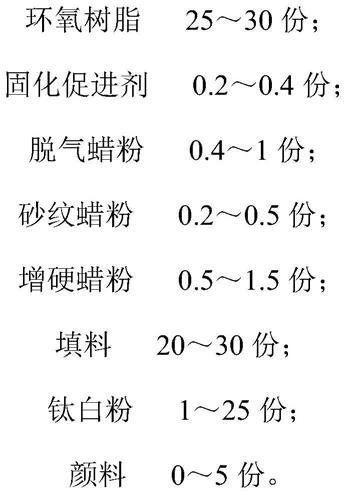
一种高硬度、耐磨抗划伤mdf粉末涂料及其制备方法
技术领域
1.本发明属于固体粉末技术领域,具体涉及一种高硬度、耐磨抗划伤mdf粉末涂料及其制备方法。
背景技术:
2.中密度纤维板(mdf)粉末涂装是当前及今后绿色家居涂装主流。考虑家具特定使用环境,例如办公桌、课桌、茶几等在日常使用中容易被坚硬物件划伤,造成涂层破坏而影响外观和使用,因此开发一款高硬度、耐磨抗划伤的mdf粉末涂料符合市场需求。
3.目前市场上主流mdf粉末涂料涂层硬度一般只有2~3h,尽管符合标准要求但抗划伤性能依然不够优异。中密度纤维板由于属于热敏感基材容易受到高温破坏,因此采用粉末静电涂装时必须采用低温固化技术,粉末涂料通常要求130~150℃下快速熔融流平固化。而对于粉末涂料而言,低温固化往往固化交联密度不够影响涂膜硬度,同时常规增硬助剂在低温条件下不容易迁移至涂膜表面,从而很难发挥增硬功效。
技术实现要素:
4.为解决上述技术问题,本发明提供了一种高硬度、耐磨抗划伤mdf粉末涂料及其制备方法。其可在130℃低温下快速固化,固化后涂层交联密度高,最终涂层硬度可达到5h,且耐磨性优异。
5.本发明采取的技术方案如下:
6.一种高硬度、耐磨抗划伤mdf粉末涂料,包括以下重量份的原料:
[0007][0008][0009]
所述高硬度、耐磨抗划伤mdf粉末涂料,优选包括以下重量份的原料:
[0010][0011]
所述聚酯树脂酸值为73
‑
85mg koh/g,此酸值范围内的聚酯树脂在本发明的粉末涂料体系下的反应活性较高。
[0012]
所述环氧树脂环氧当量为700
‑
750g/eq,在此当量范围内环氧树脂在本发明的粉末涂料体系下的反应活性较高。
[0013]
所述固化促进剂为长链型叔胺促进剂,此种类型的促进剂熔点低,在低温固化条件下可以有效提高粉末涂料中聚酯树脂与环氧树脂的反应活性,可以有效降低粉末固化温度至130℃。
[0014]
所述长链型叔胺促进剂的制备方法为:将4l十二醇、500mg催化剂cu 60/8p投入到反应釜中。向反应釜中通入足够量的氮气置换反应釜中的空气,待空气被完全置换后再通入氢气置换氮气,将反应釜环境加热至190℃并保温以活化催化剂,在加热升温过程中间需再次通入一次氢气已补充所消耗的氢气,催化剂活化完成后开始通入二甲胺气体,持续通入4h。待反应4h后先向反应釜中通入足够氮气去除反应残余气体,同时停止加热待反应釜温度降至室温后取出液体反应产物经减压蒸馏即得较高纯度的长链型叔胺促进剂。该制备方法操作简单,适用于工业化生产。
[0015]
所述脱气蜡粉为全氟蜡粉,可有效消除针孔和抗黄变,同时耐磨性优异;所述砂纹蜡粉为聚四氟乙烯蜡粉,其纹理均匀,同时耐磨性优异;两者除提供脱气、纹理作用外兼具增硬耐磨功效。
[0016]
所述增硬蜡粉的型号为pew
‑
0602f,该增硬蜡粉不仅可以显著提高涂层的硬度,同时可以提高涂层的爽滑性,粉末熔融固化时极易迁移到涂膜表面,适用于配置砂纹配方。
[0017]
所述填料为硫酸钡、碳酸钙、硅灰石中的至少一种。
[0018]
所述高硬度、耐磨抗划伤mdf粉末涂料的制备方法,包括以下步骤:将配方量的各原料充分均匀混合,经挤出机熔融挤出,再经磨机粉碎过筛。
[0019]
所述挤出机的挤出温度为80℃,所述过筛为经过220目的筛网过筛。
[0020]
本发明还提供了一种高硬度、耐磨抗划伤mdf涂层,由所述高硬度、耐磨抗划伤mdf
粉末涂料喷涂到mdf上后经固化形成。
[0021]
所述固化的方法为:采用红外线加热方式固化,固化条件为130℃、3min。
[0022]
本发明提供的高硬度、耐磨抗划伤mdf粉末涂料,涂层硬度达到5h,在日常使用中可以有效避免受到划伤损伤。同时按标准taber astm d4060/84,750g载荷1000转进行的耐磨测试结果表明,涂层耐磨性同样优异,磨损测试结果仅为3mg。本发明所提供的mdf粉末另一特点是,粉末涂料可以实现130℃/3min低温快速固化,涂层固化率高,对提高硬度有利。
[0023]
本发明所提供的高硬度、耐磨抗划伤mdf粉末涂料涂层硬度可以达到5h,耐磨抗划伤性能优异,主要原因有三个方面:
[0024]
其一,采用高活性树脂:本发明采用的聚酯树脂酸值为73
‑
85mgkoh/g,环氧树脂当量为700
‑
750g/eq,其特点是反应活性高,有利于提高交联密度。
[0025]
其二,采用长链型叔胺促进剂,其熔点低常温下为液态,有利于发挥在低温固化环境下的促进作用,提高涂层交联密度。
[0026]
其三,本发明采用了增硬蜡粉提高涂层硬度,有效物含量达到15%,且上浮速率快。同时采用的脱气蜡粉、砂纹蜡粉也具备耐磨功能。
[0027]
与现有技术相比,本发明具有以下优点:
[0028]
本发明提供的mdf粉末涂料固化成膜后涂层硬度可达5h,具有优异的耐磨抗划伤性能,有效防止在使用过程中出现划伤破损的情况。本发明提供的mdf粉末涂料可以实现130℃、3min低温快速固化,与目前市场通用mdf粉末涂料固化条件相同,因此用户可以直接使用而不需要更改涂装工艺。
具体实施方式
[0029]
下面结合实施例对本发明进行详细描述。
[0030]
各实施例所使用的聚酯树脂酸值为73
‑
85mg koh/g,型号为crylcoat1506
‑
6,厂家为湛新公司;
[0031]
环氧树脂环氧当量为700
‑
750g/eq,型号为hy 903l,厂家为恒远新材料;
[0032]
长链型叔胺促进剂的制备方法为:将4l十二醇、500mg催化剂cu 60/8p投入到反应釜中。向反应釜中通入足够量的氮气置换反应釜中的空气,待空气被完全置换后再通入氢气置换氮气,将反应釜环境加热至190℃并保温以活化催化剂,在加热升温过程中间需再次通入一次氢气已补充所消耗的氢气,催化剂活化完成后开始通入二甲胺气体,持续通入4h。待反应4h后先向反应釜中通入足够氮气去除反应残余气体,同时停止加热待反应釜温度降至室温后取出液体反应产物经减压蒸馏即得;化剂cu 60/8p的厂家为索尔维投资有限公司;
[0033]
脱气蜡粉为全氟蜡粉;砂纹蜡粉为聚四氟乙烯蜡粉;
[0034]
增硬蜡粉的型号为pew
‑
0602f,厂家为南京天诗新材料科技有限公司;
[0035]
各实施例及对比例中的且各原料如无特殊说明,则均使用的是同一批次同一型号的原料。
[0036]
实施例1
[0037]
一种高硬度、耐磨抗划伤mdf粉末涂料,其原料组成及各原料的重量份为:聚酯树脂1506
‑
6 40份,环氧树脂hy 903l 28份,长链型叔胺促进剂0.2份,脱气蜡粉0.5份,砂纹蜡
40份,环氧树脂hy 903l 28份,市售促进剂咪唑0.4份,脱气蜡粉0.5份,砂纹蜡粉0.3份,增硬蜡粉1.5份,硫酸钡28份,钛白粉3份,炭黑颜料1份。
[0053]
将各组份原料精准称量后均匀混合,经双螺杆挤出机熔融挤出、压片、冷却,挤出温度80℃,再经磨机粉碎并220目过筛,得到所述粉末涂料。将中密度纤维板(mdf)进行封边、抛光打磨处理后,用静电喷枪将粉末涂料喷涂在mdf板材表面,喷涂好后置于红外线加热炉中加热固化,设置温度为130℃,时间3min。待涂层固化后自然冷却得到所述涂层。
[0054]
对比例2
[0055]
一种mdf粉末涂料,其原料组成及各原料的重量份为:酸值为48
‑
55mg koh/g的聚酯树脂crylcoat 1620
‑
0 40份,环氧当量为800
‑
850g/eq的环氧树脂e12 28份,叔胺促进剂0.4份,脱气蜡粉0.5份,砂纹蜡粉0.3份,增硬蜡粉1.5份,硫酸钡28份,钛白粉3份,炭黑颜料1份。
[0056]
将各组份原料精准称量后均匀混合,经双螺杆挤出机熔融挤出、压片、冷却,挤出温度80℃,再经磨机粉碎并220目过筛,得到所述粉末涂料。将中密度纤维板(mdf)进行封边、抛光打磨处理后,用静电喷枪将粉末涂料喷涂在mdf板材表面,喷涂好后置于红外线加热炉中加热固化,设置温度为130℃,时间3min。待涂层固化后自然冷却得到所述涂层。
[0057]
对上述所有实施案例所述的制得的涂层进行性能检测,结果如表1所示:
[0058]
表1
[0059]
案例实施例1实施例2实施例3实施例4实施例5对比例1对比例2铅笔硬度2h3h3h4h5h2h1h磨损8 mg8mg6mg5mg3mg20mg28mg
[0060]
备注:磨损测试按标准taber astm d4060/84进行,载荷为750g,1000转测试。
[0061]
本发明各实施例中的高硬度、耐磨抗划伤mdf粉末涂料成膜后涂层具有优异的硬度和耐磨性。且在本发明的配方范围内,随着增硬蜡粉用量增加可以提高涂层硬度和耐磨性;叔胺促进剂用量增加可以提高涂层硬度和耐磨性;如果将实施例中的长链型叔胺促进剂替换为咪唑的话则固化促进效果会变差;如果将实施例中的聚酯树脂、环氧树脂替换为对比例2中的低酸值聚酯、高当量环氧树脂的话涂层的硬度和耐磨性会变差。
[0062]
本发明提供的高硬度、耐磨抗划伤粉末涂料与底材结合力高,具有优异的防刮伤性能,有效防止在使用过程中出现划伤破损的情况。同时,本发明粉末涂料依然可以实现130℃、3min快速固化,与市场主流mdf粉末涂料固化条件一致,因此客户无需更改涂装工艺。
[0063]
上述参照实施例对一种高硬度、耐磨抗划伤mdf粉末涂料及其制备方法进行的详细描述,是说明性的而不是限定性的,可按照所限定范围列举出若干个实施例,因此在不脱离本发明总体构思下的变化和修改,应属本发明的保护范围之内。