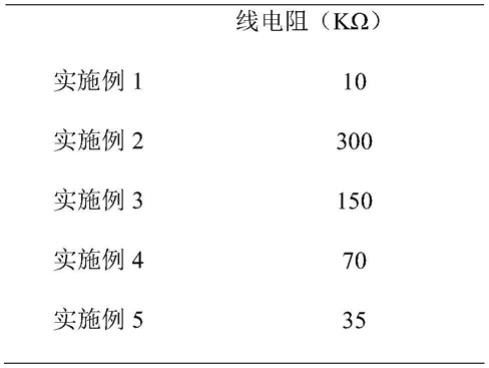
1.本发明涉及一种石墨烯油墨,特别涉及一种可直接用于电子电路的石墨烯油墨及其制备方法和应用,属于材料技术领域。
背景技术:
2.化学沉铜这个方法广泛的应用在有通孔的印制线路板的生产加工过程中。传统的化学沉铜工艺流程如下:碱性除油
→
二或三级逆流漂洗
→
粗化(微蚀)
→
二级逆流漂洗
→
预浸
→
活化
→
二级逆流漂洗
→
解胶
→
二级逆流漂洗
→
沉铜
→
二级逆流漂洗
→
浸酸,共计十二个步骤,在整个生产过程中,除了工艺繁琐外,不但需要大量的酸液、碱液以及沉铜液,而且还要添加大量的甲醛等有机溶剂。伴随产品而来的就是大量的含有诸如碱、酸、沉铜液、甲醛等的废水、废渣。这些工业垃圾一方面会给环境造成较大的污染,另一方面也会增加企业负担。
技术实现要素:
3.本发明的主要目的在于提供一种可直接用于电子电路的石墨烯油墨及其制备方法和应用,以克服现有技术中的不足。
4.为实现前述发明目的,本发明采用的技术方案包括:
5.本发明实施例提供了一种可直接用于电子电路的石墨烯油墨的制备方法,包括:
6.将氧化石墨烯、钯盐、第一溶剂和酸混合反应形成第一混合体系;
7.将气相二氧化硅分散于所述第一混合体系中形成第二混合体系,之后对所述第二混合体系进行真空干燥处理,以使钯盐与酸反应形成的纳米级的钯盐颗粒负载在所述氧化石墨烯上,且使负载有钯盐颗粒的氧化石墨烯包裹气相二氧化硅颗粒,从而形成钯催化剂
‑
氧化石墨烯
‑
气相二氧化硅复合颗粒,
8.将所述钯催化剂
‑
氧化石墨烯
‑
气相二氧化硅复合颗粒与树脂、第二溶剂、导电炭黑、分散剂、流平剂、消泡剂混合形成所述的石墨烯油墨。
9.本发明实施例提供了由所述的制备方法获得的石墨烯油墨。
10.本发明实施例提供了一种印制线电路板的制作方法,包括:
11.提供所述的石墨烯油墨;以所述石墨烯油墨在线路板基底上印刷形成线路图形,之后在所述线路图形表面形成铜层。
12.与现有技术相比,本发明实施例提供的一种可直接用于电子电路的石墨烯油墨的制备方法,与传统化学沉铜相比,只需通过表面清洗、丝网印刷、沉铜三大步即可,大大缩短了化学沉铜的工艺步骤,也大幅度减少了在沉铜过程中化学试剂的使用,对于整个行业具有颠覆式的意义。
附图说明
13.为了更清楚地说明本发明的技术方案,下面将对实施例或现有技术描述中所需要
使用的附图进行简单的介绍,显而易见地,下面描述的附图仅仅作为本文发明的一些实施例,对于本领域普通技术人员来讲,在不付出创造性劳动的前提下,还可以根据这些附图获得其他附图;
14.图1是本发明一典型实施例中催化剂
‑
氧化石墨烯
‑
气相二氧化硅复合颗粒的结构示意图;
15.图2是本发明一典型实施例中丝网印刷后油墨干膜的结构示意图;
16.图3a、图3b分别是本发明一典型实施例中油墨丝印干燥后干膜及其经过化学沉铜后油墨干膜的实物图。
具体实施方式
17.鉴于现有技术中的不足,本案发明人经长期研究和大量实践,得以提出本发明的技术方案。如下将对该技术方案、其实施过程及原理等作进一步的解释说明。
18.鉴于传统的化学沉铜法工序多、工艺繁琐、需要大量具有腐蚀性的化学试剂等缺点,本发明实施例提供了一种可直接用于电子电路的化学镀铜石墨烯油墨,其利用氧化石墨烯比表面积大、反应活性位点多、水溶易分散等性能优势,用其作为催化剂的载体,在干燥过程中使其包裹住气相二氧化硅,形成具有催化效果的催化剂
‑
氧化石墨烯
‑
气相二氧化硅复合颗粒;使用该复合颗粒制备的石墨烯油墨,在特定的线路板基底上印刷成特定的线路,然后再通过化学沉铜,在已有线路表面覆盖上一层致密的铜层,赋予线路优异的导电性,即可完成整个沉铜工艺。
19.本发明实施例提供了一种印制线电路板的制作方法与传统化学沉铜相比,只需通过表面清洗、丝网印刷、沉铜三大步即可,大大缩短了化学沉铜的工艺步骤,也大幅度减少了在沉铜过程中化学试剂的使用,对于整个行业具有颠覆式的意义。
20.本发明实施例提供了一种可直接用于电子电路的石墨烯油墨的制备方法,包括:
21.将氧化石墨烯、钯盐、第一溶剂和酸混合反应形成第一混合体系;
22.将气相二氧化硅分散于所述第一混合体系中形成第二混合体系,之后对所述第二混合体系进行真空干燥处理,以使钯盐与酸反应形成的纳米级的钯盐颗粒负载在所述氧化石墨烯上,且使负载有钯盐颗粒的氧化石墨烯包裹气相二氧化硅颗粒,从而形成钯催化剂
‑
氧化石墨烯
‑
气相二氧化硅复合颗粒,
23.将所述钯催化剂
‑
氧化石墨烯
‑
气相二氧化硅复合颗粒与树脂、第二溶剂、导电炭黑、分散剂、流平剂、消泡剂混合形成所述的石墨烯油墨。
24.在一具体实施方式中,所述钯盐与氧化石墨烯的质量比为0.1
‑
10:100,所述氧化石墨烯与第一溶剂的质量比为0.5
‑
10:100,所述钯盐与酸的质量比为1:1
‑
10。
25.在一具体实施方式中,所述钯盐包括pdcl2,所述酸为10%
‑
37%的盐酸,所述第一溶剂包括去离子水。
26.在一具体实施方式中,所述氧化石墨烯的比表面积为500
‑
1500m2/g,碳/氧质量比为1
‑
2:1。
27.在一具体实施方式中,所述的制备方法包括:将气相二氧化硅分散于所述第一混合体系中形成糊状的第二混合体系。
28.在一具体实施方式中,所述气相二氧化硅与氧化石墨烯的固体质量比为1
‑
10:1。
29.在一具体实施方式中,所述气相二氧化硅为表面未进行修饰的二氧化硅,表面未进行修饰的二氧化硅可以是采购的东曹e
‑
220a、鸿盛kh419l、格雷斯c803中的任意一种或两种以上的组合,但不限于此。
30.在一具体实施方式中,所述真空干燥处理的温度为70
‑
120℃,时间为3
‑
8h。
31.在一具体实施方式中,所述气相二氧化硅颗粒的粒径为10
‑
30μm,包裹所述气相二氧化硅颗粒的氧化石墨烯的厚度为10
‑
100nm,负载于所述氧化石墨烯表面的钯盐颗粒的粒径为5
‑
50nm。
32.在一具体实施方式中,所述导电炭黑与树脂的固体质量比为30
‑
100:100。
33.在一具体实施方式中,所述树脂包括环氧树脂、丙烯酸树脂、氨基树脂、聚氨酯树脂中的任意一种或两种以上的组合,但不限于此。
34.在一具体实施方式中,所述导电炭黑包括导电炉法炭黑、超导电炉法炭黑、特导电炉法炭黑中的任意一种或两种以上的组合,但不限于此。
35.在一具体实施方式中,所述分散剂、流平剂和消泡剂三者的总质量为石墨烯油墨总质量的0.3
‑
2wt%。
36.在一具体实施方式中,所述分散剂包括byk2155、byk167、byk1162、byk1550中的任意一种或两种以上的组合,但不限于此。
37.在一具体实施方式中,所述消泡剂包括ks
‑
66、at
‑
80、byk
‑
057、byk
‑
092中的任意一种或两种以上的组合,但不限于此。
38.在一具体实施方式中,所述流平剂包括byk
‑
354、byk
‑
346、byk
‑
381中的任意一种或两种以上的组合,但不限于此。
39.在一具体实施方式中,所述第二溶剂包括二乙二醇丁醚、异氟尔酮、丙二醇二醋酸酯、醋酸丁酯、乙酸乙酯中的任意一种或两种以上的组合,但不限于此。
40.本发明实施例提供了由所述的制备方法获得的石墨烯油墨。
41.本发明实施例提供了一种印制线电路板的制作方法,包括:
42.提供所述的石墨烯油墨;以所述石墨烯油墨在线路板基底上印刷形成线路图形,之后在所述线路图形表面形成铜层。
43.如下将结合具体实施案例对该技术方案、其实施过程及原理等作进一步的解释说明,除非特别说明的之外,本发明实施例所采用的材料混合、加热干燥等处理工艺、后续测试工艺等均可以采用本领域技术人员已知的设备和方法实现。
44.在一具体的实施方案中,一种可直接用于电子电路的石墨烯油墨的制备方法,包括如下步骤:
45.1)先将具有大比表面积的氧化石墨烯和pdcl2溶于去离子水中,同时加入盐酸,从而形成第一混合体系,依靠氧化石墨烯比表面积大、反应活性位点多、水溶易分散等特点,吸附溶解在水中的pd
2+
,盐酸的加入能够促进氧化石墨烯的溶解,并减少pdcl2水解产生pd(oh)2沉淀;
46.2)将表面未进行修饰的气相二氧化硅颗粒分散在第一混合体系中,形成第二混合体系,所述第二混合体系为糊状的混合溶液,搅拌均匀后转移至真空烘箱中,真空烘箱的温度调整在70
‑
120℃之间,干燥时间为3
‑
8h,以使pdcl2纳米颗粒负载在氧化石墨烯表面,且使负载有pdcl2纳米颗粒的氧化石墨烯在干燥过程中包裹二氧化硅颗粒,从而形成钯催化
剂
‑
氧化石墨烯
‑
气相二氧化硅复合颗粒,其中,由于氧化石墨烯比表面积大,反应活性位点多,水溶易分散,可以吸附溶解在水中的pd
2+
,气相二氧化硅由于表面含有大量的
‑
oh基团,同样能在水中大量分散,因此在真空干燥过程中,氧化石墨烯与气相二氧化硅之间发生强相互作用力,使得含有pdcl2纳米颗粒的氧化石墨烯包裹住气相二氧化硅颗粒,形成的钯催化剂
‑
氧化石墨烯
‑
气相二氧化硅复合颗粒的结构如图1所示;
47.3)将所制备的钯催化剂
‑
氧化石墨烯
‑
气相二氧化硅复合颗粒与树脂、溶剂、导电炭黑、分散剂、流平剂、消泡剂共混,过三辊机研磨后得到最终可化学镀铜的石墨烯油墨,其中,所述三辊机辊间距为0.02~0.1mm,三辊研磨机轮辊转速比(前:中:后)为1:3:9,中辊转速为40~90r/min,研磨次数为3~5次,所获可化学镀铜的石墨烯油墨的结构如图2所示,油墨丝印干燥后干膜及其经过化学沉铜后油墨干膜的实物图分别如图3a、图3b所示。
48.本案发明人研究发现,虽然直接将氧化石墨烯、pdcl2催化剂、气相二氧化硅颗粒、盐酸、树脂、溶剂、导电炭黑、分散剂、流平剂、消泡剂进行混合同样能形成导电石墨,但此时pdcl2催化剂的颗粒尺寸为微米级,催化效果极低,同时氧化石墨烯在有机溶剂体系中不能分散,呈团状颗粒,无法吸附催化剂颗粒与包裹气相二氧化硅,使得油墨在干燥过程中,只上浮气相二氧化硅,催化剂颗粒由于尺寸过大,呈下沉状态,使得油墨膜表面不具备化学沉积铜的效果。
49.而本发明实施例将pdcl2催化剂溶解在含盐酸中,使得其在干燥后得到纳米级的钯盐颗粒,增加其催化性能,同时氧化石墨烯吸附溶液中的钯离子,在真空干燥过程中,大比表面积氧化石墨烯包裹住气相二氧化硅颗粒,气相二氧化硅在油墨干燥过程中,会随着溶剂的挥发,发生上浮运动,分布在油墨干膜表面,使得油墨表面形成微凸哑光结构,这样进一步提升了钯盐颗粒与沉铜液的接触几率,负载有催化颗粒的氧化石墨烯包裹气相二氧化硅颗粒,从而减少了催化剂的使用量,并增强了化学沉铜的效果,并且只需通过表面清洗、丝网印刷、沉铜三大步即可实现,大大缩短了化学沉铜的工艺步骤,也大幅度减少了在沉铜过程中化学试剂的使用,对于整个行业具有颠覆式的意义。
50.实施例1
51.一种可直接用于电子电路的化学镀铜石墨烯油墨的制作方法,包括如下步骤:
52.步骤一,催化剂
‑
氧化石墨烯
‑
气相二氧化硅复合颗粒的制备:在室温条件下,将1g比表面积为1500m2/g、碳/氧质量比为1的氧化石墨烯溶于100g水中,超声搅拌30min,使得氧化石墨烯完全分散,再加入0.1g pdcl2和1.0g 37%hcl,超声搅拌30min,再加入10g格雷斯c803气相二氧化硅颗粒,继续超声搅拌30min,之后移至真空干燥箱中,并于120℃真空干燥8h;
53.步骤二,可化学镀铜的石墨烯油墨制备:取步骤一中的催化剂
‑
氧化石墨烯
‑
气相二氧化硅复合颗粒5g,依次加入100g环氧树脂、30g导电炉法炭黑、1g byk2155、1g byk
‑
a354、1g ks
‑
66搅拌后混合形成石墨烯油墨初混料,调整三辊机辊间距至0.05mm,以三辊机将石墨烯油墨处初混料辊压3遍;
54.步骤三,化学镀铜石墨烯油墨制成线路进行化学沉铜后性能测试:采用丝网印刷方式将步骤二制得的石墨烯油墨按预定图案印制在pet膜上,干燥处理制成膜片,放入含有硫酸铜5g/l、甲醛10ml/l、酒石酸钾钠25g/l、稳定剂0.1mg/l、氢氧化钠7g/l的沉铜液中静置沉铜20min,清洗干燥后获得表面镀铜的测试膜片,使用电阻表测量测试膜片上两个端点
的线电阻值,其结果参见表1。
55.实施例2
56.一种可直接用于电子电路的化学镀铜石墨烯油墨的制作方法,包括如下步骤:
57.步骤一,催化剂
‑
氧化石墨烯
‑
气相二氧化硅复合颗粒的制备:在室温条件下,将1g比表面积为500m2/g、碳/氧质量比为2的氧化石墨烯溶于100g水中,超声搅拌30min,使得氧化石墨烯完全分散,再加入0.01g pdcl2和0.01g 10%hcl,超声搅拌30min,再加入1g格雷斯c803气相二氧化硅颗粒,继续超声搅拌30min,之后移至真空干燥箱中,并于70℃真空干燥5h;
58.步骤二,可化学镀铜的石墨烯油墨制备:取步骤一中的催化剂
‑
氧化石墨烯
‑
气相二氧化硅复合颗粒5g,依次加入100g环氧树脂、30g导电炉法炭黑、1g byk2155、1g byk
‑
a354、1g ks
‑
66搅拌后混合形成石墨烯油墨初混料,调整三辊机辊间距至0.05mm,以三辊机将石墨烯油墨初混料辊压3遍;
59.步骤三,化学镀铜石墨烯油墨制成线路进行化学沉铜后性能测试:采用丝网印刷的方式将步骤二制得的石墨烯油墨按预定图案印制在pet膜上,干燥处理制成膜片,放入含有硫酸铜5g/l、甲醛10ml/l、酒石酸钾钠25g/l、稳定剂0.1mg/l、氢氧化钠7g/l的沉铜液中静置沉铜20min,清洗干燥后获得表面镀铜的测试膜片,使用电阻表测量测试膜片上两个端点的线电阻值,其结果参见表1。
60.实施例3
61.一种可直接用于电子电路的化学镀铜石墨烯油墨的制作方法,包括如下步骤:
62.步骤一,催化剂
‑
氧化石墨烯
‑
气相二氧化硅复合颗粒的制备:在室温条件下,将1g比表面积为1000m2/g、碳/氧质量比为1.5的氧化石墨烯溶于100g水中,超声搅拌30min,使得氧化石墨烯完全分散,再加入0.05g pdcl2和0.25g 25%hcl hcl,超声搅拌30min,再加入5g格雷斯c803气相二氧化硅颗粒,继续超声搅拌30min,之后移至真空干燥箱中,于100℃真空干燥6.5h;
63.步骤二,可化学镀铜的石墨烯油墨制备:取步骤一中的催化剂
‑
氧化石墨烯
‑
气相二氧化硅复合颗粒5g,依次加入100g环氧树脂、30g导电炉法炭黑、1g byk2155、1g byk
‑
a354、1g ks
‑
66搅拌后混合形成石墨烯油墨初混料,调整三辊机辊间距至0.05mm,以三辊机将石墨烯油墨初混料辊压3遍;
64.步骤三,化学镀铜石墨烯油墨制成线路进行化学沉铜后性能测试:采用丝网印刷的方式将步骤二制得的石墨烯油墨按预定图案印制在pet膜上,干燥处理制成膜片,放入含有硫酸铜5g/l、甲醛10ml/l、酒石酸钾钠25g/l、稳定剂0.1mg/l、氢氧化钠7g/l的沉铜液中静置沉铜20min,清洗干燥后获得表面镀铜的测试膜片,使用电阻表测量测试膜片上两个端点的线电阻值,其结果参见表1。
65.实施例4
66.一种可直接用于电子电路的化学镀铜石墨烯油墨的制作方法,包括如下步骤:
67.步骤一,催化剂
‑
氧化石墨烯
‑
气相二氧化硅复合颗粒的制备:在室温条件下,将1g比表面积为1500m2/g、碳/氧质量比为1的氧化石墨烯溶于100g水中,超声搅拌30min,使得氧化石墨烯完全分散,再加入0.1g pdcl2和1.0g 37%hcl hcl,超声搅拌30min,再加入10g格雷斯c803气相二氧化硅颗粒,继续超声搅拌30min,之后移至真空干燥箱中,于120℃真空
干燥8h;
68.步骤二,可化学镀铜的石墨烯油墨制备:取步骤一中的催化剂
‑
氧化石墨烯
‑
气相二氧化硅复合颗粒1g,依次加入100g环氧树脂、30g导电炉法炭黑、1g byk2155、1g byk
‑
a354、1g ks
‑
66搅拌后混合形成石墨烯油墨初混料,调整三辊机辊间距至0.05mm,以三辊机将石墨烯油墨处初混料辊压3遍;
69.步骤三,化学镀铜石墨烯油墨制成线路进行化学沉铜后性能测试:采用丝网印刷方式将步骤二制得的石墨烯油墨按预定图案印制在pet膜上,干燥处理制成膜片,放入含有硫酸铜5g/l、甲醛10ml/l、酒石酸钾钠25g/l、稳定剂0.1mg/l、氢氧化钠7g/l的沉铜液中静置沉铜20min,清洗干燥后获得表面镀铜的测试膜片,使用电阻表测量测试膜片上两个端点的线电阻值,其结果参见表1。
70.实施例5
71.一种可直接用于电子电路的化学镀铜石墨烯油墨的制作方法,包括如下步骤:
72.步骤一,催化剂
‑
氧化石墨烯
‑
气相二氧化硅复合颗粒的制备:在室温条件下,将1g比表面积为500m2/g、碳/氧质量比为1的氧化石墨烯溶于100g水中,超声搅拌30min,使得氧化石墨烯完全分散,再加入0.1g pdcl2和1.0g 37%hcl hcl,超声搅拌30min,再加入10g格雷斯c803气相二氧化硅颗粒,继续超声搅拌30min,之后移至真空干燥箱中,于70℃真空干燥5h;
73.步骤二,可化学镀铜的石墨烯油墨制备:取步骤一中的催化剂
‑
氧化石墨烯
‑
气相二氧化硅复合颗粒5g,依次加入100g环氧树脂、30g导电炉法炭黑、1g byk2155、1g byk
‑
a354、1g ks
‑
66搅拌后混合形成石墨烯油墨初混料,调整三辊机辊间距至0.05mm,以三辊机将石墨烯油墨初混料辊压3遍;
74.步骤三,化学镀铜石墨烯油墨制成线路进行化学沉铜后性能测试:采用丝网印刷的方式将步骤二制得的石墨烯油墨按预定图案印制在pet膜上,干燥处理制成膜片,放入含硫酸铜5g/l、甲醛10ml/l、酒石酸钾钠25g/l、稳定剂0.1mg/l、氢氧化钠7g/l的沉铜液中静置沉铜20min,清洗干燥后获得表面镀铜的测试膜片,使用电阻表测量测试膜片上两个端点的线电阻值,其结果参见表1。
75.对比例1
76.对比例1的方案与实施例1基本相同,不同之处在于对比例1不添加盐酸,对比例1所获膜片的性能参数参见表1。
77.对比例2
78.对比例2的方案与实施例1基本相同,不同之处在于对比例2不添加氧化石墨烯,对比例2所获膜片的性能参数参见表1。
79.对比例3
80.对比例3的方案与实施例1基本相同,不同之处在于对比例2不添加气相二氧化硅,对比例2所获膜片的性能参数参见表1。
81.对比例4
82.对比例4的方案与实施例1基本相同,不同之处在于对比例4不添加氯化钯催化剂,对比例4所获膜片的性能参数参见表1。
83.对比例5
84.对比例5的方案与实施例1基本相同,不同之处在于对比例5添加表面经有机硅修饰的气相二氧化硅,对比例5所获膜片的性能参数参见表1。
85.表1为实施例1
‑
5和对比例1
‑
5中所获膜片的线电阻测试结果
[0086][0087][0088]
由表1示出的测试数据可以看出,油墨中相同复合颗粒添加量,其上催化剂颗粒越多,则线电阻越低;相同催化剂含量,复合颗粒在油墨中含量越高,则线电阻越小;线电阻越小,膜片化学沉铜效果越好;由于氧化石墨烯为二维片层材料,在真空干燥过程中会包裹气相二氧化硅颗粒,氧化石墨烯的比表面积1500m2/g,其对于二氧化硅的包裹效果更优,这样在油墨湿膜干燥过程中,上浮的复合颗粒数量越多,化学沉铜过程中催化还原铜也更多使得测试两端的线电阻值越低,同时,对比实施例1和对比例3可以看出,如果没有气相二氧化硅颗粒,钯盐催化剂与氧化石墨烯的混合物在油墨湿膜干燥过程中无法上浮,只有极少量沉铜液能够透过膜表面与催化剂接触,而盐酸能够促进氧化石墨烯的溶解,并减少pdcl2催化剂水解产生pd(oh)2的沉淀,使得pdcl2催化剂有效量增加,而表面经过修饰的气相二氧化硅颗粒因为与氧化石墨烯之间的相互作用力减弱,在干燥过程中无法很好的被包裹,导致最终化学沉铜效果减弱。
[0089]
本发明实施例提供的一种可直接用于电子电路的石墨烯油墨的制备方法,与传统化学沉铜相比,只需通过表面清洗、丝网印刷、沉铜三大步即可,大大缩短了化学沉铜的工艺步骤,也大幅度减少了在沉铜过程中化学试剂的使用,对于整个行业具有颠覆式的意义。
[0090]
本发明的各方面、实施例、特征及实例应视为在所有方面为说明性的且不打算限制本发明,本发明的范围仅由权利要求书界定。在不背离所主张的本发明的精神及范围的情况下,所属领域的技术人员将明了其它实施例、修改及使用。
[0091]
在本发明案通篇中,在将组合物描述为具有、包含或包括特定组份之处或者在将过程描述为具有、包含或包括特定过程步骤之处,预期本发明教示的组合物也基本上由所叙述组份组成或由所叙述组份组成,且本发明教示的过程也基本上由所叙述过程步骤组成或由所叙述过程步骤组组成。
[0092]
应当理解,上述实施例仅为说明本发明的技术构思及特点,其目的在于让熟悉此项技术的人士能够了解本发明的内容并据以实施,并不能以此限制本发明的保护范围。凡根据本发明精神实质所作的等效变化或修饰,都应涵盖在本发明的保护范围之内。