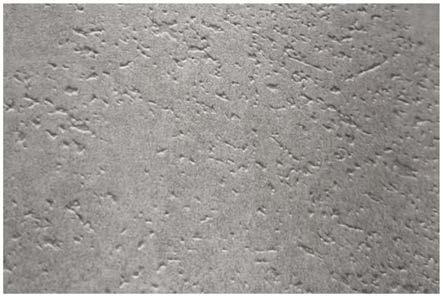
1.本发明涉及陶瓷墨水技术领域,具体涉及一种无光精雕墨水及其制备方法和应用。
背景技术:
2.陶瓷岩板是建筑陶瓷产品的新趋势,截止2021年10月,全球已建成具备生产1200
×
2400(mm)及以上规格的陶瓷岩板生产线174条。相对于传统的瓷砖,陶瓷岩板不仅拥有轻奢、超现代的外观和细腻、舒适的触感,还具有耐高温、耐磨刮、防污、耐酸碱等特点。陶瓷岩板可作为装饰材料,也可作为家居结构主材,经深加工后可替代天然石材、人造石材、木板、玻璃、铝板以及各类复合板等,并呈现更为卓越的性能。其中,为了达到更加逼真的效果,陶瓷岩板不再仅局限于表面图案设计,而是更注重陶瓷岩板表面的触感,因此,具有精细纹理的精雕效果的陶瓷岩板的需求量日益增多。
3.目前,陶瓷行业通常采用以下工艺制造具有纹理的陶瓷产品:
①
凹凸模具工艺,该工艺需制备多种效果的凹凸模具,且模具效果与图案纹理无法对位,纹理不够逼真,并且凹凸模具使用一段时间后,效果差异变大;而且,该工艺对于目前的超薄陶瓷岩板产品(即厚度在3mm以下的陶瓷岩板产品)是完全不可行的。
②
胶水+干粒的工艺,该工艺过程复杂,成本高,并且纹理的立体效果不够精细。
③
下陷墨水+亮光墨水的工艺,该工艺所制备的陶瓷产品仅能表现不连续的纹理效果,立体感差,且打印下陷墨水的位置会出现黄绿色外观,影响美观,如结合亮光墨水,则下陷处为亮光效果,与天然大理石或精雕木材相比,整体纹理效果显得不够自然逼真。如公开号cn108129026b公开的一种能够产生亮光凹陷线条效果的瓷砖,其工艺如下:在面釉上打印亮光精雕墨水后再与哑光保护釉形成凹陷纹理,通过亮光精雕墨水与哑光保护釉的光泽度差异形成能够产生亮光凹陷线条效果的瓷砖;但是该工艺制备的瓷砖纹理不够自然逼真。
④
数码模具技术,所得陶瓷产品的纹理细腻、逼真,但工艺复杂,成本高,且由于多次施釉工艺导致其不适用于超薄陶瓷岩板产品。如公开号cn112358326b公开的一种哑光深度雕刻效果的陶瓷砖的制备方法及陶瓷砖,该方法涉及数码模具技术,主要通过数码模具墨水与面釉之间的相互排斥及高压喷釉的冲击来获得深度雕刻效果好的陶瓷砖;但是该方法为确保其雕刻效果,需要进行多次施釉工艺(如施底釉、面釉等),且底釉和面釉的施釉量都很高(具体为:面釉的比重1.5-1.52g/ml、施釉量为800 1000g/m2,底釉的比重1.86-1.88g/ml、施釉量为350400g/m2),因此,过大的施釉量会对超薄陶瓷岩板产生过大的压力,进而导致超薄陶瓷岩板出现开裂等缺陷,不适用于超薄陶瓷岩板产品。
技术实现要素:
4.本发明的目的之一在于克服现有技术的不足,提供一种无光精雕墨水,以使陶瓷产品具有无光的精雕效果,以确保精雕处纹理的细腻、逼真,且该无光精雕墨水尤其适用于超薄陶瓷岩板产品。
5.本发明的目的之二在于提供一种无光精雕墨水的制备方法,所制得的无光精雕墨水性能优良(如粘度适中、流动性好、沉淀少),以免喷墨打印时喷墨机的过滤器或喷头被堵塞。
6.本发明的目的之三在于提供一种无光精雕墨水的应用方法,即将上述的一种无光精雕墨水应用于制备超薄陶瓷岩板。
7.基于此,本发明公开了一种无光精雕墨水,各原料的重量百分比为:
[0008][0009]
其中,高钡熔块为将sio2、al2o3、cao、k2o、na2o、bao、zno和sro混合形成的熔块,且bao在所述高钡熔块中的重量占比为16-20%。
[0010]
优选地,所述高钡熔块中各成分的重量百分比为:
[0011][0012][0013]
进一步优选地,所述亮光熔块中各成分的重量百分比为:
[0014][0015]
本发明的无光精雕墨水中的各固相组成部分(如钒酸锌、高钡熔块、亮光熔块)能协同控制精雕处的光泽,尤其是高钡熔块能确保陶瓷产品的精雕处与平面处无明显的光泽度差异(即实现无光效果)。而该无光精雕墨水中的钒酸锌由于会分解出五氧化二钒,五氧化二钒会大幅降低保护釉的高温表面张力,进而加深陶瓷产品的精雕处的深度;而且,该无
光精雕墨水中的亮光熔块由于熔点低,也能加深陶瓷产品的精雕处的深度。但是,钒酸锌和亮光熔块加深陶瓷产品精雕处深度的同时也会促进精雕处光泽度的提高,所以,为使该精雕墨水实现无光效果,钒酸锌和亮光熔块不能多用,且钒酸锌和亮光熔块需与高钡熔块搭配使用。
[0016]
优选地,所述溶剂为乙酰柠檬酸三丁酯、月桂酸甲酯、月桂酸异辛酯、苯甲酸异癸酯、环己烷-1,2-二羧酸二异壬酯、d150溶剂油和d200溶剂油中的一种或多种的组合物。
[0017]
所述溶剂更优选为乙酰柠檬酸三丁酯、月桂酸甲酯、月桂酸异辛酯、苯甲酸异癸酯、环己烷-1,2-二羧酸二异壬酯、d150溶剂油和d200溶剂油中的至少两种的组合物;将多种溶剂配合使用,有助于熔块颗粒及熔块粉末的研磨和分散,进而提高研磨效率。
[0018]
优选地,所述分散剂为高分子改性聚酯分散剂。
[0019]
所述分散剂更优选为辉虹hp 1064、宁柏迪fluijet 628、路博润solsperse j909和路博润solsperse j945中的一种或多种的组合物;以上分散剂能有效促进熔块颗粒及熔块粉末在上述溶剂中的分散效果,进一步提升研磨效率。
[0020]
本发明还公开了一种无光精雕墨水的制备方法,包括以下制备步骤:
[0021]
步骤s1,处理熔块:
[0022]
步骤s11,将熔块颗粒研磨至d
97
为15-20μm,得到熔块粉末;其中,所述熔块为高钡熔块和亮光熔块中的至少一种;
[0023]
步骤s12,将水和研磨助剂搅拌均匀后加入至砂磨机中继续搅拌,然后加入所述熔块粉末进行研磨,直至熔块粉末的d
97
为1-1.5μm,得到研磨后的浆料;
[0024]
步骤s13,将研磨后的浆料经压滤和洗涤,直至滤液水的电导率小于300μs/cm,得到熔块滤饼;
[0025]
步骤s14,将所述熔块滤饼保温后,破碎,过筛,得到超细熔块粉体;
[0026]
步骤s2,制备无光精雕墨水:
[0027]
步骤s21,将部分溶剂与分散剂混合搅拌均匀后加入至砂磨机内继续搅拌;
[0028]
步骤s22,向砂磨机中缓慢加入配方中的固相组成部分,继续研磨至墨水的d
97
达到0.8-1μm,然后加入剩余溶剂调整墨水的粘度和密度;其中,所述固相组成部分为超细熔块粉体和钒酸锌中的至少一种;
[0029]
步骤s23,将步骤s22调整后的墨水过滤后装瓶打包入库。
[0030]
其中,步骤s21中的部分溶剂占总溶剂的重量百分比的70-85%。
[0031]
优选地,所述步骤s12中,研磨体系的重量百分比配方为:水49.6-54.9%、研磨助剂0.1-0.4%和熔块45-50%;
[0032]
所述研磨助剂为三聚磷酸钠、十六烷基三甲基溴化铵和十二烷基硫酸钠中的一种或多种的组合物。
[0033]
优选地,所述步骤s14中,将所述熔块滤饼在150-200℃下保温10-15h,然后经打粉机破碎,过100目筛,得到所述超细熔块粉体;
[0034]
所述步骤s12和步骤s22中,研磨介质为0.3-0.4mm的钇稳定氧化锆珠;
[0035]
所述步骤s23中,所述墨水依次通过5μm和2μm的滤芯进行过滤。
[0036]
由于本发明的无光精雕墨水中的熔块(如高钡熔块、亮光熔块)硬度高且为玻璃态,现有分散剂的锚固基团很难吸附在其表面,导致其在油性溶剂体系中很难破碎研磨至
亚微米,基于此,所以,本发明在无光精雕墨水的制备方法中,改成先水性体系研磨熔块,以确保水磨后的熔块颗粒细小均匀,烘干后再放入油性的溶剂体系中研磨(也即进行步骤s1的熔块处理过程);试验发现,相比直接将熔块放入油性的溶剂体系中研磨,对熔块进行步骤s1的处理后,超细熔块粉体的粒径细小、分散均匀,从而能使所得的无光精雕墨水的粘度适中、流动性更好、沉淀更低,进而能有效避免该无光精雕墨水在喷墨打印时堵塞喷墨机的过滤器或喷头,还能缩短熔块的研磨时间。
[0037]
本发明还公开了一种无光精雕墨水的应用,即将所述无光精雕墨水应用于制备超薄陶瓷岩板;
[0038]
其应用方法,包括依次进行的以下应用步骤:
[0039]
步骤s31,压制坯体,干燥;
[0040]
步骤s32,坯体表面喷少量水,施面釉,干燥;
[0041]
步骤s33,依次喷墨打印颜色图案和无光精雕墨水,再施保护釉;
[0042]
步骤s34,将施完保护釉的坯体干燥,烧成,再经轻抛和磨边,即得所述超薄陶瓷岩板。
[0043]
优选地,所述步骤s32中,所述面釉的比重为1.45-1.55g/ml、施釉量为500-600g/m2;
[0044]
所述步骤s33中,所述保护釉的比重为1.3-1.4g/ml、施釉量为180-280g/m2;所述无光精雕墨水的喷墨量为20-50g/m2。
[0045]
相比公开号cn112358326b公开的一种哑光深度雕刻效果的陶瓷砖的制备方法及陶瓷砖,本发明的无光精雕墨水应用至陶瓷产品时,仅需施面釉和保护釉,无需施底釉,能简化施釉工艺,且施釉量更低(具体地:面釉的比重为1.45-1.55g/ml、施釉量为500-600g/m2,保护釉的比重为1.3-1.4g/ml、施釉量为180-280g/m2),因此,不会对超薄陶瓷岩板产生过大的压力而有效避免超薄陶瓷岩板出现开裂等缺陷,故而本发明的无光精雕墨水尤其适用于制备超薄陶瓷岩板产品。
[0046]
与现有技术相比,本发明至少包括以下有益效果:
[0047]
本发明的无光精雕墨水,在应用至陶瓷产品时,通过无光精雕墨水的油性溶剂与水性的保护釉的油水排斥原理,在喷完保护釉之后即可形成精雕效果;而且,试验发现:再结合该无光精雕墨水中的各固相组成部分(如钒酸锌、高钡熔块、亮光熔块)的协同配合能控制精雕处的光泽,尤其是高钡熔块能确保陶瓷产品的精雕处与平面处无明显的光泽度差异(即实现无光)。如此,通过无光精雕墨水的油性溶剂与水性的保护釉的排斥作用,结合该无光精雕墨水中各固相组成部分的协同作用,能使陶瓷产品具有无光的精雕效果,进而使精雕处的纹理细腻、逼真,且不影响陶瓷产品的图案发色。
[0048]
此外,相比直接将熔块放入油性的溶剂体系中研磨,本发明在制备该无光精雕墨水时,对熔块进行步骤s1的处理过程,以使超细熔块粉体的粒径细小、分散均匀,从而能使所得无光精雕墨水的粘度适中、流动性更好、沉淀更低,进而能有效避免该无光精雕墨水在喷墨打印时堵塞喷墨机的过滤器或喷头,并能缩短熔块的研磨时间。
附图说明
[0049]
图1为对比例1和实施例1的一种无光精雕墨水的制备方法中经步骤s1处理后的熔
块粉体的粒度分布对比图。
[0050]
图2为实施例1的一种无光精雕墨水的制备方法中经水研磨处理后的超细熔块粉体的sem图。
[0051]
图3为本发明的一种无光精雕墨水应用至超薄陶瓷岩板上的效果图。
具体实施方式
[0052]
为使本发明的上述目的、特征和优点能够更加明显易懂,下面结合附图和具体实施方式对本发明作进一步详细的说明。
[0053]
实施例1
[0054]
本实施例的一种无光精雕墨水,各原料的重量百分比为:高钡熔块:38%、亮光熔块:3%、钒酸锌:3%、月桂酸异辛酯:37.5%、环己烷-1,2-二羧酸二异壬酯:10%、d150溶剂油:4%、路博润solsperse j909:4.5%。
[0055]
其中,月桂酸异辛酯、环己烷-1,2-二羧酸二异壬酯和d150溶剂油为溶剂,路博润solsperse j909为分散剂。
[0056]
其中,高钡熔块中各成分的重量百分比为:sio2:40%、al2o3:19%、cao:3%、k2o:2%、na2o:6%、bao:19%、zno:6%、sro:5%。
[0057]
其中,亮光熔块中各成分的重量百分比为:sio2:60%、al2o3:20%、cao:2%、k2o:4%、na2o:5%、bi2o3:9%。
[0058]
本实施例的一种无光精雕墨水的制备方法,包括以下步骤:
[0059]
步骤s1,处理熔块(具体指高钡熔块和亮光熔块),具体包括如下步骤:
[0060]
步骤s11,将熔块颗粒通过振动磨研磨至d
97
为20μm,得到熔块粉末。
[0061]
步骤s12,将水和研磨助剂搅拌均匀后加入至卧式砂磨机中,继续搅拌,然后将步骤s11的熔块粉末加入至卧式砂磨机中进行研磨,直至熔块粉末的d
97
为1.1μm;其中,研磨介质为0.3-0.4mm的钇稳定氧化锆珠;步骤s12的研磨配方为:水:51.7%、三聚磷酸钠:0.3%、熔块:48%。
[0062]
步骤s13,将研磨后的浆料经过压滤洗涤,直至滤液水的电导率小于300μs/cm,得到熔块滤饼。
[0063]
步骤s14,将熔块滤饼在200℃下保温10h,然后经打粉机破碎,过100目筛后得超细熔块粉体。
[0064]
步骤s2,制备无光精雕墨水,具体包括如下步骤:
[0065]
步骤s21,将部分溶剂与分散剂混合搅拌均匀后加入至砂磨机内继续搅拌。
[0066]
步骤s22,向砂磨机中缓慢加入配方中的固相组成部分(即钒酸锌和步骤s14的超细熔块粉体),继续研磨至墨水的d
97
达到0.8μm,然后加入剩余溶剂调整墨水的粘度和密度;其中,研磨介质为0.3-0.4mm的钇稳定氧化锆珠。
[0067]
步骤s23,将步骤s22调整后的墨水依次通过5μm和2μm滤芯过滤后装瓶打包入库,即得本实施例的无光精雕墨水。
[0068]
本实施例的一种无光精雕墨水的应用方法,包括依次进行的如下应用步骤:
[0069]
p1.压制坯体,干燥,干燥温度为165℃。
[0070]
p2.坯体表面喷少量水,施面釉,面釉比重为1.45g/ml、施釉量为520g/m2。
[0071]
p3.施完面釉后进行干燥,干燥温度为170℃、干燥时间为3min。
[0072]
p4.喷墨打印颜色图案,打印无光精雕墨水,无光精雕墨水的喷墨量为35g/m2。
[0073]
p5.施保护釉,保护釉的比重为1.3g/ml、施釉量为200g/m2。
[0074]
p6.将施完保护釉的坯体经干燥窑干燥,干燥温度为180℃、干燥时间为3min,然后进窑烧成,烧成温度为1170℃、烧成时间为70min。
[0075]
p7.烧成后,经轻抛、磨边,即得本实施例的具有无光精雕效果的超薄陶瓷岩板。
[0076]
其中,以下实施例1-5,以p2中的面釉配方为:钾长石:20%、钠长石:25%、煅烧高岭土:6%、碳酸钡:8%、白云石:13%、烧滑石:12%、煅烧氧化锌:5%、石英:3%、硅酸锆:8%,以及p5中的保护釉配方为:钾长石:35%、烧滑石:13%、碳酸钡:15%、氧化锌:4%、烧高岭土:10%、硅灰石:8%、高岭土:15%为例,制备超薄陶瓷岩板。
[0077]
实施例2
[0078]
本实施例的一种无光精雕墨水,各原料的重量百分比为:高钡熔块:37%、乙酰柠檬酸三丁酯:16%、苯甲酸异癸酯:15%、月桂酸甲酯:20%、d200溶剂油:9%、宁柏迪fluijet 628:3%。
[0079]
其中,乙酰柠檬酸三丁酯、苯甲酸异癸酯、月桂酸甲酯和d200溶剂油为溶剂,宁柏迪fluijet 628为分散剂。
[0080]
其中,高钡熔块中各成分的重量百分比为:sio2:45%、al2o3:20%、cao:2%、k2o:1%、na2o:3%、bao:20%、zno:5%、sro:4%。
[0081]
本实施例的一种无光精雕墨水的制备方法,包括以下步骤:
[0082]
步骤s1,处理熔块(具体指高钡熔块),具体包括如下步骤:
[0083]
步骤s11,将熔块颗粒通过振动磨研磨至d
97
为18μm,得到熔块粉末。
[0084]
步骤s12,将水和研磨助剂搅拌均匀后加入至卧式砂磨机中,继续搅拌,然后将步骤s11的熔块粉末加入至卧式砂磨机中进行研磨,直至熔块粉末的d
97
为1.2μm;其中,研磨介质为0.3-0.4mm的钇稳定氧化锆珠;步骤s12的研磨配方为:水:54.7%、十六烷基三甲基溴化铵:0.3%、熔块:45%。
[0085]
步骤s13,将研磨后的浆料经过压滤洗涤,直至滤液水的电导率小于300μs/cm,得到熔块滤饼。
[0086]
步骤s14,将熔块滤饼在180℃下保温12h,然后经打粉机进行破碎,过100目筛后得超细熔块粉体。
[0087]
步骤s2,制备无光精雕墨水,具体制备步骤参照实施例1,其与实施例1的区别在于:步骤s22中,继续研磨至墨水的d
97
达到0.9μm;进而制得本实施例的无光精雕墨水。
[0088]
本实施例的一种无光精雕墨水的应用方法,包括依次进行的如下应用步骤:
[0089]
p1.压制坯体,干燥,干燥温度为180℃。
[0090]
p2.坯体表面喷少量水,施面釉,面釉比重为1.50g/ml、施釉量为560g/m2。
[0091]
p3.施完面釉后进行干燥,干燥温度为185℃、干燥时间为4min。
[0092]
p4.喷墨打印颜色图案,打印无光精雕墨水,无光精雕墨水的喷墨量为20g/m2。
[0093]
p5.施保护釉,保护釉的比重为1.4g/ml、施釉量为180g/m2。
[0094]
p6.将施完保护釉的坯体经干燥窑干燥,干燥温度为178℃、干燥时间为3min,然后进窑烧成,烧成温度为1190℃、烧成时间为65min。
[0095]
p7.烧成后,经轻抛、磨边,即得本实施例的具有无光精雕效果的超薄陶瓷岩板。
[0096]
实施例3
[0097]
本实施例的一种无光精雕墨水,各原料的重量百分比为:高钡熔块:28%、亮光熔块:6%、钒酸锌:8%、月桂酸异辛酯:34%、苯甲酸异癸酯:20%、辉虹hp 1064:4%。
[0098]
其中,月桂酸异辛酯和苯甲酸异癸酯为溶剂,辉虹hp 1064为分散剂。
[0099]
其中,高钡熔块中各成分的重量百分比为:sio2:43%、al2o3:17%、cao:2%、k2o:3%、na2o:7%、bao:16%、zno:4%、sro:8%;
[0100]
其中,亮光熔块中各成分的重量百分比为:sio2:62%、al2o3:25%、cao:2%、k2o:2%、na2o:3%、bi2o3:6%。
[0101]
本实施例的一种无光精雕墨水的制备方法,包括以下步骤:
[0102]
步骤s1,处理熔块(具体指高钡熔块和亮光熔块),具体包括如下步骤:
[0103]
步骤s11,将熔块颗粒通过振动磨研磨至d
97
为15μm,得到熔块粉末。
[0104]
步骤s12,将水和研磨助剂搅拌均匀后加入至卧式砂磨机中继续搅拌,然后将步骤s11的熔块粉末加入至卧式砂磨机中进行研磨,直至熔块粉末的d
97
为1μm;其中,研磨介质为0.3-0.4mm的钇稳定氧化锆珠;步骤s12的研磨配方为:水:49.6%、十二烷基硫酸钠:0.4%、熔块:50%。
[0105]
步骤s13,将研磨后的浆料经过压滤洗涤,直至滤液水的电导率小于300μs/cm,得到熔块滤饼。
[0106]
步骤s14,将熔块滤饼在150℃下保温15h,然后经打粉机进行破碎,过100目筛后得超细熔块粉体。
[0107]
步骤s2,制备无光精雕墨水,具体制备步骤参照实施例1,其与实施例1的区别在于:步骤s22中,继续研磨至墨水的d
97
达到1μm;进而制得本实施例的无光精雕墨水。
[0108]
本实施例的一种无光精雕墨水的应用方法,包括依次进行的如下应用步骤:
[0109]
p1.压制坯体,干燥,干燥温度为200℃。
[0110]
p2.坯体表面喷少量水,施面釉,面釉比重为1.48g/ml、施釉量为500g/m2。
[0111]
p3.施完面釉后进行干燥,干燥温度为160℃、干燥时间为4min。
[0112]
p4.喷墨打印颜色图案,打印无光精雕墨水,无光精雕墨水的喷墨量为50g/m2。
[0113]
p5.施保护釉,保护釉的比重为1.3g/ml、施釉量为280g/m2。
[0114]
p6.将施完保护釉的坯体经干燥窑干燥,干燥温度为200℃、干燥时间为5min,然后进窑烧成,烧成温度为1200℃、烧成时间为75min。
[0115]
p7.烧成后,经轻抛、磨边,即得本实施例的具有无光精雕效果的超薄陶瓷岩板。
[0116]
实施例4
[0117]
本实施例的一种无光精雕墨水,各原料的重量百分比为:高钡熔块:35%、亮光熔块:6%、月桂酸异辛酯:40%、d150溶剂油:15%、宁柏迪fluijet 628:2%、辉虹hp 1064:2%。
[0118]
其中,月桂酸异辛酯和d150溶剂油为溶剂,宁柏迪fluijet 628和辉虹hp 1064为分散剂。
[0119]
其中,高钡熔块中各成分的重量百分比为:sio2:44%、al2o3:16%、cao:2%、k2o:2%、na2o:5%、bao:18%、zno:6%、sro:7%。
[0120]
其中,亮光熔块中各成分的重量百分比为:sio2:65%、al2o3:18%、cao:4%、k2o:5%、na2o:4%、bi2o3:4%。
[0121]
本实施例的一种无光精雕墨水的制备方法,包括以下步骤:
[0122]
步骤s1,处理熔块(具体指高钡熔块和亮光熔块),具体包括如下步骤:
[0123]
步骤s11,将熔块颗粒通过振动磨研磨至d
97
为17μm,得到熔块粉末。
[0124]
步骤s12,将水和研磨助剂搅拌均匀后加入至卧式砂磨机中继续搅拌,然后将步骤s11的熔块粉末加入至卧式砂磨机中进行研磨,直至熔块粉末的d
97
为1.2μm;其中,研磨介质为0.3-0.4mm的钇稳定氧化锆珠;步骤s12的研磨配方为:水:50.8%、三聚磷酸钠:0.1%、十二烷基硫酸钠:0.1%、熔块:49%。
[0125]
步骤s13,将研磨后的浆料经过压滤洗涤,直至滤液水的电导率小于300μs/cm,得到熔块滤饼。
[0126]
步骤s14,将熔块滤饼在170℃下保温12h,然后经打粉机进行破碎,过100目筛后得超细熔块粉体。
[0127]
步骤s2,制备无光精雕墨水,具体制备步骤参照实施例1,其与实施例1的区别在于:步骤s22中,继续研磨至墨水的d
97
达到0.9μm;进而制得本实施例的无光精雕墨水。
[0128]
本实施例的一种无光精雕墨水的应用方法,包括依次进行的如下应用步骤:
[0129]
p1.压制坯体,干燥,干燥温度为160℃。
[0130]
p2.坯体表面喷少量水,施面釉,面釉比重为1.47g/ml、施釉量为600g/m2。
[0131]
p3.施完面釉后进行干燥,干燥温度为200℃、干燥时间为5min。
[0132]
p4.喷墨打印颜色图案,打印无光精雕墨水,无光精雕墨水的喷墨量为25g/m2。
[0133]
p5.施保护釉,保护釉的比重为1.4g/ml、施釉量为220g/m2。
[0134]
p6.将施完保护釉的坯体经干燥窑干燥,干燥温度为160℃、干燥时间为6min,然后进窑烧成,烧成温度为1200℃、烧成时间为55min。
[0135]
p7.烧成后,经轻抛、磨边,即得本实施例的具有无光精雕效果的超薄陶瓷岩板。
[0136]
实施例5
[0137]
本实施例的一种无光精雕墨水,各原料的重量百分比为:高钡熔块:34%、钒酸锌:8%、月桂酸异辛酯:30%、d150溶剂油:15%、环己烷-1,2-二羧酸二异壬酯:7%、宁柏迪fluijet 628:6%。
[0138]
其中,月桂酸异辛酯、d150溶剂油和环己烷-1,2-二羧酸二异壬酯为溶剂,宁柏迪fluijet 628为分散剂。
[0139]
其中,高钡熔块中各成分的重量百分比为:sio2:42%、al2o3:18%、cao:1%、k2o:0.5%、na2o:7%、bao:20%、zno:6%、sro:5.5%。
[0140]
本实施例的一种无光精雕墨水的制备方法,包括以下步骤:
[0141]
步骤s1,处理熔块(具体指高钡熔块),具体包括如下步骤:
[0142]
步骤s11,将熔块颗粒通过振动磨研磨至d
97
为15μm,得到熔块粉末。
[0143]
步骤s12,将水和研磨助剂搅拌均匀后加入至卧式砂磨机中继续搅拌,然后将步骤s11的熔块粉末加入至卧式砂磨机中进行研磨,直至熔块粉末的d
97
为1.5μm;其中,研磨介质为0.3-0.4mm的钇稳定氧化锆珠;步骤s12的研磨配方为:水:52.6%、三聚磷酸钠:0.4%、熔块:47%。
[0144]
步骤s13,将研磨后的浆料经过压滤洗涤,直至滤液水的电导率小于300μs/cm,得到熔块滤饼。
[0145]
步骤s14,将熔块滤饼在160℃下保温12h,然后经打粉机进行破碎,过100目筛后得超细熔块粉体。
[0146]
步骤s2,制备无光精雕墨水,具体制备步骤参照实施例1,其与实施例1的区别在于:步骤s22中,继续研磨至墨水的d
97
达到1μm;进而制得本实施例的无光精雕墨水。
[0147]
本实施例的一种无光精雕墨水的应用方法,包括依次进行的如下应用步骤:
[0148]
p1.压制坯体,干燥,干燥温度为180℃。
[0149]
p2.坯体表面喷少量水,施面釉,面釉比重为1.55g/ml、施釉量为550g/m2。
[0150]
p3.施完面釉后进行干燥,干燥温度为200℃、干燥时间为2min。
[0151]
p4.喷墨打印颜色图案,打印无光精雕墨水,无光精雕墨水的喷墨量为45g/m2。
[0152]
p5.施保护釉,保护釉的比重为1.3g/ml、施釉量为260g/m2。
[0153]
p6.将施完保护釉的坯体经干燥窑干燥,干燥温度为175℃、干燥时间为5min,然后进窑烧成,烧成温度为1180℃、烧成时间为80min。
[0154]
p7.烧成后,经轻抛、磨边,即得本实施例的具有无光精雕效果的超薄陶瓷岩板。
[0155]
对比例1
[0156]
本对比例的一种无光精雕墨水及其应用方法均参照实施例1,其与实施例1的区别在于:
[0157]
本对比例的一种无光精雕墨水的制备方法,包括以下步骤:
[0158]
步骤s1,处理熔块(具体指高钡熔块和亮光熔块):将熔块颗粒通过振动磨研磨至d
97
为19μm,得到熔块粉末,省略实施例1中步骤s12-s14的水研磨步骤。
[0159]
步骤s2,制备无光精雕墨水,具体制备步骤参照实施例1,得到本对比例的无光精雕墨水。进而参照实施例1的应用方法得到本对比例的超薄陶瓷岩板。
[0160]
对比例2
[0161]
本对比例的一种无光精雕墨水及其应用方法均参照实施例2,其与实施例2的区别在于:本对比例的一种无光精雕墨水的制备方法,包括以下步骤:
[0162]
步骤s1,处理熔块(具体指高钡熔块):将熔块颗粒通过振动磨研磨至d
97
为18μm,得到熔块粉末,省略实施例1中步骤s12-s14的水研磨步骤。
[0163]
步骤s2,制备无光精雕墨水,具体制备步骤参照实施例2,得到本对比例的无光精雕墨水。进而参照实施例2的应用方法得到本对比例的超薄陶瓷岩板。
[0164]
对比例3
[0165]
本对比例的一种墨水及其制备方法和应用方法均参照实施例1,其与实施例1的区别在于:本对比例的一种墨水中不添加高钡熔块,对应地,本对比例中的熔块即为亮光熔块;进而得到本对比例的墨水。再参照实施例1的应用方法得到本对比例的超薄陶瓷岩板。
[0166]
性能测试
[0167]
对实施例1-5和对比例1-3的墨水的性能及采用实施例1-5和对比例1-3的墨水对应制得的超薄陶瓷岩板的精雕效果进行性能测试,其测试结果如下表1所示:
[0168]
表1
[0169][0170]
注:流动性检测方法为在压力-0.08mpa条件下,250ml墨水通过型号为934-ah的玻璃纤维膜片所需时间,时间越长,说明墨水流动性越差,墨水分散性能越差,反之亦然。
[0171]
从图1-2可知,本发明所得的超细熔块粉体的粒径小;且相比对比例1-2的振动磨研,本发明采用先振动磨研后水研磨的熔块处理方式(即采用步骤s11-s14的熔块处理)所得的超细熔块粉的粒度分布更均一。
[0172]
从表1可知,本发明经步骤s11-s14的熔块处理后制得的无光精雕墨水的粘度适中,流动性好;而对比例1-2仅经振动磨研的墨水的粘度较高,分散性差,从而导致墨水的流动性差,使用时会堵塞喷墨机的过滤器或喷头。而且,结合表1和图3可知,本发明的添加有高钡熔块的墨水表现出无光的精雕效果(无光是指:精雕处与平面处无明显的光泽度差异,肉眼观察不出精雕处与平面处的光泽度差异),使陶瓷产品精雕处的纹理更加细腻、逼真;而对比例3的未添加高钡熔块的墨水尽管表现出好的深度雕刻效果,但由于其精雕处的光泽度明显大于其平面处的光泽度,也即其精雕处被暴露在较高光泽下,导致其精雕处的纹理在较高光泽下容易被淡化,进而导致其精雕处的纹理不够细腻、逼真。
[0173]
另外,申请人还发现,若以其他形式(如添加氧化钡的形式)向本发明的无光精雕墨水中引入钡(而非添加高钡熔块),则所制得的墨水的粘度、流动性等性能无法满足喷墨
打印的需求,墨水无法正常使用。
[0174]
尽管已描述了本发明实施例的优选实施例,但本领域内的技术人员一旦得知了基本创造性概念,则可对这些实施例做出另外的变更和修改。所以,所附权利要求意欲解释为包括优选实施例以及落入本发明实施例范围的所有变更和修改。
[0175]
以上对本发明所提供的技术方案进行了详细介绍,本文中应用了具体个例对本发明的原理及实施方式进行了阐述,以上实施例的说明只是用于帮助理解本发明的方法及其核心思想;同时,对于本领域的一般技术人员,依据本发明的思想,在具体实施方式及应用范围上均会有改变之处,综上所述,本说明书内容不应理解为对本发明的限制。