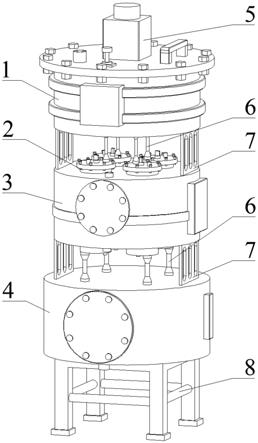
1.本发明涉及催化裂化油浆净化领域,特别是涉及一种催化裂化油浆降粘、脱固一体化装置。
背景技术:
2.催化裂化油浆(fccs)主要是指催化裂化装置主分馏塔塔底没有裂化的烃类化合物。fccs可用作生产炭黑、橡胶填充剂和针状焦原料,但是fccs含有大量固体颗粒,直接加工容易造成生产装置管道堵塞和设备磨损,因此在对fccs利用之前需要进行脱固处理。现对fccs的脱固处理方法主要有重力沉降法、离心法、过滤法、添加沉降助剂和静电分离法等。其中用静电分离法在进行fccs脱固时因具有处理量大、分离效果好、压降小等优点而得到了广泛应用。在静电分离脱固之前通常需要对油浆进行降粘处理,常用加热或加入降粘剂方法,但是该方法通常降粘效果差,影响后续的脱固。因此,亟待开发一种高效降粘、脱固一体化装置,节约装置生产成本,保证高效降粘的同时也要简化静电分离流程,提高生产效率。
技术实现要素:
3.本发明的目的是提供一种催化裂化油浆降粘、脱固一体化装置,可以有效对催化裂化油浆进行降粘、脱固处理。
4.本发明的目的通过以下技术方案来实现:
5.催化裂化油浆降粘、脱固一体化装置,包括超声降粘罐、恒温水浴罐、静电分离罐、储油罐、电机、软管、支撑架、底座;所述超声降粘罐通过左、右两块支撑架固定连接在恒温水浴罐顶端的中间;所述恒温水浴罐内部焊接的4个轴向静电分离罐,端盖的圆心呈正方形排布,侧壁设有观察口和温度控制面板;所述4个轴向静电分离罐顶部的尖嘴管接上软管,软管另一端与超声降粘罐底部的尾嘴管相连;所述静电分离罐底部设有尾管,尾管接上软管与储油罐顶部的4个储油罐尖嘴管相连;所述储油罐顶部通过左、右两块支撑架与恒温水浴罐连接,侧壁设有观察口和液位计,底部靠近侧壁位置设有输油管;所述储油罐底部通过底座固定支撑。
6.所述超声降粘罐包括降粘罐端盖、降粘罐罐体、安装把手、油浆入口管、粘度传感器、粘度控制面板、第一导线安装通道、尾嘴管、涡流喷射管、超声换能器、联动轴、中心轴、搅拌板;所述降粘罐端盖与降粘罐罐体呈法兰连接,端盖上表面设有安装把手和凸台,中心位置设有电机;凸台上设有插入到超声降粘罐内的粘度传感器。
7.所述粘度控制面板传感部分的导线与凸台上的粘度传感器相连,控制部分的导线通过超声降粘罐外侧的两层第一导线安装通道与罐内的超声换能器相连。
8.所述电机通过联动轴与超声降粘罐内部的中心轴相连,进而驱动中心轴上连接的搅拌板对罐内油浆进行搅拌降粘;此外,超声降粘罐内壁均布有两排共12个超声换能器对油浆进行超声降粘;超声降粘罐底部设有4个正方形排布的尾嘴管。
9.所述尾嘴管内设有涡流喷射管,涡流喷射管内部设有螺旋状的涡流发生槽,油浆经过时涡旋运动加剧,能使油浆内的蜡晶产生滑移、扭转,促使晶体断裂,从而起到降粘作用。
10.所述4个尾嘴管通过软管与4个静电分离罐端盖的尖嘴管相连;静电分离罐与超声降粘罐通过左、右两块支撑架连接。
11.所述静电分离罐包括分离罐端盖、尖嘴管、反冲洗入口管、反冲洗出口管、绝缘座、扁头接电片、电极柱、球形玻璃填料、分离罐罐体、尾管、筛孔板、液体分布器、螺旋小孔板;静电分离罐的分离罐端盖设有带控制阀门的尖嘴管和反冲洗出口管,中心位置螺纹连接绝缘座,分离罐端盖与分离罐罐体呈法兰连接;罐底部设有带阀门控制的尾管和反冲洗入口管。
12.所述油浆入口管下端接有液体分布器;以电极柱为圆心,四周均布多块沿静电分离罐底部投影形状为扇环形的螺旋小孔板。
13.所述螺旋小孔板沿静电分离罐底部的投影形状为扇环形,其角度范围为180
‑
270度,螺旋小孔板内、外圆弧均为螺旋线形,板面均布多个圆形小孔;螺旋小孔板焊接在静电分离罐内壁面,其中上下相邻的两块螺旋小孔板错开一定角度;螺旋小孔板之间充满直径小于圆形小孔的球形玻璃填料。
14.所述绝缘座优选陶瓷等绝缘材料制成,上端直径略大,螺纹连接扁头接电片;下端直径略小,螺纹连接电极柱;电极柱与静电分离罐的罐体之间充满直径2
‑
4mm的球形玻璃填料。
15.所述恒温水浴罐包括水浴罐罐体、注水口、出水口、观察口、第二导线安装通道、温度控制器、安装口、加热器、保温层;安装口共4个,呈正方形排布并接有4个静电分离罐,静电分离罐的顶部和底部均高于恒温水浴罐的罐体;恒温水浴罐罐体外侧壁设有法兰连接结构的观察口、温度控制器和导线连接通道;恒温水浴罐内、外侧壁之间为保温层,保温层内放置有隔热石棉等保温材料;恒温水浴罐的罐体内侧壁均布6个加热器,加热器导线依次穿过隔热层、导线安装通道与温度控制器相连;恒温水浴罐罐底接有左、右两块支撑架与储油罐上表面固定连接。
16.所述储油罐包括储油罐罐体、储油罐尖嘴管、封盖、液位计、油浆出口管;储油罐罐体顶部设有4个正方形排布的储油罐尖嘴管,储油罐尖嘴管接上软管并与4个静电分离罐底部的4个尾管相连;储油罐罐体侧壁设有法兰连接的检修口和液位计,检修口通过封盖封闭,储油罐罐体底部与支撑架固定连接并设有带有控制阀门的油浆出口管。
17.本发明具备如下优点:
18.1、本发明的超声降粘罐能实现对油浆进行多重降粘:搅拌降粘和超声降粘,避免了单一降粘的不足,控制器可根据油浆种类和粘度的不同选择开关降粘设备的个数,实现控制降粘、节约生产成本;
19.2、本发明采用4个静电分离罐并联,因此可以适当减小每个分离罐的直径,避免了仅使用单个大直径分离罐而导致的靠近外壁面的分离区域不均匀系数偏小、分离效率低下;
20.3、本发明的静电分离罐不仅易于控制反应温度,而且易于反冲洗和更换填料,简化了设备结构、提高了生产效率;
21.4、本发明的超声降粘罐和静电分离罐管道由控制阀控制开关,能实现油浆的降粘、脱固操作分别进行,互不干扰,提高了生产效率;本发明的油浆降粘和油浆脱固处理分别在不同的区域同时运行并由各自的阀门控制,能实现多批次油浆降粘和脱固的循环操作,且降粘和脱固操作互不干扰:第一批油浆降粘后可立即打开相应阀门排出进行脱固处理;此时开、关相应阀门便可立即进行第二批油浆的降粘处理,第一批油浆脱固结束后打开相应阀门流入到储油罐储存,然后再开关相应阀门进行第二批油浆的脱固处理和第三批油浆的降粘处理,操作弹性大;
22.5、本发明的静电分离罐内部设有螺旋小孔板,静电吸附操作时,部分油浆流经球形玻璃填料之间的缝隙再沿着螺旋小孔板环向逐板向下流动,另一部分油浆流经球形玻璃填料之间的缝隙由螺旋小孔板上的小孔竖直向下流动,这样既延长了油浆在吸附区域的停滞时间,又能实现油浆的多向运动,提高填料内部接触点的吸附效率。
附图说明
23.为了更清楚地说明本发明实施例或现有技术中的技术方案,下面将对实施例或现有技术描述中所需要使用的附图作简单地介绍,显而易见地,下面描述中的附图仅仅是本发明的一些实施例,对于本领域普通技术人员来讲,在不付出创造性劳动的前提下,还可以根据这些附图获得其他的附图。
24.图1为本发明装置的整体结构简图;
25.图2为本发明装置中超声降粘罐整体结构示意图;
26.图3为本发明装置中超声降粘罐内部结构示意图;
27.图4为本发明装置中超声降粘罐尾嘴管结构示意图;
28.图5为本发明装置中静电分离罐整体结构示意图;
29.图6为本发明的静电分离罐剖面视图;
30.图7为本发明的静电分离罐内部构件排列图;
31.图8为本发明装置中的螺旋小孔板正视图和俯视图;
32.图9为本发明装置中的筛孔板结构结构示意图;
33.图10为本发明装置中的绝缘座示意图;
34.图11为本发明装置中的绝缘座剖面图;
35.图12为本发明装置中恒温水浴罐整体结构图;
36.图13为本发明装置中恒温水浴罐剖面图;
37.图14为本发明装置中储油罐结构示意图;
38.图中:1、超声降粘罐,1
‑
1、降粘罐端盖,1
‑
2、降粘罐罐体,1
‑
3、安装把手,1
‑
4、粘度传感器,1
‑
5、油浆入口管,1
‑
6、联动轴,1
‑
7、中心轴,1
‑
8、凸台,1
‑
9、搅拌板,1
‑
10、超声换能器,1
‑
11、第一导线安装通道,1
‑
12、粘度控制面板,1
‑
13、尾嘴管,1
‑
14、涡流喷射管;
39.2、静电分离罐,2
‑
1、分离罐端盖,2
‑
2、分离罐罐体,2
‑
3、反冲洗出口管,2
‑
4、尖嘴管,2
‑
5、绝缘座,2
‑
6、扁头接电片,2
‑
7、电极柱,2
‑
8、球形玻璃填料,2
‑
9、尾管,2
‑
10、反冲洗入口管,2
‑
11、筛孔板,2
‑
12、螺旋小孔板,2
‑
13、液体分布器;
[0040]2‑5‑
1、排气孔,2
‑5‑
2、上螺纹,2
‑5‑
3、下螺纹;
[0041]
3、恒温水浴罐,3
‑
1、注水口,3
‑
2、出水口,3
‑
3、安装口,3
‑
4、加热器,3
‑
5、观察口,
3
‑
6、温度控制器,3
‑
7、第二导线安装通道,3
‑
8、水浴罐罐体,3
‑
9、保温层;
[0042]
4、储油罐,4
‑
1、储油罐罐体,4
‑
2、储油罐尖嘴管,4
‑
3、封盖,4
‑
4、液位计,4
‑
5、油浆出口管;
[0043]
5、电机,6、软管,7、支撑架,8、底座。
具体实施方式
[0044]
通过下述技术方案可以详细的解释本发明,公开本发明的目的旨在保护本发明范围内的一切技术改进。
[0045]
图1为本发明装置的整体结构简图,如图所示,本发明的催化裂化油浆降粘、脱固一体化装置,包括超声降粘罐1、静电分离罐2、恒温水浴罐3和储油罐4,所述恒温水浴罐3通过支撑架7设置在储油罐4上方,所述超声降粘罐1通过支撑架7设置在恒温水浴罐3上方,所述静电分离罐2安装于恒温水浴罐3内部,所述超声降粘罐1与静电分离罐2之间以及所述静电分离罐2与储油罐4之间均通过软管6连通,所述储油罐4通过腿式底座8固定安装。
[0046]
图2为本发明装置中超声降粘罐整体结构示意图,图3为本发明装置中超声降粘罐内部结构示意图,图4为本发明装置中超声降粘罐尾嘴管结构示意图,结合图2
‑
3对本发明的超声降粘罐进一步说明如下:所述超声降粘罐1包括降粘罐罐体1
‑
2,所述降粘罐罐体1
‑
2为筒体结构,其上端面由降粘罐端盖1
‑
1封闭,所述降粘罐端盖1
‑
1上设置有油浆入口管1
‑
5和粘度传感器1
‑
4,所述粘度传感器1
‑
4用于检测超声降粘罐1内部油浆粘度,所述降粘罐罐体1
‑
2的底部设置有多个尾嘴管1
‑
13,所述尾嘴管1
‑
13经由软管6连通静电分离罐2;所述超声降粘罐1内部设置搅拌结构,所述搅拌结构包括中心轴1
‑
7以及圆周阵列式分布在中心轴1
‑
7周围的多个搅拌板1
‑
9,所述中心轴1
‑
7通过联接轴1
‑
6外接电机5,所述电机5设置在降粘罐端盖1
‑
1顶部,其带动中心轴1
‑
7及多个搅拌板1
‑
9转动以对油浆进行搅拌降粘,搅拌过程中,每个搅拌板1
‑
9相对于其中轴线也可以发生转动,以使得搅拌更加均匀。
[0047]
且所述降粘罐罐体1
‑
2上还设置有粘度控制面板1
‑
12,所述粘度控制面板1
‑
12的导线通过超声降粘罐1外壁的两层导线安装通道1
‑
11与超声降粘罐1内壁的两层共12个超声换能器1
‑
10相连,可对比油浆实测粘度值与预设粘度值控制开关超声换能器1
‑
10的个数。
[0048]
所述超声换能器1
‑
10能振动产生声波并通过声波的热作用对油浆起到加热降粘作用,另一方面,声波能以一定频率通过油浆,使油浆内部产生微型的气泡,气泡的压缩溃灭过程很快,能在短时间内释放大量能量,通过空化作用使长链石蜡分子、沥青质分子等大分子碎裂,起到降粘效果。
[0049]
粘度传感器1
‑
4通过凸台1
‑
8安装在降粘罐端盖1
‑
1上,粘度控制面板1
‑
12接收粘度传感器1
‑
4信号,当粘度达到预设值后粘度控制面板1
‑
12会打开超声降粘罐1罐底尾嘴管1
‑
13的控制阀开关,油浆在流入尾嘴管1
‑
13之前会经过尾嘴管1
‑
13前段的涡流喷射管1
‑
14,然后油浆经过尾嘴管1
‑
13相连的软管6流入到静电分离罐2进行静电分离的脱固操作。
[0050]
如图4所示,所述涡流喷射管1
‑
14内部设有螺旋状的涡流发生槽,油浆经过时涡旋运动加剧,能使油浆内的蜡晶产生滑移、扭转,促使晶体断裂,从而起到降粘作用。
[0051]
在进行降粘操作时,用户可根据实际需求通过油浆入口管1
‑
5加入降粘剂,也可在粘度控制面板1
‑
12手动调节超声换能器1
‑
10的开关个数和开启时间及控制尾嘴管1
‑
13的
阀门开关。降粘操作完成后,超声降粘罐1下端尾嘴管1
‑
13的控制阀打开,油浆从尾嘴管1
‑
13下端连接的软管6进入静电分离罐2内,用户可根据油浆种类的不同选择每次分离操作时的油浆注入量,注入完毕后关闭超声降粘罐1尾嘴管1
‑
13的控制阀可继续往超声降粘罐1内加入下一批需要进行降粘操作的油浆。
[0052]
所述静电分离罐2安装于恒温水浴罐3内部,具体的,图12为本发明装置中恒温水浴罐整体结构图,图13为本发明装置中恒温水浴罐剖面图,参见图12和图13,所述恒温水浴罐3中部设置多个圆柱型的安装口3
‑
3,多个静电分离罐2一对一安装在多个安装口3
‑
3内部,以使得每个静电分离罐2周围均为恒温水浴罐3所包裹;恒温水浴罐3的水浴罐罐体3
‑
8上部设置注水口3
‑
1、底部设置出水口3
‑
2,通过注水口3
‑
1向水浴罐罐体3
‑
8内部注入热水以对静电分离罐2恒温水浴,冷却后的水经由出水口3
‑
2排出;所述恒温水浴罐3外侧设有温度控制器3
‑
6,温度控制器3
‑
6的导线通过水浴罐罐体3
‑
8外侧的第二导线安装通道3
‑
7与内壁的六个加热器3
‑
4相连,用户可根据实际需求设置水浴温度及加热器3
‑
4开关个数,进而控制恒温水浴罐3内的4个静电分离罐2的操作温度。
[0053]
优选地,如图13所示,所述恒温水浴罐3的水浴罐罐体3
‑
8采用双层侧壁,最外侧的保温层3
‑
9既是加热器3
‑
4与温度控制器3
‑
6的连接通道,也能起到隔热保温的效果,为提高保温效果,保温层3
‑
9内可填充隔热石棉。
[0054]
优选地,所述恒温水浴罐3外壁面还设有法兰连接结构的观察口3
‑
5,便于用户定期清理罐内水垢。
[0055]
所述静电分离罐2可设置多个,本实施例中,设置了四个,参见图5
‑
11,图5为本发明装置中静电分离罐整体结构示意图,图6为本发明的静电分离罐剖面视图,如图所示,所述静电分离罐2包括筒体式的分离罐罐体2
‑
2,所述分离罐罐体2
‑
2的顶部由分离罐端盖2
‑
1封闭,所述分离罐端盖2
‑
1上设置有反冲洗出口管2
‑
3和尖嘴管2
‑
4,所述分离罐罐体2
‑
2的底部设置有尾管2
‑
9和反冲洗入口管2
‑
10,尖嘴管2
‑
4和尾管2
‑
9用于油浆的注入和流出,所述反冲洗入口管2
‑
10和反冲洗出口管2
‑
3用于向静电分离罐2内注入反冲洗液,以清洗内部组件。
[0056]
参见图6和图7,图7为本发明的静电分离罐内部构件排列图,静电分离罐2内部设置电极柱2
‑
7,电极柱7顶端连接扁头接电片2
‑
8,所述扁头接电片2
‑
8通过分离罐端盖2
‑
1中心位置处的绝缘座2
‑
5穿出所述分离罐端盖2
‑
1,以与外部电源连接;所述分离罐罐体2
‑
2内部的上方设置有液体分布器2
‑
13,用于将经由尖嘴管2
‑
4注入的油浆均匀分散在静电分离罐2内部。
[0057]
所述静电分离罐2内部焊接多块螺旋小孔板2
‑
12,如图8所示,为本发明装置中的螺旋小孔板正视图和俯视图,所述多块螺旋小孔板2
‑
12沿静电分离罐2底部的投影形状为扇环形,其角度优选180至270度,螺旋小孔板2
‑
12的内、外圆弧均为螺旋线形,板面均布多个圆形小孔;多块螺旋小孔板2
‑
12等间距焊接在静电分离罐2内壁面,其中上下相邻的两块螺旋小孔板2
‑
12错开一定角度;板之间充满直径小于圆形小孔的球形玻璃填料2
‑
8,以防止填料直接完全堵塞小孔;电极柱2
‑
7插入到静电分离罐2的内腔且电极柱2
‑
7与多块等间距排列的螺旋小孔板2
‑
12保持同圆心;电极柱2
‑
7浸没在球形玻璃填料2
‑
8中,作为静电分离罐2内径向的高电势位置,而静电分离罐2的端盖2
‑
1及罐体2
‑
2则需接地。
[0058]
静电吸附操作时,部分油浆流经球形玻璃填料2
‑
8之间的缝隙再沿着螺旋小孔板
2
‑
12环向逐板向下流动,另一部分油浆流经球形玻璃填料2
‑
8之间的缝隙由螺旋小孔板2
‑
12上的小孔竖直向下流动,这样既延长了油浆在吸附区域的停滞时间,又能实现油浆的多向运动,从而提高了多个球形玻璃填料2
‑
8的内部接触点的利用率。
[0059]
所述球形玻璃填料2
‑
8优选直径2至4mm,静电分离操作时,球形玻璃填料2
‑
8之间的接触点作为催化剂等固体颗粒的吸附点,为防止球形玻璃填料2
‑
8堵塞管口,静电分离罐2底部的尾管2
‑
9、反冲洗入口管2
‑
10之间分别接入了一块圆形的筛孔板2
‑
11,筛孔板2
‑
11上分布有许多直径小于球形玻璃填料2
‑
8的小孔,保证油浆顺利通过的同时将球形玻璃填料2
‑
8阻挡在静电分离罐2的内腔,图9为本发明装置中的筛孔板结构示意图。
[0060]
图10为本发明装置中的绝缘座示意图,图11为本发明装置中的绝缘座剖面图;如图所示,所述绝缘座2
‑
5,由上部粗直径柱段和下部细直径柱段一体式构成,上部粗直径柱段的外螺纹与分离罐端盖2
‑
1的中心孔螺纹连接,其中部设置有上螺纹2
‑5‑
2,所述上螺纹2
‑5‑
2用于螺纹安装扁头接电片2
‑
6;下部细直径柱段位于分离罐端盖2
‑
1下方,其中部设置有下螺纹2
‑5‑
3,所述下螺纹2
‑5‑
3用于固定安装电极柱2
‑
7,绝缘座2
‑
5与分离罐端盖2
‑
1及电极柱2
‑
7与绝缘座2
‑
5之间均采用螺纹连接,便于用户根据实际需要更换不同直径、不同材料的电极柱2
‑
7。绝缘座2
‑
5采用绝缘材料制成,将电极柱2
‑
7和静电分离罐2罐体2
‑
2和端盖2
‑
1隔开,从而保证油浆脱固时静电分离罐2内腔具有径向的电势差。进一步的,为保证油浆脱固操作时的安全性,绝缘座2
‑
5上设有4个排气孔2
‑5‑
1。
[0061]
所述静电分离罐2在安装时,静电分离罐2的分离罐端盖2
‑
1的上表面和罐底面均高过恒温水浴罐3的上下表面,从而为静电分离罐2的上端盖2
‑
1与罐体之间的螺栓连接留出足够空间。
[0062]
静电分离罐2下方的尾管2
‑
9通过软管6连通储油罐4上方的储油罐尖嘴管4
‑
2,从而使得油浆进入储油罐4内部,如图14所示,为本发明装置中储油罐结构示意图,其包括筒体型的储油罐罐体4
‑
1,储油罐罐体4
‑
1的上方封面上设置有储油罐尖嘴管4
‑
2,用于连接软管6,所述储油罐罐体4
‑
1的下方封面上设置有油浆出口管4
‑
5,用以排出油浆,所述储油罐4侧面还设置有液位计4
‑
4和封盖4
‑
3,所述液位计4
‑
4供维护人员及时获知储油罐4内部油浆存量,所述封盖4
‑
3供检修和清理储油罐内部杂物。
[0063]
在进行静电分离操作之前,静电分离罐2的分离罐端盖2
‑
1的反冲洗出口管2
‑
3和罐底部的尾管2
‑
9、反冲洗入口管2
‑
10控制阀门关闭,静电分离罐2的端盖2
‑
1中心位置设有绝缘座2
‑
5,绝缘座2
‑
5的上螺纹2
‑5‑
2的扁头接电片2
‑
6接入高压直流电并与绝缘座2
‑
5的下螺纹2
‑5‑
3连接的电极柱2
‑
7直接接触。然后可关闭静电分离罐2罐底尾管2
‑
9的控制阀并打开分离罐端盖2
‑
1上的尖嘴管2
‑
4和超声降粘罐1尾嘴管1
‑
13的控制阀,注入降粘之后的油浆并对其进行脱固处理。静电分离操作完成后打开静电分离罐2罐底尾管2
‑
9的控制阀,油浆经过依次流过尾管2
‑
9、软管6进入到储油罐4内。
[0064]
由于球形玻璃填料2
‑
8之间的吸附点达到饱和后吸附能力会急剧减弱,所以根据油浆固含量的不同,每隔2
‑
4h需要排出静电分离罐2内脱固后的油浆并对其进行反冲洗操作。油浆排出时,打开静电分离罐2尾管2
‑
9的控制阀,脱固后的油浆经过尾管2
‑
9及尾管2
‑
9上连接的软管6流入到储油罐4中。反冲洗操作时,关闭静电分离罐2的分离罐端盖2
‑
1的供油浆进入的尖嘴管2
‑
4的控制阀,打开罐底反冲洗入口管2
‑
10和分离罐端盖2
‑
1上的反冲洗出口管2
‑
3的控制阀,从反冲洗入口管2
‑
10往静电分离罐2内腔注入反冲洗液,反冲洗液将
球形玻璃填料2
‑
8之间的固体颗粒冲洗干净并从反冲洗出口管2
‑
3排出。用户可根据油浆初始的固含量确定反冲洗时间,油浆初始的固含量越多,则需要反冲洗的时间越长。
[0065]
反冲洗结束后关闭反冲洗入口管2
‑
10和反冲洗出口管2
‑
3的控制阀,打开超声降粘罐1尾嘴管1
‑
13及静电分离罐2的分离罐端盖2
‑
1的尖嘴管2
‑
4和罐底尾管2
‑
9的控制阀,继续往静电分离罐2注入降粘后的油浆进行脱固处理。
[0066]
优选地,静电分离罐2的尾管2
‑
9和反冲入口管2
‑
10与分离罐罐体2
‑
2之间为螺纹连接,因装置长时间使用而需更换球形玻璃填料2
‑
8时,关闭尾管2
‑
9、尖嘴管2
‑
4、反冲洗入口管2
‑
10及反冲洗出口管2
‑
3的控制阀,旋出尾管2
‑
9和反冲洗入口管2
‑
10,便可排出静电分离罐2内的球形玻璃填料2
‑
8。
[0067]
优选地,超声降粘罐1底部的4个尾嘴管1
‑
13与4个静电分离罐2的尖嘴管2
‑
4之间采用软管6连接,需要更换电极柱2
‑
7或者往静电分离罐2内添加球形玻璃填料2
‑
8时,取下软管6,以便于留出足够空间旋开静电分离罐2的端盖2
‑
1。
[0068]
优选地,4个静电分离罐2底部的尾管2
‑
9与储油罐4的储油罐尖嘴管4
‑
2之间用软管6连接,需要排出静电分离罐2中的球形玻璃填料时可取下软管,便于留出足够空间旋下静电分离罐2底部的尾管2
‑
9和反冲洗入口管2
‑
10。