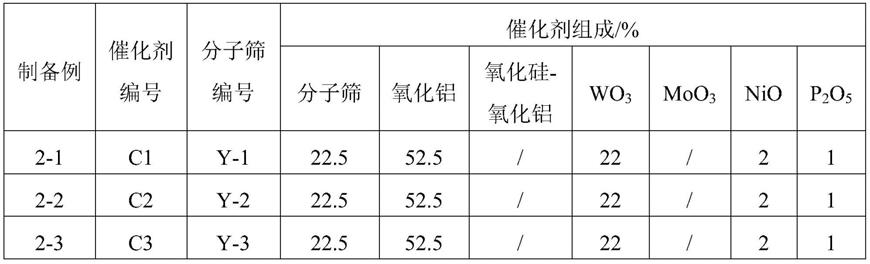
1.本发明涉及一种处理富含芳烃馏分油的方法。
背景技术:
2.随着环保法规的日益严格,清洁汽、柴油的生产成为人们日益关注的问题。世界许多国家的燃油新标准和环保法规对车用柴油制定了严格的要求,要求柴油产品具有低的硫含量和芳烃含量以及高的十六烷值,目前,由于催化裂化作为重要的油品轻质化工艺,我国柴油池中约有1/3来自催化裂化柴油(lco),这部分柴油具有密度大、杂质及芳烃含量高、十六烷值低、安定性差等特点,难以直接满足清洁柴油的标准,需要高苛刻度的加氢过程才能作为清洁柴油的调合组分,操作成本高,经济效益差。
3.近年来,随着高苛刻度催化裂化技术如多产异构烷烃的催化裂化技术(mip)的广泛应用,mip催化柴油中芳烃含量尤其是多环芳烃含量进一步升高,十六烷值进一步降低。而随着环保意识的不断增强,国家对普通柴油的清洁质量要求不断升级,同时柴油的市场需求明显下降,柴油过剩问题凸显。因此,将劣质柴油加工成高附加值产品显得很有必要。
4.同时,由于我国汽车市场的扩大,目前对汽油的需求量持续增加。炼油化工企业生产汽油及芳烃的主要装置之一是催化裂化装置,如fcc装置。结合加氢处理、催化裂化工艺过程的特点,中国石化石科院已成功开发了加氢处理—催化裂化生产高辛烷值汽油组分的单/双向组合技术。该技术先将lco加氢精制,然后作为催化裂化装置的进料。lco中芳烃大部分为双环以上芳烃(多环芳烃),lco加氢精制的目的就是将lco中的多环芳烃进行选择性加氢,在饱和多环芳烃的同时保留单环芳烃。但是由于在加氢过程中多环芳烃尤其是萘类的选择性加氢产物是四氢萘类,四氢萘在进一步的催化裂化过程中易发生氢转移反应,对提高催化裂化的转化率造成困难,因此需要在加氢过程中对四氢萘类进行有效转化,抑制其在催化装置中氢转移的反应路径。
5.cn 110551525 a公开了一种催化裂化柴油生产btx馏分的方法,将催化裂化柴油切割为轻催化裂化柴油馏分和重催化裂化柴油馏分,轻催化裂化柴油馏分进入低压加氢裂化单元进行反应,重催化裂化柴油馏分进入加氢处理单元后,所得液相物流进入催化裂化单元,与催化裂化催化剂接触进行反应,其反应生成物进入分馏系统,分馏后得到干气、液化气、富含btx馏分、柴油馏分。该方法可根据催化裂化柴油原料硫氮杂质多,芳烃含量高的特点,采用组合工艺的技术方案来生产富含btx馏分。
6.cn 108795495 a公开了一种柴油原料的处理方法,将柴油原料油切割成轻柴油馏分和重柴油馏分,所得的轻柴油馏分在第一反应区进行反应,得到富含环烷烃的组分,重柴油馏分在第二反应区反应,所得的加氢重柴油馏分进入催化裂化单元,在催化裂化催化剂的存在下进行催化裂化反应,反应油气经过分离后得到富含芳烃族化合物的汽油产品。
7.cn 110437875 a公开了一种催化裂化柴油加氢异构-流化催化裂解的方法,包括如下步骤:将催化裂化柴油与氢气混合,进入一段串联的加氢反应装置,所述的加氢反应装置内进行加氢精制-加氢异构反应;之后的加氢异构柴油进入流化床催化裂解装置,进行催
化裂解反应。本发明方法利用催化裂化柴油生产低碳烯烃和清洁燃料油品,产物中低碳烯烃含量>35质量%,汽油馏分中芳烃含量>50质量%。
技术实现要素:
8.本发明针对现有技术存在的问题,提供一种处理富含芳烃馏分油的方法。
9.本发明提供的方法,包括:
10.(1)富含芳烃馏分油经切割后得到轻馏分和重馏分,切割点为220-240℃,所述富含芳烃馏分油的馏程为150-400℃,总芳烃的含量为60-90重量%;
11.(2)将重馏分送至加氢单元,依次通过加氢精制反应区与加氢异构反应区,加氢精制反应区装填加氢精制催化剂,加氢异构反应区装填加氢异构催化剂,反应流出物经分离后得到加氢重馏分,加氢重馏分的馏程范围为200-400℃,以进入加氢异构反应区液体进料为基准,所述加氢异构反应区液体产物的单环芳烃异构选择性不低于15%;
12.(3)将轻馏分和加氢重馏分送至催化裂化单元进行催化裂化反应,反应流出物经分离至少得到气体、催化裂化汽油馏分、催化裂化柴油馏分。
13.在本发明中,在优选的情况下,所述富含芳烃馏分油中双环以上芳烃的含量为40-80重量%,所述富含芳烃馏分油的十六烷值小于25。
14.在优选的情况下,所述富含芳烃馏分油选自催化裂化柴油馏分、焦化柴油馏分、乙烯裂解油馏分、煤焦油中的一种或几种。
15.在优选的情况下,加氢精制反应区的反应条件包括:氢分压为3-12mpa,反应温度为300-400℃,氢油体积比为400-1600nm3/m3,液时体积空速为0.3-4h-1
;
16.加氢异构反应区的反应条件包括:氢分压为3-12mpa,反应温度为300-400℃,氢油体积比为400-1600nm3/m3,液时体积空速为0.3-4h-1
;
17.以加氢精制催化剂和加氢异构催化剂的总体为基准,加氢精制催化剂装填比例为40-70体积%,加氢异构催化剂装填比例为30-60体积%。
18.现有技术中,采用高芳烃含量的馏分油生产高辛烷值汽油组分或者芳烃组分时,需先将馏分油原料中多环芳烃选择性加氢,然后作为催化裂化单元进料。多环芳烃的加氢饱和是逐环进行的,第一个环加氢饱和反应通常比单环芳烃加氢饱和反应速率常数大,也就是说多环芳烃第一个环的加氢较单环芳烃的加氢饱和容易,因此,在一定的加氢深度下,可有效保留单环芳烃。
19.此外,萘类等多环芳烃的选择性加氢饱和产物是四氢萘类化合物。四氢萘类化合物在分子筛催化剂上进行催化裂化时,存在双分子及单分子两条反应路径,其中单分子反应路径为通过环烷烃开环反应,生成丙烷、丙烯、丁烷、丁烯、甲基戊烷、环戊烷、环己烷等非芳烃,以及苯、c1~c4烷基取代苯等单环芳烃。由于该路径产物的价值较高,为理想路径。双分子反应路径为四氢萘类化合物通过脱氢缩合反应生成萘、烷基萘、菲、芘等多环芳烃直至焦炭等,该路径在催化裂化反应中占一定比例,但需要尽可能避免。
20.由于富含芳烃馏分油原料中的双环芳烃主要以萘类的形式存在,并且大部分是有烷基取代的萘类化合物,因此加氢后原料中的四氢萘类化合物多数以烷基取代的四氢萘类形式存在。本发明的发明人通过研究发现,环烷环上的取代基在催化裂化反应中会明显促进氢转移反应,从而造成催化裂化装置的汽油产率降低。
21.本发明的发明人通过研究进一步发现,四氢萘类中的六元环烷环在临氢条件下,在酸性催化剂上可以异构生成五元环,即四氢萘类化合物可转化成为茚满类化合物,茚满类化合物在催化裂化反应中,较少发生氢转移反应,更易发生开环裂化及断侧链反应,从而生成烷基取代的单环芳烃,即催化裂化装置的理想目标产物。此外,由于芳烃的加氢饱和反应为可逆反应,多环芳烃加氢生成四氢萘,与四氢萘脱氢生成多环芳烃反应之间存在一定平衡。但是在加氢异构过程中,随着四氢萘类异构反应的进行,芳烃加氢饱和反应之间的平衡被打破,从而进一步促进了多环芳烃转化为单环芳烃。
22.基于上述研究,本发明将富含芳烃馏分油进行切割,得到富含单环芳烃的轻馏分和富含多环芳烃的重馏分,切割点为220-240℃。将轻馏分送至催化裂化单元进行催化裂化反应,将富含单环芳烃的轻馏分转化为烷基取代的单环芳烃。将重馏分送至加氢单元,在加氢精制催化剂存在下,进行加氢脱硫、加氢脱氮反应,同时进行多环芳烃选择性加氢饱和反应生成六元环烷取代的单环芳烃,加氢精制反应区的反应流出物在加氢异构催化剂存在下,进行六元环烷取代的单环芳烃加氢异构反应生成五元环烷取代的单环芳烃(茚满类化合物)。
23.在优选的情况下,以进入加氢单元的重馏分为基准,加氢精制反应区液体产物中多环芳烃的饱和率不低于60%,单环芳烃选择性不低于85%;
24.以进入加氢异构反应区液体进料为基准,所述加氢异构反应区液体产物中多环芳烃的饱和率不低于80重量%,单环芳烃选择性不低于80%,单环芳烃异构选择性不低于重量18%;其中,
25.多环芳烃饱和率=(a
p1-a
p2
)/a
p1
*100%
26.单环芳烃选择性=(a
m2-a
m1
)/(a
p1-a
p2
)*100%
27.单环芳烃异构选择性=(a
i2-a
i1
)/(a
p1-a
p2
+a
m1
)*100%
28.式中:a
p1
—反应区液体进料中多环芳烃含量,质量%
29.a
p2
—反应区液体产品中多环芳烃含量,质量%
30.a
m1
—反应区液体进料中单环芳烃含量,质量%
31.a
m2
—反应区液体产品中单环芳烃含量,质量%
32.a
i1
—反应区液体进料中茚满类化合物含量,质量%
33.a
i2
—反应区液体产品中茚满类化合物含量,质量%。
34.本发明所述的“多环芳烃含量”指的是以质谱法(分析方法sh/t-0606)得到的质谱组成数据中双环以上芳烃其中包括双环芳烃本身的质量分数之和。
35.本发明所述的“单环芳烃含量”指的是以质谱法(分析方法sh/t-0606)得到的质谱组成数据中单环芳烃的质量分数。
36.本发明所述的“茚满类化合物含量”指的是以质谱法(分析方法sh/t-0606)得到的质谱组成数据中茚满类化合物的质量分数。
37.本发明对加氢精制催化剂没有特别限定,本领域常规的加氢精制催化剂都可以应用,包括市售加氢精制催化剂和实验室制备的加氢精制催化剂。
38.在本发明其中一种优选的实施方式中,所述加氢精制催化剂包括载体和负载在所述载体上的活性金属组分;所述载体选自氧化铝、氧化硅、氧化钛、氧化镁、氧化锆、氧化钍、氧化铍中的一种或几种;
39.所述活性金属组分为至少一种选自第vib族的金属元素和至少一种选自第viii族的金属元素,所述第vib族金属元素为钼和/或钨,所述第viii族金属元素为钴和/或镍;
40.以加氢精制催化剂的干基重量为基准并以氧化物计,至少一种选自第vib族的金属元素的含量为1-30重量%,至少一种选自第viii族的金属元素的含量为3-35重量%。
41.在本发明其中一种优选的实施方式中,所述加氢精制催化剂载体为氧化铝,活性金属组分为镍和钨。
42.在优选的情况下,所述加氢精制催化剂的堆密度为0.4-1.3g/cm3,平均颗粒直径为0.08-1.2mm,比表面积为100-300m2/g。
43.在本发明中,堆密度采用催化剂堆密度分析方法(q/sh 3360 245-2014)测定。
44.比表面积采用低温氮气吸附法(符合gb/t5816-1995标准)测定。
45.在优选的情况下,所述加氢异构催化剂含有包括载体和负载在所述载体上的活性金属组分,所述载体包括基质和y分子筛,以所述载体为基准,所述y分子筛的含量为10-60重量%,所述基质的含量为40-90重量%;
46.所述基质选自氧化铝、氧化硅和氧化硅-氧化铝中的一种或多种;
47.所述活性金属组分包括至少一种选自第viii族的金属组分和至少一种选自第vib族的金属组分。
48.进一步优选,以所述载体为基准,所述y分子筛的含量为15-45重量%,所述基质的含量为55-85重量%。
49.在优选的情况下,以所述加氢异构催化剂为基准,以氧化物计,所述第viii族的金属组分含量为1-10重量%,第vib族的金属组分含量为5-50重量%。
50.进一步优选,以所述加氢异构催化剂为基准,以氧化物计,所述第viii族的金属组分含量为2-8重量%,第vib族的金属组分含量为10-35重量%。
51.上述加氢异构催化剂可以实现本发明,但本发明的发明人发现,通过采用一种优选的加氢异构催化剂,其具有更高的异构效果,能进一步提高单环芳烃异构比例。优选的加氢异构催化剂由于具有良好的加氢与异构活性协同作用,使得四氢萘类可以异构生成茚满类,但并不进一步开环并断侧链,能够有效降低加氢单元氢耗,同时还具有良好的加氢异构催化剂的稳定性。在本发明优选的实施方式中,所述y分子筛的晶胞常数为2.415-2.440nm;所述y分子筛的强酸酸量占总酸量比例70%以上。
52.本发明中y分子筛的强酸是指nh3程序升温脱附(nh
3-tpd)曲线中脱附温度大于320℃的酸,强酸酸量占总酸量的比例是指nh
3-tpd结果中脱附温度大于320℃强酸酸量与总酸酸量的比值。
53.在优选的情况下,所述y分子筛的27al mas nmr谱中化学位移为0
±
2ppm共振信号的峰面积占总峰面积的比例不大于4%,优选不大于3%。
54.在优选的情况下,所述y分子筛的微孔比表面积至少为650m2/g,更优选至少为700m2/g;所述y分子筛的介孔体积占总孔体积的比例为30%-50%,更优选为33%至45%。
55.进一步优选,所述y分子筛的微孔比表面积至少为700m2/g,所述y分子筛的介孔体积占总孔体积的比例为33%-45%。
56.本发明对上述加氢异构催化剂的制备方法没有特别限定。在其中一种优选的实施方式中,加氢异构催化剂通过以下方法制备得到:
57.将y分子筛、基质混合均匀并添加助剂成型后焙烧得到所述载体;
58.用含有金属组分的溶液浸渍所述载体,经干燥焙烧后得到所述加氢异构催化剂。
59.本发明的加氢异构催化剂中,载体包括分子筛和基质,视不同要求可制成各种易于操作的成型物,例如微球、球形、片剂或条形等。该成型可按常规的方法进行,例如,将分子筛和基质挤条成型并焙烧的方法制备。在载体挤出成型时,可以向载体中加入适量助挤剂和/或胶粘剂,然后挤出成型。所述助挤剂、胶溶剂的种类及用量为本领域技术人员所公知,例如常见的助挤剂可以选自田菁粉、甲基纤维素、淀粉、聚乙烯醇、聚乙醇中的一种或几种。
60.在加氢异构催化剂的制备过程中,在足以将活性金属组分负载于载体上的前提下,本发明对负载方法没有特别限制,优选的方法为浸渍法,包括配制含金属组分的化合物的浸渍溶液,之后用该溶液浸渍载体。浸渍方法为常规方法,例如,可以是过量液浸渍、孔饱和法浸渍法。其中,通过对含金属组分的浸渍溶液的浓度、用量或载体用量的调节和控制,可以制备出指定含量的催化剂,这是本领域技术人员所容易理解和实现的。
61.在其中一种优选的实施方式中,本发明加氢异构催化剂中的y分子筛是以nay分子筛为原料,经多次交换和三次水热焙烧制备得到,其中每次水热焙烧之前至少进行一次交换处理,在第三次水热焙烧后至少进行两次交换处理;除第一次水热焙烧前采用铵盐进行交换外,第二次水热焙烧和第三次水热焙烧前要额外加入脱铝剂进行化学脱铝,第三次水热焙烧后,至少需要连续两次额外加入脱铝剂进行脱铝,并且在最后一次脱铝过程中采用含硅的脱铝剂进行。
62.具体而言,本发明优选的加氢异构催化剂中的y分子筛可通过以下制备方法得到:
63.将nay分子筛与铵盐和水混合进行第一铵交换处理,得到第一铵交换分子筛;
64.将所述第一铵交换分子筛在水蒸气气氛中进行第一水热焙烧处理,得到第一水焙分子筛;
65.将所述第一水焙分子筛与铵盐和水混合后进行第二铵交换处理,再加入第一脱铝剂进行第一脱铝处理,得到第二铵交换分子筛;
66.将所述第二铵交换分子筛在水蒸气气氛中进行第二水热焙烧处理,得到第二水焙分子筛;
67.将所述第二水焙分子筛与铵盐和水混合后进行第三铵交换处理,再加入第二脱铝剂进行第二脱铝处理,得到第三铵交换分子筛;
68.将所述第三铵交换分子筛在水蒸气气氛中进行第三水热焙烧处理,得到第三水焙分子筛;
69.将所述第三水焙分子筛与铵盐和水混合后进行第四铵交换处理,再加入第三脱铝剂进行第三脱铝处理,得到第四铵交换分子筛;以及将所述第四铵交换分子筛与铵盐和水混合后进行第五铵交换处理,再加入第四脱铝剂进行第四脱铝处理,之后经过滤、洗涤得到所述y分子筛,
70.其中,所述铵盐各自独立地选自氯化铵、硝酸铵、碳酸铵、碳酸氢铵、草酸铵、硫酸铵、硫酸氢铵中的一种或多种,所述第一脱铝剂、所述第二脱铝剂和所述第三脱铝剂各自独立地选自有机酸、无机酸以及有机和无机盐中的一种或多种。优选,所述有机酸选自乙二胺四乙酸、草酸、柠檬酸和磺基水杨酸中一种或多种,所述无机酸选自氟硅酸、盐酸、硫酸和硝
酸中一种或多种,所述有机和无机盐选自草酸铵、氟化铵、氟硅酸铵和氟硼酸铵中一种或多种。
71.所述第四脱铝剂包括含硅的脱铝剂以及有机酸和/或无机酸。在优选的情况下,所述的含硅的脱铝剂为氟硅酸、氟硅酸铵或者氟硅酸和氟硅酸铵的混合物,所述有机酸选自乙二胺四乙酸、草酸、柠檬酸和磺基水杨酸中的一种或多种,所述无机酸选自盐酸、硫酸和硝酸中的一种或多种。
72.在优选的情况下,所述第一铵交换处理中,所述nay分子筛:铵盐:水=1:0.3~1.0:5~10;
73.所述第二铵交换处理和所述第一脱铝处理中,所述第一水焙分子筛:铵盐:所述第一脱铝剂:水=1:0~0.50:0.02~0.3:5~10;
74.所述第三铵交换处理和所述第二脱铝处理中,所述第二水焙分子筛:铵盐:所述第二脱铝剂:水=1:0~0.50:0.02~0.3:5~10;
75.所述第四铵交换处理和所述第三脱铝处理中,所述第三水焙分子筛:铵盐:所述第三脱铝剂:水=1:0~0.70:0.02~0.3:5~10;
76.所述第五铵交换处理和所述第四脱铝处理中,所述第四铵交换分子筛:铵盐:所述含硅脱铝剂:所述有机酸和/或无机酸:水=1:0.02~0.70:0.02~0.3:0~0.07:5~10。
77.本发明上述加氢异构催化剂中的制备方法中,y分子筛由多次脱铝及三次水焙制备得到,脱铝过程形成的铝空位可在水焙过程中尽可能多地由硅进行填充,而产生的非骨架铝通过多次脱铝而逐步剥离,三次水热焙烧和多次脱铝相辅相成,有利于保持晶体的完整,保留更多的强酸中心。
78.本发明优选的加氢异构催化剂中的y分子筛硅铝比高,非骨架铝少,强酸中心比例高,比表面积大,二次孔丰富,在多环芳烃加氢异构过程中具有更高的反应活性且开环裂化等二次反应少;同时金属组分分散好,加氢异构催化剂上加氢功能与异构功能协同作用强,加氢异构催化剂失活缓慢、稳定性好。
79.根据本发明,加氢反应区的反应流出物经换热和气液分离后得到富氢气体和加氢重馏分。其中,所述换热的程度优选使得尽可能多的重馏分的加氢产物以液体的形式存在,从而能够在后续的气液分离中能够有效地将重馏分加氢产物和富氢气体进行分离。经过分离后,所得加氢重馏分可以送至催化裂化单元中,所得富氢气体可以循环至加氢单元作为加氢单元的至少部分氢气。
80.在本发明的催化裂化单元中,在优选的情况下,催化裂化单元的反应条件包括:温度为520-580℃,更优选为520-560℃,剂油质量比为4-10,更优选为4-8,油气停留时间为2-15s,更优选为2-14s,压力为0.1-0.3mpa,水蒸气/催化裂化原料油质量比为0-0.20,更优选为0-0.15。
81.本发明对催化裂化催化剂没有任何限定,所述催化裂化催化剂可以为本领域常规的催化裂化催化剂。所述催化裂化还包括在老化剂的存在下进行,所述老化剂可以为本领域常规的用于催化裂化的老化剂。
82.所述催化裂化单元中,还包括任选的催化裂化原料油,可以为但不限于焦化蜡油、常压渣油、减压馏分油、减压渣油中一种或多种。
83.根据本发明,催化裂化所得产品通常包括液化气、催化裂化汽油馏分、催化裂化柴
油馏分及油浆。所述催化裂化汽油馏分的馏程范围为65-180℃,所述催化裂化柴油馏分的馏程范围在150-450℃之内,优选为在150-400℃之内,总芳烃的含量为60-90重量%,双环以上芳烃的含量为40-80重量%。
84.优选的,所述催化裂化柴油在20℃的密度为0.900-0.970g/cm3。
85.优选的,所述催化裂化柴油的单环芳烃含量为10.0-32.0重量%。
86.优选的,所述催化裂化柴油的十六烷值小于25。
87.在本发明其中一种优选的实施方式中,在催化裂化单元的分馏系统直接将催化裂化柴油馏分进行切割,然后得到催化裂化柴油轻馏分和催化裂化柴油重馏分,切割点为220-240℃。
88.在本文中所披露的范围的端点和任何值都不限于该精确的范围或值,这些范围或值应当理解为包含接近这些范围或值的值。对于数值范围来说,各个范围的端点值之间、各个范围的端点值和单独的点值之间,以及单独的点值之间可以彼此组合而得到一个或多个新的数值范围,这些数值范围应被视为在本文中具体公开。
89.本发明具有以下优点:
90.1、本发明对富含芳烃馏分油进行切割,得到轻馏分和重馏分,一方面轻馏分不进行加氢,直接为催化裂化单元提供可生产高辛烷值汽油的原料。另一方面,通过对重馏分进行加氢精制与加氢异构合理匹配,控制异构过程而避免过度加氢饱和,通过这两个方面结合,明显降低了加氢单元总氢耗。
91.2、本发明在加氢单元提高了多环芳烃的转化率与生成单环芳烃的选择性,并通过控制单环芳烃异构选择性,即在加氢异构过程中促使四氢萘类的环烷环异构生成带有茚满类化合物。通过上述加氢单元与催化裂化单元结合,可抑制了催化裂化中氢转移等非理想反应,明显提高催化裂化产物中高辛烷值汽油产品的收率,提高其芳烃含量,避免非理想副产品的生成。
92.3、本发明优选的加氢异构催化剂通过使用硅铝比高、非骨架铝少、比表面积大、二次孔丰富、强酸中心比例高的y分子筛,改善了加氢异构催化剂的扩散通道,提高了加氢异构催化剂的加氢功能与异构功能的协同作用,进一步提高了单环芳烃异构选择性。
具体实施方式
93.下面的实施例将对本发明提供的方法予以进一步的说明,但并不因此而限制本发明。
94.制备例1
95.本制备例用于说明加氢精制催化剂的来源
96.加氢精制催化剂为购买的成型rs-2100催化剂,由中国石化股份有限公司长岭催化剂分公司生产,为镍-钼催化剂,堆密度为0.82g/cm3,平均颗粒直径为2-3mm,比表面积为165m2/g。
97.制备例2-1
98.本制备例用于说明加氢异构催化剂及其制备方法。
99.所用的原料规格如下:
100.nay分子筛,工业品,硅铝比>4.7,结晶度>85%
101.硫酸、盐酸、硝酸、草酸(固体)、硝酸铵、硝酸铵、氯化铵、草酸铵、硫酸铵为化学纯;所用氟硅酸纯度为工业级
102.具体制备方法如下:
103.(1)以nay沸石为原料用硫酸铵溶液进行交换,处理条件为:按照nay分子筛(干基):硫酸铵:水=1:1.0:10的比例,在90℃下交换2h,过滤后经去离子水洗涤,在120℃下干燥4h。
104.(2)将步骤(1)得到的分子筛,进行第一次水热焙烧处理,焙烧温度为520℃,在100%水蒸气气氛下焙烧2h。
105.(3)将步骤(2)得到的分子筛按分子筛(干基):硫酸:氯化铵:水=1:0.06:0.40:9的比例,先将分子筛加水打浆后缓慢滴加浓度为20%的硫酸,控制滴加时间30min,升温,于70℃下处理40min,过滤后经去离子水洗涤,在120℃下干燥4h。
106.(4)将步骤(3)得到的分子筛进行第二次水热焙烧处理,焙烧温度为620℃,在100%水蒸气气氛下焙烧2h。
107.(5)将步骤(4)得到的分子筛按分子筛(干基):硫酸:水=1:0.09:8的比例,先将分子筛加水打浆后,缓慢滴加浓度为20%的硫酸,控制滴加时间30min,升温于70℃下处理60min,过滤后经去离子水洗涤,在120℃下干燥4h。
108.(6)将步骤(5)得到的分子筛进行第三次水热焙烧处理,焙烧温度为650℃,在100%水蒸气气氛下焙烧2h。
109.(7)将步骤(7)得到的分子筛按分子筛(干基):硫酸:水=1:0.09:8的比例,先将分子筛加水打浆后,缓慢滴加浓度为30%的硫酸,控制滴加时间40min,升温,于70℃下处理60min,过滤后经去离子水洗涤。
110.(8)将步骤(7)得到的分子筛按分子筛:硫酸铵:氟硅酸:硫酸:h2o=1:0.2:0.05:0.02:8的比例,先将分子筛加水打浆后,加入硫酸铵,缓慢滴加浓度为30%的氟硅酸和20%浓度的硫酸,控制滴加时间40min,升温后于80℃下处理90min,过滤后经去离子水洗涤,得到分子筛y-1,其各项参数如表1所示。
111.(9)称取干基为70%的拟薄水铝石(催化剂长岭分公司)200.0克和干基为82%的分子筛y-1(步骤8所制得)73.2克混合均匀,在挤条机上挤成外圆直径为1.6毫米的三叶条形,于120℃烘干3小时,600℃焙烧4小时得到催化剂载体z1。
112.(10)取载体z1 100克,用80毫升分别含wo
3 275.0克/升、nio 25.0克/升、p2o
5 12.5克/升的偏钨酸铵、碱式碳酸镍、磷酸和柠檬酸混合溶液浸渍3小时,于120℃烘干3小时后180℃活化3小时,得到加氢异构催化剂c1。
113.以加氢异构催化剂c1为基准,加氢异构催化剂c1焙烧后的组成如表2所示。
114.制备例2-2
115.具体制备方法如下:
116.(1)以nay沸石为原料用硫酸铵溶液进行交换,处理条件为:按照nay分子筛(干基):硫酸铵:水=1:0.5:7的比例,在80℃下交换1h,过滤后经去离子水洗涤,在120℃下干燥4h。
117.(2)将步骤(1)得到的分子筛,进行第一次水热焙烧处理,焙烧温度为670℃,在100%水蒸气气氛下焙烧2h。
118.(3)将步骤(2)得到的分子筛按照分子筛(干基):草酸:硝酸铵:水=1:0.20:0.40:9的比例,先将分子筛加水打浆,于室温在搅拌下加入硝酸铵,再加入草酸,搅拌60min,过滤后经去离子水洗涤两次,在120℃下干燥3h。
119.(4)将步骤(3)得到的分子筛进行第二次水热焙烧处理,焙烧温度为645℃,在100%水蒸气气氛下焙烧2.5h。
120.(5)将步骤(4)得到的分子筛加入7倍水打浆,浆液升温至60℃后,按分子筛(干基):硝酸:草酸铵:水=1:0.13:0.2的比例,将草酸铵和硝酸及水配置成溶液,将水溶液加入分子筛浆液中,控制滴加时间30min,于60℃下继续搅拌40min,过滤后经去离子水洗涤,在105℃下干燥2h。
121.(6)将步骤(5)得到的分子筛进行第三次水热焙烧处理,焙烧温度为670℃,在100%水蒸气气氛下焙烧2h。
122.(7)将步骤(6)得到的分子筛按分子筛(干基):硫酸:硝酸铵:水=1:0.13:0.30:9的比例,先将分子筛加适量水打浆后,再加入硝酸铵,后匀速加入浓度为30%的硫酸水溶液,控制滴加时间40min,升温,于70℃下处理60min,过滤后经去离子水洗涤,在120℃下干燥4h。
123.(8)将步骤(7)得到的分子筛按分子筛:硫酸铵:h2sif6:h2o=1:0.2:0.15:7的比例,先将分子筛加水打浆后,加入硫酸铵,缓慢滴加浓度为30%的氟硅酸,控制滴加时间60min,升温后于60℃下处理50min,过滤后经去离子水洗涤,在120℃下烘干,得到分子筛y-2,其各项参数如表1所示。
124.(9)称取干基为70%的拟薄水铝石(催化剂长岭分公司)200.0克和干基为81%的分子筛y-2(步骤8所制得)74.1克混合均匀,在挤条机上挤成外接圆直径为1.6毫米的三叶条形,于120℃烘干3小时,600℃焙烧4小时得到催化剂载体z2。
125.(10)取载体z2 100克,用81毫升分别含wo
3 271.6克/升、nio 24.7克/升、p2o
5 12.3克/升的偏钨酸铵、碱式碳酸镍、磷酸和柠檬酸混合溶液浸渍3小时,于120℃烘干3小时后180℃活化3小时,得到加氢异构催化剂c2。
126.以加氢异构催化剂c2为基准,加氢异构催化剂c2焙烧后的组成如表2所示。
127.制备例2-3
128.称取干基为70%的拟薄水铝石(催化剂长岭分公司)100.0克和干基为76%的现有y分子筛(标记为y-3,催化剂长岭分公司,商业牌号lay)78.9克混合均匀,在挤条机上挤成外接圆直径为1.6毫米的三叶条形,于120℃烘干3小时,600℃焙烧4小时得到催化剂载体z3。
129.取载体z3 100克,用75毫升分别含wo
3 293.3克/升、nio 26.7克/升、p2o
5 13.3克/升的偏钨酸铵、碱式碳酸镍、磷酸和柠檬酸混合溶液浸渍3小时,于120℃烘干3小时后180℃活化3小时,得到加氢异构催化剂d1。
130.以加氢异构催化剂c3催化剂为基准,加氢异构催化剂c3焙烧后的组成如表2所示。
131.表1制备例分子筛的参数
132.分子筛晶胞常数/nm介孔比例/%强酸比例/%微孔比表面积/(m2/g)a0±
2ppm
/a
总
/%
*
y-12.42642806853.2y-22.42036757104.0
y-32.45320616177.2
133.注:*表示
27
al mas nmr谱中化学位移为0
±
2ppm共振信号的峰面积占总峰面积的比例。
134.表2加氢异构催化剂的组成
[0135][0136]
催化剂硫化
[0137]
如上制备的各催化剂采用程序升温硫化法将氧化态催化剂转化为硫化态催化剂。硫化条件为:硫化压力为6.4mpa,硫化油为含cs
2 2%重量的煤油,体积空速为2h-1
,氢油比为300v/v,首先在230℃/h恒温6h,然后再升温至320℃硫化8h,每个阶段的升温速率为10℃/h。
[0138]
实施例1
[0139]
本实施例采用的富含芳烃馏分油为催化裂化柴油a,经切割后得到轻馏分b和重馏分c,性质如表3所示。
[0140]
将重馏分c送至加氢单元,依次通过加氢精制反应区与加氢异构反应区,分别与加氢精制催化剂(rs-2100)与加氢异构催化剂c1(制备例2-1所得)接触进行加氢反应,加氢精制催化剂与加氢异构催化剂的体积比例为2:1。反应流出物经分离后得到加氢重馏分。
[0141]
将轻馏分和加氢重馏分送至催化裂化单元进行催化裂化反应,反应流出物经分离至少得到气体、催化裂化汽油馏分、催化裂化柴油馏分。
[0142]
催化裂化单元的反应条件包括:反应温度为565℃,剂油质量比为6,油气停留时间为8s,压力为0.20mpa,水蒸气/原料质量比为0.03。
[0143]
采用的催化裂化催化剂为mlc-500,为中国石化催化剂分公司生产。
[0144]
加氢精制反应区和加氢异构反应区的加氢反应条件、反应产物性质和催化裂化产物分布如表4所示。
[0145]
实施例2-3
[0146]
按照实施例1的方法进行实施,不同的是,将实施例2中加氢异构催化剂替换为等量的制备例2-2制备的加氢异构催化剂c2,实施例3中加氢异构催化剂替换为等量的制备例2-3制备的加氢异构催化剂c3。加氢精制反应区和加氢异构反应区的加氢反应条件、反应产物性质和催化裂化产物分布如表4所示。
[0147]
实施例4
[0148]
按照实施例1的方法进行实施,不同的是,加氢精制催化剂与加氢异构催化剂c1的体积比例为1:3。加氢精制反应区和加氢异构反应区的加氢反应条件和催化裂化产物分布如表4所示。
[0149]
实施例5
[0150]
按照实施例1的方法进行实施,不同的是,采用原料为原料d,原料d为催化柴油与煤焦油的混合物,经切割后得到轻馏分e和重馏分f,性质如表3所示。加氢精制反应区和加氢异构反应区的加氢反应条件、反应产物性质和催化裂化产物分布如表5所示。
[0151]
对比例1
[0152]
按照实施例1的方法进行实施,不同的是,将加氢异构催化剂替换为rs-2100。加氢精制反应区和加氢异构反应区的加氢反应条件、反应产物性质和催化裂化产物分布如表5所示。
[0153]
对比例2
[0154]
将原料a不进行分馏,而是直接将催化裂化柴油原料a与氢气混合后进入加氢单元进行处理,所得加氢产品进入催化单元进行反应。加氢精制反应区和加氢异构反应区的加氢反应条件、反应产物性质和催化裂化产物分布如表5所示。
[0155]
对比例3
[0156]
按照实施例1的方法进行实施,不同的是,所述轻馏分与重馏分的切割点为260℃。加氢精制反应区和加氢异构反应区的加氢反应条件、反应产物性质和催化裂化产物分布如表5所示。
[0157]
由表4、表5可以看出,将实施例1、2、3与对比例1相比可以看出,在
[0158]
本发明优选范围内的加氢异构催化剂能够进一步提高加氢单元中的多环芳烃饱和率及单环芳烃选择性,从而提高了催化裂化装置中汽油产物的产率和汽油馏分中芳烃的含量,并且加氢单元的总氢耗更低。
[0159]
将实施例1与对比例2相比可以看出,采用本发明的方法对混合柴油原料a进行分馏,加氢产物整体的单环芳烃选择性明显提升,并且加氢单元的总氢耗显著降低,此外所得催化裂化产物汽油产率显著提升,且汽油ron值显著提升。
[0160]
表3
[0161][0162]
表4
[0163][0164]
表5
[0165][0166]
实施例和对比例中:重柴油馏分加氢产物的多环芳烃饱和率、单环芳烃选择性及单环芳烃异构选择性采用如下公式计算:
[0167]
多环芳烃饱和率=(a
p1-a
p2
)/a
p1
*100%
[0168]
单环芳烃选择性=(a
m2-a
m1
)/(a
p1-a
p2
)*100%
[0169]
单环芳烃异构选择性=(a
i2-a
i1
)/(a
p1-a
p2
+a
m1
)*100%
[0170]
式中:a
p1
—反应区液体进料中多环芳烃含量,质量%
[0171]
a
p2
—反应区液体产品中多环芳烃含量,质量%
[0172]
a
m1
—反应区液体进料中单环芳烃含量,质量%
[0173]
a
m2
—反应区液体产品中单环芳烃含量,质量%
[0174]
a
i1
—反应区液体进料中茚满类化合物含量,质量%
[0175]
a
i2
—反应区液体产品中茚满类化合物含量,质量%。
[0176]
本发明所述的“多环芳烃含量”指的是以质谱法(分析方法sh/t-0606)得到的质谱组成数据中双环以上芳烃其中包括双环芳烃本身的质量分数之和。
[0177]
本发明所述的“单环芳烃含量”指的是以质谱法(分析方法sh/t-0606)得到的质谱组成数据中单环芳烃的质量分数。
[0178]
本发明所述的“茚满类化合物含量”指的是以质谱法(分析方法sh/t-0606)得到的质谱组成数据中茚满类化合物的质量分数。
[0179]
以上详细描述了本发明的优选实施方式,但是,本发明并不限于此。在本发明的技术构思范围内,可以对本发明的技术方案进行多种简单变型,包括各个技术特征以任何其它的合适方式进行组合,这些简单变型和组合同样应当视为本发明所公开的内容,均属于本发明的保护范围。