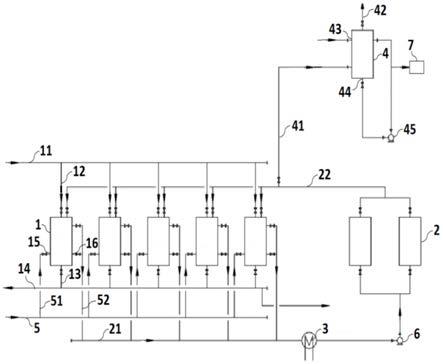
1.本发明属于煤气脱硫技术领域,更具体地说,涉及一种焦炉煤气微晶分子筛精脱硫装置及其方法,该方案同样适用于高炉煤气和气化炉煤气复杂成分的有机硫脱除。
背景技术:
2.钢铁工业加热炉和锅炉所用燃气主要来自于炼焦生产的焦炉煤气和高炉冶炼产生的高炉煤气,煤气中硫化物含量决定其燃烧后烟气so2含量能否达标排放。钢铁联合企业的焦炉煤气经脱硫脱氰后,还含有一定量的h2s和有机硫(二硫化碳、硫氧化碳、硫醇、硫醚、噻吩、甲基硫醇、甲基硫醚等)、以及少量的萘、焦油、苯、氨、氰化氢等;高炉煤气除含有1.5
‑
3.0%的h2、0.2
‑
0.5%的ch4、25
‑
30%的co、9
‑
12%的co2、55
‑
60%的n2、0.2
‑
0.4%的o2,还含有30
‑
60mg/nm3的h2s、80
‑
150mg/nm3的有机硫(羰基硫、二硫化碳、硫醇和硫醚)和粉尘等。
3.现有的焦炉煤气脱硫技术以脱除无机硫为主,很少考虑有机硫的脱除,因而,即使h2s含量达到标准(小于20mg/m3),也难以保证煤气燃烧后的烟气so2能够达标排放;高炉煤气因h2s含量低而不脱除。焦炉煤气中的h2s脱除方法较多,目前国内常用的有真空碳酸盐、as、hpf、pds法,脱硫后煤气的h2s含量一般≤300mg/nm3、有机硫含量≯350mg/nm3。为了贯彻执行钢铁工业大气污染物超低排放标准,减少焦炉煤气、高炉煤气下游用户烟气so2含量,实行源头治理,需要对焦炉煤气、高炉煤气进行有机硫精脱硫或深度脱硫处理。焦炉煤气精脱硫或深度脱硫包括有机硫和硫化氢的脱除,比较成熟的方法是干法脱硫和有机硫催化加氢转化。干法脱硫工艺种类较多,如氧化工艺、吸附
‑
脱附工艺等,但因煤气中含有焦油、萘、苯、氨、氰化氢等有机物而使脱硫剂存在不同程度的中毒失效,不利于脱硫工艺的连续进行。
4.文献[焦炉煤气催化加氢转化精脱硫工艺及生产实践],介绍了zno作为催化剂的焦炉煤气催化加氢转化法精脱硫工艺,该工艺过程中煤气中o2、h2s、焦油、粉尘等组分含量超标可能会引起zno催化剂高温失活、寿命缩短及设备堵塞等危害,但文献中并没有提出如何提高精脱硫效率、降低系统能耗和运行成本的有效措施。
[0005]
文献[焦炉煤气精脱硫工艺的流程分析],针对精脱硫过程中所用铁锰催化剂成本高、固废难处理等问题,提出了用中温氧化锌替代铁锰催化剂及原先的一级加氢改为二级加氢流程,属于对铁锰催化剂精脱硫工艺的一种改进,但此类工艺运行成本高、工艺路线长、催化剂更换频繁、对噻吩脱除不理想等难题仍没有得到有效解决。
[0006]
经检索,中国专利申请号为201911353163.7的申请案,公开了一种焦炉煤气中有机硫的超深度脱除装置及其脱除工艺,该申请案针对焦炉煤气甲烷化制天然气工艺中,氧化锌脱除有机硫能力弱,提出了一种有机硫超深度脱除装置,该装置在原脱硫工艺中的二级加氢反应器与精脱硫塔前设置钴钼加氢反应器、精脱硫塔后设置超精脱硫塔,虽然能够提升甲烷化过程中催化剂的使用寿命,提升甲烷化工艺稳定性,但并没有涉及微晶分子筛精脱硫工艺以及吸附剂的再生工艺。
[0007]
又如,中国专利申请号为201710590574.2的申请案,公开了一种焦炉煤气中有机
硫的脱除方法,其方法是将来自炼焦炉的煤气首先进入粗脱苯单元、采用溶剂萃取的方法脱苯,粗脱苯后的煤气进入粗脱硫单元、采用有机胺、石灰石、氢氧化钙或氧化铁中的至少一种脱硫剂粗脱硫,粗脱硫后的煤气进入水气分离器、用含有分子筛或者活性炭中的至少一种脱除焦炉煤气中的水分,从水气分离器出来的煤气进入含有分子筛类吸附剂的综合净化塔、同时脱除煤气中的芳烃和有机硫化物。该申请案中脱除有机硫的方法主要是过滤吸附,虽然提到了分子筛吸附剂可以再生,但工艺方案中没有体现,也没有说明吸附剂如何再生及有机硫的催化转化。
[0008]
又如,中国专利申请号为201810829320.6的申请案,该申请案针对焦炉煤气干法净化工艺中,焦炉气中烯轻、有机硫化物及氧等微量杂质在合成催化剂表面发生放热反应、结碳堵塞催化剂孔道,容易引起催化剂失活的问题,提出了一种焦炉煤气除氧精脱硫方法,包括如下步骤:s1)、换热升温,s2)、预加氢转化和一级加氢转化,s3)、一级脱硫,s4)、二次换热升温,s5)、二级加氢转化,s6)、二级精脱硫。该申请案的本质还是加氢转化,且工艺路线长、能耗高。
[0009]
又如,中国专利申请号为201922197621.4的申请案,公开了一种高炉煤气脱硫及再生气预处理系统,包括电加热装置、喷碱塔和吸附塔,吸附塔内装填有净化介质,高炉煤气进入吸附塔后,h2s等无机硫、cos和cs2等有机硫以及杂质被净化介质吸附,得到净高炉煤气;当吸附塔内的净化介质吸附达到饱和时,再生气经过加热后返回吸附塔内,可脱附再生,并能够原位催化转化有机硫为无机硫。该申请案通过对净化介质的吸附和再生,虽然能够提高高炉煤气的净化效果,但煤气中的焦油、萘、粉尘等容易引起吸附剂堵塞,氰化氢等容易引起催化剂中毒的问题仍然没能得到有效的解决。
技术实现要素:
[0010]
1、要解决的问题
[0011]
针对现有技术中,净化介质再生过程中吸附剂易堵塞、催化剂易中毒,从而降低了吸附塔的工作效率的问题,本发明提供了一种能够适应焦炉煤气、高炉煤气、气化炉煤气复杂成分的微晶分子筛催化剂有机硫脱除的装置及其方法,采用本发明的技术方案,能够有效延长吸附塔的连续工作时间,在提高脱除焦炉煤气、高炉煤气、气化炉煤气中有机硫效率的同时,还能够降低整个工艺中的能耗。
[0012]
2、技术方案
[0013]
为了解决上述问题,本发明所采用的技术方案如下:
[0014]
本发明的一种焦炉煤气的精脱硫装置,包括吸附塔和洗涤塔,该吸附塔的进气口与煤气进气主管连通,出气口与净煤气出气主管连通;该精脱硫装置还包括转化槽,所述的转化槽的进气口通过循环解析气进气管与吸附塔相连通,出气口通过循环解析气出气管与吸附塔相连通;所述的循环解析气进气管上设有加热装置和脱附风机,循环解析气出气管通过解析气外排进气管与洗涤塔相连通。
[0015]
进一步地,所述的吸附塔设置n个,n≥3;n个吸附塔的进气口分别通过煤气进气支管与煤气进气主管相连通;出气口分别通过净煤气出气支管与净煤气出气主管相连通。
[0016]
进一步地,所述的转化槽设置m个,m≥2,m个转化槽并联设置,且转化槽中至少一个作为备用转化槽。
[0017]
进一步地,所述的n个吸附塔上均设有解析气进气口和解析气出气口,解析气进气口通过解析气进气管与解析气主管相连通,解析气出气口通过解析气出气管与循环解析气进气管相互连通。
[0018]
进一步地,所述的洗涤塔上设有解析气外排出气管、喷淋口和冷凝液排出口,经洗涤后的再生脱附解析气由解析气外排出气管排出,冷凝液排出口通过循环泵与澄清槽相连通。
[0019]
进一步地,本发明的一种焦炉煤气的精脱硫方法,具体包括以下步骤:
[0020]
步骤一、粗脱硫系统的炉煤气进入吸附塔中,吸附剂吸附炉煤气中的无机硫、有机硫及有机杂质,得到净煤气;
[0021]
步骤二、吸附塔内吸附剂达到饱和后,取吸附塔出口的净煤气作为再生脱附解析气,对吸附剂进行加热再生;
[0022]
步骤三、吸附塔解析脱附出来的再生脱附气进入转化槽,经催化加氢或催化水解,将有机硫转化成h2s;
[0023]
步骤四、再生脱附气在吸附塔与转化槽之间循环作业,同时,连续切出一部分转化后的富含h2s气体,送入洗涤塔进行降温处理,降温后气体返回粗脱硫系统,与未脱硫煤气一起在粗脱硫系统进行粗脱硫。
[0024]
进一步地,步骤二中吸附塔的加热解析脱附再生轮流进行,具体过程为:
[0025]
a、关闭待脱附吸附塔的炉煤气进出口阀,打开待脱附吸附塔的再生脱附解析气进出口阀,形成待脱附吸附塔与转化槽之间的气路循环;同时,开启加热装置维持转化槽内温度;
[0026]
b、关闭已脱附吸附塔的再生脱附解析气进出口阀,打开已脱附吸附塔的脱附气进口阀门,引入净煤气进入已脱附吸附塔,对吸附剂进行降温操作,净煤气被加热后参与再生脱附气循环;
[0027]
c、已脱附吸附塔中吸附剂降至一定温度,具备吸附能力时,关闭已脱附吸附塔的脱附气进口阀门,打开炉煤气进出口阀门,吸附剂重新投入对煤气中的无机硫、有机硫及有机杂质的吸附操作。
[0028]
进一步地,所述的吸附塔在同一时刻,必有1台处于加热再生状态,一台处于热量回收状态,剩余吸附塔处于煤气吸附有机硫状态。
[0029]
进一步地,步骤四中送入洗涤塔中的富含h2s气体的流量,与步骤b中引入已脱附吸附塔中净煤气的流量保持一致。
[0030]
进一步地,所述的吸附剂为微晶分子筛催化剂、微晶分子筛或分子筛;所述的转化槽的转化温度为180
‑
320℃、压力为0
‑
8.0mpa。
[0031]
3、有益效果
[0032]
相比于现有技术,本发明的有益效果为:
[0033]
(1)本发明的一种焦炉煤气的精脱硫装置,将吸附与转化功能分开,分别在吸附塔与转化槽内完成,互不干涉,可有效防止煤气中的焦油、萘、粉尘等对吸附剂堵塞,从而延长了吸附塔的连续工作时间,提高了工作效率。
[0034]
(2)本发明的一种焦炉煤气的精脱硫装置,循环再生脱附解析气在吸附塔和转化槽之间实现大流量内循环,吸附塔再生时间缩短为已有精脱硫工艺的1/5
‑
1/6,保证了精脱
硫的效率。
[0035]
(3)本发明的一种焦炉煤气的精脱硫装置,其解析气进气口通过解析气进气管与解析气主管相连通,脱附出气口通过脱附出气管与循环解析气进气管相互连通,这种设计使得再生脱附解析气首先进入一台已经再生、但未投入运行的吸附塔,带走塔内吸附剂的热量,再与循环再生脱附解析气合并,加热后进入再生塔,实现热量转移,可降低能耗30
‑
50%。
[0036]
(4)本发明的一种焦炉煤气的精脱硫装置,吸附塔和转化槽均设有多个,且至少一个为备用吸附塔,至少一个为备用转化槽,在需要更换催化剂时,不必停用吸附塔,可实现连续脱附、连续转化;同时,转化槽使用的温度和操作压力相对稳定,可延长其使用寿命至18个月以上。
附图说明
[0037]
图1为本发明的精脱硫装置的结构示意图;
[0038]
图中:1、吸附塔;11、煤气进气主管;12、煤气进气支管;13、净煤气出气支管;14、净煤气出气主管;15、解析气进气口;16、解析气出气口;
[0039]
2、转化槽;21、循环解析气进气管;22、循环解析气出气管;
[0040]
3、加热装置;
[0041]
4、洗涤塔;41、解析气外排进气管;42、解析气外排出气管;43、喷淋口;44、冷凝液排出口;45、循环泵;
[0042]
5、解析气主管;51、解析气进气管;52、解析气出气管;
[0043]
6、脱附风机;7、澄清槽。
具体实施方式
[0044]
下面结合具体实施例对本发明进一步进行描述。
[0045]
实施例1
[0046]
如图1所示,本实施例的一种焦炉煤气的精脱硫装置,包括吸附塔1、转化槽2和洗涤塔4,该吸附塔1的进气口与煤气进气主管11连通,出气口与净煤气出气主管14连通;转化槽2的进气口通过循环解析气进气管21与吸附塔1相连通,出气口通过循环解析气出气管22与吸附塔1相连通;循环解析气进气管21上设有加热装置3和脱附风机6,循环解析气出气管22通过解析气外排进气管41与洗涤塔4相连通。其中,吸附塔1内填充有吸附剂,该吸附剂可以是微晶分子筛催化剂,也可以是微晶分子筛或具有良好吸附性能的分子筛;转化槽2为加氢转化槽或催化水解槽,本实施例中将吸附与转化或水解功能分开,分别在吸附塔与转化槽内完成,互不干涉,有效延长了吸附塔的连续工作时间。
[0047]
根据实际生产的需要,吸附塔1可设置4
‑
7台,其中,1台处于加热再生状态,一台处于热量回收状态,剩余吸附塔处于吸附煤气有机硫状态。转化槽2可设置1
‑
3个,实现一用两备、两用一备或一用一备(两个转化槽)。多个吸附塔1的进气口分别通过煤气进气支管12与煤气进气主管11相连通;出气口分别通过净煤气出气支管13与净煤气出气主管14相连通。另外,多个吸附塔1上均设有解析气进气口15和解析气出气口16,解析气进气口15通过解析气进气管51与解析气主管5相连通,解析气出气口16通过解析气出气管52与循环解析气进
气管21相互连通。
[0048]
本实施例中的精脱硫装置,由5台并联的微晶分子筛或微晶分子筛催化剂吸附塔(以下简称吸附塔),其中,1台处于加热再生状态,一台处于热量回收状态,剩余吸附塔处于吸附煤气有机硫状态。2台并联的的加氢转化槽或催化水解槽(以下简称转化槽),实现一用一备,这样在需要更换催化剂时,不必停用吸附塔,保证了整个脱硫工艺的连续性,从而可提高效率。
[0049]
在脱硫工艺中,再生脱附解析气(以下简称脱附气)分三路,第1路是新加入的30
‑
45℃脱附气,来自于煤气进气主管,吸附了无机硫和有机硫以后的干净煤气,这路脱附气通过解析气主管5,首先进入一台已经再生、但未投入运行的吸附塔,带走塔内吸附剂的热量,送往脱附风机,与第2路循环脱附气合并;吸附塔温度由180
‑
320℃降到30
‑
45℃。第2路的循环脱附气通过循环解析气进气管21和循环解析气出气管22,实现在吸附塔1和转化槽2之间的循环流通,第2路的循环脱附气流量可调,调节范围是3000
‑
30000m3/h,这路循环脱附气的温度为200
‑
330℃,其热量来自于第1路脱附气带来的吸附剂显热和加热装置3的辅助加热;第2路循环脱附气送入某个因吸附饱和待再生脱附的吸附塔,进行加热再生。第3路脱附气是外排的脱附气,其外排流量与第1路脱附气的加入流量相等;第3路脱附气通过解析气外排进气管41进入洗涤塔4中,经轻质焦油氨水喷洒降温后被冷却到60
‑
85℃,通过解析气外排出气管42送入煤气初冷器的前端,冷凝液在循环泵45的带动下,通过冷凝液排出口44送入机械化焦油氨水澄清槽7。
[0050]
该工艺中的5个吸附塔轮流吸附
‑
脱附再生,循环脱附气(第2路气)含有高浓度cos、cs2、h2s酸气,循环脱附气的温度保持在180
‑
320℃,经过辅助电加热升温至200
‑
330℃,进入一台转化槽,将cos、cs2等转化成h2s气体,且经转化的脱附气外排属于连续进行,含有h2s在内的外排脱附气被洗涤降温后送入煤气初冷器的前端参与粗脱硫,进而将精脱硫吸附塔分离出来的有机硫与无机硫处理掉。该工艺理路径可表示为:洗苯塔后煤气中的有机硫
→
微晶吸附
→
加热脱附
→
加氢催化转化成h2s
→
返回初冷器
→
进入湿法脱硫塔
→
转化成硫磺产品。
[0051]
具体步骤如下:
[0052]
1、来自粗脱硫系统的焦炉煤气(硫化氢含量≤300mg/nm3、有机硫含量≯350mg/nm3;实际应用时的硫化氢和有机硫含量上限可分别放宽至≤500mg/nm3,也可根据实际含量进行设计)进入并联的吸附塔;
[0053]
2、含有h2s和cos、cs2、硫醇、噻吩等有机硫化物及少量焦油、萘、苯、氨、氰化氢等有机物的来自粗脱硫系统的焦炉煤气进入吸附塔,塔内吸附剂将煤气中的h2s和各种有机硫化物及萘、焦油、氨、hcn等有机杂质吸附于其内外表面及孔道,洁净煤气从吸附塔排出进入净煤气出气主管,供下游用户使用;
[0054]
3、吸附塔内吸附剂达到饱和后,加热至300℃、取自吸附塔出口的洁净焦炉煤气作为再生脱附解析气,对吸附剂进行加热再生,以解析脱附出吸附剂吸附的h2s、有机硫化物及萘、焦油、氨、hcn等杂质;
[0055]
4、吸附塔的加热解析脱附再生轮流进行;
[0056]
5、吸附塔解析脱附出来的高浓度含硫气体和其它有机物进入转化槽,经催化加氢或催化水解将有机硫转化成h2s;
[0057]
6、再生脱附气在吸附塔与转化槽之间循环作业的同时,连续切出一部分转化后的富含h2s气体,送入一台喷淋塔,用轻质焦油喷淋洗涤降温后,煤气温度被降到80℃,送入煤气初冷器进行降温后返回粗脱硫塔前,与未脱硫煤气一起进入粗脱硫系统进行粗脱硫;补充与切出气体等量的新鲜洁净煤气参与再生脱附。喷淋塔底部是煤气冷却过程中产生的冷凝液,送往鼓冷工段的机械化澄清槽;
[0058]
7、转化槽的操作温度180℃、操作压力8.0mpa。
[0059]
本实施例中所涉及的化学原理如下:
[0060]
1、吸附脱附
[0061]
吸附剂利用其比表面和孔容进行选择性吸附;吸附一定时间后加热脱附,再生气为焦炉煤气;解析脱附气为焦炉煤气、高浓度有机硫化物和有机物。
[0062]
2、加氢转化或催化水解
[0063]
2.1解析脱附气的加氢催化
[0064]
cos+h2→
co+h2s
[0065]
cs2+4h2→
ch4+2h2s
[0066]
c4h4s+4h2→
c4h
10
+h2s
[0067]
rsh+h2→
rh+h2s
[0068]
2.2解析脱附气的催化水解
[0069]
cos+h2o
→
h2s+co2[0070]
cs2+2h2o
→
2h2s+co2[0071]
3、加氢转化或催化水解后的脱附气返回前端粗脱硫系统。
[0072]
本实施例的脱硫工艺,旨在克服现有工艺技术中的微晶分子筛催化剂易中毒、寿命短、再生时间长之缺陷,将煤气中的总硫含量降至10mg/m3以下,再生解析出来的硫化氢和芳烃等杂质送回粗脱硫系统。本实施例的工艺特点:
[0073]
1、本精脱硫系统单独设置用于加氢转化或催化水解的加氢转化槽或催化水解槽,将吸附与转化或水解功能分开,分别在吸附塔与转化槽内完成,互不干涉,有效延长了吸附塔的连续工作时间。
[0074]
2、根据煤气流量设置1
‑
3个转化槽,实现一用两备或两用一备或一用一备(两个转化槽),在需要更换催化剂时,不必停用吸附塔;同时,水解催化剂或加氢转化催化剂的使用温度和操作压力相对稳定,可延长其使用寿命至18个月以上。
[0075]
3、本工艺可实现连续脱附、连续水解或加氢转化,再生脱附气采用大流量内循环,吸附塔再生时间缩短为已有精脱硫工艺的1/5
‑
1/6,保证了精脱硫工艺效率。
[0076]
4、脱附阶段的吸附剂含有大量显热,冷吹过程中,随着吸附塔内吸附剂的温降,冷吹气被加热,将冷却塔的热量转移至加热再生塔,实现热量转移,可降低能耗30
‑
50%。
[0077]
5、吸附再生与加氢转化或催化水解分开操作,吸附剂可以是微晶分子筛催化剂,也可以是微晶分子筛或具有良好吸附性能的分子筛,避免了已有精脱硫工艺只能用微晶分子筛催化剂作为吸附剂的单一性,因而,可以降低工艺运行成本。
[0078]
6、再生温度能在180
‑
320℃范围内选择,根据微晶分子筛结晶度和吸附条件计算,分子筛的使用寿命可反复再生达5
‑
7年的使用期限。
[0079]
以10万m3/h焦炉煤气精脱硫为例,可设计五个吸附塔和2个转化塔(一用一备)。其
中,5#(图1中位于最右边)吸附塔已完成加热脱附,处于已脱附状态,温度为180
‑
320℃,准备降温;同时1#(图1中位于最左边)吸附塔需要加热脱附再生,处于待脱附状态,但初始温度只有30
‑
50℃。现拟定在40小时内,完成5#吸附塔的降温、以及1#吸附塔的升温。1#塔升温与5#塔降温同步进行。具体流程如下:
[0080]
第一步:5#吸附塔炉煤气进出口阀处于关闭状态;转化槽的温度维持180
‑
320℃;
[0081]
第二步:关闭1#吸附塔的炉煤气进出口阀,将该槽切出、准备再生;
[0082]
第三步:打开1#吸附塔的再生脱附解析气进出口阀,形成1#吸附塔与转化槽之间的气路循环;同时开启电加热器对再生脱附煤气加热,确保转化槽温度维持180℃;
[0083]
第四步:关闭5#吸附塔的再生脱附解析气进出口阀,此时,5#吸附塔不参与再生脱附环节的气路循环,进而实现再生脱附气全部集中在1#吸附塔与转化槽之间的气路循环,循环气量为0.5
‑
5.0万m3/h;
[0084]
第五步:打开5#吸附脱附气进口阀门,引入2000m3/h的新鲜洁净煤气进入5#吸附塔,对吸附剂进行降温操作,新鲜洁净煤气被加热后参与再生脱附气循环;因5#吸附塔的吸附剂温度260℃,不具备吸附能力,不能立即开启炉煤气进出口阀进行吸附操作;
[0085]
第六步:打开解析气外排进气管,引出与补充新鲜洁净煤气2000m3/h等量的富含h2s等有机物的再生脏煤气进入喷淋塔,用煤焦油喷淋洗涤,从而保证进气与出气的平衡。
[0086]
以上操作,必须有1台吸附塔处于加热状态,一台吸附塔同时处于冷吹降温状态,以形成热量的转移通道,另外三台吸附塔处于煤气吸附有机硫状态。
[0087]
以上示意性的对本发明及其实施方式进行了描述,该描述没有限制性,附图中所示的也只是本发明的实施方式之一,实际的结构并不局限于此。所以,如果本领域的普通技术人员受其启示,在不脱离本发明创造宗旨的情况下,不经创造性的设计出与该技术方案相似的结构方式及实施例,均应属于本发明的保护范围。