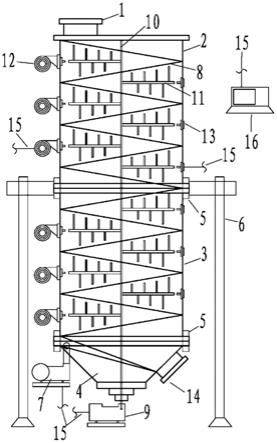
1.本实用新型涉及污泥和生物质处理技术领域,具体涉及一种螺旋干燥碳化一体设备。
背景技术:
2.污废水的处理过程会产生大量的废弃污泥,废弃污泥里含有大量有机质、重金属、磷、病菌和虫卵等物质,如果不妥善处置,那么废弃污泥将进一步对环境造成污染和破坏。
3.传统污泥处理处置方法包括海洋倾倒、堆场填埋和污泥焚烧等。然而使用这些方法处理处置污泥,都存在二次污染问题:海洋倾倒和堆场填埋使得污泥包含的有害物质再次释放;堆场填埋占地面积大;污泥焚烧产生大量有毒有害气体,大量的热源需求使得污泥成本大大提高。
4.污泥碳化制备生物碳被认为是一种优良的污泥处理方法,污泥碳化能有效裂解有机质、固化重金属和营养盐、杀灭病菌虫卵等,碳化后形成的生物碳在使用过程不造成二次污染。发明专利cn1123181129a公开了城市污水厂污泥制备生物碳的方法,污泥在无氧状态下热解产生的生物碳可用以堆肥和土壤修复等。而适当添加生物质可使污泥黏性降低、提高污泥生物碳有机质含量,并可有效减少污泥碳化过程产生的臭气。发明专利cn1112311532a、 cn128119810510a、cn128111282a、cn1231138002a等均阐述了生物质碳化制备生物碳的方法,发明专利cn1111009885a公开了污泥和园林废弃物干化干馏的装置,但目前仍缺少污泥掺烧生物质制备复合生物碳的装置和方法,也未曾提出污泥掺烧生物质在实际操作过程的可行性;实用新型cn212911219u、 cn2122109221u和发明专利cn111904339a等均公开了滚筒式(旋窑)污泥碳化的装置,但滚筒式碳化炉均存在长期运行稳定性问题和臭气废气外泄问题。
技术实现要素:
5.针对现有技术存在的不足,本实用新型的目的在于提供一种螺旋干燥碳化一体设备,该装置能够对废弃污泥和废弃生物质进行干燥碳化,且可以长期高温稳定运行,并考虑可对臭气尾气进行利用或处理。
6.本实用新型实现废弃污泥和废弃生物质的协同干燥碳化,干燥温度为105℃左右,碳化温度为300℃~600℃,干燥碳化时间为1~2h,在同时处理两种废弃物的同时,处理后的产生的生物碳还能进行资源化利用,生物质掺入污泥中进行碳化还能有效改善生物碳的性能。本实用新型将废弃生物质掺入污泥中,能有效降低污泥的黏性,有利于污泥后续干燥碳化过程的进行。本实用新型将废弃生物质掺入污泥中,能有效提高生物碳产率、增加生物碳热值。本实用新型摒弃了旋窑的设置,采用立式炉体和螺旋传送带进行污泥的碳化,可长期不间歇稳定运行、连续生产。本实用新型的立式结构起到热量的内部循环作用,使得本实用新型热效率高,从而使投资和运行成本降低。本实用新型为立式炉体,通过螺旋传送带的连续运行,实现连续进料、连续碳化、连续出料的过程,保证设备长期高温运行的连续性和
炉腔高温的充分利用,打散杆的打散作用使污泥均匀受热,减少反应时间,打散造粒使得碳化更为彻底。本实用新型通过温度传感器传递碳化炉温度,并通过中央控制系统控制多台燃烧机启闭个数和燃烧功率,起到精确控温螺旋干燥碳化一体设备炉腔内的温度控制,可根据需要上下调整和监控温度,充分利用热量。本实用新型的燃烧机在炉外布设,维修方便。本实用新型的炉体内壁经过特殊处理,具有抗腐蚀能力,因此可将本实用新型用于工业污泥、食品污泥等具有腐蚀性污泥的碳化。本实用新型采用中央控制系统自动控制进出料、设备启动运行、温度等。
7.本实用新型可用于三大类污泥的碳化处理:生活污水处理厂污泥;水体疏浚污泥;食品污泥、印染污泥、造纸污泥等工业污泥。本实用新型同时具有焚烧模式:也可对上述污泥进行焚烧处理。
8.为了实现上述目的,本实用新型提供如下技术方案:
9.一种螺旋干燥碳化一体设备,其特征在于,一体设备主要由干燥炉体、碳化炉体和出料仓组成,设备内部设置有一根从上到下的固定杆,螺旋传送带和打散杆安装在固定杆上,螺旋传送带起到传送污泥的作用,打散杆起到打散污泥的作用;在设备的外壁面设置有加热装置,所述加热装置的发热口位于所述干燥炉体和碳化炉体一侧;所述加热装置使得碳化炉体内温度具有梯度变换,设备内热气流进行内部循环流动。
10.进一步地,所述干燥炉体和碳化炉体为圆柱腔体,直径为3~5m,高度为 3
‑
10m;所述出料仓为到圆锥腔体,直径为3~5m,与干燥炉体和碳化炉体直径大小对应,高度为1~2m;干燥炉体、碳化炉体和出料仓通过密封连接卡箍固定密封连接;所述干燥炉体、碳化炉体和出料仓固定密封连接后,由支撑架支撑站立。
11.进一步地,所述设备内部设置有一根从上到下的固定杆,固定杆上安装有一条从上到下的螺旋传送带;所述螺旋传送带宽度根据干燥炉体和碳化炉体直径大小设置1~2m;螺旋传送带上下层间距可根据需求设定20~60cm;所述螺旋传送带可由传送驱动器带动转动,向下传送污泥;所述固定杆上安装有多根打散杆;所述打散杆长1~2m,对应螺旋传送带宽度;打散杆可由转动驱动器带动转动,对污泥起到打散造粒作用。
12.进一步地,所述加热装置为燃烧机、不锈钢电加热管、陶瓷电加热器或石墨烯加热器。
13.进一步地,设备腔体内设置有温度传感器;所述的温度传感器安装在干燥炉体和碳化炉体一侧。
14.进一步地,还包括中央控制系统,所述中央控制系统分别与传送驱动器温度传感器和加热装置通过中央控制系统连接线电性连接,用于采集温度数据以及控制传送驱动器、转动驱动器和加热装置的启闭和功率;所述中央控制系统控制传送驱动器启闭和功率,进而控制螺旋传送带的启闭和功率,调节污泥生物质混合物的干燥碳化时间;所述的中央控制系统控制加热装置的启闭和燃烧功率,调节干燥炉体和碳化炉体内的干燥温度、碳化温度和温度梯度。
15.进一步地,还包括进料口和出料口;所述进料口为边长20cm~100cm正方形;污泥生物质混合物由所述进料口进入碳化炉;所述进料口大小可根据需要碳化的污泥生物质混合物进料量进行设计;所述出料口为直径20cm~100cm圆形;碳化后形成的复合生物碳由所述出料口排出设备;所处出料口大小可根据需要碳化后的复合生物碳量进行设计。
16.进一步地,所述干燥炉体包括进料口、干燥炉腔、干燥炉腔加热装置安装口和干燥炉腔温度传感器安装口;所述进料口设置在干燥炉腔上部边缘;所述干燥炉腔加热装置安装口设置在干燥炉腔一侧,加热装置安装口直径为50 cm~150cm的圆形;所述干燥炉腔温度传感器安装口设置在干燥炉腔一侧,温度传感器安装口为直径2cm~5cm的圆形。
17.进一步地,所述碳化炉体包括碳化炉腔、碳化炉腔加热装置安装口和碳化炉腔温度传感器安装口;所述碳化炉腔加热装置安装口设置在碳化炉腔一侧,加热装置安装口直径为50cm~150cm的圆形;所述碳化炉腔温度传感器安装口设置在碳化炉腔一侧,温度传感器安装口为直径2cm~5cm的圆形。
18.进一步地,所述出料仓包括出料口、出料圆锥腔和固定杆固定装置;所述出料圆锥腔为倒圆锥腔体;所述出料口设置在出料圆锥腔一侧;所述固定杆固定装置设置在出料圆锥腔底部。
19.进一步地,所述转动驱动器包括传动主机、主机传动带、传动主轮、副传动带和传动副轮;所述主机传动带安装在传动主机和传动主轮之间,传动主机通过主机传动带带动传动主轮转动;所述副传动带安装在传动主轮和传动副轮之间,传动主轮通过副传动带带动传动副轮转动;螺旋传送带安装在转动副轮上;所述传动主轮带动副传动带和传动副轮运动,进而带动螺旋传送带传送;所述传动主机为电机。
20.进一步地,所述打散杆包括打散主杆、打散副杆和打散次杆;所述打散主杆一端连接在固定杆上,长度为1~2m;所述打散副杆安装在打散主杆上,长度为0.5~1m;所述打散次杆安装在打散副杆上,长度为10~20cm;
21.进一步地,所述打散杆活动连接在固定杆上,安装有转动带,转动带与转动驱动器连接;所述打散杆可由转动带驱动转动。
22.进一步地,所述进料口包括进料仓、进料上翻板和进料下闸板;所述进料上翻板设置在进料仓顶部,进料下闸板设置在进料仓底部。
23.进一步地,所述出料口包括出料储存仓、出料上闸板和出料下翻板;所述出料上闸板设置在出料储存仓顶部,出料下翻板设置在出料储存仓底部。
24.进一步地,所述设备整体均使用不锈钢316材质。
25.所述设备中处于缺氧状态,将污泥生物质混合物放入精确控温螺旋干燥碳化一体设备中,由螺旋传送带从上到下传送,打散杆协同进行污泥打散;干燥炉体对污泥进行干燥,碳化炉体对干燥后的污泥进行碳化;碳化炉体同时采用设备内具有梯度温度变化的热解方法进行热解;设备中相邻两层螺旋传送带温度差为10℃~50℃,下层温度高于上层。
26.本实用新型立式结构可使热量充分利用,碳化炉体较高温度的热气流向上流动,对干燥设备中的污泥进行干燥,干燥后的污泥进入碳化炉体进行碳化;加热装置使得碳化炉体内温度具有梯度变换,设备内热气流进行内部循环流动,最顶层传送带污泥经过最低温度热解后传送入下一层,较高温度的下一层使污泥持续受热。
27.一种螺旋干燥碳化一体设备用于污泥掺烧生物质共热解的方法,包括如下步骤:
28.(1)碳化前先进行干燥炉体和碳化炉体的预热,随后中央控制系统对燃烧机根据干燥和碳化过程温度高低进行启闭和功率调整,每层燃烧机同时加热,温度传感器实时监控各层温度;干燥炉体控制温度为105
±
5℃;碳化炉体控制最底层温度为目标碳化温度,由下而上逐层递减10℃~50℃,形成炉内温度梯度;所述碳化炉体预热具体步骤为:进行20~
80min的预热,预热温度为300℃~600℃;
29.(2)干燥炉体和碳化炉体到达干燥碳化所需温度后,进料上翻板开启,进料下闸板关闭,污泥生物质混合物进入到进料仓中临时储存;之后进料上翻板关闭,进料下翻板开启,污泥生物质混合物由进料口进入到干燥炉体内,落到螺旋传送带上;所述污泥生物质混合物中,生物质占混合物总重量1%~2%;所述生物质包括树叶、茶叶渣、锯木屑、甘蔗渣或水葫芦中的一种以上;所述螺旋传送带由转动驱动器和固定杆带动传送污泥生物质混合物,对污泥生物质混合物进行干燥;
30.(3)污泥生物质混合物干燥后随螺旋传送带进入碳化炉体,先经过较上层低温碳化后,逐渐进入中下层高温进行碳化,碳化炉体内由于温度梯度的存在,产生的热气流使污泥生物质混合物碳化效率增大;碳化后的余热气体向上流动,对干燥炉体进行温度补偿,起到余热利用的功能;
31.(4)温度传感器实时监控干燥炉体和碳化炉体内的温度,并实时反馈给中央控制系统,中央控制系统通过对燃烧机的调控,实时控制干燥炉体和碳化炉体内的温度稳定在目标温度内;
32.(5)碳化后形成的生物碳进入出料仓,出料上闸板开启,碳化后的复合生物碳进入出料储存仓临时储存;出料上闸板关闭,出料下翻板开启,出料储存仓中临时储存的复合生物碳排出出料仓进行进一步利用。
33.上述方法中,所述污泥为工业污泥或生活污泥中的一种以上。
34.上述方法中,所述工业污泥包括印染污泥、洗水污泥、食品工业污泥、造纸污泥、高浓废水处理污泥、电镀污泥或垃圾渗滤液污泥中的一种以上。
35.上述方法中,所述生活污泥包括生活污水处理厂污泥或河道疏浚淤泥中的一种以上。
36.本实用新型精确控温螺旋干燥碳化一体设备在使用过程中不设置干燥阶段,可直接将两个炉体当成碳化炉体,进行单一碳化过程。
37.本实用新型的精确控温螺旋干燥碳化一体设备在使用过程中将进料口和出料口打开还可以作为焚烧炉使用,通过混入空气,形成有氧环境,对污泥等固体废物进行焚烧。
38.与现有技术相比,本实用新型的有益效果是:
39.1.本实用新型将生物质(树叶、茶叶渣、锯木屑、甘蔗渣、水葫芦等)掺入污泥中,能有效降低污泥的黏性,有利于污泥后续碳化过程的进行,并提高了生物碳产率、增加生物碳热值,还可减少污泥碳化过程产生的臭气。
40.2.本实用新型摒弃了传统旋窑的设置,采用立式炉体和螺旋传送带进行污泥的碳化,可极大程度解决设备长期高温运行引起的设备变形、过快老化和趴窝等问题,立式炉体设置可在高温条件下长期不间歇稳定运行、连续生产。
41.3.本实用新型的立式结构起到热量的内部循环作用,使得本实用新型热效率高,并可根据实际所需设备大小,选择燃烧机和温度传感器个数;多台燃烧机可有效控制炉腔内各层形成温度梯度,多层螺旋传送带逐级反应,使得碳化更为彻底,碳化产生的余热还可利用到干燥炉体内对污泥生物质混合物进行干燥,节约能源的同时提高了工作效率。
42.4.本实用新型的燃烧机等组件均在炉外布设,维修方便;且炉体内壁经过特殊处理,具有抗腐蚀能力,因此可将本实用新型用于工业污泥、食品污泥等具有腐蚀性污泥的碳
化。
43.5.本实用新型采用中央控制系统自动控制进出料、自动控制设备启动运行、根据温度传感器反馈碳化炉实时温度、自动控制碳化炉温度等。
附图说明
44.图1为一种螺旋干燥碳化一体设备结构示意图。
45.图2为一种螺旋干燥碳化一体设备的螺旋传送带结构示意图。
46.图3为一种螺旋干燥碳化一体设备的干燥炉体结构示意图。
47.图4为一种螺旋干燥碳化一体设备的碳化炉体结构示意图。
48.图5为一种螺旋干燥碳化一体设备的出料仓结构示意图。
49.图6为一种螺旋干燥碳化一体设备的传送驱动器结构示意图。
50.图7为一种螺旋干燥碳化一体设备的打散杆结构示意图。
51.图8为一种螺旋干燥碳化一体设备的打散杆转动带结构示意图。
52.图9为一种螺旋干燥碳化一体设备的转动驱动器结构示意图。
53.图10为一种螺旋干燥碳化一体设备的进料口结构示意图。
54.图11为一种螺旋干燥碳化一体设备的出料口结构示意图;
55.图12为一种螺旋干燥碳化一体设备的螺旋传送带立体示意图。
56.图中各个部件如下:
57.进料口1、干燥炉体2、碳化炉体3、出料仓4、密封连接卡箍5、支撑架6、传送驱动器7、螺旋传送带8、转动驱动器9、固定杆10、打散杆11、燃烧机 12、温度传感器13、出料口14、中央控制系统连接线15、中央控制系统16、进料仓101、进料上翻板102、进料下闸板103、干燥炉腔201、干燥炉腔加热装置安装口202、和干燥炉腔温度传感器安装口203、碳化炉腔301、碳化炉腔加热装置安装口302、和碳化炉腔温度传感器安装口303、出料圆锥腔401、固定杆固定装置402、传动主机701、主机传动带702、传动主轮703、副传动带 704、传动副轮705、转动主轮901、转动杆902、打散主杆1101、打散副杆1102、打散次杆1103、转动带1104、出料储存仓1401、出料上闸板1402、出料下翻板1403。
具体实施方式
58.下面将结合本实用新型中的附图,对本实用新型实施例中的技术方案进行清楚、完整地描述,显然,所描述的实施例仅仅是本实用新型一部分实施例,而不是全部的实施例。基于本实用新型中的实施例,本领域普通技术人员在没有做出创造性劳动前提下所获得的所有其他实施例,都属于本实用新型保护的范围。
59.除非另有定义,本文所使用的所有的技术和科学术语与属于本实用新型的技术领域的技术人员通常理解的含义相同。本文中在本实用新型的说明书中所使用的术语只是为了描述具体的实施例的目的,不是旨在于限制本实用新型。本文所使用的术语“及/或”包括一个或多个相关的所列项目的任意的和所有的组合。
60.下面结合具体实施例对本实用新型作进一步地具体详细描述,但本实用新型的实施方式不限于此,对于未特别注明的工艺参数,可参照常规技术进行。
61.如图1~图12所述,一种螺旋干燥碳化一体设备,一体设备主要由干燥炉体 2、碳
化炉体3和出料仓4组成,设备内部设置有一根从上到下的固定杆10,螺旋传送带8和打散杆11安装在固定杆10上,螺旋传送带8起到传送污泥的作用,打散杆11起到打散污泥的作用;在设备的外壁面设置有加热装置,所述加热装置的发热口位于所述干燥炉体2和碳化炉体3一侧;所述加热装置使得碳化炉体3内温度具有梯度变换,设备内热气流进行内部循环流动。所述干燥炉体2和碳化炉体3为圆柱腔体,直径为3~5m,高度为3
‑
10m,出料仓4为到圆锥腔体,直径为3~5m,与干燥炉体和碳化炉体直径大小对应,高度为1~2m,干燥炉体2、碳化炉体3和出料仓4通过密封连接卡箍5固定密封连接;所述干燥炉体2、碳化炉体3和出料仓4固定密封连接后,由支撑架6支撑站立。
62.本实用新型所述设备内部设置有一根从上到下的固定杆10,固定杆10上安装有一条从上到下的螺旋传送带8;所述螺旋传送带8宽度根据干燥炉体2和碳化炉体3直径大小设置1~2m;螺旋传送带8上下层间距可根据需求设定20~60 cm;所述螺旋传送带8可由传送驱动器7带动转动,如图2所示,传送驱动器 7位于螺旋传送带8的一端,用于带动起运动,向下传送污泥;所述固定杆10 上安装有多根打散杆11,打散杆11可由转动驱动器9带动转动,对污泥起到打散造粒作用。所述加热装置为燃烧机12、不锈钢电加热管、陶瓷电加热器或石墨烯加热器。所述设备腔体内设置有温度传感器13;所述的温度传感器13安装在干燥炉体2和碳化炉体3一侧。
63.本实用新型还包括中央控制系统16,所述中央控制系统16分别与传送驱动器7温度传感器13和加热装置通过中央控制系统连接线15电性连接,用于采集温度数据以及控制传送驱动器7、转动驱动器9和加热装置的启闭和功率;所述中央控制系统16控制传送驱动器7启闭和功率,进而控制螺旋传送带8的启闭和功率,调节污泥生物质混合物的干燥碳化时间;所述的中央控制系统16控制加热装置的启闭和燃烧功率,调节干燥炉体2和碳化炉体3内的干燥温度、碳化温度和温度梯度。
64.本实用新型还包括进料口1和出料口14;所述进料口1为边长20cm~100cm 正方形;污泥生物质混合物由所述进料口1进入碳化炉;所述进料口1大小可根据需要碳化的污泥生物质混合物进料量进行设计;所述出料口14为直径20 cm~100cm圆形;碳化后形成的复合生物碳由所述出料口14排出设备;所处出料口14大小可根据需要碳化后的复合生物碳量进行设计。
65.如图3所示,所述干燥炉体2包括进料口1、干燥炉腔201、干燥炉腔加热装置安装口202和干燥炉腔温度传感器安装口203;所述进料口1设置在干燥炉腔201上部边缘;所述干燥炉腔加热装置安装口202设置在干燥炉腔201一侧,加热装置安装口202直径为50cm~150cm的圆形;所述干燥炉腔温度传感器安装口203设置在干燥炉腔201一侧,温度传感器安装口203为直径2cm~5cm 的圆形。
66.如图4所示,所述碳化炉体3包括碳化炉腔301、碳化炉腔加热装置安装口 302和碳化炉腔温度传感器安装口303;所述碳化炉腔加热装置安装口302设置在碳化炉腔201一侧;所述碳化炉腔温度传感器安装口203设置在碳化炉腔201 一侧。
67.如图5所示,所述出料仓4包括出料口14、出料圆锥腔401和固定杆固定装置402;所述出料圆锥腔401为倒圆锥腔体;所述出料口设置在出料圆锥腔401一侧;所述固定杆固定装置402设置在出料圆锥腔401底部。
68.如图6所示,所述转动驱动器7包括传动主机701、主机传动带702、传动主轮703、副
传动带704和传动副轮705;所述主机传动带702安装在传动主机 701和传动主轮703之间,传动主机701通过主机传动带702带动传动主轮703 转动;所述副传动带704安装在传动主轮703和传动副轮705之间,传动主轮 703通过副传动带704带动传动副轮705转动;螺旋传送带8安装在转动副轮 705上;所述传动主轮703带动副传动带704和传动副轮705运动,进而带动螺旋传送带8传送;所述传动主机701为电机。
69.如图7所示,所述打散杆11包括打散主杆1101、打散副杆1102和打散次杆1103;所述打散主杆1101一端连接在固定杆10上,长度为1~2m;所述打散副杆1102安装在打散主杆1101上,长度为0.5~1m;所述打散次杆1103安装在打散副杆1102上,长度为10~20cm。
70.如图8所示,所述打散杆11活动连接在固定杆10上,安装有转动带1104,转动带1104与转动驱动器9连接;所述打散杆可由转动带1104驱动转动。
71.如图9所示,所述进料口包括进料仓101、进料上翻板102和进料下闸板 103;所述进料上翻板102设置在进料仓101顶部,进料下闸板103设置在进料仓101底部。
72.如图10所示,所述进料口14包括出料储存仓1401、出料上闸板1402和出料下翻板1403;所述出料上闸板1402设置在出料储存仓1401顶部,出料下翻板1403设置在出料储存仓1401底部。
73.本实用新型精确控温螺旋干燥碳化一体设备在使用过程中不设置干燥阶段,可直接将两个炉体当成碳化炉体,进行单一碳化过程。
74.本实用新型精确控温螺旋干燥碳化一体设备在使用过程中将进料口和出料口打开还可以作为焚烧炉使用,通过混入空气,形成有氧环境,对污泥等固体废物进行焚烧。
75.实施例1
76.采用低温碳化工艺,要求水体疏浚淤泥污泥生物质混合物处理量为8500 kg/h:
77.1)精确控温螺旋干燥碳化一体设备中,干燥炉体2和碳化炉体3均设置高度3m,直径3m,出料仓直径3m,高度1m;螺旋传送带8上下层间距50cm,共设置12层;干燥炉体2的燃烧机12设置3个,碳化炉体3的燃烧机12设置 6个,温度传感器13均设置6个;由中央控制系统16控制9个燃烧机12最大功率启动,对精确控温螺旋干燥碳化一体设备进行预热;干燥炉体2目标温度 105℃,到达指定温度后停止加热;碳化炉体3预热目标温度最高300℃,最上层温度到达230℃时,最上一台燃烧机12关闭,第二层温度到达240℃时,第二台燃烧机12关闭,以此类推,直至最低层温度到达300℃,由温度传感器13 实时反馈碳化炉体3内的温度;
78.2)预热温度到达300℃后,温度传感器13反馈信息至中央控制系统16,螺旋传送带8和打散杆11开始运行;
79.3)中央控制系统16控制进料上翻板102开启,进料下闸板103关闭,800 kg水体疏浚淤泥污泥生物质混合物进入到进料仓101中临时储存;之后进料上翻板102关闭,进料下闸板103开启,水体疏浚淤泥污泥生物质混合物由进料口1进入到干燥炉体2内;800kg水体疏浚淤泥污泥生物质混合物落到螺旋传送带8上,并开始传送干燥和碳化;控制干燥碳化整个过程1h,期间打散杆11 将水体疏浚淤泥污泥生物质混合物打散造粒;
80.4)第一次进料的水体疏浚淤泥污泥生物质混合物受热5min后,中央控制系统16控制进料上翻板102开启,进料下闸板103关闭,800kg水体疏浚淤泥污泥生物质混合物进入到进料仓101中临时储存;之后进料上翻板102关闭,进料下闸板103开启,水体疏浚淤泥污泥生物质混合物由进料口1进入到干燥炉体2内,800kg水体疏浚淤泥污泥生物质混合物落到
螺旋传送带8上,并开始传送干燥和碳化;
81.5)水体疏浚淤泥污泥生物质混合物经过干燥炉体2和碳化炉体3逐级受热并打散后,产生复合生物碳,最终进入出料仓4;
82.6)干燥水体疏浚淤泥污泥生物质混合物经过1h碳化后,中央控制系统16 控制出料上闸板1402开启,碳化后的复合生物碳进入出料储存仓1401临时储存;出料上闸板1402关闭,出料下翻板1403开启,出料储存仓中临时储存的复合生物碳排出,运输至储存仓储存;系统连续运行300天,1h产生的复合生物碳约为420kg;
83.7)碳化过程,碳化炉体2内温度由温度传感器13实时监控,最高温度偏离300
±
30℃时,温度传感器13将信息反馈至中央控制系统16,中央控制系统控制燃烧机12功率增减,对碳化炉体3内温度进行调控,保持炉腔温度为 300
±
30℃。
84.实施例2
85.采用高温快速碳化工艺,要求印染污泥(该印染污泥中含有生物质,含量约为2%)处理量为1200kg/h:
86.1)精确控温螺旋干燥碳化一体设备中,不设置干燥工艺,只设置碳化工艺 3;干燥炉体2和碳化炉体3均设置高度3m,直径3m,出料仓直径3m,高度 1m;螺旋传送带8上下层间距1m,共设置6层;干燥炉体2和碳化炉体3的燃烧机12设置3个,温度传感器13均设置3个;由中央控制系统16控制6个燃烧机12最大功率启动,对精确控温螺旋干燥碳化一体设备进行预热;两个碳化炉体3预热目标温度最高600℃,最上层温度到达500℃时,最上一台燃烧机 12关闭,第二层温度到达520℃时,第二台燃烧机12关闭,以此类推,直至最低层温度到达600℃,由温度传感器13实时反馈碳化炉体3内的温度;
87.2)预热温度到达600℃后,温度传感器13反馈信息至中央控制系统16,螺旋传送带8和打散杆11开始运行;
88.3)中央控制系统16控制进料上翻板102开启,进料下闸板103关闭,200 kg印染污泥生物质混合物进入到进料仓101中临时储存;之后进料上翻板102 关闭,进料下闸板103开启,印染污泥生物质混合物由进料口1进入到干燥炉体2内;200kg印染污泥生物质混合物落到螺旋传送带8上,并开始传送碳化;控制干燥碳化整个过程1h,期间打散杆11将印染污泥生物质混合物打散造粒;
89.4)第一次进料的印染污泥生物质混合物受热10min后,中央控制系统16 控制进料上翻板102开启,进料下闸板103关闭,200kg印染污泥生物质混合物进入到进料仓101中临时储存;之后进料上翻板102关闭,进料下闸板103 开启,印染污泥生物质混合物由进料口1进入到干燥炉体2内,200kg印染污泥生物质混合物落到螺旋传送带8上,并开始传送干燥和碳化;
90.5)印染污泥生物质混合物经过干燥炉体2和碳化炉体3逐级受热并打散后,产生复合生物碳,最终进入出料仓4;
91.6)干燥印染污泥生物质混合物经过1h碳化后,中央控制系统16控制出料上闸板1402开启,碳化后的复合生物碳进入出料储存仓1401临时储存;出料上闸板1402关闭,出料下翻板1403开启,出料储存仓中临时储存的复合生物碳排出,运输至储存仓储存;系统连续运行300天,1h产生的复合生物碳约为 420kg;
92.7)碳化过程,碳化炉体2内温度由温度传感器13实时监控,最高温度偏离600
±
20
℃时,温度传感器13将信息反馈至中央控制系统16,中央控制系统控制燃烧机12功率增减,对碳化炉体3内温度进行调控,保持炉腔温度为 600
±
20℃。
93.实施例3
94.采用高温焚烧工艺,要求干燥污泥处理量为1200kg/h:
95.1)精确控温螺旋干燥碳化一体设备安装6个燃烧机12、6个温度传感器13;由中央控制系统16控制6个燃烧机12最大功率启动,螺旋传送带8和打散杆 11开始运行,进料口1和出料口14均打开,由温度传感器13实时反馈设备内的温度;
96.2)200kg干燥污泥由进料口1进入到设备内;200kg干燥污泥由螺旋传送带8承接传送,打散杆11进行打散;
97.3)10min后,最顶层污泥传送至第二层,中央控制系统16控制200kg干燥污泥由进料口1进入到设备内,200kg干燥污泥由螺旋传送带8承接传送,打散杆11进行打散,干燥污泥保持均匀受热状态;以此类推,直至所有振动翻板3均承接了干燥污泥;
98.4)干燥污泥经过螺旋传送带8逐级传送焚烧并打散后,最底层污泥已高温焚烧1h,有机质和有害物质均已气化,仅剩下灰分,灰分由出料口14排出。
99.上述说明是针对本实用新型较佳可行实施例的详细说明,但实施例并非用以限定本实用新型的实用新型申请范围,凡本实用新型所提示的技术精神下所完成的同等变化或修饰变更,均应属于本实用新型所涵盖的实用新型范围。