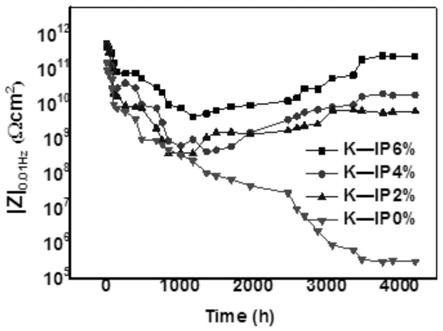
1.本发明涉及防锈技术领域,尤其是涉及一种防锈剂及其制备方法和应用。
背景技术:
2.基材的锈蚀是影响基材性能的重要因素,也是基材报废成本提高的重要来源。通常情况下,锈蚀的基材为金属基材,当金属基材在外界环境中经受水分侵蚀、氧化反应等情况下容易出现锈蚀。为了降低基材的锈蚀程度,在基材表面形成防护涂层是较为有效的办法。但是在传统的方法中,在锈蚀基材表面形成防护涂层时,需要对基材表面进行严格复杂的表面预处理,以使基材表面满足形成防护涂层的条件。比如,在使用传统的防锈剂时,为了使防护涂层能够较好地作用于基材表面,需要使处理之后的表面状态达到gb8923《涂装前钢材表面锈蚀等级和除锈等级》中st3或sa1等级后,才可以在锈蚀基材表面形成有效的防护涂层。严格复杂的表面预处理给施工带来了较大的难度,导致工作人员的工作强度大,特别是当外界环境恶劣、基材表面形状不规整的情况下,基材的表面预处理尤为困难。
技术实现要素:
3.基于此,有必要提供一种能够在带锈基材表面形成防护涂层的防锈剂、所述防锈剂的制备方法以及应用。所述防锈剂能够在带锈基材表面形成防护涂层,可以大大降低表面预处理的难度。
4.为了解决以上技术问题,本发明的技术方案为:
5.一种防锈剂,由包括如下质量份数的各原料制成:
6.植酸钾
ꢀꢀꢀꢀꢀ
2份~8份、
7.环氧树脂
ꢀꢀꢀ
25份~35份、以及
8.溶剂
ꢀꢀꢀꢀꢀꢀꢀ
8份~15份。
9.在其中一个实施例中,所述防锈剂由包括如下质量份数的各原料制成:
10.植酸钾
ꢀꢀꢀꢀꢀ
4份~8份、
11.环氧树脂
ꢀꢀꢀ
28份~32份、以及
12.溶剂
ꢀꢀꢀꢀꢀꢀꢀ
10份~12份。
13.在其中一个实施例中,所述溶剂为二甲苯和/或正丁醇。
14.在其中一个实施例中,所述溶剂由二甲苯和正丁醇按照质量比为7:(2~5)混合而成。
15.一种上述任一实施例中所述的防锈剂的制备方法,包括如下步骤:
16.对所述植酸钾、所述环氧树脂以及所述溶剂按照各自的质量份数备料;
17.将所述植酸钾、所述环氧树脂以及所述溶剂进行研磨处理。
18.在其中一个实施例中,所述研磨处理的温度为15℃~25℃。
19.在其中一个实施例中,所述研磨处理的为球磨处理;所述球磨处理的转速为100r/min~600r/min,所述球磨处理的时间为1.5h~3h。
20.一种上述任一实施例中所述的防锈剂在带锈基材表面形成防护涂层的应用,所述应用包括如下步骤:
21.将所述防锈剂与固化剂混合,得到第一混合料;
22.对所述第一混合料进行静置处理,得到静置料;
23.将所述静置料与消泡剂混合,得到第二混合料;
24.将所述第二混合料涂覆于带锈基材的表面。
25.在其中一个实施例中,所述固化剂与所述环氧树脂的质量比为1:(1~5)。
26.在其中一个实施例中,所述静置处理包括如下步骤:将所述第一混合料在真空环境下静置8min~15min;和/或,
27.形成所述真空环境的抽真空时间为3min~8min。
28.上述防锈剂由包括质量份数分别为2份~8份的植酸钾、25份~35份的环氧树脂以及8份~15份的溶剂的原料制备而成。在该防锈剂的原料中,通过植酸钾、环氧树脂以及溶剂的配合,可以形成对基材表面锈层具有良好的渗透性、且能够在锈层以及基材表面形成稳定致密结构防护涂层的防锈剂。在使用该防锈剂时,不需要对带锈基材表面进行严格复杂的表面预处理,就可以在带锈基材的表面形成稳定致密的防护涂层,有效降低带锈基材表面预处理的难度,简化施工要求。另外,本实施例中的防锈剂在带锈基材表面具有良好的渗透性,可以在很好地渗入锈层内,起到更好地防护效果。
附图说明
29.图1为典型南海岛礁设备的锈蚀示例;
30.图2为另一典型南海岛礁设备的锈蚀示例;
31.图3中a为本发明实施例1中带锈基材的表面示意图,图3中b为带锈基材表面形成防护涂层之后的示意图;
32.图4中a为对比例1中形成的防护涂层的截面示意图,图4中b为实施例1中形成的防护涂层的截面示意图;
33.图5中a为对比例1中形成的防护涂层下方的基材的表面示意图,图5中b为实施例1中形成的防护涂层下方的基材的表面示意图;
34.图6中a为对比例1中形成的防护涂层下方的锈层的表面示意图,图6中b为实施例1中形成的防护涂层下方的锈层的表面示意图;
35.图7为防护涂层的电化学阻抗谱。
具体实施方式
36.为使本发明的上述目的、特征和优点能够更加明显易懂,下面对本发明的具体实施方式做详细的说明。在下面的描述中阐述了很多具体细节以便于充分理解本发明。但是本发明能够以很多不同于在此描述的其它方式来实施,本领域技术人员可以在不违背本发明内涵的情况下做类似改进,因此本发明不受下面公开的具体实施例的限制。
37.除非另有定义,本文所使用的所有的技术和科学术语与属于本发明的技术领域的技术人员通常理解的含义相同。本文中在本发明的说明书中所使用的术语只是为了描述具体的实施例的目的,不是旨在于限制本发明。本文所使用的术语“和/或”包括一个或多个相
关的所列项目的任意的和所有的组合。
38.本发明一实施例提供了一种防锈剂。该防锈剂由包括如下质量份数的各原料制成:植酸钾2份~8份、环氧树脂25份~35份、以及溶剂8份~15份。在该防锈剂的原料中,通过植酸钾、环氧树脂以及溶剂的配合,可以形成对基材表面锈层具有良好的渗透性、且能够在锈层以及基材层形成稳定致密结构防护涂层的防锈剂。在使用该防锈剂时,不需要对带锈基材表面进行严格复杂的表面预处理、不需要使基材的表面状态达到gb8923《涂装前钢材表面锈蚀等级和除锈等级》中的st或sa等级就可以在带锈基材的表面形成稳定致密的防护涂层,有效降低带锈基材表面预处理的难度,简化施工要求。另外,本实施例中的防锈剂在带锈基材表面具有良好的渗透性,可以在很好地渗入锈层内,起到更好地防护效果。
39.在一个具体的示例中植酸钾、环氧树脂以及溶剂的质量比为11:30:(2~8)。
40.发明人在对防锈剂进行探索的过程中发现,在本实施例中,植酸钾呈中性,可以大量存在于环氧树脂体系中,形成相应浓度的稳定的防锈剂。另外,植酸钾结构中具有如式(1)所示的平面结构基团。该基团能够和金属离子形成结构紧密的螯合物,比如,该基团可以和fe
3+
、ca
2+
、mg
2+
等金属离子形成结构紧密的螯合物。该基团的存在可以促使本实施例中的防锈剂能够在带锈基材的表面形成防护涂层。进一步地,采用植酸钾2份~8份、环氧树脂25份~35份、以及溶剂8份~15份的配比,得到可以在带锈基材表面形成防护涂层,且渗透性好、便于涂装的防锈剂。更进一步地,为了进一步提高本实施例中防锈剂的防护效果,采用本实施例中的防锈剂对带锈基材的表面进行涂装时,可以对带锈基材的表面进行简单的浮锈处理,进行一定的初步打磨操作即可。此时经过初步打磨之后的基材表面的状态低于gb8923《涂装前钢材表面锈蚀等级和除锈等级》中st或sa等级的要求。初步打磨之后,采用本实施例中的防锈剂进行涂装即可。
[0041][0042]
可以理解的是,本实施例中的防锈剂可以用于日常生产和生活中的锈蚀金属设备表面的带锈防护,还可以适用于环境恶劣的户外条件下的锈蚀金属设备表面的带锈防护。比如在热带海洋性气候的环境下,金属设备长时间处于高温、高湿、高盐和强太阳辐射的环境,锈蚀速度更快,锈蚀问题明显,此时对于金属设备的防护更为困难。当采用的传统的方式进行防护处理时,需要对锈蚀的金属设备表面进行严格复杂的表面预处理,此时需要大量的人力参与。并且在金属设备的异形区域,比如弯曲、焊接、铰接或铆接等复杂的形状和连接的位置处,更加难以对这些位置进行有效的表面预处理。此时传统的防护方式难以形成有效的防护层,即使是形成防护层之后,由于金属设备表面的状态难以达到处理要求,导致形成的防护层容易脱落,进而失去防护效果。
[0043]
因此,本发明还有一实施例提供了一种适用于热带海洋性气候环境下金属防锈的防锈剂,该防锈剂由包括如下质量份数的各原料制成:植酸钾2份~8份、环氧树脂25份~35份、以及溶剂8份~15份。
[0044]
进一步地,请参阅图1和图2。图1和图2分别示出了两个典型南海岛礁金属设备的锈蚀示例。南海岛礁气候恶劣,在设备表面容易出现锈蚀的问题。采用传统的方式在设备表面形成防护层之后,防护层在恶劣的气候条件下容易出现鼓泡、粉化以及漆膜脱落的问题,导致设备继续锈蚀。此时,采用传统的方法对设备进行防护时,需要对设备表面至少进行打磨除锈处理,使设备表面状态达到gb8923《涂装前钢材表面锈蚀等级和除锈等级》中的st或sa等级的要求之后才能够进行涂装。而南海岛礁环境条件差,对设备的打磨除锈需要投入大量的人力物力,且工况条件差,工作人员的工作强度很大。
[0045]
对于南海岛礁设备容易出现锈蚀、且防锈处理工作强大的问题。本发明一实施例提供了一种适用于南海岛礁金属防锈的防锈剂,该防锈剂由包括如下质量份数的各原料制成:植酸钾2份~8份、环氧树脂25份~35份、以及溶剂8份~15份。采用该防锈剂能够在南海岛礁恶劣的环境条件下,对锈蚀金属进行带锈涂装,在带锈金属的表面形成防护涂层,不需要对金属进行严格且复杂的表面预处理,在较差的表面状态下即可以对金属进行涂装,进而起到良好的防护效果。并且防锈剂对锈层具有良好的渗透效果,可以使防锈剂很好地适于表面形状不规整的基材,在不规整的表面形成稳定的防护涂层。
[0046]
进一步地,防锈剂由质量份数分别为2份~8份的植酸钾、25份~35份的环氧树脂以及8份~15份的溶剂制备而成。在该示例中,仅以植酸钾、环氧树脂以及溶剂按照质量份数分别为2份~8份、25份~35份以及8份~15份即可以制成能够在带锈基材表面形成防护涂层的防锈剂。
[0047]
可以理解的是,作为植酸钾的一些具体质量份数,植酸钾的质量份数可以是但不限定为2份、2.5份、3份、3.5份、4份、4.5份、5份、5.5份、6份、6.5份、7份、7.5份或8份。作为环氧树脂的一些具体质量份数,环氧树脂的质量份数可以是但不限定为25份、26份、27份、28份、29份、30份、31份、32份、33份、34份或35份。作为溶剂的一些具体质量份数,溶剂的质量份数可以是但不限定为8份、9份、10份、11份、12份、13份、14份或15份。还可以理解的是,在防锈剂的原料备料时,植酸钾、环氧树脂以及溶剂的质量份数可以在以上所列出的各质量份中对应地进行选择或形成相应的质量份数范围,以用来作为防锈剂的制备原料。
[0048]
在一个具体的示例中,防锈剂由包括如下质量份数的各原料制成:植酸钾4份~8份、环氧树脂28份~32份、以及溶剂10份~12份。
[0049]
进一步地,防锈剂由质量份数分别为4份~8份的植酸钾、28份~32份的环氧树脂以及10份~12份的溶剂制备而成。
[0050]
在一个具体的示例中,溶剂为二甲苯和/或正丁醇。在选择溶剂时,可以选择二甲苯作为溶剂,或者选择正丁醇作为溶剂,或者选择二甲苯和正丁醇进行混合得到的混合溶剂作为溶剂。
[0051]
具体地,当溶剂为二甲苯和正丁醇混合而成时。溶剂由二甲苯和正丁醇按照质量比为7:(2~5)混合而成。可选地,在形成混合溶剂时,二甲苯和正丁醇的质量比可以是但不限定为7:2、7:3、7:4或7:5。更具体地,溶剂由二甲苯和正丁醇按照质量比为7:3混合而成。
[0052]
在一个具体的示例中,防锈剂还包括固化剂,固化剂与环氧树脂的质量比为1:(1
~5)。通过在防锈剂中添加固化剂,在使防锈剂具有一定的粘度的基础上保持一定的流动性,便于将防锈剂涂装在带锈基材的表面。可选地,固化剂与环氧树脂的质量比为1:1、1:1.5、1:2、1:2.5、1:3、1:3.5、1:4、1:4.5或1:5。进一步可选地,固化剂为聚酰胺固化剂651。具体地,固化剂与环氧树脂的质量比为1:2。
[0053]
在一个具体的示例中,防锈剂还包括质量份数为0.05份~0.15份的消泡剂。消泡剂的加入可以使防锈剂具有更好地涂覆性能,便于在带锈基材的表面进行涂覆。具体地,消泡剂的质量份数可以是但不限定为0.05份、0.06份、0.07份、0.08份、0.09份、0.1份、0.11份、0.12份、0.13份、0.14份或0.15份。可选地,消泡剂采用本领域常规消泡剂即可。
[0054]
本发明还有一个实施例提供了一种上述防锈剂的制备方法。该防锈剂的制备方法包括如下步骤:对植酸钾、环氧树脂以及溶剂按照各自的质量份数备料;将植酸钾、环氧树脂以及溶剂进行研磨处理。
[0055]
在本实施例中,将植酸钾、环氧树脂以及溶剂分别按照2份~8份、25份~35份以及8份~15份的质量份数进行备料。然后将植酸钾、环氧树脂以及溶剂进行研磨处理,此时能够使植酸钾、环氧树脂以及溶剂保持均匀地混合。尤其是使植酸钾在环氧树脂中分散均匀,可以在保证良好涂覆、防锈的基础上,提高防护涂层的屏蔽性能,进而进一步实现对基材表面锈层进行结构上的转化,进一步提高涂层的防护性能。
[0056]
进一步地,研磨处理的温度为15℃~25℃,通过对研磨温度进行控制,使各原料稳定地混合,在保持植酸钾、环氧树脂以及溶剂自身性能的基础上实现更好地混合。可选地,研磨处理的温度为15℃、16℃、17℃、18℃、19℃、20℃、21℃、22℃、23℃、24℃或25℃。
[0057]
作为研磨处理的一种具体形式,研磨处理的为球磨处理。具体地,球磨处理的转速为100r/min~600r/min,球磨处理的时间为1.5h~3h。
[0058]
可选地,球磨处理的转速为100r/min、150r/min、200r/min、250r/min、300r/min、350r/min、400r/min、450r/min、500r/min、550r/min或600r/min。球磨处理的时间为1.5h、2h、2.5h或3h。
[0059]
在一个具体的示例中,研磨处理之后还包括如下步骤:对研磨处理得到的混合物进行过滤处理,得到滤液。以滤液作为防锈剂进行涂覆。
[0060]
除了以上各实施例和示例中的防锈剂、以上各实施例和示例中的防锈剂的制备方法,本发明还有一实施例提供了一种以上防锈剂在带锈基材表面形成防护涂层的应用。该应用包括如下步骤:将防锈剂与固化剂混合,得到第一混合料;对第一混合料进行静置处理,得到静置料;将静置料与消泡剂混合,得到第二混合料;将第二混合料涂覆于带锈基材的表面。
[0061]
本实施例中的应用,可以将防锈剂在带锈基材表面进行涂装,不需要基材表面具有严格的表面状态,不需要预先对基材表面进行复杂的表面处理可以大大简化涂装的预处理,降低工作人员的工作强度。将防锈剂涂装在带锈基材表面形成防护涂层时,将防锈剂与固化剂混合,得到第一混合料,使防锈剂具有一定的粘度和流动性,便于将防锈剂在带锈基材表面进行涂覆,进而形成防护涂层。
[0062]
在一个具体的示例中,将防锈剂与固化剂混合之前还包括如下步骤:对防锈剂进行过滤处理。然后将滤液与固化剂混合。
[0063]
在一个具体的示例中,将防锈剂与固化剂混合时,固化剂与环氧树脂的质量比为
1:(1~5)。可选地,固化剂与环氧树脂的质量比为1:1、1:1.5、1:2、1:2.5、1:3、1:3.5、1:4、1:4.5或1:5。
[0064]
进一步地,将静置料与消泡剂混合时,消泡剂的质量份数为0.05份~0.15份。具体地,消泡剂的质量份数可以是但不限定为0.05份、0.06份、0.07份、0.08份、0.09份、0.1份、0.11份、0.12份、0.13份、0.14份或0.15份。
[0065]
作为静置处理的一个具体示例,静置处理包括如下步骤:将第一混合料在真空环境下静置8min~15min。可以理解的是,在实际操作过程中,可以将第一混合料放置在真空室内进行静置处理,控制静置的时间为8min~15min。还可以将防锈剂与固化剂在真空环境下混合,然后静置。比如,将防锈剂与固化剂在真空室内混合,然后在真空室内静置。可选地,将第一混合料在真空环境下静置的时间可以是8min、9min、10min、11min、12min、13min、14min或15min。
[0066]
进一步地,形成真空环境的抽真空时间为3min~8min。具体地,抽真空的时间可以是但不限定为3min、4min、5min、6min、7min或8min。
[0067]
以下为具体实施例。
[0068]
实施例1
[0069]
本实施例中防锈剂的原料为植酸钾1.08g、环氧树脂15g以及溶剂5.5g。其中溶剂由3.85g二甲苯和1.65g正丁醇混合而成。
[0070]
本实施例中固化剂为聚酰胺固化剂651,固化剂7.5g。本实施例中消泡剂为0.05g。
[0071]
本实施例中的防锈剂的制备方法为:
[0072]
s101:对植酸钾、环氧树脂以及溶剂按照上述质量备料。
[0073]
s102:将植酸钾、环氧树脂以及溶剂加入球磨机中,控制球磨的温度为15℃,控制球磨处理的转速为300r/min,球磨处理的时间为2.5h。
[0074]
本实施例中防锈剂在带锈基材表面形成防护涂层的应用包括如下步骤:
[0075]
s201:对s102中得到的防锈剂进行过滤处理,采用不锈钢滤网过滤,得到滤液。
[0076]
s202:将s201中得到的滤液与固化剂混合,搅拌15min,使滤液与固化剂混合均匀,得到第一混合料。
[0077]
s203:将s202中得到的第一混合料在真空室内静置处理。其中抽真空时间5min,静置10min,得到静置料。
[0078]
s204:将s203中得到的静置料与消泡剂混合,得到第二混合料。
[0079]
s205:将s204中得到的第二混合料涂覆于带锈的南海岛礁环境下锈蚀的q235钢基材表面,得到防护涂层。
[0080]
其中,s205中没有涂覆第二混合料之前的钢基材的表面如图3中a所示,形成防护涂层之后的表面如图3中b所示。在图3中a示出的涂覆之前的钢基材表面为带锈状态,没有经过严格的表面预处理,此时钢基材的表面有较多的锈蚀残留,表面状态低于gb8923《涂装前钢材表面锈蚀等级和除锈等级》中的st等级。采用第二混合料直接在钢基材表面进行涂覆,涂覆之后得到如图3中b所示的表面。
[0081]
对比例1
[0082]
与实施例1相比,对比例1的不同之处在于,在防锈剂中不含有植酸钾。
[0083]
测试例1
[0084]
将实施例1和对比例1中涂覆之后得到的防护涂层、钢基材表面以及锈层进行分析。其中,对比例1中涂层的截面示意图如图4中a所示,实施例1中涂层的截面示意图如图4中b所示。
[0085]
将实施例1和对比例1中涂覆之后的基材在3.5%nacl水溶液中浸泡800h,测试涂层下方的钢基材的表面形貌,以及测试涂层下方的锈层的表面形貌。其中对比例1中涂层下方的钢基材的表面示意图如图5中a所示,实施例1中涂层下方的钢基材的表面示意图如图5中b所示。对比例1中涂层下方的锈层的表面示意图如图6中a所示,实施例1中涂层下方的锈层的表面示意图如图6中b所示。
[0086]
由图4可以看出,对比例1中得到的防护涂层中存在较多的空隙和裂纹,涂层缺陷较多,实施例1中得到的防护涂层空隙和裂纹都较少,且植酸钾在涂层中分散均匀。与对比例1相比,实施例1中得到的防护涂层具有更好地致密性。
[0087]
由图5可以看出,与对比例1相比,实施例1中涂层下方的钢基材的表面更加致密。涂层下方的钢基材表面的锈蚀程度较对比例1明显降低。
[0088]
由图6可以看出,对比例1中涂层下方的锈层明显疏松,实施例1中涂层下方的锈层则更加致密。表明实施例1中防锈剂能够与锈层形成致密的结构,这样可以在带锈的情况下使钢基材保持良好的防锈性能。
[0089]
测试例2
[0090]
分别配置不同植酸钾浓度的防锈剂,并按照实施例1中的方法在相同的钢基材表面进行涂覆。其中不同植酸钾浓度的防锈剂分别为:植酸钾浓度为0%(即对比例1中的防锈剂)、2%、4%、6%。实施例1中植酸钾的浓度为5%。
[0091]
将不同植酸钾浓度的防锈剂形成防护涂层之后的钢基材分别在3.5%nacl水溶液中浸泡3500h,并分别测试电化学阻抗图谱,结果如图7所示。由图7可以看出,在浸泡的处事阶段,低频阻抗模值均较高,说明耐锈蚀性良好。随着时间的延长,低频阻抗模值呈现一定的下降。尤其是在50h以后,低频阻抗模值均开始下降,而添加有植酸钾的防锈剂涂覆的基材表现为先降低,后升高,最后趋于稳定的趋势,表明防锈剂具有良好的防锈蚀性能,且植酸钾浓度为6%时,低频阻抗模值最高,说明植酸钾浓度为6%时,对涂层的耐锈蚀性能提高效果更加明显。
[0092]
以上所述实施例的各技术特征可以进行任意的组合,为使描述简洁,未对上述实施例中的各个技术特征所有可能的组合都进行描述,然而,只要这些技术特征的组合不存在矛盾,都应当认为是本说明书记载的范围。
[0093]
以上所述实施例仅表达了本发明的几种实施方式,其描述较为具体和详细,但并不能因此而理解为对发明专利范围的限制。应当指出的是,对于本领域的普通技术人员来说,在不脱离本发明构思的前提下,还可以做出若干变形和改进,这些都属于本发明的保护范围。因此,本发明专利的保护范围应以所附权利要求为准,说明书及附图可以用于解释权利要求的内容。