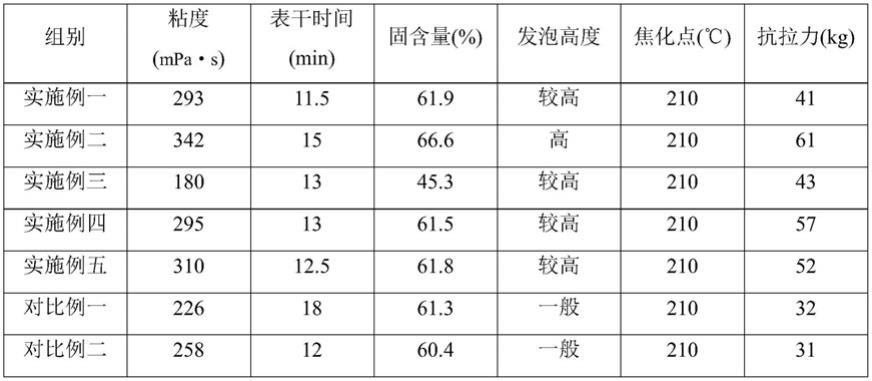
1.本发明涉及一种粘接能力强的单组分聚氨酯发泡胶及其制备方法,属于聚氨酯发泡胶技术领域。
背景技术:
2.聚氨酯发泡胶是气雾技术和聚氨酯泡沫技术交叉结合的产物,通过将聚氨酯预聚体、发泡剂、催化剂等组分装填于耐压气雾罐中,当物料从气雾罐中喷出时,沫状的聚氨酯物料会迅速膨胀并与空气中的水分发生固化反应形成泡沫。由于该聚氨酯发泡胶对一般的建筑材料均具有较高的粘附性,广泛应用于建筑、门窗等的密封堵漏、填空补缝、固定粘结、保温隔音等方面。
3.现有技术中,单组分聚氨酯发泡胶通常由聚酯多元醇树脂、聚醚多元醇树脂等与异氰酸酯反应,再辅以其他助剂形成发泡胶产品,这类聚氨酯发泡胶的制备成本相对较高,在减小聚氨酯发泡胶的原料中聚酯、聚醚多元醇树脂的含量比例,加入替代物时,则会降低单组分聚氨酯发泡胶的粘接能力及发泡高度,影响聚氨酯发泡胶的使用性能。
技术实现要素:
4.本发明的目的在于克服现有技术的不足,提供一种成本低、发泡高度好、粘接能力强的单组分聚氨酯发泡胶及其制备方法。
5.本发明的目的是通过以下技术方案来实现的:一种粘接能力强的单组分聚氨酯发泡胶,按重量百分比计,包括1~5%的松香树脂、1~5%的聚醚多元醇、1~5%的氨基树脂、15~35%的组合料树脂、30~52%的溶剂、18~28%的异氰酸酯和0.02~0.4%的催化剂,所述组合料树脂为再生料合成的聚酯或聚醚多元醇。
6.进一步的,所述的聚醚多元醇的羟值为30~38mgkoh/g,酸值≤0.1mgkoh/g,官能度为3。
7.进一步的,所述组合料树脂的羟值为30~60mgkoh/g,酸值≤3mgkoh/g。
8.进一步的,所述的氨基树脂为异丁醚化氨基树脂,所述氨基树脂的酸值≤0.1mgkoh/g、固含量为56~68%、容忍度为7~12。
9.进一步的,所述的松香树脂为c9松香树脂、松香424中的任意一种或两种。
10.进一步的,所述的溶剂为二氯甲烷。
11.进一步的,所述催化剂为双吗啉和有机锡催化剂中的任意一种或两种。
12.进一步的,按重量百分比计,所述的催化剂包括0.01~0.2%的双吗啉和0.01~0.2%的有机锡催化剂。
13.本发明还提供一种上述粘接能力强的单组分聚氨酯发泡胶的制备方法,称取各重量比例的原料,将松香树脂溶解于溶剂内,加入聚醚多元醇、氨基树脂和组合料树脂,搅拌均匀后继续加入异氰酸酯搅拌均匀,然后加入催化剂,搅拌均匀并过滤,即得。
14.本发明的有益效果是:
15.通过在配方中采用松香树脂、氨基树脂和组合料树脂与聚醚多元醇复配,减少了现有配方中聚醚多元醇树脂的用量,有利于降低所制备聚氨酯发泡胶的造价成本。组合料树脂是由废瓶片等为主要原材料合成的一种聚酯或聚醚多元醇,其价格明显低于聚醚多元醇树脂,含有能够与
‑
nco基团反应的羟基,得到端基为异氰酸基的聚氨酯预聚体,配以聚醚多元醇以提高聚氨酯发泡胶的润湿能力。同时,氨基树脂中的氨基与异氰酸根的反应活性较大,其能够与异氰酸根在更低的温度下反应生成缩二脲等交联结构,再与松香树脂复配,有利于降低组合料树脂生成的聚氨酯预聚体生成聚氨酯的反应条件、提高单组分聚氨酯发泡胶的发泡高度和粘接能力,使本发明采用组合料树脂量较多、聚醚多元醇量较少的配方所制备的聚氨酯发泡胶依然具有良好的发泡和粘接能力。本发明的制备方法简单、加工效率高、对设备要求低,制备得到的单组分聚氨酯发泡胶质量稳定。
具体实施方式
16.下面将结合实施例,对本发明的技术方案进行清楚、完整地描述,显然,所描述的实施例仅仅是本发明一部分实施例,而不是全部的实施例。基于本发明中的实施例,本领域技术人员在没有付出创造性劳动的前提下所获得的所有其他实施例,都属于本发明保护的范围。
17.本发明提供一种技术方案:一种粘接能力强的单组分聚氨酯发泡胶,按重量百分比计,包括1~5%的松香树脂、1~5%的聚醚多元醇、1~5%的氨基树脂、15~35%的组合料树脂、30~52%的溶剂、18~28%的异氰酸酯和0.02~0.4%的催化剂。其中,本发明配方中采用的松香树脂为c9松香树脂、松香424中的任意一种或两种,这两种松香树脂均为常见的市售产品。聚醚多元醇选择采用羟值为30~38mgkoh/g,酸值≤0.1mgkoh/g,官能度为3的市售产品。组合料树脂为由再生料合成的聚酯或聚醚多元醇,是由废瓶片等回收再生料为主要原材料合成的一种聚酯或聚醚多元醇,可替代聚酯、聚醚多元醇与异氰酸酯进行反应,可选择采用羟值为30~60mgkoh/g,酸值≤3mgkoh/g的组合料树脂。氨基树脂则可采用油性油漆专用异丁醚化氨基树脂,选择酸值≤0.1mgkoh/g、固含量为56~68%、容忍度为7~12的氨基树脂市售产品。溶剂可采用沸点较低、易挥发的二氯甲烷,其具有不易燃、毒性较低等特点,在聚氨酯发泡胶热压时还可作为发泡剂使用。异氰酸酯可采用二苯基甲烷二异氰酸酯或甲苯二异氰酸酯等中的一种。这里的催化剂可采用双吗啉和有机锡催化剂中的任意一种或两种,优选地,按重量百分比计,催化剂包括0.01~0.2%的双吗啉和0.01~0.2%的有机锡催化剂。
18.本发明还提供一种上述粘接能力强的单组分聚氨酯发泡胶的制备方法,按上述配方称取各重量比例的原料,先将松香树脂溶解于溶剂内,再加入聚醚多元醇、氨基树脂和组合料树脂,搅拌均匀后继续加入异氰酸酯搅拌均匀,然后加入催化剂,搅拌均匀并过滤,即得。
19.实施例一
20.本实施例提供一种粘接能力强的单组分聚氨酯发泡胶,该单组分聚氨酯发泡胶的原料配方按照重量百分比计,包括1%的松香树脂、35%的二氯甲烷、2.7%的聚醚多元醇、1%的氨基树脂、35%的组合料树脂、25%的异氰酸酯、0.1%的双吗啉和0.2%的有机锡催化剂。本实施例采用的松香树脂为松香树脂424,聚醚多元醇为聚醚多元醇330n,氨基树脂
为氨基树脂yc
‑
017,组合料树脂为兰歌45#组合料树脂,异氰酸酯为二苯基甲烷二异氰酸酯,双吗啉为双吗啉cy204,有机锡催化剂为有机锡催化剂t
‑
12。
21.上述单组分聚氨酯发泡胶的制备方法过程如下:按重量百分比称取各原料后,将松香树脂溶解于二氯甲烷中,再加入聚醚多元醇、氨基树脂和组合料树脂并搅拌均匀,然后加入异氰酸酯搅拌均匀,最后加入双吗啉和有机锡催化剂搅拌均匀,用120目的滤网过滤,即得。
22.实施例二
23.本实施例与实施例一的区别主要在于:本实施例的原料配方按照重量百分比计,包括3.8%的松香树脂、30%的二氯甲烷、1%的聚醚多元醇、5%的氨基树脂、32%的组合料树脂、28%的异氰酸酯、0.01%的双吗啉和0.19%的有机锡催化剂。本实施例采用的松香树脂为c9松香树脂。
24.实施例三
25.本实施例与实施例一的区别主要在于:本实施例的原料配方按照重量百分比计,包括5%的松香树脂、52%的二氯甲烷、5%的聚醚多元醇、4.8%的氨基树脂、15%的组合料树脂、18%的异氰酸酯、0.19%的双吗啉和0.01%的有机锡催化剂。
26.实施例四
27.本实施例与实施例一的区别主要在于:本实施例的原料配方按照重量百分比计,包括2%的松香树脂、35%的二氯甲烷、3%的聚醚多元醇、3%的氨基树脂、31.7%的组合料树脂、25%的异氰酸酯、0.2%的双吗啉和0.1%的有机锡催化剂。
28.实施例五
29.本实施例与实施例一的区别主要在于:本实施例的原料配方按照重量百分比计,包括2%的松香树脂、35%的二氯甲烷、3%的聚醚多元醇、3%的氨基树脂、31.9%的组合料树脂、25%的异氰酸酯、0.05%的双吗啉和0.05%的有机锡催化剂。本实施例采用的松香树脂为c9松香树脂。
30.对比例一
31.本对比例提供一种单组分聚氨酯发泡胶,其原料配方以重量百分比计,包括35%的二氯甲烷、4%的聚醚多元醇、35.9%的组合料树脂、25%的异氰酸酯、0.05%的双吗啉和0.05%的有机锡催化剂。
32.对比例二
33.本对比例的单组分聚氨酯发泡胶为直接购买的市售聚氨酯发泡胶。
34.产品检测
35.粘度:在室内常温环境条件下,用旋转式粘度计对产品试样的粘度进行检查,在直径≥6cm,高度≥11cm的容器中,将粘度计的测试转子垂直浸入试样中心部位,并使液面达到转子液位标线处;开启粘度计进行测试,并读取显示不变时的读数,每个试样测定三次并以算术平均值表示。
36.表干时间:将产品试样均匀地涂刮于清洁的刮表细度计表面,在空气流通相对平缓的自然环境下,要求0.1
‑
0.3mm厚度的产品试样在放置一定时间后,以裁切光滑的瓦楞纸立面从约3cm高处自由落体至产品试样表面,无粘接拉丝现象。
37.焦化点:使用鼓风干燥箱对规定容器内3mm厚的产品试样,进行高温温度烘烤,经
过20min的高温烘烤后,产品试样仍呈浅棕色或褐色,并不允许出现焦化现象。
38.固含量:将2.0
±
0.5g重量的产品试样,置于已称量的培养皿中,使试样均匀地流布于容器的底部;在105
±
2℃的高温下烘烤30min后,取出放入干燥器中冷却至室温后称量;然后再在105
±
2℃的高温下烘烤10min后,取出放入干燥器中冷却至室温后称量,至前后两次称量的差≤0.01g为止;根据产品试样试验前后的比值,得出其固含量值。
39.发泡高度:目测。
40.抗拉力:
41.1、抗拉力要求:
42.1)、发泡胶在热压,并经过高温(焦化点温度)烘烤后,抗拉力应大于规定数值。
43.2)、当拉力小于规定数值10kg内,则根据蜂窝纸断裂进行判定
44.a、蜂窝纸纤维断裂,且蜂窝纸与胶水黏结紧密,则为合格。
45.b、蜂窝纸与胶水脱落,无蜂窝纸断裂在胶体上,则为不合格。
46.2、试验方法
47.以0.5mm厚度板材经过前处理后,制作成有效面积为120mm*170mm的样板,按照正常生产流程,使用生产用发泡胶刮板在样板表面均匀刷上一层产品试样,将蜂窝纸固定于样板中,将样板经过热压后常温放置大于4小时,再放置于焦化点温度恒温烤箱高温烘烤25min,烘烤完成后放置于常温下温度平衡大于1小时;分别使用万能试验机对热压后和烘烤后的样板进行拉力测试。
48.根据上述方法对实施例一至五及对比例一和二的单组分聚氨酯发泡胶产品进行性能检测,检测结果如表1所示。
49.表1各实施例和对比例的检测结果
[0050][0051]
由表1可见,由本发明五个实施例制备的单组分聚氨酯发泡胶产品的抗拉力及粘度明显高于对比例一和对比例二,其发泡高度也明显高于对比例一,可见通过加入的氨基树脂与松香树脂的复配,在发泡胶内起交联作用,对发泡胶的粘接能力和发泡高度均有改善作用。
[0052]
以上所述仅是本发明的优选实施方式,应当理解本发明并非局限于本文所披露的形式,不应看作是对其他实施例的排除,而可用于各种其他组合、修改和环境,并能够在本文所述构想范围内,通过上述教导或相关领域的技术或知识进行改动。而本领域人员所进
行的改动和变化不脱离本发明的精神和范围,则都应在本发明所附权利要求的保护范围内。