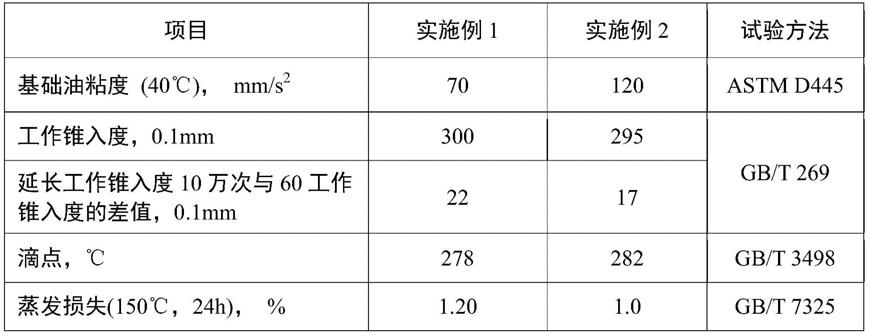
1.本发明涉及润滑脂技术领域,尤其涉及一种汽车滚珠式单向离合器用润滑脂组合物及其制备方法和应用。
背景技术:
2.汽车起动机单向离合器的种类有滚珠式单向离合器,摩擦片式单向离合器和弹簧式单向离合器。从目前起动机的生产趋势来看摩擦片式单向器逐渐减少趋向被淘汰。这是由于其结构复杂,摩擦片的制造工艺要求高,使用中容易发生打滑等缺陷所决定的。滚珠式单向离合器的结构已有九十余年的历史,但其发展特别是在汽车起动机中的应用存在争议,例如在苏联与东欧民主国家的汽车电气设备专业书上的观点是滚珠式单向离合器只适用于4马力以下的起动机。但是近年来无论是从理论分析或生产实践的发展都证明了滚珠式单向离合器既适用于小马力起动机也适用于大马力起动机。多个汽车生产厂家已将滚柱单向器大量用于10马力以上的起动机。
3.目前滚珠式单向离合器由于其结构简单但是性能稳定,得以广泛应用于家用汽车,但是现有技术中针对于滚珠式单向离合器的研究仍不够透彻,针对应用于汽车起动机的滚珠式单向离合器的润滑脂的研究也不充分,缺少能够满足滚珠式单向离合器要求的润滑脂。
技术实现要素:
4.为了解决现有技术存在的问题,本发明提供一种润滑脂组合物及其制备方法和应用,采用以硅油为主的基础油,并且额外添加磷盐作为固体剂,制备得到一种具有较大摩擦系数的润滑脂组合物,该润滑脂组合物可以有效延长起动机的滚珠式单向离合器的使用寿命。
5.第一方面,本发明提供一种润滑脂组合物,包括:基础油和固体剂;
6.所述基础油包括硅油;所述固体剂包括磷酸盐;
7.所述硅油占所述基础油的1/2~3/4,所述磷酸盐占所述固体剂的 1/3~2/3;所述基础油和所述固体剂的质量比为(8~12):(1~2)。
8.优选为(10~12):(1~2)。
9.起动机单向离合器的作用是在起动过程中可靠地传递起动机发出的扭矩给发动机的曲轴和发动机被发动后藉其单向作用保护起动机电枢不致因超越引起高速而损坏。因此单向器之性能优劣决定着起动机的可靠性。起动机的驱动齿轮与飞轮齿圈啮合的瞬间,冲击载荷很大;而且需要经受25万次以上的起停耐久测试和低温制动冲击试验,因此需要润滑脂具有较好的抗冲击载荷的能力和较长的使用寿命。
10.目前起动机所需的润滑脂相关的技术公开较少。本发明通过大量研究,总结规律经验,掌握了起动机单向离合器的润滑原理以及润滑脂产品应具有的基本性能,发现针对
于起动机的滚珠式单向离合器而言,润滑脂并非是需要类似于其他结构一样需要较小的摩擦系数,反而是需要较大的摩擦系数,这有助于滚珠在被十字块推入楔形槽的较窄处时能与外壳牢固的卡死,进而带动发动机转动。但是摩擦系数也不能过高,过高反而会影响起动机的滚珠式单向离合器的性能。依据上述发现的原理,本发明提供了一种润滑脂组合物,通过以硅油为主要成分的基础油,以及在润滑脂组合物中添加磷酸盐提升润滑脂的摩擦系数至合适的范围内。进一步地,所述硅油占所述基础油的1/2~3/4,所述磷酸盐占所述固体剂的1/2~2/3。
11.进一步地,所述硅油为二甲基硅油、乙基硅油或苯基硅油中的一种或多种,优选为苯基硅油;所述磷酸盐为磷酸锌、磷酸锂或磷酸铝中的一种或多种,优选为磷酸锌。
12.在实际应用中,苯基硅油在使用时效果较佳,使得润滑脂具备合适的摩擦系数的同时,和其他成分复合使用时,具备较好的抗冲击负荷的能力和使用寿命。
13.进一步地,所述基础油的40℃运动粘度为70.0~120.0mm2/s,低温倾点不高于-50℃。
14.进一步地,所述基础油还包括酯类油或醚类油;所述固体剂还包括碳酸钙或氰尿酸三聚氰胺。
15.基础油中除了硅油外其他成分可以采用酯类油或醚类油,例如二元醇酯、多元醇酯、季戊四醇酯或烷基二苯醚,使其满足用于滚珠式单向离合器的耐低温、抗氧化、使用寿命要求,以及具备合适的摩擦系数。总结而言,本发明通过改进润滑脂中基础油的组成保证润滑脂产品的使用温度达到-50℃~180℃、具有优异的抗氧化性能、长的使用寿命以及较大的摩擦系数。并且在此基础上选用了合适的固体剂,使得产品的具有优异的抗冲击载荷的能力、防锈性能之外,摩擦系数维持在合适的范围内。
16.进一步地,以重量份计,所述润滑脂组合物包括所述基础油 50~80份、氢氧化锂2~5份、稠化剂5~18份、抗氧剂1~5份、防锈剂 1~10份、极压剂1~10份和所述固体剂5~20份。
17.优选地,所述润滑脂组合物包括所述基础油64~75份、氢氧化锂 2.5~3.5份、稠化剂10.5~13.5份、抗氧剂2~3份、防锈剂1~2份、极压剂1~2份和所述固体剂8~12份。
18.进一步地,所述稠化剂由脂肪酸和二元酸组成,所述脂肪酸和二元酸的质量比为(8~10):(2.5~3.5);
19.所述抗氧剂包括胺和酚,所述胺和酚的质量比为1:(0.5~2);
20.所述防锈剂为亚硝酸钠或磺酸盐;
21.所述极压剂为为硫化烯烃或dmtd类极压剂。
22.进一步地,所述脂肪酸为十二羟基硬脂酸、氢化蓖麻油中的一种或两种;所述二元酸为壬二酸、癸二酸或己二酸中的一种或多种;所述胺为苯胺、萘胺中的一种或两种;所述酚为受阻酚类;所述磺酸盐为石油磺酸钙、二壬基萘磺酸锌、二壬基萘磺酸钡或石油磺酸钠中的一种或多种。
23.第二方面,本发明提供所述润滑脂组合物的制备方法,包括:
24.混合稠化剂、部分基础油和氢氧化锂后进行皂化反应;
25.之后加入剩余基础油,在175~185℃条件下恒温20~30min;
26.进一步加入抗氧剂、固体剂、极压剂和防锈剂。
27.进一步地,所述氢氧化锂以碱液的形式进行混合,所用去离子水和氢氧化锂的质量比为(4~6):1。
28.进一步地,所述皂化反应为先加入30%~50%的碱液在90~100℃反应0.5~1小时;后加入剩余碱液,继续反应1~1.5小时;反应完成后在135~140℃条件下恒温30~40min,在205~208℃条件下恒温3~5min;
29.进一步地,所述进一步加入抗氧剂、固体剂、极压剂和防锈剂为在150~155℃条件下加入抗氧剂和固体剂,在80℃以下的条件下加入极压剂和防锈剂。
30.进一步地,本发明进一步提供所述润滑脂组合物作为滚珠式单向离合器的润滑脂中的应用。
31.作为一种优选的具体实施方式,本发明提供润滑脂组合物的制备方法,包括:
32.(1)用80~90℃的去离子水将单水氢氧化锂配成碱液,水的质量是单水氢氧化锂的4~6倍;
33.(2)将脂肪酸和二元酸加入到1/2~2/3基础油中,混合加热至85~ 95℃;脂肪酸溶解后,加入已备好碱液的30~50%,温度控制在90℃~ 100℃,皂化反应0.5~1.0小时;
34.(3)皂化反应完成后加入剩余碱液,继续反应1.0~1.5小时;反应完成后升温至135~140℃,恒温30~40分钟;
35.(4)升温到205~208℃,恒温3~5分钟;
36.(5)加入剩余基础油,175~180℃恒温20~30分钟;
37.(6)降温至150℃~155℃加入抗氧剂和固体剂,继续降温到80℃以下后依次加入极压剂、防锈剂。
38.本发明具备如下优异效果:
39.本发明采用以硅油为主的基础油,并且额外添加磷盐作为固体剂,制备得到一种具有较大摩擦系数的润滑脂组合物,该润滑脂组合尤其适用于起动机的滚珠式单向离合器,可以有效提高其耐用性。
40.除此之外,本发明提供的润滑脂组合物在多种指标上也具备优异的性能,具体如下:
41.1)本发明提供的润滑脂具有优良的启动性能,采用sh/t 0338标准方法测试,-50℃下启动转矩≤500mn
·
m。
42.2)本发明提供润滑脂具有优异的的抗剪切性能,采用gb/t 269 方法,10万次延长工作锥入度与60次工作锥入度差值≤30(0.1mm)。
43.3)本发明提供的润滑脂防锈性能好,采用gb/t 5018测试,所有轴承无锈。
44.4)本发明提供的润滑脂具有优良的极压性能,采用sh/t 0202测试,极压性能(四球机法)pd值≥4904n。
45.5)本发明提供的润滑脂具有优异的抗氧化性能,采用sh/t 0790 测试,氧化诱导期(210℃、o2流量100ml/min、压力3.50mpa)≥120min。
46.6)本发明所制备的润滑脂具有合适的摩擦系数,采用astmd5707测试,摩擦系数(400n、80℃、50hz、1.0mm)在0.30~0.40 范围内。
47.7)起动电机单向离合器耐久测试次数超过25万次,部件无磨损,而且低温制动试验无打滑现象。
具体实施方式
48.以下实施例用于说明本发明,但不用来限制本发明的范围。
49.实施例1
50.本实施例提供一种用于汽车滚珠式单向离合器用润滑脂组合物,具体以重量份计,包括如下成分:
51.十二羟基硬脂酸8份、壬二酸2.5份、氢氧化锂2.5份、抗氧剂2 份、防锈剂1份、极压剂1份、固体剂8份以及基础油70份。
52.其中抗氧剂为苯胺和受阻酚的混合物,两者质量比为1:1;防锈剂为亚硝酸钠;极压剂为硫化烯烃;固体剂为碳酸钙和磷酸盐的混合物,两者质量比为1:1;基础油为季戊四醇酯和苯基硅油的混合物,质量比为1:1。
53.上述组合物通过如下方法制备成润滑脂:
54.(1)用80℃的热水将单水氢氧化锂配成碱液,水的质量是单水氢氧化锂的5倍。
55.(2)将十二羟基硬脂酸、壬二酸加入到2/3基础油中,混合加热至85℃;脂肪酸溶解后,加入已备好碱液的40%,温度控制在80℃,皂化反应0.5小时。
56.(3)皂化反应完成后加入剩余碱液,继续反应1.0小时;反应完成后升温至135℃,恒温30分钟。
57.(4)恒温完成后,开始升温,升温到205℃,恒温3分钟。
58.(5)恒温结束后加入剩余基础油,175℃恒温20分钟。
59.(6)恒温结束后降温,150℃加入抗氧剂和固体剂,继续降温到 80℃以下后依次加入极压剂、防锈剂,搅拌均匀后经过三辊机轧油后灌装。
60.实施例2
61.本实施例提供一种用于汽车滚珠式单向离合器用润滑脂组合物,具体以重量份计,包括如下成分:
62.十二羟基硬脂酸10份、癸二酸3.5份、氢氧化锂3.5份、抗氧剂 3份、防锈剂2份、极压剂2份、固体剂12份以及基础油64份。
63.其中抗氧剂为萘胺和受阻酚的混合物,两者质量比为1:1;防锈剂为磺酸盐;极压剂为dmtd二聚体;固体剂为氰尿酸三聚氰胺和磷酸盐的混合物,两者质量比为1∶1;基础油为多元醇酯和甲基苯基硅油的混合物,质量比为1∶1。
64.上述组合物通过如下方法制备成润滑脂:
65.(1)用90℃的热水将单水氢氧化锂配成碱液,水的质量是单水氢氧化锂的5倍。
66.(2)将十二羟基硬脂酸、癸二酸加入到2/3基础油中,混合加热至95℃;脂肪酸溶解后,加入已备好碱液的40%,温度控制在100℃,皂化反应1小时。
67.(3)皂化反应完成后加入剩余碱液,继续反应1.5小时;反应完成后升温至140℃,恒温40分钟。
68.(4)恒温完成后,开始升温,升温到208℃,恒温5分钟。
69.(5)恒温结束后加入剩余基础油,180℃恒温30分钟。
70.(6)恒温结束后降温,155℃加入抗氧剂和固体剂,继续降温到 80℃以下后依次加入极压剂、防锈剂,搅拌均匀后经过三辊机轧油后灌装。
71.试验例1
72.本试验例针对实施例1-2制备得到的润滑脂组合物进行各项性能的测试,得到如下结果:
73.表1各实施例的润滑脂性能测试结果
[0074][0075][0076]
如上表格中所示,本发明实施例1和2提供润滑脂组合物在各项性能上均合格,尤其是25万次起动机耐久测试,证明了本发明提供的润滑脂组合物适用于起动机的滚珠式单向离合器的要求。
[0077]
试验例2
[0078]
本试验例进一步提供研究过程中涉及的多种润滑脂组合的效果对比,具体包括:
[0079]
润滑脂组合3:十二羟基硬脂酸8份、壬二酸2.5份、氢氧化锂2.5 份、抗氧剂2份、防锈剂1份、极压剂1份、固体剂8份以及基础油 70份。
[0080]
其中抗氧剂为苯胺和受阻酚的混合物,两者质量比为1:1;防锈剂为亚硝酸钠;极压剂为硫化烯烃;固体剂为碳酸钙和氰尿酸三聚氰胺的混合物,两者质量比为1:1;基础油为季戊四醇酯和苯基硅油的混合物,质量比为1:1。
[0081]
润滑脂组合4:十二羟基硬脂酸8份、壬二酸2.5份、氢氧化锂2.5 份、抗氧剂2份、防锈剂1份、极压剂1份、固体剂8份以及基础油 70份。
[0082]
其中抗氧剂为苯胺和受阻酚的混合物,两者质量比为1:1;防锈剂为亚硝酸钠;极压剂为硫化烯烃;固体剂为碳酸钙和磷酸盐的混合物,两者质量比为1:1;基础油为二元醇
酯与乙基硅油的混合物,质量比为1:1。
[0083]
润滑脂组合5:氢化蓖麻油8份、己二酸2.5份、氢氧化锂2.5份、抗氧剂2份、防锈剂1份、极压剂1份、固体剂8份以及基础油70 份。
[0084]
其中抗氧剂为苯胺和受阻酚的混合物,两者质量比为1:1;防锈剂为亚硝酸钠;极压剂为硫化烯烃;固体剂为碳酸钙和磷酸盐的混合物,两者质量比为1:1;基础油为季戊四醇酯和苯基硅油的混合物,质量比为1:1。
[0085]
润滑脂组合6:十二羟基硬脂酸8份、壬二酸2.5份、氢氧化锂2.5 份、抗氧剂2份、防锈剂1份、极压剂1份、固体剂4份以及基础油74 份。
[0086]
其中抗氧剂为苯胺和受阻酚的混合物,两者质量比为1:1;防锈剂为亚硝酸钠;极压剂为硫化烯烃;固体剂为碳酸钙和磷酸盐的混合物,两者质量比为1:1;基础油为二元醇酯和二甲基硅油的混合物,质量比为1:1。
[0087]
本试验例针对实施例1、2所得润滑脂组合物,以及如上润滑脂组合进行起动机滚珠单向离合器的润滑实验,所有润滑脂组合物的制备方式均和实施例1中的制备方式相同,结果如下:
[0088]
表2各实施例的润滑脂性能测试结果
[0089]
[0090][0091]
由表2可以看出,试验例2中润滑脂组合3在不使用磷酸盐时产品的摩擦系数明显变小,起动机耐久测试出现打滑现象;润滑脂组合4在使用乙基硅油时,产品的摩擦系数明显变大,超过了0.40,起动机耐久测试虽然不打滑,但是部件出现了磨损现象;润滑脂组合5在使用不同二元酸制备稠化剂时,产品的抗剪切性能变差,同时摩擦系数变小,起动机耐久测试出现打滑现象;润滑脂组合6采用二甲基硅油和降低固体剂的比例时,产品的摩擦系数发生显著变小,起动机耐久测试出现打滑现象。通过试验例1和试验例2的结果对比,突出了苯甲基硅油作为基础油组分、二元酸采用壬二酸或癸二酸、固体剂采用碳酸钙和磷酸盐时制备的产品具有优异的抗冲击载荷的能力、抗剪切性能、较长的耐久寿命等。
[0092]
虽然,上文中已经用一般性说明及具体实施方案对本发明作了详尽的描述,但在本发明基础上,可以对之作一些修改或改进,这对本领域技术人员而言是显而易见的。因此,在不偏离本发明精神的基础上所做的这些修改或改进,均属于本发明要求保护的范围。