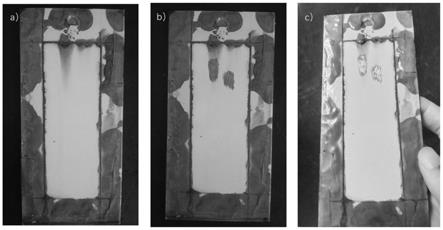
1.本发明涉及金属防腐技术领域,具体涉及一种水性有机硅防腐涂料及其制备方法。
背景技术:
2.众所周知,煤气管道、供热管道、汽车排气管、消声器等部件都需要在高温环境下工作,在其表面涂覆防腐涂料是保护金属基材、延长金属制品使用寿命行之有效的办法之一。然而,现有的防腐涂料形成的涂层在高温环境(500℃~600℃)中耐腐蚀性能会显著下降,对金属基材的保护作用会大打折扣,难以满足高温环境下的实际应用需求。
3.因此,开发一种可以在高温下长期使用的防腐涂料具有十分重要的意义。
技术实现要素:
4.本发明的目的在于提供一种水性有机硅防腐涂料及其制备方法。
5.本发明所采取的技术方案是:
6.一种水性有机硅防腐涂料,其包括以下质量百分比的组分:
7.有机硅乳液:45%~50%;
8.钛白粉:2%~3%;
9.防锈颜料:6%~8%;
10.低熔点玻璃粉:10%~15%;
11.沉淀硫酸钡:5%~8%;
12.分散剂:0.8%~1.2%;
13.润湿剂:0.2%~0.3%;
14.消泡剂:0.2%~0.3%;
15.增稠剂:0.1%~0.3%;
16.防闪锈剂:0.1%~0.3%;
17.水:余量。
18.优选的,所述有机硅乳液中的主要组分的结构式为式中,r为
19.优选的,所述有机硅乳液的固含量为40%~50%。
20.优选的,所述钛白粉的粒径为5μm~20μm。
21.优选的,所述防锈颜料为磷酸锌、磷酸铁锌、三聚磷酸铝、磷酸锌铝中的至少一种。
22.优选的,所述防锈颜料的粒径为5μm~15μm。
23.优选的,所述低熔点玻璃粉的熔融温度为400℃~1300℃。
24.优选的,所述低熔点玻璃粉的粒径为5μm~10μm。
25.优选的,所述低熔点玻璃粉的组成元素包括al、si、b、k和o。
26.优选的,所述沉淀硫酸钡的粒径为10μm~20μm。
27.优选的,所述分散剂为聚丙烯酸铵盐类分散剂。
28.进一步优选的,所述分散剂为byk
‑
190、tego
‑
760w、dow
‑
1124中的至少一种。
29.优选的,所述润湿剂为有机硅聚醚型非离子表面活性剂。
30.进一步优选的,所述润湿剂为岳阳凯门水性助剂有限公司的a04bc、上海荟研新材料有限公司的hy67、byk
‑
156中至少一种。
31.优选的,所述消泡剂为有机硅消泡剂。
32.进一步优选的,所述消泡剂为tego
‑
901w、tego
‑
902w、dow
‑
8590中的至少一种。
33.优选的,所述增稠剂为甲基纤维素、羟乙基纤维素、羟丙基甲基纤维素中的至少一种。
34.优选的,所述防闪锈剂为亚硝酸钠、有机锌螯合物中的至少一种。
35.进一步优选的,所述防闪锈剂为广州航宇高新科技有限公司的有机锌螯合物hy
‑
189。
36.上述水性有机硅防腐涂料的制备方法包括以下步骤:将分散剂、润湿剂、消泡剂、增稠剂和防闪锈剂分散在水中,再加入钛白粉、防锈颜料、低熔点玻璃粉和沉淀硫酸钡,进行混合和研磨,再加入有机硅乳液,进行混合,即得水性有机硅防腐涂料。
37.优选的,上述水性有机硅防腐涂料的制备方法包括以下步骤:将分散剂、润湿剂、消泡剂、增稠剂和防闪锈剂加入水中,调节搅拌速度为750rpm~1000rpm,搅拌15min~30min,再加入钛白粉、防锈颜料、低熔点玻璃粉和沉淀硫酸钡,继续搅拌15min~30min,再研磨至细度为5μm~15μm,再加入有机硅乳液,调节搅拌速度为300rpm~500rpm,搅拌30min~60min,即得水性有机硅防腐涂料。
38.本发明的有益效果是:本发明的水性有机硅防腐涂料形成的涂层可以耐600℃高温,且力学性能和耐腐蚀性能优异,可以在高温下长期使用,适合用于汽车排气管、锅炉以及工业管道等高温设备的涂装保护。
39.具体来说:
40.1)本发明的水性有机硅防腐涂料中添加有低熔点玻璃粉,在高温环境中低熔点玻璃粉通过熔融可以粘结颜/填料和有机硅树脂分解产生的二氧化硅,形成致密的二氧化硅保护层,最终得到的涂层可以在500℃~600℃下长期使用;
41.2)本发明的水性有机硅防腐涂料形成的涂层具有优异的柔韧性和抗冲击强度,耐水和耐中性盐雾时间长,且在高温环境中仍然可以保持长的耐中性盐雾时间;
42.3)本发明的水性有机硅防腐涂料的可挥发性有机物含量低,绿色无污染,且其制备工艺简单,适合进行大规模生产应用。
附图说明
43.图1为实施例3中的防腐蚀涂层进行高温处理前后的外观图。
44.图2为实施例3中的防腐蚀涂层进行高温处理后耐盐雾10天的外观图。
具体实施方式
45.下面结合具体实施例对本发明作进一步的解释和说明。
46.实施例1:
47.一种水性有机硅防腐涂料,其组成如下表所示:
48.表1水性有机硅防腐涂料的组成表
[0049][0050][0051]
注:
[0052]
有机硅乳液:固含量约40%,主要组分的结构式为式中,r为
[0053]
低熔点玻璃粉:广州歌林尔新材料有限公司,熔融温度为450℃(常压下在500℃~1380℃的温区,产品属于稳定的液相,温度越高粘度越低),粒径为粒径5μm~10μm,组成元素包括al、si、b、k和o。
[0054]
上述水性有机硅防腐涂料的制备方法包括以下步骤:
[0055]
将分散剂dow
‑
1124、润湿剂hy67、消泡剂dow
‑
8590、羟丙基甲基纤维素和亚硝酸钠加入水中,调节搅拌速度为850rpm,搅拌20min,再加入钛白粉、磷酸锌、低熔点玻璃粉和沉淀硫酸钡,继续搅拌20min,再研磨至细度为5μm,再加入有机硅乳液,调节搅拌速度为300rpm,搅拌60min,即得水性有机硅防腐涂料。
[0056]
防腐蚀涂层的制备:
[0057]
将本实施例的水性有机硅防腐涂料用喷枪以0.8mpa的压力、30cm的间距喷涂在喷砂钢板上,再220℃固化1h,即得防腐蚀涂层。
[0058]
实施例2:
[0059]
一种水性有机硅防腐涂料,其组成如下表所示:
[0060]
表2水性有机硅防腐涂料的组成表
[0061][0062][0063]
注:
[0064]
有机硅乳液:固含量约40%,主要组分的结构式为式中,r为
[0065]
低熔点玻璃粉:广州歌林尔新材料有限公司,熔融温度为450℃(常压下在500℃~1380℃的温区,产品属于稳定的液相,温度越高粘度越低),粒径为粒径5μm~10μm,组成元
素包括al、si、b、k和o。
[0066]
上述水性有机硅防腐涂料的制备方法包括以下步骤:
[0067]
将分散剂dow
‑
1124、润湿剂hy67、消泡剂dow
‑
8590、羟丙基甲基纤维素和亚硝酸钠加入水中,调节搅拌速度为1000rpm,搅拌15min,再加入钛白粉、磷酸铁锌、低熔点玻璃粉和沉淀硫酸钡,继续搅拌15min,再研磨至细度为5μm,再加入有机硅乳液,调节搅拌速度为300rpm,搅拌60min,即得水性有机硅防腐涂料。
[0068]
防腐蚀涂层的制备:
[0069]
将本实施例的水性有机硅防腐涂料用喷枪以0.8mpa的压力、30cm的间距喷涂在喷砂钢板上,再200℃固化1h,即得防腐蚀涂层。
[0070]
实施例3:
[0071]
一种水性有机硅防腐涂料,其组成如下表所示:
[0072]
表3水性有机硅防腐涂料的组成表
[0073][0074][0075]
注:
[0076]
有机硅乳液:固含量约40%,主要组分的结构式为式中,r为
[0077]
低熔点玻璃粉:广州歌林尔新材料有限公司,熔融温度为450℃(常压下在500℃~
1380℃的温区,产品属于稳定的液相,温度越高粘度越低),粒径为粒径5μm~10μm,组成元素包括al、si、b、k和o。
[0078]
上述水性有机硅防腐涂料的制备方法包括以下步骤:
[0079]
将分散剂dow
‑
1124、润湿剂hy67、消泡剂dow
‑
8590、甲基纤维素和有机锌螯合物hy
‑
189加入水中,调节搅拌速度为750rpm,搅拌30min,再加入钛白粉、三聚磷酸铝、低熔点玻璃粉和沉淀硫酸钡,继续搅拌30min,再研磨至细度为15μm,再加入有机硅乳液,调节搅拌速度为500rpm,搅拌30min,即得水性有机硅防腐涂料。
[0080]
防腐蚀涂层的制备:
[0081]
将本实施例的水性有机硅防腐涂料用喷枪以0.4mpa的压力、40cm的间距喷涂在喷砂钢板上,再200℃固化1h,即得防腐蚀涂层。
[0082]
实施例4:
[0083]
一种水性有机硅防腐涂料,其组成如下表所示:
[0084]
表4水性有机硅防腐涂料的组成表
[0085]
原料质量百分比(%)有机硅乳液45钛白粉(粒径5μm~20μm)2磷酸锌铝(粒径5μm~15μm)6低熔点玻璃粉10沉淀硫酸钡(粒径10μm~20μm)7分散剂dow
‑
11240.8润湿剂hy670.3消泡剂dow
‑
85900.3羟乙基纤维素0.3有机锌螯合物hy
‑
1890.3水28
[0086]
注:
[0087]
有机硅乳液:固含量约40%,主要组分的结构式为式中,r为
[0088]
低熔点玻璃粉:广州歌林尔新材料有限公司,熔融温度为450℃(常压下在500℃~1380℃的温区,产品属于稳定的液相,温度越高粘度越低),粒径为粒径5μm~10μm,组成元素包括al、si、b、k和o。
[0089]
上述水性有机硅防腐涂料的制备方法包括以下步骤:
[0090]
将分散剂dow
‑
1124、润湿剂hy67、消泡剂dow
‑
8590、羟乙基纤维素和有机锌螯合物
hy
‑
189加入水中,调节搅拌速度为1000rpm,搅拌30min,再加入钛白粉、磷酸锌铝、低熔点玻璃粉和沉淀硫酸钡,继续搅拌30min,再研磨至细度为15μm,再加入有机硅乳液,调节搅拌速度为500rpm,搅拌30min,即得水性有机硅防腐涂料。
[0091]
防腐蚀涂层的制备:
[0092]
将本实施例的水性有机硅防腐涂料用喷枪以0.4mpa的压力、40cm的间距喷涂在喷砂钢板上,再180℃固化1.5h,即得防腐蚀涂层。
[0093]
对比例1:
[0094]
一种水性有机硅防腐涂料,其组成如下表所示:
[0095]
表5水性有机硅防腐涂料的组成表
[0096]
原料质量百分比(%)甲基苯基有机硅乳液60铜铬黑(粒径5μm~20μm)12滑石粉(粒径10μm~20μm)3低熔点玻璃粉7云母粉(粒径10μm~20μm)3分散剂dow
‑
11242.8润湿剂hy670.3消泡剂dow
‑
85900.1流平剂a56430.3羟乙基纤维素0.8多聚磷酸钠1.2乙二醇丁醚1.5水8
[0097]
注:
[0098]
甲基苯基有机硅乳液:sh
‑
9608,湖北新四海化工股份有限公司,固含量40%~50%;
[0099]
低熔点玻璃粉:广州歌林尔新材料有限公司,熔融温度为450℃(常压下在500℃~1380℃的温区,产品属于稳定的液相,温度越高粘度越低),粒径为粒径5μm~10μm,组成元素包括al、si、b、k和o;
[0100]
流平剂a5643:台湾佳谦化学股份有限公司。
[0101]
上述水性有机硅防腐涂料的制备方法包括以下步骤:
[0102]
将分散剂dow
‑
1124、润湿剂hy67、消泡剂dow
‑
8590、羟乙基纤维素和多聚磷酸钠加入水中,调节搅拌速度为1000rpm,搅拌30min,再加入铜铬黑、滑石粉、低熔点玻璃粉和云母粉,继续搅拌30min,再研磨至细度为15μm,再加入甲基苯基有机硅乳液、乙二醇丁醚和流平剂a5643,调节搅拌速度为500rpm,搅拌30min,即得水性有机硅防腐涂料。
[0103]
防腐蚀涂层的制备:
[0104]
将本对比例的水性有机硅防腐涂料用喷枪以0.4mpa的压力、40cm的间距喷涂在喷砂钢板上,再250℃固化1.5h,即得防腐蚀涂层。
[0105]
对比例2:
[0106]
一种水性有机硅防腐涂料,其组成如下表所示:
[0107]
表6水性有机硅防腐涂料的组成表
[0108]
原料质量百分比(%)有机硅乳液48钛白粉(粒径5μm~20μm)3三聚磷酸铝(粒径5μm~15μm)6滑石粉(粒径10μm~20μm)12沉淀硫酸钡(粒径10μm~20μm)6分散剂dow
‑
11241润湿剂hy670.3消泡剂dow
‑
85900.3甲基纤维素0.2有机锌螯合物hy
‑
1890.3水22.9
[0109]
注:
[0110]
有机硅乳液:固含量约40%,主要组分的结构式为式中,r为
[0111]
上述水性有机硅防腐涂料的制备方法包括以下步骤:
[0112]
将分散剂dow
‑
1124、润湿剂hy67、消泡剂dow
‑
8590、甲基纤维素和有机锌螯合物hy
‑
189加入水中,调节搅拌速度为750rpm,搅拌30min,再加入钛白粉、三聚磷酸铝、滑石粉和沉淀硫酸钡,继续搅拌30min,再研磨至细度为15μm,再加入有机硅乳液,调节搅拌速度为500rpm,搅拌30min,即得水性有机硅防腐涂料。
[0113]
防腐蚀涂层的制备:
[0114]
将本对比例的水性有机硅防腐涂料用喷枪以0.4mpa的压力、40cm的间距喷涂在喷砂钢板上,再200℃固化1h,即得防腐蚀涂层。
[0115]
性能测试:
[0116]
1)对实施例1~4和对比例1~2中的防腐蚀涂层进行机械性能测试,测试结果如下表所示:
[0117]
表7防腐蚀涂层的机械性能测试结果
[0118][0119]
注:
[0120]
附着力:参照“gb/t 9286
‑
1998色漆和清漆漆膜的划格试验”进行测试;
[0121]
柔韧性:参照“gb/t 1731
‑
1993漆膜柔韧性测定法”进行测试;
[0122]
抗冲击强度:参照“gb/t 1732
‑
1993漆膜耐冲击测定法”进行测试;
[0123]
铅笔硬度:参照“gb/t 6739
‑
2006色漆和清漆铅笔法测定漆膜硬度”进行测试。
[0124]
由表7可知:实施例1~4和对比例2中的防腐蚀涂层的柔韧性和抗冲击强度均能达到0.5mm和50kg
·
cm,铅笔硬度可达1h,而对比例1中的防腐蚀涂层的脆性较大,原因在于:防腐蚀涂层的机械性能主要是受树脂及颜基比的影响,对比例1中采用的是甲基苯基有机硅乳液,制得的漆膜脆性较大。
[0125]
2)对实施例1~4和对比例1~2中的防腐蚀涂层进行防腐性能测试,测试结果如下表所示:
[0126]
表8防腐蚀涂层的防腐性能测试结果
[0127][0128]
注:
[0129]
耐水时间:参照“gb/t 1733
‑
1993漆膜耐水性测定法”进行测试;
[0130]
耐盐雾时间:参照“gb 1771
‑
2007色漆和清漆耐中性盐雾性能”进行测试;
[0131]
耐盐雾时间/高温:将测试样板放入高温炉,升温至600℃,保持3h,停止加热,打开高温炉门,随高温炉降温至200℃后取出,常温放置24h,再参照“gb 1771
‑
2007色漆和清漆耐中性盐雾性能”进行测试。
[0132]
由表8可知:实施例1~4中的防腐蚀涂层的耐水时间可达24h,耐盐雾时间可达64h,耐盐雾时间/高温可达240h,耐水性能和耐腐蚀性能优异,而对比例1和对比例2中的防
腐蚀涂层的耐盐雾时间/高温仅48h和72h,高温下的耐盐雾性能差,原因在于:本发明的水性有机硅防腐涂料中添加有低熔点玻璃粉,高温过程中熔融的玻璃粉在树脂高温分解产生的二氧化硅骨架上流淌,可以在涂层与基材之间形成一层“氧化膜”,进而可以保护基材。
[0133]
3)实施例3中的防腐蚀涂层进行高温处理(处理过程参照“耐盐雾时间/高温”)前后的外观图如图1(图中左边的测试样板为高温处理前,右边的测试样板为高温处理后)所示。
[0134]
由图1可知:实施例3中的防腐蚀涂层进行高温处理后未出现起泡和开裂,仅颜色发生轻微变化。
[0135]
4)实施例3中的防腐蚀涂层进行高温处理(处理过程参照“耐盐雾时间/高温”)后,再参照“gb 1771
‑
2007色漆和清漆耐中性盐雾性能”进行耐中性盐雾试验,耐盐雾10天后防腐蚀涂层的外观图如图2(a为涂层表面,b表示将涂层上部锈迹晕染处划开,c表示在阳光下)所示。
[0136]
由图2可知:测试样板只有边缘处生锈,将上部锈迹晕染处划开发现基材钢板未被腐蚀,而且在阳光下仍然保持光亮,说明实施例3中的防腐蚀涂层具有优异的耐高温性能和防腐蚀性能。
[0137]
上述实施例为本发明较佳的实施方式,但本发明的实施方式并不受上述实施例的限制,其他的任何未背离本发明的精神实质与原理下所作的改变、修饰、替代、组合、简化,均应为等效的置换方式,都包含在本发明的保护范围之内。