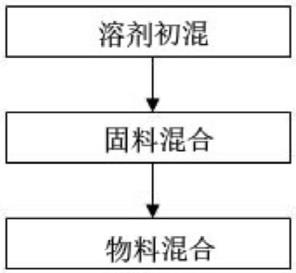
1.本发明涉及一种长效自修复智能防护涂料及制备方法,属防护技术领域。
背景技术:
2.目前自修复防护涂料是重要的一种防腐涂料之一,使用量巨大,产品种类众多,但当前的自修复防护涂料,往往均是通过简单的有机基材与缓蚀剂、防腐填料混合制备得到,如专利申请号为“2017107945138”的“一种防腐自修复涂料”、专利申请号为“2021102701896”的“一种用于布袋除尘器的自修复防腐涂料及制备方法”等产品,虽然可以一定程度满足使用的需要,但由于涂料中的缺乏有效的填充骨料,从而导致构成防护涂料的各组份间的分子作用力弱,各组份原料混合分散稳定性差且对外部环境中注入氧气等造成的氧化侵蚀也缺乏有效的抵御能力,从而当前的自修复防护涂料往往结构强度、弹性形变能力、抗氧化能力不足及涂料受损后修复效率低且修复质量差,从而严重影响了当前自修复防护涂料的防腐防护能力、抗损能力及使用寿命。
3.因此针对这一问题,开发了一种长效自修复智能防护涂料及制备方法,以解决当前产品存在的问题,满足实际使用的需要。
技术实现要素:
4.为了解决现有技术上的不足,本发明提供一种长效自修复智能防护涂料及制备方法。
5.一种长效自修复智能防护涂料,由以下重量份数组组分构成:石墨烯3.1%—5.2%、氧化铁粉2.1%—4.3%、氧化铜粉2.5%—6.8%、气相二氧化硅1.6%—2.5%、碳化硅粉1.6%—3.9%、偶联剂0.3%—1.4%、活性稀释剂0.3%—2.1%、颜料0—2.1%、苯丙乳液0—0.8%、缓蚀剂1.3%—2.1%、附着力促进剂0.3%—1.5%、成膜助剂1.1%—2.3%、消泡剂0.5%—1.15%、聚酰胺3.2%—9.5%、流平剂1.1%—2.1%、乳化剂0.3%—1.45%、改性环氧树脂8.1%—11.4%,余量为有机溶剂。
6.进一步的,所述的石墨烯、氧化铁粉、氧化铜粉、气相二氧化硅、碳化硅粉粒径均不大于400目,其中所示氧化铁粉为四氧化三铁铁粉;所述氧化铜粉为氧化亚铜;所述气相二氧化硅为四氧化三铁改性磁性气相二氧化硅。
7.进一步的,所述的偶联剂为硅烷偶联剂;活性稀释剂为甲基丙烯酸-β-羟乙酯、1,6-己二醇二丙烯酸酯中的任意一种;缓蚀剂为苯骈三氮唑、巯基苯骈噻唑 、甲基苯骈三氮唑、琉基苯并噻唑中的任意一种或几种共同使用;成膜助剂为苯甲醇ba、乙二醇、十二碳醇酯、乙二醇丁醚eb、丙二醇甲醚pm、己二醇丁醚醋酸酯、3-乙氧基丙酸乙酯eep中的任意一种;流平剂为聚甲基苯基硅氧烷、聚二甲基硅氧烷、聚醚聚酯改性有机硅氧烷、烷基改性有机硅氧烷中的任意一种;乳化剂为十二烷基硫酸钠、十二烷基苯磺酸钠、n-十二烷基二甲胺、环氧乙烷和环氧丙烷嵌段共聚物、多元醇脂肪酸酯中的任意一种;改性环氧树脂为低分子量双酚a型环氧树脂、中分子量双酚a型环氧树脂及高分子量双酚a型环氧树脂中的任意
一种。
8.进一步的,所述的有机溶剂为乙醇、正丁醇、丙二醇甲醚、环己酮、植物油及丙三醇中的任意一种。
9.一种长效自修复智能防护涂料的制备方法,包括以下步骤:s1,溶剂初混,首先将有机溶剂、消泡剂、颜料、成膜助剂、偶联剂一同添加到制备设备内,并在1.3—2.5倍标准大气压环境下以80℃—120℃恒温搅拌均匀,搅拌时间为10—30分钟,且并对搅拌均匀的混合液保温保压保存,得到有机混合液;s2,固料混合,将石墨烯、氧化铁粉、氧化铜粉、碳化硅粉混合,得到固体混合料,然后将活性稀释剂、聚酰胺、苯丙乳液、改性环氧树脂添加到固体混合料中并超声波搅拌均匀,并在搅拌过程中和固液混合物温度匀速升高至40℃—80℃,并在搅拌的同时将s1步骤制备的有机混合液同步匀速降温至40℃—80℃,并使有机混合液温度比固液混合物温度高10—20℃;s3,物料混合,将s2步骤制备的固液混合物与缓蚀剂、附着力促进剂、流平剂、乳化剂及气相二氧化硅一同添加到降温后的有机混合液内,并对混合物首先进行超声波搅拌10—20分钟,然后对混合物施加压力,使得混合物压力为1.5—3.6kg/cm2,并保持压力恒定的同时对混合物进行超声波均质,并在超声波均质的同时,对混合物内通入直流电流,并使直流电流的流动方向与压力作用力方向垂直分布,并在进行10—15分钟超声波均质后,使混合物保持压力及电流恒定状态下静置并自然冷却至常温,然后卸载压力并将混合液与外部电晕电路断开连接,即可得到成品涂料并管状无氧保存。
10.进一步的,所述的s1步骤至s3步骤中进行无聊混合制备过程中,物料混合制备环境中氧气含量不大于3%。
11.进一步的,所述的s3步骤中,在对混合物内通入直流电流时,另对混合物施加磁感线与电流方向呈30
°
—120
°
夹角分布的交变磁场。
12.进一步的,所述的制备设备包括承载机架、反应釜、输送料管、控制阀、供给泵、增压泵、惰性气体储气罐及驱动电路,所述承载机架为轴向截面呈“凵”字形槽状结构,所述反应釜共两个,嵌于承载机架内并与承载机架内侧面间通过滑轨滑动连接,与承载机架底部通过承载柱连接,两反应釜对称分布在承载机架轴线两侧,所述反应釜上端面设一个加料口,一个排气口,下端面设一个排料口,且两反应釜的排料口间通过输送料管连通,所述输送料管与排料口间通过供给泵连通,所述增压泵与输送料管及排料口间通过控制阀连通,所述输送料管、供给泵均与承载机架底部连接,所述排气口另通过三通阀与增压泵连通,所述增压泵另与惰性气体储气罐间通过导流管连通,所述惰性气体储气罐至少一个,并与承载机架外侧面连接,所述驱动电路与承载机架外侧面连接,并分别与反应釜、控制阀、供给泵、增压泵及三通阀电气连接。
13.进一步的,所述的反应釜为混合罐、密封盖、电磁铁、驱动电极、超声波换能器、电加热线圈、温度传感器、气压传感器、氧气传感器、接线端子,其中所述混合罐为轴向截面呈“凵”字形结构,其上端面与密封盖连接并构成密闭腔体结构,所述加料口和排气口嵌于密封盖内,排料口嵌于混合罐底部,所述驱动电极至少两个,对称分布在混合罐轴线两侧并嵌于混合罐侧壁内表面内,对称分布的两驱动电极间同轴分布,且驱动电极轴线与混合罐轴线垂直分布,所述电磁铁和超声波换能器均至少三个,嵌于混合罐侧壁内表面内并环绕混
合罐轴线均布并相互并联,且所述电磁铁和超声波换能器轴线与混合罐轴线呈30
°
—120
°
夹角,并分布在与混合罐底部垂直分布的平面内,所述温度传感器、气压传感器、氧气传感器均嵌于混合罐内,并与密封盖下端面连接,所述电加热线圈至少两个,嵌于混合罐底部内,并与混合罐同轴分布,且相邻两个电加热线圈直径差为10—50毫米,且各电加热线圈间相互并联,所述接线端子至少一个,嵌于混合罐外表面,并分别与电磁铁、驱动电极、超声波换能器、电加热线圈、温度传感器、气压传感器、氧气传感器及驱动电路电气连接。
14.本发明较传统的工艺,通过在构成防腐涂料中同时添加石墨烯、氧化铁粉、氧化铜粉、气相二氧化硅、碳化硅粉原料,极大的提高了防腐涂料的结构强度,可有效抵御外力冲击对涂料层造成的损伤,且设置的氧化铁粉、氧化铜粉另可一方面提高生产时物料混合均匀性、混合效率和通过磁场效应、电场效应提高物料间分子作用力,提高产品质量;另一方面可在使用中有效的提高涂料对外部氧化环境的抵御能力,同时通过配置的苯丙乳液、附着力促进剂、成膜助剂、聚酰胺、流平剂及改性环氧树脂有效的提高了涂料的弹性形变能力,粘接能力的同时,从而使得涂料在具备与目标物间良好的粘接稳定性的同时,另可在受到外力冲击时一方面通过弹性形变对外力冲击进行抵消,防止外力冲击对涂料层造成的损害;另一方面可通过涂料的弹性形变能力对因外力冲击造成的涂料层损伤部位进行弹性修复,确保涂料层的完整性,从而达到提高防护、防损的目的;此外,本发明中另通过设置的缓蚀剂,进一步辅助实现对涂料层受损后的修复能力,强化了涂料的受损修复性能,极大的提高了涂料的防护性能。
附图说明
15.下面结合附图和具体实施方式来详细说明本发明;图1为本发明方法流程示意图;图2为制备设备结构示意图。
具体实施方式
16.为使本发明实现的技术手段、创作特征、达成目的与功效易于施工,下面结合具体实施方式,进一步阐述本发明。
17.实施例1如图1所示,一种长效自修复智能防护涂料,由以下重量份数组组分构成:石墨烯3.1%、氧化铁粉2.1%、氧化铜粉2.5%、气相二氧化硅1.6%、碳化硅粉1.6%、偶联剂0.3%、活性稀释剂0.3%、缓蚀剂1.3%、附着力促进剂0.3%、成膜助剂1.1%、消泡剂0.5%、聚酰胺3.2%、流平剂1.1%、乳化剂0.3%、改性环氧树脂8.1%,余量为有机溶剂。
18.本实施例中,所述的石墨烯、氧化铁粉、氧化铜粉、气相二氧化硅、碳化硅粉粒径均不大于400目,其中所示氧化铁粉为四氧化三铁铁粉;所述氧化铜粉为氧化亚铜;所述气相二氧化硅为四氧化三铁改性磁性气相二氧化硅。
19.本实施例中,所述的偶联剂为硅烷偶联剂;活性稀释剂为甲基丙烯酸-β-羟乙酯;缓蚀剂为苯骈三氮唑;成膜助剂为乙二醇;流平剂为聚二甲基硅氧烷;乳化剂为十二烷基硫酸钠;改性环氧树脂为低分子量双酚a型环氧树脂。
20.同时,所述的有机溶剂为丙三醇。
21.一种长效自修复智能防护涂料的制备方法,包括以下步骤:s1,溶剂初混,首先将有机溶剂、消泡剂、颜料、成膜助剂、偶联剂一同添加到制备设备内,并在1.3倍标准大气压环境下以80℃恒温搅拌均匀,搅拌时间为10分钟,且并对搅拌均匀的混合液保温保压保存,得到有机混合液;s2,固料混合,将石墨烯、氧化铁粉、氧化铜粉、碳化硅粉混合,得到固体混合料,然后将活性稀释剂、聚酰胺、苯丙乳液、改性环氧树脂添加到固体混合料中并超声波搅拌均匀,并在搅拌过程中和固液混合物温度匀速升高至40℃,并在搅拌的同时将s1步骤制备的有机混合液同步匀速降温至50℃;s3,物料混合,将s2步骤制备的固液混合物与缓蚀剂、附着力促进剂、流平剂、乳化剂及气相二氧化硅一同添加到降温后的有机混合液内,并对混合物首先进行超声波搅拌10分钟,然后对混合物施加压力,使得混合物压力为1.5kg/cm2,并保持压力恒定的同时对混合物进行超声波均质,并在超声波均质的同时,对混合物内通入直流电流,并使直流电流的流动方向与压力作用力方向垂直分布,并在进行10分钟超声波均质后,使混合物保持压力及电流恒定状态下静置并自然冷却至常温,然后卸载压力并将混合液与外部电晕电路断开连接,即可得到成品涂料并管状无氧保存。
22.其中,接入到混合物张的直流电流的电压为6v,电流为1.5a;磁场强度为8000高斯。
23.本实施例中,所述的s1步骤至s3步骤中进行无聊混合制备过程中,物料混合制备环境中氧气含量不大于3%。
24.同时,所述的s3步骤中,在对混合物内通入直流电流时,另对混合物施加磁感线与电流方向呈30
°
夹角分布的交变磁场。
25.实施例2如图1所示,一种长效自修复智能防护涂料,由以下重量份数组组分构成:石墨烯5.2%、氧化铁粉4.3%、氧化铜粉6.8%、气相二氧化硅2.5%、碳化硅粉3.9%、偶联剂1.4%、活性稀释剂2.1%、颜料2.1%、苯丙乳液0.8%、缓蚀剂2.1%、附着力促进剂1.5%、成膜助剂2.3%、消泡剂1.15%、聚酰胺9.5%、流平剂2.1%、乳化剂1.45%、改性环氧树脂11.4%,余量为有机溶剂。
26.本实施例中,所述的石墨烯、氧化铁粉、氧化铜粉、气相二氧化硅、碳化硅粉粒径均不大于400目,其中所示氧化铁粉为四氧化三铁铁粉;所述氧化铜粉为氧化亚铜;所述气相二氧化硅为四氧化三铁改性磁性气相二氧化硅。
27.同时,所述的偶联剂为硅烷偶联剂;活性稀释剂为1,6-己二醇二丙烯酸酯;缓蚀剂为甲基苯骈三氮唑、琉基苯并噻唑1:1比例混合使用;成膜助剂为丙二醇甲醚pm;流平剂为聚甲基苯基硅氧烷;乳化剂为十二烷基硫酸钠;改性环氧树脂为低分子量双酚a型环氧树脂、中分子量双酚a型环氧树脂及高分子量双酚a型环氧树脂中的任意一种。
28.本实施例中,所述的有机溶剂为正丁醇。
29.一种长效自修复智能防护涂料的制备方法,包括以下步骤:s1,溶剂初混,首先将有机溶剂、消泡剂、颜料、成膜助剂、偶联剂一同添加到制备设备内,并在2.2倍标准大气压环境下以110℃恒温搅拌均匀,搅拌时间为25分钟,且并对搅拌均匀的混合液保温保压保存,得到有机混合液;s2,固料混合,将石墨烯、氧化铁粉、氧化铜粉、碳化硅粉混合,得到固体混合料,然
后将活性稀释剂、聚酰胺、苯丙乳液、改性环氧树脂添加到固体混合料中并超声波搅拌均匀,并在搅拌过程中和固液混合物温度匀速升高至70℃,并在搅拌的同时将s1步骤制备的有机混合液同步匀速降温至90℃,并使有机混合液温度比固液混合物温度高10—20℃;s3,物料混合,将s2步骤制备的固液混合物与缓蚀剂、附着力促进剂、流平剂、乳化剂及气相二氧化硅一同添加到降温后的有机混合液内,并对混合物首先进行超声波搅拌15分钟,然后对混合物施加压力,使得混合物压力为2.1kg/cm2,并保持压力恒定的同时对混合物进行超声波均质,并在超声波均质的同时,对混合物内通入直流电流,并使直流电流的流动方向与压力作用力方向垂直分布,并在进行12分钟超声波均质后,使混合物保持压力及电流恒定状态下静置并自然冷却至常温,然后卸载压力并将混合液与外部电晕电路断开连接,即可得到成品涂料并管状无氧保存。
30.其中,接入到混合物张的直流电流的电压为12v,电流为3.5a;磁场强度为9000高斯。
31.本实施例中,所述的s1步骤至s3步骤中进行无聊混合制备过程中,物料混合制备环境中氧气含量不大于3%。
32.同时,所述的s3步骤中,在对混合物内通入直流电流时,另对混合物施加磁感线与电流方向呈45
°
夹角分布的交变磁场。
33.实施例3如图1所示,一种长效自修复智能防护涂料,由以下重量份数组组分构成:石墨烯4.2%、氧化铁粉3.3%、氧化铜粉5.8%、气相二氧化硅2.1%、碳化硅粉2.6%、偶联剂0.8%、活性稀释剂0.7%、颜料1.1%、苯丙乳液0.3%、缓蚀剂1.8%、附着力促进剂0.7%、成膜助剂1.5%、消泡剂0.9%、聚酰胺9.%、流平剂1.7%、乳化剂0.8%、改性环氧树脂10%,余量为有机溶剂。
34.本实施例中,所述的石墨烯、氧化铁粉、氧化铜粉、气相二氧化硅、碳化硅粉粒径均不大于400目,其中所示氧化铁粉为四氧化三铁铁粉;所述氧化铜粉为氧化亚铜;所述气相二氧化硅为四氧化三铁改性磁性气相二氧化硅。
35.同时,所述的偶联剂为硅烷偶联剂;活性稀释剂为甲基丙烯酸-β-羟乙酯;缓蚀剂为琉基苯并噻唑;成膜助剂为己二醇丁醚醋酸酯;流平剂为聚醚聚酯改性有机硅氧烷;乳化剂为环氧乙烷和环氧丙烷嵌段共聚物;改性环氧树脂为中分子量双酚a型环氧树脂。
36.进一步说明的,所述的有机溶剂为丙二醇甲醚。
37.一种长效自修复智能防护涂料的制备方法,包括以下步骤:s1,溶剂初混,首先将有机溶剂、消泡剂、颜料、成膜助剂、偶联剂一同添加到制备设备内,并在2倍标准大气压环境下以100℃恒温搅拌均匀,搅拌时间为20分钟,且并对搅拌均匀的混合液保温保压保存,得到有机混合液;s2,固料混合,将石墨烯、氧化铁粉、氧化铜粉、碳化硅粉混合,得到固体混合料,然后将活性稀释剂、聚酰胺、苯丙乳液、改性环氧树脂添加到固体混合料中并超声波搅拌均匀,并在搅拌过程中和固液混合物温度匀速升高至50℃,并在搅拌的同时将s1步骤制备的有机混合液同步匀速降温至70℃;s3,物料混合,将s2步骤制备的固液混合物与缓蚀剂、附着力促进剂、流平剂、乳化剂及气相二氧化硅一同添加到降温后的有机混合液内,并对混合物首先进行超声波搅拌15分钟,然后对混合物施加压力,使得混合物压力为3kg/cm2,并保持压力恒定的同时对混合
物进行超声波均质,并在超声波均质的同时,对混合物内通入直流电流,并使直流电流的流动方向与压力作用力方向垂直分布,并在进行12分钟超声波均质后,使混合物保持压力及电流恒定状态下静置并自然冷却至常温,然后卸载压力并将混合液与外部电晕电路断开连接,即可得到成品涂料并管状无氧保存。
38.其中,接入到混合物张的直流电流的电压为18v,电流为2.5a;磁场强度为10000高斯。
39.本实施例中,所述的s1步骤至s3步骤中进行无聊混合制备过程中,物料混合制备环境中氧气含量不大于3%。
40.本实施例中,所述的s3步骤中,在对混合物内通入直流电流时,另对混合物施加磁感线与电流方向呈90
°
夹角分布的交变磁场。
41.实施例4如图1所示,一种长效自修复智能防护涂料,由以下重量份数组组分构成:石墨烯4.8%、氧化铁粉4.1%、氧化铜粉6.5%、气相二氧化硅2.3%、碳化硅粉3.5%、偶联剂1.1%、活性稀释剂1.5%、颜料1.9%、苯丙乳液0.4%、缓蚀剂1.5%、附着力促进剂1.4%、成膜助剂1.2%、消泡剂0.9%、聚酰胺8.3%、流平剂1.6%、乳化剂1.1%、改性环氧树脂10.5%,余量为有机溶剂。
42.其中,所述的石墨烯、氧化铁粉、氧化铜粉、气相二氧化硅、碳化硅粉粒径均不大于400目,其中所示氧化铁粉为四氧化三铁铁粉;所述氧化铜粉为氧化亚铜;所述气相二氧化硅为四氧化三铁改性磁性气相二氧化硅。
43.同时,所述的偶联剂为硅烷偶联剂;活性稀释剂为甲基丙烯酸-β-羟乙酯;缓蚀剂为巯基苯骈噻唑与琉基苯并噻唑以1:2比例混合使用;成膜助剂为己二醇丁醚醋酸酯;流平剂为烷基改性有机硅氧烷;乳化剂为n-十二烷基二甲胺;改性环氧树脂为低分子量双酚a型环氧树脂。
44.本实施例中,所述的有机溶剂为植物油。
45.一种长效自修复智能防护涂料的制备方法,包括以下步骤:s1,溶剂初混,首先将有机溶剂、消泡剂、颜料、成膜助剂、偶联剂一同添加到制备设备内,并在2倍标准大气压环境下以100℃恒温搅拌均匀,搅拌时间为25分钟,且并对搅拌均匀的混合液保温保压保存,得到有机混合液;s2,固料混合,将石墨烯、氧化铁粉、氧化铜粉、碳化硅粉混合,得到固体混合料,然后将活性稀释剂、聚酰胺、苯丙乳液、改性环氧树脂添加到固体混合料中并超声波搅拌均匀,并在搅拌过程中和固液混合物温度匀速升高至55℃,并在搅拌的同时将s1步骤制备的有机混合液同步匀速降温至70℃;s3,物料混合,将s2步骤制备的固液混合物与缓蚀剂、附着力促进剂、流平剂、乳化剂及气相二氧化硅一同添加到降温后的有机混合液内,并对混合物首先进行超声波搅拌16分钟,然后对混合物施加压力,使得混合物压力为2.8kg/cm2,并保持压力恒定的同时对混合物进行超声波均质,并在超声波均质的同时,对混合物内通入直流电流,并使直流电流的流动方向与压力作用力方向垂直分布,并在进行12分钟超声波均质后,使混合物保持压力及电流恒定状态下静置并自然冷却至常温,然后卸载压力并将混合液与外部电晕电路断开连接,即可得到成品涂料并管状无氧保存。
46.其中,接入到混合物张的直流电流的电压为36v,电流为1.1a;磁场强度为15000高
斯。
47.本实施例中,所述的s1步骤至s3步骤中进行无聊混合制备过程中,物料混合制备环境中氧气含量不大于3%。
48.本实施例中,所述的s3步骤中,在对混合物内通入直流电流时,另对混合物施加磁感线与电流方向呈60
°
夹角分布的交变磁场。
49.本发明在具体实施中,如图2所示,用于物料混合用的制备设备包括:承载机架1、反应釜2、输送料管3、控制阀4、供给泵5、增压泵6、惰性气体储气罐7及驱动电路8,承载机架1为轴向截面呈“凵”字形槽状结构,反应釜2共两个,嵌于承载机架1内并与承载机架1内侧面间通过滑轨9滑动连接,与承载机架1底部通过承载柱10连接,两反应釜2对称分布在承载机架1轴线两侧,反应釜2上端面设一个加料口201,一个排气口202,下端面设一个排料口203,且两反应釜2的排料口203间通过输送料管3连通,输送料管3与排料口203间通过供给泵5连通,增压泵5与输送料管3及排料口203间通过控制阀4连通,输送料管3、供给泵5均与承载机架1底部连接,排气口202另通过三通阀11与增压泵6连通,所述增压泵6另与惰性气体储气罐7间通过导流管连通,惰性气体储气罐7至少一个,并与承载机架1外侧面连接,驱动电路8与承载机架1外侧面连接,并分别与反应釜2、控制阀4、供给泵5、增压泵6及三通阀11电气连接。
50.本实施例中,所述的反应釜2为混合罐21、密封盖22、电磁铁23、驱动电极24、超声波换能器25、电加热线圈26、温度传感器27、气压传感器28、氧气传感器29、接线端子20,其中所述混合罐21为轴向截面呈“凵”字形结构,其上端面与密封盖22连接并构成密闭腔体结构,所述加料口201和排气口202嵌于密封盖22内,排料口203嵌于混合罐21底部,所述驱动电极24至少两个,对称分布在混合罐21轴线两侧并嵌于混合罐21侧壁内表面内,对称分布的两驱动电极24间同轴分布,且驱动电极24轴线与混合罐21轴线垂直分布,所述电磁铁23和超声波换能器25均至少三个,嵌于混合罐21侧壁内表面内并环绕混合罐21轴线均布并相互并联,且所述电磁铁23和超声波换能器25轴线与混合罐21轴线呈30
°
—120
°
夹角,并分布在与混合罐21底部垂直分布的平面内,所述温度传感器27、气压传感器28、氧气传感器29均嵌于混合罐21内,并与密封盖22下端面连接,所述电加热线圈26至少两个,嵌于混合罐21底部内,并与混合罐21同轴分布,且相邻两个电加热线圈26直径差为10—50毫米,且各电加热线圈26间相互并联,所述接线端子20至少一个,嵌于混合罐21外表面,并分别与电磁铁23、驱动电极24、超声波换能器25、电加热线圈26、温度传感器27、气压传感器28、氧气传感器29及驱动电路8电气连接。
51.本实施例中,所述驱动电极24为横断面呈矩形,且前端面与混合罐21轴线平行分布的板砖结构,所述驱动电极24中,单个驱动电极24前端面面积为10—50mm2,各个驱动电极24前端面总面积为混合罐21内表面总面积的10%—35%。
52.本实施例中,驱动电极24与混合罐21内侧面间通过硬质绝缘块205连接。
53.此外,所述排气口202另通过三通阀11与一个泄压阀204连接。
54.本发明较传统的工艺,通过在构成防腐涂料中同时添加石墨烯、氧化铁粉、氧化铜粉、气相二氧化硅、碳化硅粉原料,极大的提高了防腐涂料的结构强度,可有效抵御外力冲击对涂料层造成的损伤,且设置的氧化铁粉、氧化铜粉另可一方面提高生产时物料混合均匀性、混合效率和通过磁场效应、电场效应提高物料间分子作用力,提高产品质量;另一方
面可在使用中有效的提高涂料对外部氧化环境的抵御能力,同时通过配置的苯丙乳液、附着力促进剂、成膜助剂、聚酰胺、流平剂及改性环氧树脂有效的提高了涂料的弹性形变能力,粘接能力的同时,从而使得涂料在具备与目标物间良好的粘接稳定性的同时,另可在受到外力冲击时一方面通过弹性形变对外力冲击进行抵消,防止外力冲击对涂料层造成的损害;另一方面可通过涂料的弹性形变能力对因外力冲击造成的涂料层损伤部位进行弹性修复,确保涂料层的完整性,从而达到提高防护、防损的目的;此外,本发明中另通过设置的缓蚀剂,进一步辅助实现对涂料层受损后的修复能力,强化了涂料的受损修复性能,极大的提高了涂料的防护性能。
55.以上显示和描述了本发明的基本原理和主要特征和本发明的优点。本行业的技术人员应该了解,本发明不受上述实施例的限制,上述实施例和说明书中描述的只是说明本发明的原理,在不脱离本发明精神和范围的前提下,本发明还会有各种变化和改进,这些变化和改进都落入要求保护的本发明范围内。本发明要求保护范围由所附的权利要求书及其等效物界定。