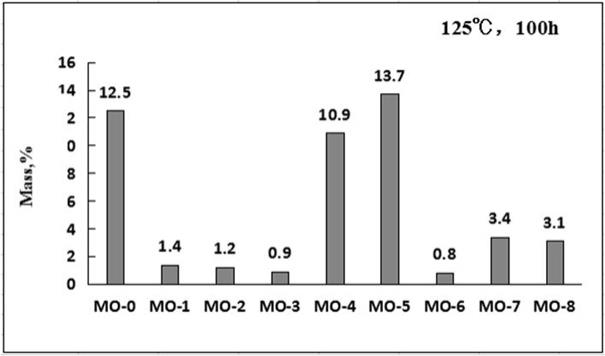
1.本发明具体涉及一种用于锂基润滑脂的抗氧化剂组合物。
背景技术:
2.润滑脂体系中脂肪酸皂的金属离子是润滑脂氧化反应的催化剂,在高温和长时间工况条件,会加速润滑脂氧化,从而导致润滑脂的结构受到破坏,造成皂油分离,生成腐蚀性产物,使用寿命缩短。通过加入抗氧剂可以阻碍润滑脂氧化, 钝化金属的催化作用,大大延长润滑脂的使用寿命。胺类抗氧剂、酚类抗氧剂和二烷基二硫代磷酸锌(zddp)等传统抗氧剂具有一定的热稳定性和抗氧化性,可以延长润滑脂寿命,已经有较多学者研究和推荐,广泛应用润滑脂产品。
3.但是,随着工业技术的发展,设备设计和制造技术在不断改进,向高温、高速和免维护方向发展,润滑条件愈加苛刻,大大提高了润滑产品在高温性能和长寿命性能方面的要求,因此急需寻找一种更加有效的润滑脂高温抗氧剂,以提高锂基润滑脂的抗氧化安定性和使用寿命。
技术实现要素:
4.基于现有的传统抗氧剂的不足,本发明的目的在于提供一种用于锂基润滑脂的抗氧化剂组合物,能够显著提高锂基润滑脂的抗氧化安定性和使用寿命。
5.为实现上述目的,本发明采用如下技术方案:一种用于锂基润滑脂的抗氧化剂组合物,所述抗氧化剂组合物由胺类或酚类和二甲基二硫代氨基甲酸铜按质量比1:2组成。
6.优选的,所述胺类为二苯胺,二异辛基二苯胺, n-苯基-α-萘胺,n-苯基-β-萘胺,n,n'-二仲丁基对苯二胺或n-环己基-n'-苯基对苯二胺。
7.优选的,所述酚类为2,6-二叔丁基对甲苯酚或高分子量酚型或2-萘酚。
8.优选的,所述抗氧化剂组合物在锂基润滑脂中的用量为0.3~2.0wt%。
9.本发明的优点在于:在润滑脂体系中,脂肪酸皂的金属离子是润滑脂氧化反应的催化剂,对基础油有促进氧化作用,而钠、锂的催化作用比钙和铝的催化作用更大。润滑脂制造中生成的甘油,也容易被氧化,其高温氧化产物是低分子酸。润滑脂使用进度范围很宽,工作环境也很复杂。高温工作环境,有害的物质侵入,使用时间加长,都是促进润滑脂氧化的条件。润滑脂氧化的结果是润滑脂的结构受到破坏,造成油皂分离,生成腐蚀性产物,滴点和稠度下降,使用寿命缩短。基础油在热、光和机械应力作用下产生自由基,发生链式自动氧化,在60℃以上,大约每升高10℃,氧化速率提高2倍。在有铁、铜等金属离子存在的氧化/还原系统中可以产生催化自动氧化,可以在较低的温度下引发氧化反应,同时将产生“雪崩”式的加速氧化,极大地损害润滑脂的质量。
10.润滑脂中添加抗氧剂的功能是阻碍基础油氧化,抑制皂基润滑脂中脂肪酸碳链和
甘油的氧化,钝化金属的催化作用,减少油品氧化变质,以延长润滑脂的使用寿命。胺类和酚类抗氧剂属于自由基拥获剂,用于捕获油品氧化产生的自由基并形成相对稳定的基团,阻止氧化反应的继续进行。其与二甲基二硫代氨基甲酸铜复配,可以起到良好的协同作用,阻止氧化的发生或者延缓发生,提高润滑脂的寿命,润滑脂的寿命是单独使用胺类或酚类抗氧剂的3~4.5倍。
附图说明
11.图1为9个样品在125℃高温试验后重量损失结果图;图2为样品mo-0在125℃高温薄片试验前后的红外光谱图;图3为样品mo-1在125℃高温薄片试验前后的红外光谱图;图4为样品mo-2在125℃高温薄片试验前后的红外光谱图;图5为样品mo-3在125℃高温薄片试验前后的红外光谱图;图6为样品mo-4在125℃高温薄片试验前后的红外光谱图;图7为样品mo-5在125℃高温薄片试验前后的红外光谱图;图8为样品mo-6在125℃高温薄片试验前后的红外光谱图;图9为样品mo-7在125℃高温薄片试验前后的红外光谱图;图10为样品mo-8在125℃高温薄片试验前后的红外光谱图;图11为9个样品在氧化安定性试验结束后的压力降图;图12为9个样品在氧化安定性试验结束后的基础油运动粘度变化图;图13为9个样品在氧化安定性试验结束后的基础油酸值变化图;图14为样品mo-0在氧化安定性试验前后的红外光谱图;图15为样品mo-1在氧化安定性试验前后的红外光谱图;图16为样品mo-2在氧化安定性试验前后的红外光谱图;图17为样品mo-3在氧化安定性试验前后的红外光谱图;图18为样品mo-4在氧化安定性试验前后的红外光谱图;图19为样品mo-5在氧化安定性试验前后的红外光谱图;图20为样品mo-6在氧化安定性试验前后的红外光谱图;图21为样品mo-7在氧化安定性试验前后的红外光谱图;图22为样品mo-8在氧化安定性试验前后的红外光谱图;图23为9个样品的轴承寿命试验结果图。
具体实施方式
12.为让本发明的上述特征和优点能更明显易懂,下文特举实施例,作详细说明。本发明的方法如无特殊说明,均为本领域常规方法。
13.以下探讨添加传统抗氧化添加剂和添加本发明新型抗氧化剂组合物的润滑脂样品在热稳定性、氧化安定性和润滑脂寿命性能对比试验。
14.1. 实验部分1.1 样品组成本次实验采用氢氧化锂、12-羟基硬脂酸、硬脂酸反应预置为锂基稠化剂,然后再
加入矿物油基础油,按1.2流程处理,分别添加胺类抗氧剂、酚类抗氧剂、二烷基二硫代磷酸锌盐、环烷酸铜、硬脂酸铜、二甲基二硫代氨基甲酸铜、二甲基二硫代氨基甲酸铜与胺类、二甲基二硫代氨基甲酸铜与酚类。样品分别按mo-1,mo-2,mo-3,mo-4,mo-5、mo-6、mo-7和mo-8编号。同时也准备了不含任何添加剂的基础脂mo-0样品对比实验。 样品组成信息见表1。
15.表 1样品组成信息注:表1中mo-1中胺类具体是辛基-丁基二苯胺;mo-2中酚类具体是高分子量型酚中的位阻酚类噻二唑btmt(cas no.: 125643-61-0);mo-7具体是指二甲基二硫代氨基甲酸铜与辛基-丁基二苯胺按质量比2:1混合;mo-8具体为二甲基二硫代氨基甲酸铜与高分子量型酚中的位阻酚类噻二唑btmt按质量比2:1混合。
16.1.2 样品制作1) 将锂基预制皂和部分基础油搅拌混合,加热到210-220℃,直至完全成液体。
17.2) 将热油皂混合液体转入剩余的基础油,搅拌冷却。
18.3) 在60-80℃加入添加剂,搅拌均匀。
19.4) 采用三辊磨研磨处理。
20.5)样品收集后脱气处理。
21.2. 样品测试2.1常规指标测试2.2 热稳定性试验(薄片试验)将润滑脂均匀地在钢片上涂为厚1mm,直径50mm的薄层,放置恒温烘箱内,观察润滑脂的重量损失和红外光谱变化。
22.2.3 氧化安定性试验(astm d942)1)压力降2)红外光谱3)基础油(抽出)运动粘度4)基础油(抽出)酸值5)润滑脂软硬度2.4 润滑脂寿命(参考astm d3336)3. 结果与讨论3.1 常规理化指标和实验结果数据表2为9个润滑脂样品常规理化指标分析结果。
23.表2常规理化指标和实验结果数据所有样品锥入度均为nlgi2号,滴点均大于180℃,在193到204℃范围。
24.3.2热稳定性试验(薄片试验)将润滑脂均匀地在钢片上涂抹厚1mm,直径50mm的薄层,放置恒温烘箱内,分别在125℃和150℃温度下恒温100小时。试验结束后观察润滑脂的重量损失和红外光谱变化情况。
25.3.2.1重量损失图1对比了9个样品在125℃高温试验后重量损失的实验结果。
26.在125℃高温薄片100小时试验后,样品mo-6和mo-3的重量损失少过1%,样品mo-1和mo-2重量损失分别为1.4%和1.2%。mo-7和mo-8的重量损失为3.4%和3.1%。样品mo-0,mo-4和mo-5试验结束后重量损失均超过10%。在125℃高温薄片试验后,重量损失方面mo-6《mo-3《mo-2《mo-1《mo-8《mo-7《mo-4《mo-0《mo-5。
27.在150℃高温薄片试验后,所有样品的重量损失均超过40%,样品试验中出现严重分油现象。这可能就是矿物油锂基润滑脂使用温度建议不超过120℃原因。3.2.2红外光谱图2到图10分别对比了9个样品在125℃高温薄片试验前后的红外光谱图。我们可以看到,样品mo-0,mo-4和mo-5在试验结束后的红外谱图在1710cm
−1附近出现很强的吸收峰。1710cm
−1处出现特征吸收峰,表明样品发生氧化产生酸性物质含
–
c=o光能团导致。样品mo-1,mo-2,mo-3,mo-6,mo-7和mo-8试验前后红外光谱没有出现明显变化,具有良好的热稳定性能。
28.3.3 氧化安定性试验氧化安定性试验结束后,我们分析对比了9个样品的压力降、基础油粘度,基础油酸值,红外光谱和软硬度结果。
29.图11对比了9个样品在氧化安定性试验结束后的压力降。样品mo-1,mo-2,mo-3,mo-6、mo-7和mo-8在试验结束后,压力降均低于30kpa,具有良好的抗氧化安定性能。样品mo-0,mo-4和mo-5在试验结束后,出现了很大的压力变化,压力降超过500kpa,表明样品抗氧化性能很差,出现了严重的氧化现象。
30.图12对比了9个样品在试验后的基础油(索氏提取法)粘度变化情况。样品mo-1,mo-2,mo-3,mo-6,mo-7和mo-8在试验结束后,粘度有稍微变小,变化值在-0.3%~-2.8%之间,具有良好的氧化稳定性。样品mo-4和mo-5试验后粘度增长超过35%,样品mo-0试验后粘度增长71.8%,表明这些样品出现了严重氧化现象。
31.图13对比了9个样品在试验后的基础油(索氏提取法)酸值变化情况。试验结束后,所有的样品的基础油酸值均出现增加现象。样品mo-1,mo-2,mo-3,mo-6、mo-7和mo-8基础油酸值增加值都小于3 mgkoh/g,具有良好的氧化稳定性能;而样品mo-0,mo-4和mo-5试验后,由于严重氧化,基础油酸值增加都接近甚至超过20 mgkoh/g。
32.图14到图22分别对比了9个样品在氧化安定性试验前后的红外光谱图。从红外光谱分析结果看,和热稳定性试验结果一样,样品mo-0,mo-4和mo-5在氧化安定性试验结束后,红外光谱图在1710 cm
−1附近出现很强的吸收峰,意味着样品氧化产生酸性物质含
–
c=o 光能团导致。样品mo-1,mo-2,mo-3,mo-6、mo-7和mo-8试验后红外光谱没有出现明显变化,表现出良好的氧化稳定性。
33.试验结束冷却后,手触摸样品表面,发现mo-0,mo-4和mo-5样品表面明显变硬,软硬不均。样品mo-1,mo-2,mo-3,mo-6,mo-7和mo-8手触摸表面软硬均匀,未出现异常硬化和软化现象。3.4 轴承润滑脂寿命试验轴承润滑脂寿命试验参考了astm d3336方法,试验条件见表3。
34.表3 寿命测试条件图23对比了9个样品的轴承寿命试验结果。
35.在150℃条件下,样品mo-6的寿命结果为147小时,mo-7的寿命结果为199小时,mo-8的寿命结果为172;这三个样品是样品mo-1,mo-2和mo-3寿命的3倍以上。样品mo-0,mo-4和mo-5在试验中由于严重漏脂导致在很短的时间就试验终止。
36.4. 结论(1)添加二甲基二硫代氨基甲酸铜的样品mo-6和含胺类、酚类以及二烷基二硫代磷酸锌盐等传统抗氧化添加剂的mo-1,mo-2和mo-3一样,都具有良好的热稳定性和氧化安定性能,但是mo-1,mo-2和mo-3的润滑脂在150℃时寿命短,因此在高温(如150℃)应用领
域,胺类、酚类以及二烷基二硫代磷酸锌盐zddp不适合单独使用作为锂基润滑脂的抗氧化添加剂。
37.(2)添加二甲基二硫代氨基甲酸铜的样品mo-6,mo-7,mo-8在轴承润滑脂寿命试验结果最好,在高温150℃条件下,寿命结果是传统胺类、酚类以及二烷基二硫代磷酸锌盐抗氧剂的3倍以上。
38.(3)添加环烷酸铜的样品mo-4和添加硬脂酸铜的mo-5在热稳定性试验、氧化安定性试验和轴承润滑脂寿命试验结果不理想,因此环烷酸铜和硬脂酸铜不适合单独使用作为锂基润滑脂的抗氧化添加剂。
39.综上,二甲基二硫代氨基甲酸铜可以考虑作为抗氧化剂用在锂基润滑脂提高氧化稳定性和润滑脂寿命,并且,其与胺类或酚类复配后,可以起到良好的协同作用,提高润滑脂的寿命,尤其是二甲基二硫代氨基甲酸铜与胺类复配后,不仅提高了抗氧化性同时还提高了润滑脂的使用寿命,效果显著。
40.以上所述仅为本发明的较佳实施例,凡依本发明申请专利范围所做的均等变化与修饰,皆应属本发明的涵盖范围。