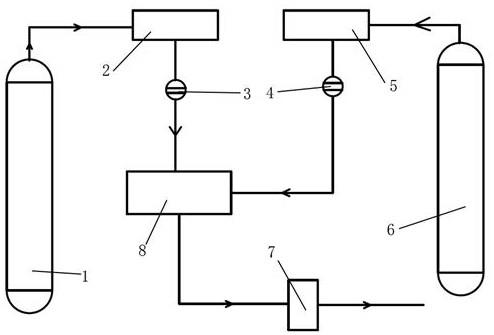
1.本实用新型涉及石油炼化装置,具体涉及原料预处理用不凝气干湿分离装置。
背景技术:
2.在石油炼化过程中,初馏塔顶不凝气在冷凝过程中,会产生瓦斯油,瓦斯油经管道汇入分液罐,瓦斯油在分液罐中大量积累无法排出,可能会导致不凝气后路不通畅,导致塔内压力升高,影响装置操作,同时也产生了安全风险。
技术实现要素:
3.本实用新型的目的就是针对现有技术存在的缺陷,提供原料预处理用不凝气干湿分离装置。
4.本实用新型的技术方案是:
5.包括初馏塔、初馏空冷器、水冷器、回流罐、常压空冷器、常压塔和自动切油分液罐,所述回流罐设置有两条进料支线和一条出料线,所述回流罐的一条进料支线由初馏塔、初馏空冷器和初馏水冷器依次连接并汇入所述回流罐,所述回流罐的另一条进料支线由常压塔、常压空冷器和常压水冷器依次连接并汇入所述回流罐,所述回流罐的出料线与所述自动切油分液罐连接。
6.优选的,所述自动切油分液罐包括外罩、中柱、混合气入管、干气出管、瓦斯油出管、螺旋冷凝板、气液分离板和切油活动块,所述外罩为中空罐体结构,所述中柱竖直固定于所述外罩内部的中央,所述气液分离板固定套设于所述中柱中部且将所述外罩内部分隔为上部的气体腔和下部的液体腔,所述混合气入管与所述气体腔的下部连通,所述干气出管与所述气体腔的顶部连通。
7.所述螺旋冷凝板为垂直螺旋曲面板结构并设置于所述气体腔内,所述螺旋冷凝板与所述中柱同轴设置且两者固定连接,所述气液分离板的一侧设置有气体液封结构,所述气体腔与所述液体腔通过所述气体液封结构连通;
8.所述切油活动块设置于所述液体腔内部,所述切油活动块为中空密封结构且与所述中柱限位上下滑动连接,所述外罩的底部设置有瓦斯油出管,所述切油活动块的底部与所述瓦斯油出管配合形成自动切油结构。
9.优选的,所述气体液封结构包括同轴设置的分液漏斗和液封槽, 所述气液分离板的一侧设置有镂空孔洞,所述分液漏斗设置于所述气液分离板的镂空孔洞处且与所述气液分离板密封固定连接,所述液封槽为碗状结构且内部填充有瓦斯油,所述液封槽的上部边缘位置设置有多个与所述分液漏斗连接的连接柱。
10.优选的,所述切油活动块底部与所述瓦斯油出管对应的位置设置有弹簧杆,所述弹簧杆的底部设置有封堵塞,所述弹簧杆和封堵塞与所述瓦斯油出管配合形成弹性切油结构。
11.优选的,所述螺旋冷凝板上设置有多个漏液孔,所述漏液孔以所述中柱为中心呈
放射状分布。
12.优选的,所述外罩下部的外表面连接有液位表,所述液位表与所述液体腔内部连通,所述外罩底部设置有多个支撑脚。
13.本实用新型与现有技术相比较,具有以下优点:
14.本装置通过自动切油分液罐能够实现自动切油,防止分液罐因瓦斯油积累导致生产线的初馏塔和常压塔运行压力过大,去除了不凝汽中的液体,避免火炬因瓦斯油滴点燃造成事故,提高了安全性和工作效率,降低了运营成本。
附图说明
15.图1为本实用新型的结构示意图;
16.图2为自动切油分液罐结构示意图;
17.图中:1
‑
初馏塔,2
‑
初馏空冷器,3
‑
初馏水冷器,4
‑
常压水冷器,5
‑
常压空冷器,6
‑
常压塔,7
‑
自动切油分液罐,71
‑
外罩,711
‑
支撑脚,712
‑
气体腔,713
‑
液体腔,714
‑
中柱,72
‑
混合气入管,73
‑
干气出管,74
‑
瓦斯油出管,75
‑
螺旋冷凝板,751
‑
漏液孔,76
‑
气液分离板,761
‑
分液漏斗,762
‑
液封槽,77
‑
切油活动块,771
‑
弹簧杆,772
‑
封堵塞,78
‑
液位表,8
‑
回流罐。
具体实施方式
18.以下将以图式揭露本实用新型的多个实施方式,为明确说明起见,许多实务上的细节将在以下叙述中一并说明。然而,应了解到,这些实务上的细节不应用以限制本实用新型。也就是说,在本实用新型的部分实施方式中,这些实务上的细节是非必要的。此外,为简化图式起见,一些习知惯用的结构与组件在图式中将以简单的示意的方式绘示之。
19.实施例一
20.参照图1所示,原料预处理用不凝气干湿分离装置,包括初馏塔1、初馏空冷器2、水冷器、回流罐8、常压空冷器、常压塔6和自动切油分液罐7,以回流罐8为中枢设置有两条进料支线和一条出料线,进料支线一是包含初馏塔1的支线,由初馏塔1、初馏空冷器2和初馏水冷器3依次连接并最终汇入回流罐8,进料支线二是包含常压塔6的一条支线,由常压塔6、常压空冷器和常压水冷器4依次连接并最终汇入回流罐8,流体在回流罐8进行混合并流出注入自动切油分液罐7来进行气液分离从而避免瓦斯油积聚。
21.自动切油分液罐7包括外罩71、中柱714、混合气入管72、干气出管73、瓦斯油出管74、螺旋冷凝板75、气液分离板76和切油活动块77,外罩71为中空罐体结构且中央竖直设置有中柱714,中柱714的中部设置有气液分离板76,
22.外罩71内部由气液分离板76分隔成两个区域,上方的是气体腔712,下方的是液体腔713,中柱714作为气体腔712内螺旋冷凝板75的支撑柱和液体腔713内切油活动块77的滑轨,气体经混合气入管72注入气体腔712,经过冷凝处理气体从气体腔712顶部连接的干气出管73流出, 液体向下穿过气液分离板76流入液体腔713。
23.本装置可以将初馏塔1出来的不凝汽经过冷凝分离,防止分液罐因瓦斯油积累导致生产线的初馏塔和常压塔运行压力过大,同时提纯了不凝汽,去除了不凝汽中的液体,避免火炬因瓦斯油滴点燃造成事故,提高了安全性和工作效率,降低了运营成本。
24.实施例二
25.参照图2所示,与实施例一基本相同,所不同在于,螺旋冷凝板75为垂直螺旋曲面板结构并设置于气体腔712内,螺旋冷凝板75与中柱714同轴设置且两者固定连接,气液分离板76的一侧设置有气体液封结构,气体腔712与液体腔713通过气体液封结构连通,气体液封结构包括同轴设置的分液漏斗761和液封槽762,气液分离板76的一侧设置有镂空孔洞,分液漏斗761设置于气液分离板76的镂空孔洞处且与气液分离板76密封固定连接,液封槽762为碗状结构且内部填充有瓦斯油,液封槽762的上部与分液漏斗761固定连接且两者连接处设置有多道溢流孔隙。
26.混合气体经由混合气入管72注入气体腔712然后在螺旋冷凝板75的冷凝和导向作用下呈螺旋形上升,一边上升一边降温冷凝,然后由气体腔712顶部连接的干气出管73流出,冷凝出的液体经由气液分离板76上气体液封结构的汇集流入液体腔713,气体液封结构由分液漏斗761和液封槽762配合构成,分液漏斗761的下方出口深入液封槽762,液封槽762内填充有瓦斯油,液体向下流动汇入瓦斯油中,当瓦斯油过多则从液封槽762溢出流向液体腔713,而气体被瓦斯油挡住无法向下流入液体腔713,因此完成气体封隔的作用。
27.切油活动块77设置于液体腔713内部,切油活动块77为中空密封结构且与中柱714限位上下滑动连接,外罩71的底部设置有瓦斯油出管74,切油活动块77的底部与瓦斯油出管74配合形成自动切油结构。
28.切油活动块77是活动的浮块,内部中空并填充有密度合适的气体,当瓦斯油积攒到达指定体积时,切油活动块77因为浮力上浮,打开与瓦斯油出管74配合的开关,从而将瓦斯油切出,从而实现自动切油。
29.实施例三
30.参照图2所示,与实施例二基本相同,所不同在于,切油活动块77底部与瓦斯油出管74对应的位置设置有弹簧杆771,弹簧杆771的底部设置有封堵塞772,弹簧杆771和封堵塞772与瓦斯油出管74配合形成弹性切油结构,封堵塞772的设置是为了配合瓦斯油出管74从而形成开关结构,自动控制瓦斯油的流出。
31.螺旋冷凝板75上设置有多个漏液孔751,漏液孔751以中柱714为中心呈放射状分布,漏液孔的设置是为了使螺旋冷凝板75上积聚的瓦斯油尽快滴落,同时,漏液孔751的放射状分布类似于蜂窝状结构,可以有效的吸附不凝汽中的瓦斯油。
32.外罩71下部的外表面连接有液位表78,液位表78与液体腔713内部连通,外罩底部设置有多个支撑脚711,液压表78的设置可以让操作人员及时通过液位表78观察液体腔713内部的储油情况,当发生堵塞时,可以及时处理从而避免发生事故,支撑脚711的设置是避免外罩71与地面直接接触,防止因为外罩71底面发生腐蚀从而使得瓦斯油泄露,提高了安全性。
33.工作原理:
34.1.初馏塔1产生的不凝汽经过初馏空冷器2和初馏水冷器3的冷却注入回流罐8,常压塔6产生的不凝汽经过常压空冷器5和常压水冷器4的冷却注入回流罐8,经过回流罐8的混合注入自动切油分液罐7进行分液处理。
35.2.不凝汽在自动切油分液罐7经过以下流程进行分离,气体从混合气入管72吹入外罩71内部,在气体腔712内螺旋冷凝板75的冷凝下,干气从干气出管73吹出并返回加工回
收流程,液体经过分液漏斗761和液封槽762流入液体腔713,从而完成气液分离的流程。
36.3.当积攒的瓦斯油达到指定限度时,切油活动块77浮起,带动弹簧杆771和封堵塞772,封堵塞772上升并解除对瓦斯油出管74的封堵,瓦斯油从瓦斯油出管74流出,从而完成自动切油的流程。
37.本实用新型并不限于上述的实施方式,在本领域技术人员所具备的知识范围内,还可以在不脱离本实用新型宗旨的前提下做出各种变化,变化后的内容仍属于本实用新型的保护范围。