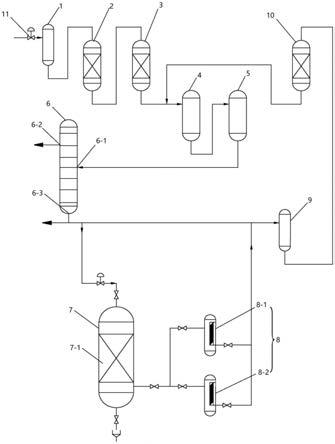
1.本实用新型涉及石油化工技术领域,尤其是涉及一种增产重石脑油的石油加氢裂化系统。
背景技术:
2.加氢裂化,是一种石油化工领域的常用工艺,即石油炼制过程中在较高的压力和温度下,氢气经催化剂作用使重质油发生加氢、裂化和异构化反应,转化为轻质油的加工过程。越来越多的石化生产厂区内的加氢裂化装置用途转变为主要用于生产重石脑油,为下游重整装置提供原料。加氢裂化工艺得到的重石脑油是重整装置的最优质原料,其产量直接决定了重整装置的原料供应情况,自产的加裂重石脑油越多,外购的石脑油量就越少,原料成本就越低;为此,努力提高加裂装置的重石脑油收率对企业原料成本控制有很大的经济利好。
3.目前,加氢裂化工艺主要采用两段法,例如,在中国专利文献上公开的“一种两段加氢裂化方法”,其公开号cn1952067,原料油与氢气混合后直接进入第一段加氢裂化反应器,第一段尾油循环至第二段加氢裂化反应器的入口。
4.然而,现有技术中的两段法加氢裂化工艺中,二段进料的循环油中容易富集hpna(稠环芳烃),造成二段裂化反应器的催化剂失活;为了减少hpna的富集,只能增大尾油的外甩量,导致重石脑油的产量较低,不利于提高经济效益。
技术实现要素:
5.本实用新型是为了克服现有技术中的两段法加氢裂化工艺中,二段进料的循环油中容易富集hpna,造成二段裂化反应器的催化剂失活;为了减少hpna的富集,只能增大尾油的外甩量,导致重石脑油的产量较低,不利于提高经济效益的问题,提供一种增产重石脑油的石油加氢裂化系统,在系统中增设hpna去除装置,部分循环油经hpna去除装置去除hpna后再进入二段裂化反应器,可有效降低hpna的累积速率,从而减少尾油外甩量,增加重石脑油的产量。
6.为了实现上述目的,本实用新型采用以下技术方案:
7.一种增产重石脑油的石油加氢裂化系统,包括一段工艺装置、hpna去除装置及二段工艺装置,所述一段工艺装置包括依次连接的一段精制反应器、一段裂化反应器、高压分离器、低压分离器及分馏塔;所述hpna去除装置包括相连接的hpna吸附罐和吸附后过滤器,所述hpna吸附罐内设有吸附填料;所述二段工艺装置包括二段裂化反应器;所述分馏塔上设有进料口、重石脑油出口及尾油出口,所述尾油出口分别与hpna吸附罐及二段裂化反应器连接,所述二段裂化反应器的出口与所述高压分离器连接。
8.本实用新型采用两段法进行石油的加氢裂化:原料油经过一段工艺装置进行一段裂化反应后,从分馏塔的尾油出口流出的尾油一部分进行外甩,另一部分作为循环油继续进入二段工艺装置进行二段裂化反应;同时,本实用新型在系统中设置了hpna去除装置,将
进入二段工艺装置中的循环油分流出一部分先经过hpna去除装置,对循环油中的稠环芳烃进行吸附去除,然后再与未经吸附的循环油混合进入二段工艺装置中进行二段裂化反应。
9.在本实用新型的hpna去除装置中,hpna吸附罐中的吸附填料可以有效吸附循环油中的稠环芳烃,降低了稠环芳烃的累积速率,从而可以减少尾油外甩量,减少的这部分外甩尾油可以作为二段工艺装置的进料,提高重石脑油的产量,为下游重整装置提供原料,从而创造大量经济效益。
10.作为优选,所述一段工艺装置中还包括设置在一段精制反应器前并与一段精制反应器相连接的一段进料缓冲罐。
11.作为优选,所述二段工艺装置中还包括设置在二段裂化反应器前并与二段裂化反应器相连接的二段进料缓冲罐,所述吸附后过滤器及分馏塔的尾油出口分别与二段进料缓冲罐连接。本实用新型在一段精制反应器和二段裂化反应器前分别设置进料缓冲罐,便于对一段精制反应器和二段裂化反应器的进料进行调节,保证进料和反应稳定性。
12.作为优选,所述吸附后过滤器包括并联的第一吸附后过滤器和第二吸附后过滤器,所述第一和第二吸附后过滤器的进口分别与hpna吸附罐连接,第一和第二吸附后过滤器的出口分别与二段进料缓冲罐连接。本实用新型在hpna吸附罐后设置了吸附后过滤器,对经过hpna吸附罐吸附后的循环油进行过滤,避免吸附填料被循环油携带进入二段工艺装置中,减少了进入二段工艺装置的循环油中的杂质。本实用新型采用两个并联的吸附后过滤器,系统运行时,一个吸附后过滤器用于过滤,另一个吸附后过滤器进行清洗,清洗完成后再进行交换,始终能够具有良好的过滤效果。
13.作为优选,所述吸附后过滤器内设有过滤精度为20~30μm的滤芯。
14.作为优选,所述一段进料缓冲罐的进口处、hpna吸附罐的进口处和出口处、吸附后过滤器的进口处和出口处分别设有控制阀。
15.作为优选,所述hpna吸附罐的高径比为3.2~3.3。hpna吸附罐的高径比在此范围内,可以保证吸附填料具有适当的装填量,并保证hpna吸附罐具有适当的进料量、水力学最大流通量及运行空速,使hpna吸附罐可以有效对循环油中的稠环芳烃进行吸附去除。
16.因此,本实用新型的有益效果为:在系统中设置了hpna去除装置,将进入二段工艺装置中的循环油分流出一部分先经过hpna去除装置,对循环油中的稠环芳烃进行吸附去除,降低了稠环芳烃的累积速率,从而可以减少尾油外甩量,减少的这部分外甩尾油可以作为二段工艺装置的进料,提高重石脑油的产量,为下游重整装置提供原料,从而创造大量经济效益。
附图说明
17.图1是本实用新型的一种连接结构示意图。
18.图中:1一段进料缓冲罐、 2一段精制反应器、 3一段裂化反应器、 4高压分离器、 5低压分离器、 6分馏塔、 6-1进料口、 6-2重石脑油出口、 6-3尾油出口、 7 hpna吸附罐、 7-1吸附填料、 8吸附后过滤器、 8-1第一吸附后过滤器、 8-2第二吸附后过滤器、 9二段进料缓冲罐、 10二段裂化反应器、 11控制阀。
具体实施方式
19.下面结合附图与具体实施方式对本实用新型做进一步的描述。
20.在本实用新型中,若非特指,所有设备和原料均可从市场购得或是本行业常用的,下述实施例中的方法,如无特别说明,均为本领域常规方法。
21.如图1所示,一种增产重石脑油的石油加氢裂化系统,包括一段工艺装置、hpna去除装置及二段工艺装置。一段工艺装置包括依次连接的一段进料缓冲罐1、一段精制反应器2、一段裂化反应器3、高压分离器4、低压分离器5及分馏塔6。hpna去除装置包括相连接的hpna吸附罐7和吸附后过滤器8,吸附后过滤器包括并联的第一吸附后过滤器8-1和第二吸附后过滤器8-2,第一和第二吸附后过滤器的进口分别与hpna吸附罐连接;hpna吸附罐的高径比为3.24,hpna吸附罐内设有吸附填料7-1,吸附填料装填体积为34m3;第一和第二吸附后过滤器内分别设有过滤精度为25μm的滤芯。二段工艺装置包括相连接的二段进料缓冲罐9和二段裂化反应器10;第一和第二吸附后过滤器的出口分别与二段进料缓冲罐连接;分馏塔上设有进料口6-1、重石脑油出口6-2及尾油出口6-3,尾油出口分别与hpna吸附罐及二段进料缓冲罐连接;二段裂化反应器的出口与高压分离器连接;一段进料缓冲罐的进口处、hpna吸附罐的进口处和出口处、吸附后过滤器的进口处和出口处分别设有控制阀11。
22.本实用新型中的系统运行时,原料油先进入一段工艺装置,从一段进料缓冲罐依次经过一段精制反应器和一段裂化反应器进行精制和裂化反应,反应产物依次经高压分离器和低压分离器进行气液分离,分离后的液相产物进入分馏塔,分馏后得到的重石脑油作为目标产物进行收集,便于后续利用;分馏后得到的尾油中1wt%进行外甩,99wt%作为循环油继续进入二段工艺装置进行二段裂化反应;进入二段工艺装置中的循环油中再分流出10wt%,先经过hpna去除装置,对此部分循环油中的稠环芳烃进行吸附去除,然后再与未经吸附的循环油混合进入二段工艺装置中进行二段裂化反应。hpna去除装置中,循环油先经过hpna吸附罐,hpna吸附罐中的吸附填料可以有效吸附循环油中的稠环芳烃,降低了稠环芳烃的累积速率,从而可以减少尾油外甩量;吸附后的循环油再进入吸附后过滤器中进行过滤,避免吸附填料被循环油携带进入二段工艺装置中,减少了进入二段工艺装置的循环油中的杂质;两个并联的吸附后过滤器,一个用于过滤,另一个进行清洗,清洗完成后再进行交换,确保始终能够具有良好的过滤效果。
23.本实用新型将二段进料循环油中的稠环芳烃脱除后,一方面对二段裂化反应器的催化剂失活有延缓作用,另一方面可以减少尾油的外甩量,使更多的循环油回到二段进料缓冲罐作为进料,提高装置生产效率,提高重石脑油的产量。不设置hpna去除装置时,尾油的外甩量需达到2wt%,才能避免稠环芳烃的富集,而本实用新型设置hpna去除装置后,可以将尾油外甩量降低至1wt%,按尾油转化重石脑油的能力推算,1w%的尾油可以转化至少0.6w%的重石脑油,即加氢裂化系统至少可以增产0.6w%的重石脑油,按照年处理量200万吨计算,每年可以增产重石脑油1.2万吨,具有显著的经济价值。