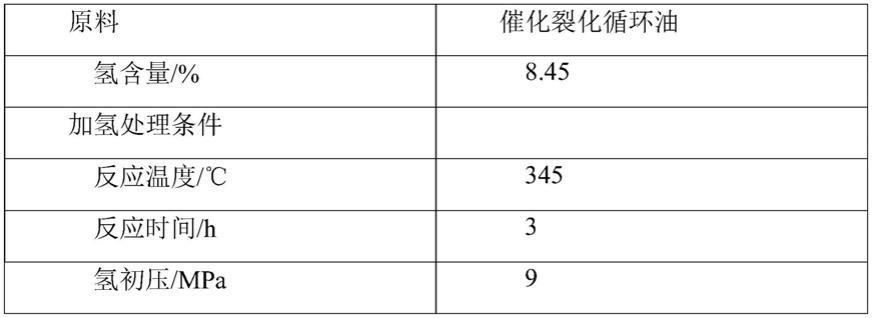
1.本发明涉及一种用于渣油浆态床加氢残渣油的处理方法,以及由此得到的吸附多孔材料的用途。
背景技术:
2.目前,渣油浆态床加氢是劣质渣油加工的有效途径之一,该工艺定位于处理高金属、高残炭、高沥青质含量的劣质重油及超稠原油,采用分散型催化剂,在催化剂添加量为0.1%~3%、反应温度420℃~470℃、反应压力14mpa~20mpa、空速0.07h-1
~0.20h-1
条件下加工劣质重油或超稠原油,可实现原料油转化率达85%~95%。
3.虽然浆态床渣油加氢技术可实现渣油转化率达90%,但仍有5%~10%甚至更多的未转化油,该未转化油为浆态床加氢改质油的减压渣油或脱沥青油,其中含有一定的油分,但亦含有较多的胶质、沥青质、甲苯不溶物以及原料中的重金属和所有的金属催化剂。浆态床渣油加氢催化剂主要有固体粉末催化剂、水溶性催化剂和油溶性催化剂。固体粉末催化剂由于其分散度低、且多采用加氢活性低的含fe矿物,因而其加工量较高(一般为原料的2%~5%),因而其尾油中催化剂含量较高,大于20%。尾油目前作为延迟焦化的原料,但由于其金属含量高,导致延迟焦化石油焦的质量不合格,因而未转化油的后续加工利用较难。
4.也有一些技术采用高加氢活性的mo系催化剂,催化剂添加量较低,,其尾渣中催化剂虽然mo金属含量较低,但由于mo价格昂贵,均采用溶剂溶解、液固旋风分离、滤饼两步热解气化等步骤来回收金属氧化物。该方法虽然可实现金属的回收,具有较好的经济效益,但是该方法步骤多,且两步热解气化能耗较高。
技术实现要素:
5.本发明方法的目的就是通过简单、易行的方法处理浆态床加氢残渣油,脱除残渣油中的金属,使其较容易二次加工处理;同时实现浆态床残渣油中金属变废为宝,作为馏分油加氢处理催化剂。
6.本发明提供一种用于渣油浆态床加氢残渣油的处理方法,该方法包括:
7.使所述渣油浆态床加氢残渣油与溶剂油、多孔材料混合,得到混合物;
8.分离所述混合物,得到吸附多孔材料和混合油;
9.分离所述混合油,得到回收溶剂油和经处理的残渣油。
10.在一种实施方式中,使所述渣油浆态床加氢残渣油与溶剂油、多孔材料在混合温度下混合,其中所述混合温度比所述渣油浆态床加氢残渣油的软化点高50℃~200℃。
11.在一种实施方式中,混合时,所述溶剂油与所述渣油浆态床加氢残渣油的质量比为2:1~10:1,所述多孔材料占2%~10%,基于所述溶剂油与所述渣油浆态床加氢残渣油的总重量。
12.在一种实施方式中,所述混合油中金属含量低于10μg/g,优选低于5μg/g,更优选
低于1μg/g。
13.在一种实施方式中,所述溶剂油是沸点低于524℃的馏分油。
14.在一种实施方式中,所述多孔材料包括介孔材料和大孔材料。
15.在一种实施方式中,所述多孔材料选自高岭土、氧化铝、氧化硅、分子筛、活性炭中的一种或多种。
16.在一种实施方式中,至少一部分所述溶剂油为所述回收溶剂油。
17.在一种实施方式中,所述吸附多孔材料作为馏分油加氢处理催化剂使用。
18.另一方面,本发明提供吸附多孔材料作为馏分油加氢处理催化剂的用途,其中,所述吸附多孔材料如下得到:使所述渣油浆态床加氢残渣油与溶剂油、多孔材料进行混合,得到混合物;分离所述混合物,得到所述吸附多孔材料。
19.本发明提供的处理方法简单、易行,不仅可高选择性地脱除浆态床加氢残渣油中的重金属;而且可实现残渣中加氢金属组元变废为宝,作为加氢催化剂进一步有效利用。同时,将混合油进行蒸馏分离可得到溶剂油,溶剂油可循环回使用,脱除金属的残渣油可作为焦化或加氢处理的原料进一步加工处理。
具体实施方式
20.本发明方法采用多孔材料对渣油浆态床加氢残渣油与溶剂油的混合物进行吸附分离,得到吸附了金属和金属硫化物的多孔材料(吸附多孔材料)以及不含金属的尾油(混合油),吸附了金属和金属硫化物的多孔材料(吸附多孔材料)可以直接作为馏分油加氢处理催化剂;同时本发明方法中溶剂油可循环使用。
21.本发明一方面提供一种用于渣油浆态床加氢残渣油的处理方法,该方法包括:
22.使所述渣油浆态床加氢残渣油与溶剂油、多孔材料混合,得到混合物;
23.分离所述混合物,得到吸附多孔材料和混合油;
24.分离所述混合油,得到回收溶剂油和经处理的残渣油。
25.本发明方法创造性使用溶剂油与多孔材料的组合来对残渣油进行处理,其中,多孔材料可以作为吸附剂来吸附残渣油中存在的金属和金属硫化物,而溶剂油可以起到降低残渣油的粘度、增加其流动性,增加其与多孔材料接触的可能性和增强其传质效果。相比于仅使用多孔材料来处理残渣油的方法,使用溶剂油与多孔材料的组合具有如下优点:1、液体物料的粘度降低、流动性增强,能够强化残渣油与多孔材料的接触;2、多孔材料吸附残渣油中金属及其硫化物的效率及效果都显著提高。
26.在本发明一种实施方式中,使所述渣油浆态床加氢残渣油与溶剂油、多孔材料在混合温度下混合,其中所述混合温度比所述渣油浆态床加氢残渣油的软化点高50℃~200℃。在该混合温度下进行混合,具有如下优点:混合原料的粘度较小、流动性好,残渣油与多孔材料的传质效率高。
27.在一种实施方式中,混合时,所述溶剂油与所述渣油浆态床加氢残渣油的质量比为2:1~10:1,所述多孔材料占2%~10%,基于所述溶剂油与所述渣油浆态床加氢残渣油的总重量。对于本发明方法来说,该溶剂油与多孔材料的用量是重要的。如果溶剂油与渣油浆态床加氢残渣油的质量比低于2:1,则具有混合原料粘度大、流动性差,残渣油与多孔材料的传质效率低的缺点;如果溶剂油与渣油浆态床加氢残渣油的质量比高于10:1,则具有
过程的物耗、能耗高的缺点。如果多孔材料用量低于2%,则具有残渣油中金属及金属硫化物回收率低的缺点;如果多孔材料用量高于10%,则具有多孔材料多导致体系固含量大、操作难度增加;固体含量高,残渣油与多孔材料的传递效率降低,残渣油中金属及金属硫化物回收率低的缺点。
28.在一种实施方式中,溶剂油是沸点低于524℃的馏分油或纯溶剂,其对重油、渣油、浆态床加氢残渣油具有较高溶解性能。可选纯芳烃溶剂,轻、重芳烃混合物,抽余油、催化裂化循环油,催化裂化油浆或催化裂化油浆窄馏分中的一种或多种混合物。在一种实施方式中,多孔材料是具有孔结构的多孔材料,可以选自高岭土、氧化铝、氧化硅、分子筛、活性炭之类的介孔材料和大孔材料。在本技术中,介孔材料是指孔径介于2-50nm的一类多孔材料。大孔材料是指孔径大于50nm的一类多孔材料。
29.在所述渣油浆态床加氢残渣油与溶剂油、多孔材料混合之后,使多孔材料对渣油浆态床加氢残渣油吸附处理一段时间,可以为1-10小时,例如1-5小时。
30.之后,分离渣油浆态床加氢残渣油、溶剂油与多孔材料的混合物,得到吸附多孔材料和混合油。分离方法可以采用过滤分离或者旋风分离来进行。所得到的吸附多孔材料吸附有残渣油中存在的金属和金属硫化物。特别重要的是,该吸附多孔材料可以直接作为馏分油加氢处理催化剂使用,而无需进一步进行加工处理。可实现残渣油中加氢金属组元变废为宝,作为加氢催化剂进一步有效利用。
31.经过吸附处理的溶剂油及尾油的混合物(混合油),其金属(ni+v+fe+mo)含量低于10μg/g,优选低于5μg/g,更优选低于1μg/g。
32.同时,将混合油进行蒸馏分离可得到回收溶剂油,回收溶剂油可循环使用,作为溶剂油的一部分;而脱除金属的残渣油(经处理的残渣油)可作为焦化或加氢处理的原料进一步加工处理。
33.如本发明所证实的,通过本发明方法得到的吸附多孔材料吸附有残渣油中存在的金属和金属硫化物,其可以直接作为馏分油加氢处理催化剂使用,而无需进一步进行加工处理。因此,本发明还涉及该吸附多孔材料作为馏分油加氢处理催化剂的用途。得到该吸附多孔材料的过程可以参见本发明说明书的以上描述,这里不再赘述。
34.相比于仅以多孔材料处理渣油浆态床加氢残渣油得到的吸附有金属和金属硫化物的材料,采用本发明方法得到的吸附多孔材料具有如下优点:1、添加溶剂油,体系粘度减小,可以强化浆态床加氢残渣油与多孔材料的传质,强化残渣油中的金属和金属硫化物向多孔材料的扩散,实现多孔材料吸附浆态床加氢残渣中的金属和金属硫化物;2、可以高选择性地脱出浆态床残渣中的金属mo、ni、v,混合油中金属mo、ni、v含量小于10μg/g,使其作为焦化或加氢处理原料进一步加工处理;3、实现含金属和金属硫化物的多孔材料与残渣油的有效分离,催化剂可用于馏分油加氢的催化剂;4、本发明方法中溶剂油可循环使用,且使用效果不错整个发明方法无固废、液废排放。
35.下面根据具体实施例对本发明的技术方案做进一步说明。本发明的保护范围不限于以下实施例,列举这些实例仅出于示例性目的而不以任何方式限制本发明。
36.在以下实施例中,渣油浆态床加氢外甩残渣油为处理对象。将该残渣油与溶剂油、多孔材料混合,在一定的温度混合、分散,采用旋风分离或过滤分离方法将吸附了金属和/或金属硫化物的吸附多孔材料以及不含金属的溶剂油及尾油的混合物分开。吸附了金属和
金属硫化物的吸附多孔材料作为馏分油加氢处理催化剂;不含金属的混合油经过分离得到的溶剂油可循环使用,脱除了金属的尾油可以作为焦化原料,其生成的石油焦灰分满足要求。
37.实施例1~3给出本发明方法采用多孔材料、溶剂油对渣油浆态床加氢外甩残渣油进行处理的效果。表4是实施例3得到的吸附了金属硫化物的吸附多孔材料催化lco加氢处理的试验结果。
38.实施例1
39.本实施例渣油浆态床加氢外甩残渣油进行处理,其中,表1-1示出渣油浆态床加氢残渣油性质,表1-2示出对该加氢残渣油在溶剂不循环的情况下进行处理的条件和效果。
40.表1-1渣油浆态床加氢残渣油性质
41.性质渣油浆态床加氢残渣油元素 mo/(μg
·
g
–1)2800ni/(μg
·
g
–1)1500v/(μg
·
g
–1)4600物理性质 密度(20℃)/(g
·
cm
–3)1.24动力粘度(160℃)/(cp)8000
42.表1-3加氢残渣油处理(溶剂不循环)条件和效果
43.残渣处理溶剂/%重芳烃混合物溶剂油比残渣比例8:1多孔材料高岭土多孔材料含量/%3残渣处理温度/℃200残渣处理时间/h4含多孔材料固体收率/%9处理后混合油中金属含量/(μg/g) mo<1ni<1v<1
44.残渣油经过溶剂油+多孔材料吸附处理后,得到(包括添加的多孔材料)滤饼固体和液体两部分。含多孔材料固体收率是指包括添加的多孔材料在内的滤饼固体占滤饼固体和液体两部分的质量百分比。
45.实施例2
46.本实施例针对渣油浆态床加氢外甩残渣油进行处理,其中,表2-1示出渣油浆态床加氢残渣油性质,表2-2示出对该加氢残渣油在溶剂不循环的情况下进行处理的条件和效果。
47.表2-1渣油浆态床加氢残渣油性质
48.性质渣油浆态床加氢残渣油元素 mo/(μg
·
g
–1)1400ni/(μg
·
g
–1)750v/(μg
·
g
–1)2300物理性质 密度(20℃)/(g
·
cm
–3)1.17动力粘度(100℃)/(cp)5400
49.表2-2加氢残渣油处理(溶剂不循环)条件和效果
50.残渣处理溶剂/%催化裂化油浆轻馏分溶剂油比残渣比例2:1多孔材料sapo分子筛多孔材料含量/%2残渣处理温度/℃280残渣处理时间/h3含多孔材料固体收率/%8处理后混合油中金属含量/(μg/g) mo<2ni<2v<3
51.实施例3
52.本实施例针对渣油浆态床加氢外甩残渣油进行处理,其中,表3-1示出渣油浆态床加氢残渣油性质,表3-2示出对加氢残渣油在溶剂循环的情况下进行处理的条件和效果。
53.表3-1渣油浆态床加氢残渣油性质
54.性质渣油浆态床加氢残渣油元素 mo/(μg
·
g
–1)2500ni/(μg
·
g
–1)1300v/(μg
·
g
–1)3900物理性质 密度(20℃)/(g
·
cm
–3)1.19动力粘度(100℃)/(cp)3037
55.表3-2加氢残渣油处理(溶剂循环)条件和效果
56.残渣处理溶剂/%催化裂化循环油溶剂油比残渣比例5:1多孔材料y分子筛多孔材料含量/%5残渣处理温度/℃240
残渣处理时间/h5含多孔材料固体收率/%10含溶剂油混合物收率/%90混合物回收溶剂操作条件 操作温度/℃100操作真空度/mmhg500溶剂回收率/%>85回收5次溶剂处理残渣得到循环溶剂中金属含量/(μg/g) mo<3ni<4v<4
57.从表1-1~表3-2的结果可以看出,与现有技术相比,本发明方法具有以下突出特点:
58.(1)本发明方法采用多孔材料、有机溶剂共同处理渣油浆态床加氢残渣,不仅可以高选择性地脱出渣油浆态床残渣中的金属mo、ni、v,混合油中金属mo、ni、v含量小于10μg/g,使其作为焦化或加氢处理原料进一步加工处理;
59.(2)本发明方法相比于现有的回收浆态床残渣中金属的方法简单、易于操作;
60.(3)本发明方法中溶剂油可循环使用,且使用效果不错,整个发明方法无固废、液废排放。
61.对比例
62.由于浆态床加氢尾油粘度大,100℃粘度大于3000cp(厘泊),所以在本发明条件下多孔材料直接加入到浆态床加氢尾油中时,不能有效传质,尾油中的金属和金属硫化物也不能扩散到多孔材料中;而且,在常规过滤分离条件下,也无法实现多孔材料和尾油的分离。
63.实施例4
64.以实施例3所得的吸附多孔材料作为催化剂,来催化lco加氢,条件列于表4。
65.表4实施例3的吸附多孔材料催化lco加氢条件
66.[0067][0068]
实施例4的表4结果显示,吸附了浆态床加氢残渣油中的金属硫化物(moxsy、nixsy、vxsy)的多孔材料催化lco加氢试验,产物的氢含量相比于原料增加了1.05个百分点。数据表明,吸附了金属硫化物的分子筛材料具有催化加氢活性,可实现加氢残渣油中的金属变废为宝、增值利用。
[0069]
本领域技术人员应当注意的是,本发明所描述的实施方式仅仅是示范性的,可在本发明的范围内作出各种其他替换、改变和改进。因而,本发明不限于上述实施方式,而仅由权利要求限定。