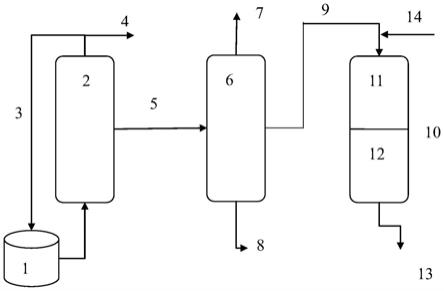
1.本发明涉及石油加工领域,特别是一种催化裂化油浆的处理方法。
背景技术:
2.催化裂化技术是重油深度加工的三大主要工艺之一,是原料轻质化的主要工艺技术,并且对原料适应性强。随着催化裂化装置加工原料的日益变重,给催化裂化装置带来许多不利因素。例如,装置因结焦和结垢而不能正常运行;产品分布及质量受到影响;轻质油收率降低。许多炼油厂为了解决此问题,普遍采用外甩油浆的方法。我国外甩油浆量占催化裂化装置处理量的5%~10%,每年外甩油浆量高达500万吨以上。催化裂化油浆密度大、残炭值高、粘度大,芳香分含量高,并含有残余催化剂颗粒,难以利用,因此如何加工利用催化裂化油浆已成为炼厂急需解决的问题。
3.针状焦是20世纪70年代大力发展的优质碳素原料,针状焦制成的石墨制品具有高密度、高强度、高纯度、高结晶度、高导电导热性、低热膨胀系数、低烧蚀性等特点,主要用于生产电炉炼钢用高功率、超高功率石墨电极。在冶金工业中,用针状焦制成的超高功率(uhp)石墨电极可缩短电炉炼钢冶炼时间50%~70%,电耗可降低 20%~50%,可以显著提高冶炼效率,降低电耗和原材料消耗,减少环境巧染。对针状焦形成机理研究发现,炼厂催化油浆是生产针状焦的优质原料,用催化油浆生产针状焦大大提升了产品的附加值,同时缓解了我国针状焦资源短缺问题。
4.由于催化裂化油浆中含有一定量的固体催化裂化催化剂粉末和较高的硫、氮及金属杂质等杂质,因此不能直接生产针状焦,必须经过进一步处理脱除有害组分,才能做为生产针状焦的原料。
5.催化裂化油浆中含有一定量的固体催化裂化催化剂粉末和金属杂质,工业上应用效果较好的油浆粉末分离方法有沉降分离法、静电分离法、过滤分离法、筛滤法及液固悬液分离法等,但这些方法对催化剂粉末和金属杂质脱除效果都不能满足固定床加氢反应器进料的要求,否则固定床会产生压降增高和堵塞问题,很难长周期稳定运转。
6.催化油浆中含有一定的轻馏分,还含有胶质、沥青质等重馏分,这些馏分严重影响生产高端针状焦的品质,需要脱除。要生产优质针状焦,对原料的选择非常关键,要求硫、氮、沥青质、灰分、金属等杂质质量分数低,芳烃含量高,其中要以三环和四环芳烃为主。
7.中国专利cn110628461 a公开了一种油浆选择性加氢脱硫保留芳烃的方法,该方法首先利用超声波辅助离心操作,将油浆中催化剂颗粒脱除,超声波的机械作用能够有效提高催化剂颗粒的脱除效果;再将油浆中残留的催化剂颗粒、沥青质、胶质除去,同时保留富集芳香烃的抽出油;再通过对抽出油进行选择性加氢脱硫,利用fe 改性的como/γal2o3选择性加氢脱硫催化剂脱硫。
8.中国专利cn103013567 a公开了一种由催化裂化油浆生产针状焦原料的方法,该方法设置保护区和加氢反应区,催化裂化油浆先进入保护区,吸附掉绝大部分催化裂化催化剂粉末,然后与氢气混合进加热炉,加热后进入加氢反应区进行加氢处理反应。本发明在
加氢反应区前设置保护区,可以滤除催化裂化油浆中夹带的绝大部分催化裂化催化剂粉末,达到保护加氢主催化剂,实现长周期运转的目的。此外,通过催化裂化油浆加氢精制,使催化裂化油浆中硫得到大部分的脱除,生产出合格的针状焦原料。
9.以上两项专利技术可以生产普通级的针状焦原料,但对于生产高端针状焦原料还需要改进,因为高端针状焦原料要求灰分、硫、氮含量更低,芳烃含量更高。
技术实现要素:
10.本发明的目的在于提供一种能高效脱除催化裂化油浆催化剂粉尘和金属杂质、深度脱硫并保留芳烃组分的由催化裂化油浆生产高端针状焦原料的方法。
11.本发明的方法具体内容如下:
12.1、对催化裂化油浆(fcc油浆)采用耐高温陶瓷膜滤芯或金属材料膜滤芯错流过滤器过滤,用以除掉催化剂细粉末和金属杂质,其膜孔径为:1.2~0.05μm,以适应颗粒分布为0.01~200μm,峰值为10~40μm的油浆。过滤的操作条件:温度190~ 300℃;压力0.4~2.0mpa。耐高温特种陶瓷膜滤芯或金属材料膜滤芯错流过滤器是一种错流形式的过滤装置,在压力驱动下,过滤介质在膜管内高速流动,小分子物质透过膜成为渗透液,固体颗粒及大分子物质被截留,从而使流体达到分离、浓缩、纯化的目的,滤后油浆灰分<50ppm。
13.2、将过滤后得到的渗透液进行减压蒸馏,保留有效组分即富含多环芳烃组分,除掉轻组分和胶质、沥青质等无用组分。同时可降低后续加氢的规模。该减压蒸馏的操作的条件为:油浆入塔温度300~350℃,塔顶压力5~30kpa,塔顶温度200~220℃, 塔底温度280~300℃,取300~450℃中间馏分。
14.3、将减压蒸馏得到的中间馏分与氢气混合后导入加氢反应器进行加氢处理,氢油体积比为800~1000:1,加氢反应器内分两个单元,按照反应物流的方向,依次上单元装填加氢脱硫催化剂和下单元装填加氢芳构化修复催化剂。反应物流先进入加氢反应器中脱硫催化剂单元,装填的加氢脱硫催化剂是一种以γ
‑
al2o3为载体,钼、镍为活性组分的加氢脱硫催化剂,并且活性组分钼、镍以氧化物计,钼的含量为0.5~ 15%(质量比),镍的含量为0.5~8%(质量比),余下量为γ
‑
al2o3载体。该加氢脱硫催化剂在加氢反应器中的装填体积百分数为70%~90%。通过该单元的催化剂除去中间馏分中的硫、氮等元素。反应物流后进入加氢反应器中加氢芳构化修复催化剂单元,装填的加氢芳构化修复催化剂是一种以氧化铝和zsm
‑
5分子筛为载体,其中氧化铝的含量10~85%(质量比),zsm
‑
5分子筛10~85%(质量比);活性组分为铁、锌的加氢芳构化修复催化剂,其可对芳烃进行修复,增大三环和四环芳烃含量,其中活性组分铁、锌以氧化物计,铁(三氧化二铁)的含量为1~5%(质量比),锌的含量为0.5~7%(质量比)。该加氢芳构化修复催化剂在加氢反应器中的装填体积百分数为10%~30%。然后采用以下的加氢操作,入口压力为3.5~4.0mpa,初期反应温度330~350℃,末期反应温度360~380℃及体积空速0.8~1.0/h
‑1。通过该加氢反应器后,可以有效地脱除催化裂化油浆中的含硫、氮化合物,同时保留多环芳烃,获得各项指标符合要求的针状焦原料。
15.本发明与现有技术相比具有如下优点:
16.1、本发明采用耐高温陶瓷膜滤芯或金属材料膜滤芯错流过滤技术,可有效过滤掉催化剂细粉末和金属杂质,防止后续减压蒸馏和加氢单元结焦,保护加氢催化剂,降低针状
焦原料灰分含量;
17.2、本发明采用减压蒸馏工艺,能保留有效组分即富含多环芳烃组分,切割掉轻组分和胶质、沥青质等非理想组分,提高加氢单元生产效率;得到的轻组分作为蜡油等调和组分出装置;塔底残余的油浆渣油组分富含胶质、沥青质,经过与氧化沥青适度调和作为道路沥青外售,实现催化油浆的产品升级,提高了经济效益。
18.3、本发明采用适合的加氢技术及专用加氢催化剂,脱除组分中硫、氮等有害元素,通过加氢芳构化修复催化剂保留生产高端针状焦的有效组分,尤其是三环和四环芳烃,满足生产高端针状焦组分的要求。
附图说明
19.图1是本发明流程示意简图。
20.在图1所示的本发明流程示意简图中,来自油浆储罐1的催化裂化油浆通过加热后进入耐高温陶瓷膜滤芯或金属材料膜滤芯错流过滤器2,固体颗粒及大分子物质被截留在膜管内并通过管线3在油浆储罐及耐高温陶瓷膜滤芯或金属材料膜滤芯错流过滤器之间循环,当循环油浆中催化剂细粉含量达到7500~8500μg/g时,通过管线4 外甩部分油浆,使循环油浆中催化剂细粉含量维持在500~8500μg/g。膜管内小分子物质透过膜成为渗透液经管线5进入减压蒸馏塔6进行减压蒸馏,该减压蒸馏塔内轻馏分通过管线7从塔顶排出,重馏分胶质、沥青质在塔底通过管线8排出,中间馏分在塔中部通过管线9与氢气管线14混合后从加氢反应器10塔顶进入。加氢反应器分上下两个单元,上单元装填加氢脱硫催化剂11,下单元装填加氢芳构化修复催化剂 12,高端针状焦原料(即有效组分)13则从加氢反应器塔底排出。
具体实施方式
21.下面的实施例将对本发明予以进一步的说明,但并不因此限制本发明。
22.下面的实施例中所用的原料即催化裂化(fcc)油浆,其主要各项指标请见下表 1
23.表1催化裂化油浆原料
[0024][0025]
由表1可见,催化裂化油浆的硫含量、灰分含量及胶质/沥青含量都较高,不符合生产针状焦原料的要求。
[0026]
本发明的具体实施例如下:
[0027]
实施例1
[0028]
取表1所示催化裂化油浆原料,采用耐高温陶瓷膜滤芯错流过滤器过滤,其膜孔径为:1.2μm、温度190℃、压力0.4mpa,将过滤后得到的渗透液,经过换热后入塔温度在300℃进行减压蒸馏,操作的条件为:塔顶压力5kpa,塔顶温度200℃,塔底温度280℃,取300~450℃中间馏分。将减压蒸馏得到的中间馏分与氢气混合后导入加氢反应器进行加氢处理,氢油体积比为800:1,加氢反应器内分上下两个单元,按照反应物流的方向,依次上单元装填加氢脱硫催化剂下单元装填加氢芳构化修复催化剂。反应物流先进入的上单元装填的加氢脱硫催化剂是一种以γ
‑
al2o3为载体,钼、镍为活性组分的加氢脱硫催化剂,并且活性组分钼、镍以氧化物计,钼的含量为15% (质量比),镍的含量为0.5%(质量比),γ
‑
al2o3载体的含量为84.5%。该加氢脱硫催化剂在加氢反应器中的装填体积百分数为90%。反应物流后进入下单元装填的是一种氧化铝的含量10%(质量比),zsm
‑
5分子筛84.5%(质量比)为载体,金属活性组分为铁、锌的加氢芳构化修复催化剂,其中活性组分铁、锌以氧化物计,铁(三氧化二铁)的含量为5%(质量比),锌的含量为0.5%(质量比)。该加氢芳构化催化剂在加氢反应器中的装填体积百分数为10%。然后以下的加氢操作条件,入口压力为3.5mpa,初
期反应温度330℃,末期反应温度360℃及体积空速0.8/h
‑1,最后获得针状焦原料产品,各项性能指标见表5。
[0029]
实施例2
[0030]
采用与实施例1相同的催化油浆原料和处理工艺,其中采用耐高温金属材料膜滤芯错流过滤器过滤,其膜孔径为:0.05μm,操作工艺条件见表2;减压蒸馏操作条件见表 3;将减压蒸馏得到的中间馏分与氢气混合后导入加氢反应器进行加氢处理,氢油体积比为1000:1,加氢塔中上部装填加氢催化剂,催化剂中钼和镍的含量分别为0.5%和8%,载体γ
‑
al2o3的含量为91.5%,塔中装填量为70%,富含芳烃馏分通过该层脱除硫、氮等元素;加氢塔中下部装填加氢芳构化修复催化剂,铁和锌的含量分别为1%和7%,载体为氧化铝的含量82%(质量比),zsm
‑
5分子筛10%(质量比)为载体,塔中装填量为30%。其它操作条件见表4;经过以上工艺处理后得到满足生产高端针状焦组分的要求,产品性质见表5。
[0031]
实施例3
[0032]
采用与实施例1相同的催化油浆原料和处理工艺,其中采用耐高温陶瓷膜滤芯错流过滤器过滤,其膜孔径为:0.1μm,操作工艺条件见表2;减压蒸馏操作条件见表3;将减压蒸馏得到的中间馏分与氢气混合后导入加氢反应器进行加氢处理,氢油体积比为 900:1,加氢塔中上部装填加氢催化剂,催化剂中钼和镍的含量分别为3%和4%,载体γ
‑
al2o3的含量为93.0%,塔中装填量为80%,富含芳烃馏分通过该层脱除硫、氮等元素;加氢塔中下部装填加氢芳构化修复催化剂,铁和锌的含量分别为2%和5%,载体为氧化铝的含量50%(质量比),zsm
‑
5分子筛43%(质量比)为载体,塔中装填量为20%。其它操作条件见表4;经过以上工艺处理后得到满足生产高端针状焦组分的要求,产品性质见表5。
[0033]
表2错流过滤器工艺条件
[0034][0035]
表3减压蒸馏单元工艺条件
[0036][0037]
表4加氢单元工艺条件
[0038][0039]
表5产品馏分性质
[0040]