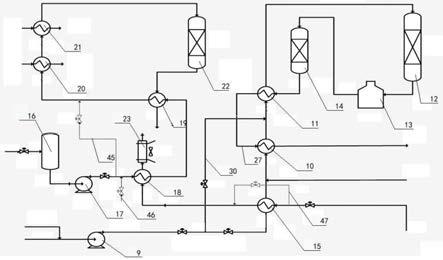
1.本实用新型涉及石化装置技术领域,具体涉及一种利用能量梯级回收利用的汽油加氢系统。
背景技术:
2.近年来,我国经济高速发展促进了汽油消费量的急剧增加,已成为仅次于美国的第二大汽油消费国。大量的汽油消费带来严重的空气污染问题,降低汽油中的硫含量是减少污染的有效手段之一。目前应用最为广泛的是各种汽油选择性加氢技术。现有技术中,高温热源以初始温度直接与换热器壳程的混合进料进行换热,温差约160℃,不利于高温热量的梯级利用,造成高温热源的浪费,同时温差过大影响换热器的安全运行,这种能量利用的不协调现象势必影响全厂的整体经济效益。
技术实现要素:
3.为解决上述问题,本实用新型提供了一种利用能量梯级回收利用的工艺的汽油加氢系统。
4.为实现上述目的,本实用新型采用的技术方案是:
5.一种汽油加氢系统,它包括催化汽油缓冲罐,一段加氢进料泵,催化汽油缓冲罐连接有预加氢反应进料泵,预加氢反应进料泵将催化汽油缓冲罐的产物依次通过精制柴油/预加氢反应进料换热器,预加氢反应进料/反应产物换热器,新增后精制反应器流出物/预加氢反应进料换热器,换热后送入预加氢反应器反应,反应后的产物通过预加氢反应进料/反应产物换热器换热后排到预分馏塔;
6.一段加氢进料泵将物料依次通过新增精制柴油/一段加氢反应进料换热器,一段反应流出物/混合进料换热器,一段反应流出物/混合进料换热器,换热后送入一段加氢反应器进行一段加氢反应,反应后的产物经过一段加氢加热炉加热后进入后精制反应器反应,反应后的产物通过一段反应流出物/混合进料换热器,一段反应流出物/混合进料换热器换热后送入到新增后精制反应器流出物/预加氢反应进料换热器;
7.新增精制柴油/一段加氢反应进料换热器上连有精制柴油输送管线,精制柴油输送管线通过新增精制柴油/一段加氢反应进料换热器、精制柴油/预加氢反应进料换热器进行换热,精制柴油/预加氢反应进料换热器上还连有精制柴油空冷器。
8.所述一段加氢进料泵与新增精制柴油/一段加氢反应进料换热器之间的管线上设置有两个阀门,上述两个阀门之间的管线上设有并联管线a,上述并联管线a连通到一段反应流出物/混合进料换热器与一段反应流出物/混合进料换热器的管线之间;一段反应流出物/混合进料换热器与一段反应流出物/混合进料换热器之间还设有并联管线d,并联管线a与并联管线d为一段加氢反应进料输送管线,并联管线a上设有阀门。
9.所述预加氢反应进料泵与精制柴油/预加氢反应进料换热器连通的管线上设有阀门,上述管线在经过阀门后设有并联管线b、并联管线c,并联管线b连通到预加氢反应进料/
反应产物换热器与新增后精制反应器流出物/预加氢反应进料换热器的管线之间,并联管线b是循环氢输送管线,并联管线b上设有阀门,并联管线c是氢气输送管线,并联管线c上设有阀门。
10.所述精制柴油输送管线上设有阀门,在阀门后经过的新增精制柴油/一段加氢反应进料换热器前后位置设有并联管线e,并联管线e为精制柴油输送管线。
11.所述新增精制柴油/一段加氢反应进料换热器、新增后精制反应器流出物/预加氢反应进料换热器为u型管式换热器。
12.所述精制柴油输送管线、氢气输送管线、一段加氢反应进料输送管线、预加氢反应进料输送管线均为碳钢材质制成。
13.所述后精制反应器、预加氢反应器、一段加氢反应器为合金钢材质制成。使用本实用新型的有益效果是:本系统解决了原工艺中热源后精制反应器产物和精制柴油存在的高温热量浪费的问题,有效地保证了换热器的安全运行,大大节省了预加氢反应进料加热器的蒸汽用量以及精制柴油空冷器的用电量,降低了精制柴油空冷器的运转负荷。有效提高了装置综合经济效益,并且实现了后精制反应器产物以及精制柴油高温热量的有效梯级利用。
附图说明
14.图1为本实用新型系统流程图。
15.附图标记包括:9为一段加氢进料泵,10、11为一段反应流出物/混合进料换热器,12为一段加氢反应器,13为一段加氢加热炉,14为后精制反应器,15为新增精制柴油/一段加氢反应进料换热器,16为催化汽油缓冲罐,17为预加氢反应进料泵,18为精制柴油/预加氢反应进料换热器,19为预加氢反应进料/反应产物换热器,20为新增后精制反应器流出物/预加氢反应进料换热器,21为预加氢反应进料加热器,22为预加氢反应器,23为精制柴油空冷器,45为循环氢输送管线,46为氢气输送管线,47为精制柴油输送管线,27、30为一段加氢反应进料输送管线。
具体实施方式
16.为使本技术方案的目的、技术方案和优点更加清楚明了,下面结合具体实施方式,对本技术方案进一步详细说明。应该理解,这些描述只是示例性的,而不是要限制本技术方案的范围。
17.本实用新型公开了一种汽油加氢系统,它包括催化汽油缓冲罐16,一段加氢进料泵9,催化汽油缓冲罐16连接有预加氢反应进料泵17,预加氢反应进料泵17将催化汽油缓冲罐16的产物依次通过精制柴油/预加氢反应进料换热器18,预加氢反应进料/反应产物换热器19,新增后精制反应器流出物/预加氢反应进料换热器20,换热后送入预加氢反应器22反应,反应后的产物通过预加氢反应进料/反应产物换热器19换热后排到预分馏塔;
18.一段加氢进料泵9将物料依次通过新增精制柴油/一段加氢反应进料换热器15,一段反应流出物/混合进料换热器10,一段反应流出物/混合进料换热器11,换热后送入一段加氢反应器12进行一段加氢反应,反应后的产物经过一段加氢加热炉13加热后进入后精制反应器14反应,反应后的产物通过一段反应流出物/混合进料换热器11,一段反应流出物/
混合进料换热器10换热后送入到新增后精制反应器流出物/预加氢反应进料换热器20;
19.新增精制柴油/一段加氢反应进料换热器15上连有精制柴油输送管线,精制柴油输送管线通过新增精制柴油/一段加氢反应进料换热器15、精制柴油/预加氢反应进料换热器18进行换热,精制柴油/预加氢反应进料换热器18上还连有精制柴油空冷器23。
20.所述一段加氢进料泵9与新增精制柴油/一段加氢反应进料换热器15之间的管线上设置有两个阀门,上述两个阀门之间的管线上设有并联管线a30,上述并联管线a30连通到一段反应流出物/混合进料换热器10与一段反应流出物/混合进料换热器11的管线之间;一段反应流出物/混合进料换热器10与一段反应流出物/混合进料换热器11之间还设有并联管线d27,并联管线a30与并联管线d27为一段加氢反应进料输送管线,并联管线a30上设有阀门。
21.所述预加氢反应进料泵17与精制柴油/预加氢反应进料换热器18连通的管线上设有阀门,上述管线在经过阀门后设有并联管线b45、并联管线c46,并联管线b45连通到预加氢反应进料/反应产物换热器19与新增后精制反应器流出物/预加氢反应进料换热器20的管线之间,并联管线b45是循环氢输送管线,并联管线b45上设有阀门,并联管线c46是氢气输送管线,并联管线c46上设有阀门。
22.所述精制柴油输送管线上设有阀门,在阀门后经过的新增精制柴油/一段加氢反应进料换热器15前后位置设有并联管线e47,并联管线e47为精制柴油输送管线。
23.所述新增精制柴油/一段加氢反应进料换热器15、新增后精制反应器流出物/预加氢反应进料换热器20为u型管式换热器。
24.所述精制柴油输送管线、氢气输送管线、一段加氢反应进料输送管线、预加氢反应进料输送管线均为碳钢材质制成。
25.所述后精制反应器14、预加氢反应器22、一段加氢反应器12为合金钢材质制成。
26.本系统工作流程如下:催化汽油进入催化汽油缓冲罐16进行沉降脱水;脱水后的原料油进入预加氢反应进料泵17增压至2.4mpa左右,与来自装置界区外的少量新氢混合,再依次与精制柴油/预加氢反应进料换热器18、预加氢反应进料/反应产物换热器19以及新增后精制反应器流出物/预加氢反应进料换热器20进行换热,再经预加氢反应进料加热器21提高到140℃以上后送入预加氢反应器22,在较低的反应温度和氢油比的条件下进行二烯烃饱和、低分子硫醇硫的转化等反应。反应产物经换热后送至预分馏塔分割轻、重汽油。
27.一段加氢混合进料与来自装置外的新氢、增压后的循环氢混合,经过新增精制柴油/一段加氢反应进料换热器15和一段反应流出物/混合进料换热器11、10换热至一段加氢反应器12所需入口温度后,以气相状态进入一段加氢反应器。一段加氢反应产物经一段加热炉13加热后,进入后精制反应器14,后精制反应器14反应产物经一段反应流出物/混合进料换热器11、10换热后送至新增后精制反应器流出物/预加氢反应进料换热器20进行换热。
28.本系统中,精制柴油输送管线起始端连接于柴油改质装置的精制柴油/原料油换热器的管程出口,循环氢输送管线起始端连接于循环氢压缩机,然后至一段加氢反应进料输送管线;氢气输送管线起始端自装置外的氢气管网来,至预加氢反应进料输送管线;一段加氢反应进料输送管线起始端链接于中汽油切割塔底及抽出油凝结器,预加氢反应进料输送管线起始端自装置外来。
29.在该实施例中,该炼厂的汽油加氢工艺装置每年可节省蒸汽用量27057.77吨,可
节省电量315200千万时,每年的经济效益为705万元,投资回收期为1.2个月。
30.与现有技术相比,本系统有如下有益效果:
31.1.通过考虑到就近原则,相邻布置的柴油改质装置同样存在高温热源浪费的情况,高温热源由200左右摄氏度直接被冷却至常温,可补充足够热量。因此,将汽油加氢装置与柴油改质装置进行热联合,经过热联合后,大大节省了现有装置的燃料及动力消耗,降低了后续设备冷却负荷,有效提高了综合经济效益,解决了高温热源浪费问题,并且实现了高温热源的有效梯级利用。
32.2.通过利用切实可行设计流程,成功实现了高温热源的梯级利用。
33.3.布局合理,控制方便。考虑到就近原则,合理利用相邻布置的柴油改质装置的高温热源,巧妙的解决了柴油改质装置和汽油加氢装置存在的高温热源浪费现象,以及装置存在的安全隐患,成功实现能量优化的梯级利用。
34.4.注重设备选型及材质,安全可靠。
35.以上内容仅为本实用新型的较佳实施例,对于本领域的普通技术人员,依据本技术内容的思想,在具体实施方式及应用范围上可以作出许多变化,只要这些变化未脱离本实用新型的构思,均属于本专利的保护范围。