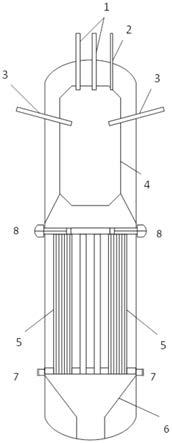
1.本发明属于煤化工技术领域,具体涉及一种多喷嘴带有热量回收装置的气化炉。
背景技术:
2.中国一次能源中,以煤为能源的占比大约在56%,在碳排放达标的大环境下,提升煤化工领域的气化炉能效、碳排放达标意义重大。气化炉技术属于煤化工领域的核心技术。近些年发展的粉煤气化炉相对于水煤浆气化炉具有更高的转换率和煤质适应性,逐渐取代水煤浆气化炉的市场,但仍存在气化物料在炉内停留时间短,难以取得更好的碳转化率,且气化炉产生的高温合成气显热无法有效回收,这些问题没有得到有效解决。
3.专利cn109504445a公开了多喷嘴干粉气化炉,包括壳体、顶置烧嘴、侧置烧嘴、辐射废锅和排渣池,其中,壳体内形成气化室,气化室内设置有水冷壁,壳体的底部收缩形成气化室出渣口;烧嘴包括顶置烧嘴和侧置烧嘴,顶置烧嘴设置在壳体的顶壁上且适于向气化室喷射干粉煤、氧气和蒸汽;侧置烧嘴设置在壳体的侧壁上且适于向气化室喷射干粉煤、氧气和蒸汽。该发明顶部喷嘴集成点火棒,其以顶部进气为主,侧面设置两个或以上喷嘴,通过顶部和侧面喷嘴的碰撞提升混合效果,然而,气化物料进入炉内停留时间比较短、反应不充分,碳转化率仍有待于提高。
技术实现要素:
4.本发明的目的就是为了解决上述问题而提供一种多喷嘴带有热量回收装置的气化炉,通过喷嘴的设置,提升氧化还原反应时间,以提高碳转化率。
5.本发明的目的通过以下技术方案实现:
6.一种多喷嘴带有热量回收装置的气化炉,包括壳体,所述壳体内腔上部设有氧化还原室,所述氧化还原室下部设有热量回收装置;
7.所述壳体的侧面至少设有4个用于通入气化物料的侧面喷嘴,且所述侧面喷嘴呈倾斜状插入所述气化炉壳体,所述壳体的顶端设有通入气体的顶部喷嘴;
8.所述侧面喷嘴以及顶部喷嘴均与所述氧化还原室相连通。
9.粉煤通过管线输送至侧面喷嘴,通过混合适量的氧气和蒸汽,在气化炉上部进行氧化还原反应。
10.反应主要生成含有氢气和一氧化碳的高温合成气,主要的反应如下:
[0011][0012][0013][0014]
c+1/2o2→
co
[0015]
本发明通过侧主喷嘴形成旋涡流提升氧化还原反应时间,侧喷嘴必须要设置4个以上才能形成旋涡流,且侧喷嘴呈略微倾斜插入气化炉,流体通过自行旋转至氧化还原反应室底部延长反应时间增加转化率,顶部辅助烧嘴通入少量气体,通过气量增加起调节侧
主烧嘴形成的旋流时间。
[0016]
氧化还原反应室下方设置热量回收装置,用于回收气化反应后的多余热量,回收高温辐射热。炉内气化物料反应流场特征以侧喷嘴为主,气化物料切圆进入炉内延长了停留及反应时间,提高了气化炉内碳棵粒混(湍)流效果,不仅提高碳转换率,并能够更好的实现在氧化还原反应段的掛渣情况。
[0017]
进一步地,所述的侧面喷嘴设有4个或6个,等间距沿所述壳体的圆周设置。
[0018]
进一步地,所述的侧面喷嘴与所述气化炉炉膛中心成夹角为2~7
°
切圆布置。
[0019]
进一步地,所述顶部喷嘴设置2个,顶部2个辅助喷嘴主要用于调节气化炉负荷。
[0020]
进一步地,所述气化炉从上至下设置膜式水冷壁和辐射屏,所述辐射屏由16~28组换热排管或盘管组成,呈片状或环状布置在靠近膜式水冷壁的内壁中,降低设备造价,保护设备,并减少热量损失。
[0021]
进一步地,所述膜式水冷壁和辐射屏内部为锅炉水,所产生的蒸汽为中、高压,根据工艺需求的不同,副产3.8~10mpa(g)高压蒸汽。
[0022]
进一步地,所述热量回收装置下部设有激冷和除渣装置,合成气通过激冷段完成洗涤,降温的过程,大部分灰渣从激冷段下部排出炉外。
[0023]
进一步地,所述壳体的顶端设有独立的点火烧嘴。
[0024]
进一步地,该气化炉操作压力为3.0~6.9mpa(g),气化温度为1100~1900℃,优选的操作温度为1200~1600℃,碳转化率99%以上。
[0025]
进一步地,进入热量回收装置的合成气温度为1400~1600℃,大部分反应余热在所述热量回收装置内得到回收。
[0026]
cn109504445a的顶部喷嘴集成点火棒,其以顶部进气为主,侧面设置两个或以上喷嘴,通过顶部和侧面喷嘴的碰撞提升混合效果;而本发明主要通过侧主喷嘴形成旋涡流提升氧化还原反应时间,侧喷嘴必须要设置4个或者6个才能形成旋涡流。且侧喷嘴呈略微倾斜插入气化炉,不是通过增大返混及摩擦加强反应,而是流体通过自行旋转至氧化还原反应室底部延长反应时间增加转化率。顶部辅助烧嘴通入少量气体,通过气量增加起调节侧主烧嘴形成的旋流时间。
[0027]
本发明在气化炉侧面设置4个或6个主喷嘴,呈切圆布置,顶部设置2个辅助进料喷嘴,炉内气化物料反应流场特征以侧喷嘴为主,气化物料切圆进入炉内停留时间长、反应充分,能够取得更好的碳转化率。
[0028]
与现有技术相比,本发明具有以下优点:
[0029]
(1)现有技术气化炉的主喷嘴位于顶部,存在停留时间短,反应不够充分的弊端,在负荷改变,煤种改变的情况下无法满足充分的反应时间,造成操作弹性很小。本发明主喷嘴位于气化炉的圆周处,通过产生旋流,增加流体流经路程,能够大大提升反应停留时间,提高气化炉的碳转化率,顶部双喷嘴用于调节负荷,同时通过流速调节可用其改变反应停留时间,极大的增加了气化炉的负荷调整范围及煤种的适应。
[0030]
(2)现有气化技术气化炉主烧嘴集成点火烧嘴,结构复杂,维护成本高,停车成本高;本发明顶部单独设置1个点火、开工烧嘴,简化结构、备件便宜,更换便捷方便,降低造价和提高点火成功率,也可选作长明灯。
[0031]
(3)采用换热降温回收辐射热及激冷组合模式副产中高压蒸汽、降温和除尘,并减
少激冷水用量,大大降低能耗、降低操作费用。符合绿色环保要求。
附图说明
[0032]
图1为本发明一种多喷嘴带有热量回收装置的新型气化炉示意图;
[0033]
图2为侧面喷嘴设置分布图;
[0034]
图中:1
‑
顶部喷嘴;2
‑
点火烧嘴;3
‑
侧面喷嘴;4
‑
氧化还原室;5
‑
热量回收装置;6
‑
激冷和除渣装置;7
‑
锅炉水进口;8
‑
蒸汽出口。
具体实施方式
[0035]
下面结合附图和具体实施例对本发明进行详细说明。
[0036]
如图1,一种多喷嘴带有热量回收装置的气化炉,包括壳体,壳体内腔上部设有氧化还原室4,氧化还原室4下部设有热量回收装置5;壳体的侧面至少设有4个用于通入气化物料的侧面喷嘴3,且侧面喷嘴3呈倾斜状插入气化炉壳体,壳体的顶端设有通入气体的顶部喷嘴1,侧面喷嘴3以及顶部喷嘴1均与氧化还原室4相连通。
[0037]
粉煤通过管线输送至侧面喷嘴3,通过混合适量的氧气和蒸汽,在气化炉上部进行氧化还原反应。本发明通过侧主喷嘴形成旋涡流提升氧化还原反应时间,侧喷嘴必须要设置4个以上才能形成旋涡流,且侧喷嘴呈略微倾斜插入气化炉,流体通过自行旋转至氧化还原反应室底部延长反应时间增加转化率,顶部辅助烧嘴通入少量气体,通过气量增加起调节侧主烧嘴形成的旋流时间。
[0038]
氧化还原反应室下方设置热量回收装置5,用于回收气化反应后的多余热量,回收高温辐射热。炉内气化物料反应流场特征以侧喷嘴为主,气化物料切圆进入炉内延长了停留及反应时间,提高了气化炉内碳棵粒混湍流效果,不仅提高碳转换率,并能够更好的实现在氧化还原反应段的掛渣情况。
[0039]
如图2所示,侧面喷嘴3设有4个或6个,本实施例设有4个,等间距沿壳体的圆周设置,侧面喷嘴3与气化炉炉膛中心成夹角为2~7
°
切圆布置。
[0040]
壳体的顶端设有独立的点火烧嘴2,顶部喷嘴1设置2个,顶部2个辅助喷嘴主要用于调节气化炉负荷。气化炉从上至下设置膜式水冷壁和辐射屏,辐射屏由16~28组换热排管或盘管组成,呈片状或环状布置在靠近膜式水冷壁的内壁中,降低设备造价,保护设备,并减少热量损失。
[0041]
膜式水冷壁和辐射屏内部为锅炉水,热量回收装置的上部设有蒸汽出口8,下部设有锅炉水进口7,所产生的蒸汽为中、高压,根据工艺需求的不同,副产3.8~10mpa(g)高压蒸汽。热量回收装置5下部设有激冷和除渣装置6,合成气通过激冷段完成洗涤,降温的过程,大部分的灰渣从激冷段下部排出炉外。该气化炉操作压力为3.0~6.9mpa(g),气化温度为1100~1900℃,优选的操作温度为1200~1600℃,碳转化率99%以上。进入热量回收装置5的合成气温度为1400~1600℃,大部分反应余热在热量回收装置5内得到回收。
[0042]
以下为两个具体应用示例
[0043]
实施例1
[0044]
原料自上而下分别经过氧化还原反应室,热量回收装置,和激冷排渣装置后生产合成气。气化炉侧面设置4个主喷嘴,顶部设置2个辅助喷嘴,气化炉合成气出口压力
4.1mpag。热量回收段采用24组换热管,副产4.2mpag饱和蒸汽。氧化还原室出口温度1350度,经热量回收后温度为350℃,进入激冷和排渣段。经激冷后产生合成气进入后续工段,底部排渣。
[0045]
实施例2
[0046]
原料自上而下分别经过氧化还原反应室,热量回收装置,和激冷排渣装置后生产合成气。气化炉侧面设置6个主喷嘴,顶部设置2个辅助喷嘴,气化炉合成气出口压力6.8mpag。热量回收段分两组,第一组采用20组换热管,副产9.8mpag过热蒸汽,蒸汽过热度>30℃。第二组副产4.2mpag过热蒸汽,蒸汽过热度>30℃。氧化还原室出口温度1600度,经热量回收装置第一组出口温度为580℃,第二组出口温度为360℃,进入激冷和排渣段。经激冷后产生合成气进入后续工段,底部排渣。
[0047]
上述的对实施例的描述是为便于该技术领域的普通技术人员能理解和使用发明。熟悉本领域技术的人员显然可以容易地对这些实施例做出各种修改,并把在此说明的一般原理应用到其他实施例中而不必经过创造性的劳动。因此,本发明不限于上述实施例,本领域技术人员根据本发明的揭示,不脱离本发明范畴所做出的改进和修改都应该在本发明的保护范围之内。