔内的热粘性作用和孔边界处的涡脱落作用,达到对声波能量的耗散效果。背腔穿孔隔板喷嘴示意图如图1所示,由隔板喷嘴和穿孔板组成,隔板喷嘴外形为圆柱形,中空为推进剂通道,穿孔板为围绕隔板喷嘴一圈的具有一定厚度的打孔的板。穿孔板与隔板喷嘴之间存在一定的距离,孔隙率变化范围为0.01
‑
0.5,孔径变化范围为0.01mm
‑
1mm,板厚变化范围为1mm
‑
10mm,隔板喷嘴高度为10mm,隔板喷嘴的直径为10mm,穿孔板与隔板喷嘴之间的距离为5mm,相邻穿孔板之间距离为1mm。
7.comsol仿真模型如图2所示,取隔板喷嘴之间的单个通道进行研究,使用压力声学模块对整体声学系统进行计算,其控制方程为:
[0008][0009]
式中,p为声波压强扰动,ρ为密度,c为声速,ω为声波传播的角频率,下标0代表时
均量,符号是哈密顿算子。
[0010]
在comsol软件中,其内置的内部穿孔板边界条件能够模拟穿孔板声学特性,其声学转移阻抗模型为:
[0011][0012]
式中,z为穿孔板的声学转移阻抗,i为虚数单位,t
p
为穿孔板的厚度,d为孔的直径,σ为孔隙率,为fok函数,其表达式为a
n
为fok函数的级数的系数,y
v
表达式为j
n
为第一类贝塞尔函数的n阶函数,μ为动力粘度。此模型即描述了穿孔板的声学特性,可在计算中使用此声学转移阻抗来模拟穿孔板,使用此模型的前提为声波的波长远大于板厚和孔径,即ωt
p
/c0<<1且ωd/c0<<1。
[0013]
在进口处给定频率为f,大小为1pa的入射平面声波,通过隔板喷嘴上游和下游的声波幅值计算声波能量耗散系数e:
[0014][0015]
式中,和分别代表隔板喷嘴前端声波向下游和向上游传播的幅值,和分别代表隔板喷嘴后端声波向下游和向上游传播的幅值,耗散系数e表示声波的能量在经过穿孔板后的损失情况,其值越大,则能量损失越多。
[0016]
本发明中,固定孔的直径和板的厚度,通过改变穿孔数量,从而改变孔隙率,吸声系数随孔隙率的变大而先变大后减小,存在最大吸声系数的最佳孔隙率,最佳孔隙率在不同频率下略有不同,其值在0.2
‑
0.3之间。
[0017]
本发明中,固定穿孔数量和板的厚度,改变孔的直径,吸声系数随孔径的变大而先变大后减小,存在最大吸声系数的最佳孔径,最佳孔径在不同频率下略有不同,其值在0.1mm
‑
0.2mm之间,此时满足声波波长远大于孔径的前提条件。
[0018]
本发明中,固定穿孔数量和孔的直径,改变板的厚度,吸声系数随板厚的变大而先变大后减小,存在最大吸声系数的最佳板厚,最佳板厚在不同频率下略有不同,其值在2mm
‑
4mm之间,此时满足声波波长远大于板厚的前提条件。
[0019]
本发明中,在声波扰动频率为800hz下,给出穿孔板结构参数设计方案为孔径0.15mm,孔隙率0.3,板厚3mm时,穿孔板的吸声能力强于仅靠隔板喷嘴间隙热粘性的吸声能力。
[0020]
本发明其优点及功效在于:使得隔板喷嘴的安装更易操作,同时实现更大的吸声效果,且结构简单、安装方便、成本低、易加工。
附图说明
[0021]
图1为背腔穿孔隔板喷嘴结构示意图。
[0022]
图2为comsol仿真模型示意图。
[0023]
图3为不同孔隙率条件下的声能耗散系数的变化。
[0024]
图4为不同孔径条件下声能耗散系数的变化。
[0025]
图5为不同板厚条件下声能耗散系数的变化。
[0026]
图6为背腔穿孔隔板喷嘴与隔板喷嘴热粘性吸声能力对比。
[0027]
图中符号:σ穿孔板孔隙率,d穿孔板孔径,t
p
穿孔板厚度,e吸声系数,gap相邻隔板喷嘴间隙。
具体实施方式:
[0028]
下面结合附图,对本发明进行详细描述。在本实施例中,通过改变穿孔板结构尺寸参数,改变了系统的吸声系数,具体实施说明如下:
[0029]
在本实施例中,在常温常压下,在进口处给定频率为f,大小为1pa的入射平面声波,出口设为固壁,频率取值为500hz,800hz,1000hz,1200hz。孔隙率变化范围为0.01
‑
0.5,孔径变化范围为0.01mm
‑
1mm,板厚变化范围为1mm
‑
10mm,隔板喷嘴高度为10mm,隔板喷嘴的直径为10mm,穿孔板与隔板喷嘴之间的距离为5mm,相邻穿孔板之间距离为1mm。
[0030]
图3给出了不同频率下,吸声系数随孔隙率的变化规律。固定其它结构参数,改变穿孔数量,进而改变孔隙率,吸声系数随孔隙率的变大而先变大后减小,存在最大吸声系数的最佳孔隙率,最佳孔隙率在不同频率下略有不同,其值在0.2
‑
0.3之间。
[0031]
图4给出了不同频率下,吸声系数随孔径的变化规律。固定其它结构参数,改变孔的直径,吸声系数随孔径的变大而先变大后减小,存在最大吸声系数的最佳孔径,最佳孔径在不同频率下略有不同,其值在0.1mm
‑
0.2mm之间,此时满足声波波长远大于孔径的前提条件。
[0032]
图5给出了不同频率下,吸声系数随板厚的变化规律。固定其它结构参数,改变板的厚度,吸声系数随板的厚度的变大而先变大后减小,存在最大吸声系数的最佳板的厚度,最佳板的厚度在不同频率下略有不同,其值在2mm
‑
4mm之间,此时满足声波波长远大于板厚的前提条件。
[0033]
图6给出了在声波频率为800hz时背腔穿孔隔板喷嘴和传统的隔板喷嘴间隙热粘性吸声能力的对比。若以隔板喷嘴间隙热粘性特性来吸声,则最大吸声系数只能到0.45,而穿孔板在合适的结构尺寸参数下,最大吸声系数可以到0.65,因此穿孔板的吸声能力强于仅靠隔板喷嘴间隙热粘性的吸声能力。由此给出此模型下穿孔板结构参数最佳设计方案为孔径0.15mm,孔隙率0.3,板厚3mm。
[0034]
以上对本发明及其实施方式的描述,并不局限于此,附图中所示仅是本发明的实施方式之一。在不脱离本发明创造宗旨的情况下,不经创造地设计出与该技术方案类似的结构或实施例,均属本发明保护范围。