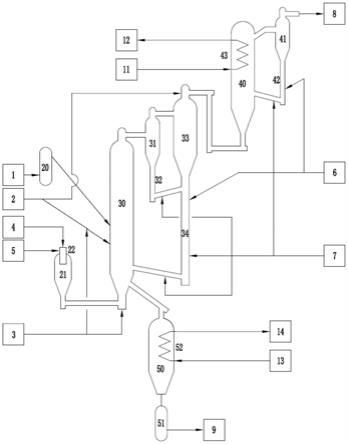
1.本发明属于能源领域,涉及一种生物质气化制合成气的装置及方法。
背景技术:
2.相比于常规化石能源,生物质能资源具有可再生性、低污染性、可替代性、碳中性及储量丰富且开发潜力巨大等优势。特别是在当前碳减排的宏观背景下,由于生物质能资源的综合优势,全球各国都将生物质能源的高效利用作为实现低碳经济、绿色可再生能源体系建设重要且现实的技术路径。常规的生物质气化技术主要包括固定床气化、流化床气化技术等。按床层内生物质物料接触方式分,固定床生物质气化技术又可分为上吸式、下吸式、横吸式、开心式气化炉;流化床生物质气化炉又分为单流化床、双流化床、循环流化床气化等。在固定床生物质气化、流化床生物质气化技术开发的基础上,此外,国内外部分企业及科研单位又相继开展了生物质气流床气化技术的研究及开发工作。专利cn202898353u公开了一种多段式固定床生物质气化炉,该多段式固定床生物质气化炉包括纵向设置的炉体,炉体包括位于底部的锥斗状尾灰段以及位于所述尾灰段之上的至少两个产气段;专利cn102816602a公开了一种新型上吸式生物质气化炉,该生物质气化炉包括设置在炉体一侧的螺旋进料装置、设置在螺旋进料装置上的料斗、炉体、设置在炉体内的炉膛以及分别设置在炉体另一侧的上端和下端的出气管和冷空气进气管;专利cn113105917a公开了一种生物质流化床多级气化炉装置,气化炉内部结构分为下级高温燃烧室,中级高温热解室,上级水蒸气气化室,以生物质为原料生产高热值气化气和高质量生物质炭/活性炭;专利cn112980513a公开了一种恒密度生物质气化炉装置,该气化装置包括炉体和活动炉盖以及自旋转喷嘴,通过装置自旋转喷嘴,使气化剂从中心方向均匀进入反应区,使氧化层、还原层稳定均衡,消除了烧穿现象;专利cn107513434a公开了一种生物质气化炉气化处理设备,包括气化炉、冷却室、加压装置和设置于气化炉下方的鼓风装置,气化炉包括内炉体和外炉体;专利cn111073711a公开了一种低焦油生物质气化方法,利用焦油的低温冷凝特性,将燃气通过换热器和料床,对气化剂和生物质原料进行预热的同时,将焦油冷凝吸附在生物质原料上,可产出气相中焦油含量较低的燃气。
3.虽然有关生物质气化的技术有固定床、流化床、气流床等三种气化方式,但仍存在如下的问题:
4.1)固定床生物质气化技术。生物质原料变化适应性差,合成气中焦油及粉尘含量高,极易发生管路系统焦油冷凝堵塞现象,碳转化率低、装置气化强度低,且由于生物质灰分中碱金属含量高,降低了灰分的熔点,同时气化炉结构设计缺陷,很容易导致炉内熔渣、结渣堵塞而迫使气化系统停车,而且气化炉的进料、排渣系统也极易出现故障。此外,还存在单炉规模小难以大规模工业化应用,且主要以常压空气气化生产燃气为主,装置运行不连续,不能为碳一化工合成提供稳定原料气;
5.2)常规流化床生物质气化技术。气化温度低(通常600~900℃)、碳转化率低且粗合成气中焦油及co2含量较高,合成气中焦油含量最高可达20g/nm3,有效碳利用率低,通常
以大气
‑
固比的常压或低压气化为主,加压气化对常规流化床气化装置的流化稳定性较大影响,易导致回料系统稳定控制较难,容易发生下料架桥、沟流等所导致的返料及下料困难等问题。与固定床类似,由于生物质灰分中碱金属含量高,灰熔点低,在流化床生物质气化炉内局部也易发生局部的熔渣、结渣堵塞、气化炉内耐火材料的碱金属熔盐腐蚀膨胀剥落等问题,从而导致床料流化状态恶化导致沟流、短路等现象,引发气化炉失温、气化反应无法正常进行、出口合成气组分变差、焦油及灰分含量增高,进而无法连续、稳定运行、停车等严重后果;
6.3)气流床生物质气化技术。稳态进料输送较困难,需将生物质粉碎至平均粒径<100μm,而生物质颗粒的可磨性通常较差,因此很难粉碎至100μm以下,且由于微细生物质颗粒的流动性极差,因此很难通过进料喷嘴进入气化炉中。且气化温度通常高于生物质灰熔点,液态排渣,系统显热利用率低,合成气中h2/co较低,很难与合成气制甲醇、乙醇、二甲醚、生物质柴油等液体燃料、化学品合成生产系统耦合,通常采用水洗激冷降温,会产生大量待处理含灰废水,且鉴于生物质原料化学组成及其他物化性能的特殊性,气流床生物质气化技术大多处于实验室小试或中试开发阶段,与煤炭气流床气化技术存在较大的不同。
技术实现要素:
7.针对现有技术存在的不足,本发明目的在于提供一种生物质气化制合成气的装置及方法,基于高倍率循环流化及快速热量分散核心技术,具有生物质原料适应性强、碳转化率高、合成气有效气含量高、进料连续稳定,且可实现连续化、规模化生产。
8.为了实现上述目的,本发明采用以下技术方案:
9.一种生物质气化制合成气的装置,包括加料器、预热器、反应器、一级气
‑
固分离器、二级气
‑
固分离器、合成气冷却器、三级气
‑
固分离器、固渣冷却器和排渣器;
10.所述加料器通过管道连接至反应器底部,反应器顶部通过衬里管道与一级气
‑
固分离器连接,一级气
‑
固分离器顶部通过衬里管道与二级气
‑
固分离器连接,二级气
‑
固分离器顶部通过衬里管道与合成气冷却器底部连接,合成气冷却器顶部通过衬里管道与三级气
‑
固分离器连接;所述预热器通过衬里管道与反应器底部连接;所述固渣冷却器通过衬里管道与反应器底部连接,固渣冷却器底部通过管道与排渣器连接;
11.所述一级气
‑
固分离器底部通过一级料腿与二级料腿连接,二级气
‑
固分离器底部通过二级料腿与反应器底部连接,三级气
‑
固分离器底部通过三级料腿与合成气冷却器连接。
12.进一步,所述预热器顶部设有燃烧器,燃料和空气分别通过管道接入燃烧器。
13.进一步,所述合成气冷却器内部设有蒸汽发生器,锅炉给水从蒸汽发生器底部进入,产生的蒸汽产品从蒸汽发生器顶部排出。
14.进一步,所述固渣冷却器内部设有预热盘管,冷物料从预热盘管底部进入,热物料从预热盘管顶部排出。
15.进一步,所述预热器、反应器、一级气
‑
固分离器、二级气
‑
固分离器、合成气冷却器、三级气
‑
固分离器和固渣冷却器内部均设有耐火材料衬里。
16.一种生物质气化制合成气的方法,包括以下步骤:
17.第一步:向二级料腿和三级料腿注入一定量的惰性颗粒,同时向一级料腿、二级料
腿和三级料腿通入吹扫气;
18.第二步:向燃烧器通入燃料和空气的同时点燃燃料,通过燃烧器将预热器温度控制在1200~1500℃,通过预热器出来的高温烟气逐渐提升反应器温度至500~900℃,同时向蒸汽发生器和预热盘管分别通入锅炉给水和冷物料;
19.第三步:继续逐渐提升反应器温度至900~1100℃时,开启加料器向反应器加入生物质,与此同时向反应器加入氧气和蒸汽;
20.第四步:逐渐降低燃烧器的燃料和空气加入量直至完全关闭燃烧器,同时提高生物质、氧气和蒸汽的加入量,调整反应器温度稳定在1000~1300℃进行正常生产;
21.第五步:通过调整蒸汽发生器的实际负荷控制三级气
‑
固分离器出口的粗合成气温度达到操作指标,并通过固渣冷却器和排渣器逐渐将反应器内经气化反应后固渣排出去。
22.进一步,所述生物质为由秸秆、木屑、椰壳、玉米秆或其他富含有机质的废弃物中的一种或两种以上原料经干燥、成型预处理后所制成的当量粒径<6mm的颗粒物。
23.进一步,所述固渣冷却器将反应器排放的固渣从1000~1300℃降温至200℃。
24.进一步,所述合成气冷却器将气化反应后的高温合成气从1000~1300℃将温至350℃。
25.进一步,所述三级气
‑
固分离器分离出的粗合成气含尘量小于30mg/m3。
26.本发明具有以下有益效果:
27.1)在加压操、高温条件下可实现生物质的高效转化。可实现3.5
‑
4.0mpag、1000~1300℃压力下生物质进料的高效气化,总碳转化率可达99.5%以上,与后续的合成气变换、低温甲醇洗、甲醇合成、费托合成等碳一合成生产系统实现稳态兼容、连接;
28.2)合成气品质高。产品合成气中有效气含量>75%,出气化炉界区合成气中灰含量<30mg/nm3,合成气中无焦油组分,h2/co>1,可为后续的碳一合成生产系统提供稳定、连续的原料气;
29.3)原料适应性广、气化强度高。可以农作物秸秆、农产品加工残余物、林木、有机固废、生活垃圾等作为原料,对生物质的灰分含量、灰熔点、挥发分含量、固定碳含量等无特殊要求,气化炉气化强度>2000kg
·
(m2h)
‑1。
30.4)规模效应明显。基于独有的高倍率循环流化及快速热量分散核心技术,核心气化装置易于实现规模化放大,技术安全可靠,最大生物质处理规模>3000t/d,操作弹性大,比氧耗、比蒸汽消耗低于常规生物质气化技术,装置运行负荷可灵活调节,投资强度及单位合成气生产成本优势明显。
31.5)节能环保竞争性强。出界区合成气中无焦油组分,含尘量较低,无需进行复杂的焦油及灰尘脱除,干法排灰,无需急冷,合成气显热高效干法回收,无难处理的除焦油、激冷、除尘废水产生。
附图说明
32.图1为本发明装置的结构示意图
33.图中:1
‑
生物质;2
‑
氧气;3
‑
蒸汽;4
‑
燃料;5
‑
空气;6
‑
惰性颗粒;7
‑
吹扫气;8
‑
粗合成气;9
‑
固渣;11
‑
锅炉给水;12
‑
蒸汽产品;13
‑
冷物料;14
‑
热物料;20
‑
加料器;21
‑
预热器;
22
‑
燃烧器;30
‑
反应器;31
‑
一级气
‑
固分离器;32
‑
一级料腿;33
‑
二级气
‑
固分离器;34
‑
二级料腿;40
‑
合成气冷却器;41
‑
三级气
‑
固分离器;42
‑
三级料腿;43
‑
蒸汽发生器;50
‑
固渣冷却器;51
‑
排渣器;52
‑
预热盘管。
具体实施方式
34.以下结合实施例对本发明的具体内容做进一步详细解释说明。
35.如图1所示,生物质气化制合成气的装置包括加料器20、预热器21、生物质气化反应炉30、一级气
‑
固分离器31、二级气
‑
固分离器33、合成气冷却器40、三级气
‑
固分离器41、固渣冷却器50和排渣器51。
36.一级气
‑
固分离器31实现粗颗粒与合成气气相物流的初次分离,二级气
‑
固分离器33实现介颗粒与一次净化合成气气相物流的二次分离,三级气
‑
固分离器41实现微纳尺度的微细颗粒与二次净化合成气气相物流的深度分离。
37.加料器20通过管道连接至反应器30底部,反应器30顶部通过衬里管道与一级气
‑
固分离器31连接,一级气
‑
固分离器31顶部通过衬里管道与二级气
‑
固分离器33连接,二级气
‑
固分离器33顶部通过衬里管道与合成气冷却器40底部连接,合成气冷却器40顶部通过衬里管道与三级气
‑
固分离器41连接;所述的反应器30底部还通过衬里管道与预热器21连接;预热器21顶部设有燃烧器22,燃料4和空气5分别通过管道接入燃烧器22。
38.所述的反应器30底部还通过衬里管道与固渣冷却器50连接,固渣冷却器50底部通过管道与排渣器51连接;一级气
‑
固分离器31底部通过一级料腿32与二级料腿34连接,二级气
‑
固分离器33底部通过二级料腿34与反应器30底部连接,三级气
‑
固分离器41底部通过三级料腿42与合成气冷却器40连接。
39.合成气冷却器40内部设有蒸汽发生器43,锅炉给水11从蒸汽发生器43底部进入,产生的蒸汽产品12从顶部排出。
40.固渣冷却器50内部设有预热盘管52,冷物料13从底部进入,热物料14从顶部排出。
41.预热器21、反应器30、一级气
‑
固分离器31、二级气
‑
固分离器三级气
‑
固分离器、合成气冷却器40、三级气
‑
固分离器41和固渣冷却器50内部均设有耐火材料衬里。
42.生物质气化制合成气的方法,包括以下步骤:
43.第一步:向二级料腿34和三级料腿42注入一定量的惰性颗粒6,同时向一级料腿32、二级料腿34和三级料腿42通入吹扫气7;
44.第二步:向燃烧器22通入燃料4和空气5的同时点燃燃料4,通过燃烧器22将预热器21温度控制在1200~1350℃,通过预热器21出来的高温烟气逐渐提升反应器30温度至600℃,与此同时,向蒸汽发生器43和预热盘管52分别通入锅炉给水11和冷物料13。
45.第三步:继续逐渐提升反应器30温度至980℃时,开启加料器20向反应器30加入生物质1,与此同时向反应器30加入氧气2和蒸汽3;
46.第四步:逐渐降低燃烧器22的燃料4和空气5加入量直至完全关闭燃烧器22,同时提高生物质1、氧气2和蒸汽3的加入量,调整反应器30温度稳定在1000℃进行正常生产;
47.第五步:通过调整蒸汽发生器43的实际负荷控制三级气
‑
固分离器41出口的粗合成气8温度达到操作指标,并通过固渣冷却器50和排渣器51逐渐将反应器30内经气化反应后固渣9排出去。
48.生物质1为为由秸秆、木屑、椰壳、玉米秆或其他富含有机质的废弃物(含农林剩余物、生活垃圾、生活污泥、畜禽粪污、果蔬剩余物和工业有机废渣废液等)的一种或两种以上原料经干燥、成型预处理后所制成的当量粒径<6mm的颗粒物。
49.固渣冷却器50将反应器30排放的固渣9从1000℃降低至200℃,排渣器51将200℃的固渣9排放至下游系统,进行进一步的降压或装车运输。
50.合成气冷却器40将气化反应后的高温合成气从1000℃将至350℃,三级气
‑
固分离器41分离出夹带的一部分固体颗粒后排放出含尘量小于30g/m3的粗合成气8。
51.生物质气化制合成气反应原理或者反应过程:
52.焦油蒸汽及二氧化碳重整、催化热裂解反应:
53.c
n
h
m
+nh2o
→
n co+(n+m/2)h254.c
n
h
m
+2nh2o
→
n co2+(2n+m/2)h255.c
n
h
m
→
n co+m/2h256.c
n
h
m
+n co2→
2n co+m/2h257.氧化反应:
58.c+o2→
co259.c+o2→
2co
60.水蒸汽还原反应:
61.c+h2o
→
co+h262.c+2h2o
→
co2+2h263.二氧化碳还原反应:
64.co2+c
→
2co
65.一氧化碳变换反应:
66.co+h2o
→
co+h2。