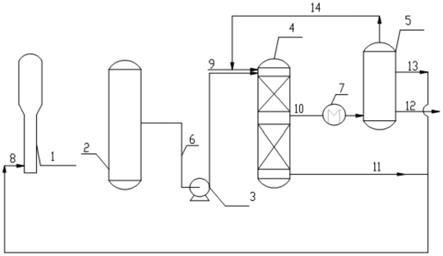
1.本技术涉及石化领域,尤其涉及一种柴油分离回炼装置。
背景技术:
2.随着经济发展及产业结构的调整,成品油消费结构发生较大发化,尤其是柴油消费日渐减少,消费柴汽比大幅降低。
3.目前,由于柴油过剩,一些老炼厂纷纷将催化裂化(裂解)装置产生的柴油裂解生产石脑油,进而为重整提供原料,扩大芳烃生产的路线或者将柴油裂解石脑油作为乙烯裂解装置的原料扩大烯烃生产路线。由于催化装置柴油的收率往往在20-30%,甚至超过30%,这部分柴油芳烃尤其是多环芳烃含量高,多环芳烃很难裂解且容易在裂解过程中生焦,所以目前常规路线是催化柴油经过柴油加氢处理将多环芳烃转化后再进行裂解产生石脑油,石脑油作为重整或乙烯裂解原料来生产芳烃和烯烃,这种路线装置投资非常高且占地增加很大,对一些老炼厂的改造存在相当大的难度,现有技术中缺少一种便于改造的并能提高汽油及烯烃产出率的设备。
技术实现要素:
4.有鉴于此,本技术提出了一种柴油分离回炼装置,包括一种柴油分离回炼装置,包括顺次连接的柴油泵、吸附分馏塔及蒸馏分馏塔;所述柴油泵的进油端连接管路用以注入催化柴油;出油端与所述吸附分馏塔的进液口通过管路连通;所述吸附分馏塔设置有抽出液出口与余液出口;所述抽出液出口与所述蒸馏分馏塔的进液端通过管路连通;所述余液出口与后端反应装置通过第一管路连通;所述蒸馏分馏塔设置有单环芳烃出液端与多环芳烃出液端;所述单环芳烃出液端与所述后端反应装置通过第二管路连通;所述多环芳烃出液端适用于通过管路连接到所述柴油分离回炼装置的外部。
5.在一种可能的实现方式中,所述后端反应装置设置有第三管路,所述第一管路与所述第二管路分别与所述第三管路连通后,连通至所述后端反应装置。
6.在一种可能的实现方式中,所述后端反应装置为提升管反应器。
7.在一种可能的实现方式中,所述吸附分馏塔与所述蒸馏分馏塔的连通管路上设置有加热器。
8.在一种可能的实现方式中,还包括催化装置分馏塔;所述催化装置分馏塔与所述柴油泵的进油端相连接。
9.在一种可能的实现方式中,所述吸附分馏塔上还设置有与前端设备连通的吸收剂补充管路,用以增添吸收剂。
10.在一种可能的实现方式中,所述吸附分馏塔与所述蒸馏分馏塔之间还通过吸收剂返回管路连通;所述吸附分馏塔还设置有第四管路,所述吸收剂返回管路与所述吸收剂补充管路分别与所述第四管路连通后,连通至所述吸附分馏塔。
11.在一种可能的实现方式中,所述抽出液出口设置在所述吸附分馏塔的一侧中部。
12.在一种可能的实现方式中,所述单环芳烃出液端设置在所述蒸馏分馏塔的一侧中部。
13.本实用新型的有益效果:通过吸附分馏塔,将柴油馏分中芳烃与非芳分开,再经蒸馏分馏塔细分为单环芳烃与多环芳烃,多环芳烃作为芳烃溶剂油,非芳组分及单环芳烃混合返回催化装置的进一步反应,提高催化装置的汽油及烯烃产出率,保证柴油馏分的价值最大化,低投资少占地前提下,提高经济效益。
14.根据下面参考附图对示例性实施例的详细说明,本技术的其它特征及方面将变得清楚。
附图说明
15.包含在说明书中并且构成说明书的一部分的附图与说明书一起示出了本技术的示例性实施例、特征和方面,并且用于解释本技术的原理。
16.图1示出本技术实施例的柴油分离回炼装置的各部分连接示意图;
17.表1为使用柴油分离回炼装置的催化收率。
具体实施方式
18.以下将参考附图详细说明本技术的各种示例性实施例、特征和方面。附图中相同的附图标记表示功能相同或相似的元件。尽管在附图中示出了实施例的各种方面,但是除非特别指出,不必按比例绘制附图。
19.其中,需要理解的是,术语“中心”、“纵向”、“横向”、“长度”、“宽度”、“上”、“下”、“前”、“后”、“左”、“右”、“竖直”、“水平”、“顶”、“底”、“内”、“外”、“顺时针”、“逆时针”、“轴向”、“径向”、“周向”等指示的方位或位置关系为基于附图所示的方位或位置关系,仅是为了便于描述本实用新型或简化描述,而不是指示或暗示所指的装置或元件必须具有特定的方位、以特定的方位构造和操作,因此不能理解为对本实用新型的限制。
20.此外,术语“第一”、“第二”仅用于描述目的,而不能理解为指示或暗示相对重要性或者隐含指明所指示的技术特征的数量。由此,限定有“第一”、“第二”的特征可以明示或者隐含地包括一个或者更多个该特征。在本实用新型的描述中,“多个”的含义是两个或两个以上,除非另有明确具体的限定。
21.在这里专用的词“示例性”意为“用作例子、实施例或说明性”。这里作为“示例性”所说明的任何实施例不必解释为优于或好于其它实施例。
22.另外,为了更好的说明本技术,在下文的具体实施方式中给出了众多的具体细节。本领域技术人员应当理解,没有某些具体细节,本技术同样可以实施。在一些实例中,对于本领域技术人员熟知的方法、手段、元件和电路未作详细描述,以便于凸显本技术的主旨。
23.图1示出本技术实施例的柴油分离回炼装置的各部分连接示意图。
24.如图1所示,该柴油分离回炼装置,包括顺次连接的柴油泵3、吸附分馏塔4及蒸馏分馏塔5,柴油泵3的进油端连接管路用以进油,出油端与吸附分馏塔4的进液口之间连通有管路,吸附分馏塔4的出液口包括抽出液出口10与余液出口8,抽出液出口10与蒸馏分馏塔5的进液端之间连通有管路,余液出口8与后端反应装置连通有第一管路,蒸馏分馏塔5的出液端包括单环芳烃出液端13与多环芳烃出液端12,单环芳烃出液端13与后端反应装置连通
有第二管路,多环芳烃出液端12适用于通过管路运输至柴油分离回炼装置外。
25.在此种可能的实现方式中,通过吸附分馏塔4,将柴油馏分中芳烃与非芳分开,再经蒸馏分馏塔5细分为单环芳烃与多环芳烃,多环芳烃作为芳烃溶剂油,非芳组分及单环芳烃混合返回催化装置再进一步反应,提高催化装置的汽油及烯烃产出率,优化组合流程,使催化装置尽可能少出柴油,保证柴油馏分的价值最大化,在低投资少占地的情况下给工厂带来更好的经济效益。
26.还需特别强调的是,柴油泵3进油端通过侧线柴油管路6连通至其前端的催化装置分馏塔2,柴油泵3进油为催化柴油,催化柴油从催化装置分馏塔2进入柴油泵3。
27.本技术的柴油分离回炼装置的具体工作流程为:催化柴油自侧线柴油管路6进入柴油泵3,柴油泵3升压后,将催化柴油经吸附分馏塔4的进液口压入塔内,催化柴油在其内分离为两路:一路为抽出液(含芳烃组分),另一路为抽余液(非芳烃组分);
28.其中,抽出液从抽出液出口10抽出,随管路经加热器7加热到一定温度后进入蒸馏分馏塔5;
29.抽余液从余液出口8送出,经第一管路运输至后端催化装置,即送至提升管反应器1;
30.抽出液进入蒸馏分馏塔5后分离为三路:一路为单环芳烃、一路为多环芳烃,还有一路为能重复利用的吸收剂;
31.多环芳烃从多环芳烃出液端12直接排出并收集,作为芳烃溶剂油;
32.单环芳烃从单环芳烃出液端13送出,经第二管路送至提升管反应器1,进一步反应;
33.能重复利用的吸收剂经吸收剂补充管路9送回至吸附分馏塔4内,进行重复利用。
34.在一种可能的实现方式中,后端反应装置设置有第三管路8,第一管路与第二管路分别与第三管路8连通后,连通至后端反应装置。
35.在此种实现方式中,抽余液的第一管路与单环芳烃所走的第二管路合并为第三管路8,即回炼柴油管路,抽余液与单环芳烃混合后一同进入提升管反应器1。第一管路与第二管路合并的第三管路8,管路连接结构的设计更合理,节约材料及成本,提高管路利用率。
36.在一种可能的实现方式中,后端反应装置为提升管反应器1。
37.在一种可能的实现方式中,吸附分馏塔4与蒸馏分馏塔5的连通管路上设置有加热器7。
38.在一种可能的实现方式中,还包括催化装置分馏塔2,催化装置分馏塔2与柴油泵3的进油端相连接。
39.在一种可能的实现方式中,吸附分馏塔4上还设置有与前端设备连通的吸收剂补充管路9,用以增添吸收剂。
40.在一种可能的实现方式中,吸附分馏塔4与蒸馏分馏塔5之间还通过吸收剂返回管路14连通;吸附分馏塔4还设置有第四管路,吸收剂返回管路14与吸收剂补充管路9分别与第四管路连通后,连通至吸附分馏塔。
41.在一种可能的实现方式中,吸附分馏塔4上还包括吸收剂补充管路9,用以增添吸收剂。
42.在一种可能的实现方式中,吸附分馏塔4与蒸馏分馏塔5之间连通有吸收剂返回管
路14,吸收剂返回管路14与吸收剂补充管路9合并为一路,连通至吸附分馏塔4。
43.在此种可能的实现方式中,吸收剂返回管路14与吸收剂补充管路9合并为公用管路,置管路连接结构的设计更合理,节约材料及成本,提高管路利用率。
44.在一种可能的实现方式中,抽出液出口10设置在吸附分馏塔4的一侧中部。
45.在一种可能的实现方式中,单环芳烃出液端13设置在蒸馏分馏塔5的一侧中部。
46.进一步的,经测试,采用本技术的柴油分离回炼装置,提高了催化装置的汽柴比,同时增加了液化气中烯烃产量,催化装置收率的详情见表1。
47.从表1可以看出,通过利用本技术的柴油分离回炼装置,120万吨/年催化装置的汽油收率提高了7.4%,产量提高了约9万吨/年,液化气产量提高了6.6%,其中丙烯产量提高了1.3%,解决了目前催化柴油的销售瓶颈,同时多产了丙烯高附加值产品,给企业带来了较好的经济效益。
48.以上已经描述了本技术的各实施例,上述说明是示例性的,并非穷尽性的,并且也不限于所披露的各实施例。在不偏离所说明的各实施例的范围和精神的情况下,对于本技术领域的普通技术人员来说许多修改和变更都是显而易见的。本文中所用术语的选择,旨在最好地解释各实施例的原理、实际应用或对市场中的技术的改进,或者使本技术领域的其它普通技术人员能理解本文披露的各实施例。