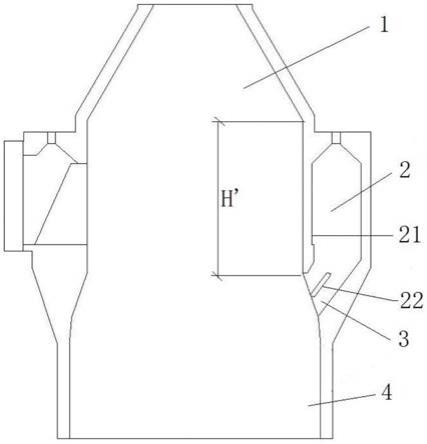
1.本实用新型涉及干熄焦技术领域,尤其涉及一种处理能力为210~230t/h的干熄炉炉体结构。
背景技术:
2.干熄焦是指采用惰性气体将红焦降温冷却的一种熄焦方法,其常用的工艺设备为干熄炉。干熄炉从上而下分别为预存区、环形风道区、斜道区和冷却区,红焦从干熄炉的炉顶装入,低温惰性气体由循环风机鼓入干熄焦冷却区的红焦层内,吸收红焦显热后,途经斜道区和环形风道区后自干熄炉引出,送至锅炉区换热产生蒸汽。
3.干熄焦工艺随着焦炉工艺的发展而不断完善改进,近年来,焦炉炉体结构具有向大型化发展的趋势,已发展出炭化室高度为7m和7.65m的大型顶装焦炉,以及炭化室高度6.25m和6.78m的捣固焦炉;作为与焦炉匹配的设施,干熄焦装置的大型化开发势在必行,干熄炉炉体结构的大型化设计急需实现突破。
4.在干熄炉炉体结构大型化的同时,还应注重干熄炉的长寿化,如采用目前已经较为成熟的分格式斜道技术、斜道区牛腿保护技术、环形风道区内环墙加固技术等,都有利于大型化后的干熄炉炉体结构更加牢固稳定。
技术实现要素:
5.本实用新型提供了一种处理能力为210~230t/h的干熄炉炉体结构,将传统的“高瘦型”炉体结构改进为“矮胖型”炉体结构,通过优化各工作区域的结构,在提高干熄炉处理能力的同时,加强炉体结构的整体强度,保证干熄炉运行稳定,实现节能降耗,满足大容积焦炉的熄焦需求。
6.为了达到上述目的,本实用新型采用以下技术方案实现:
7.一种处理能力为210~230t/h的干熄炉炉体结构,所述干熄炉炉体包括预存区、环形风道区、斜道区及冷却区;其特征在于,所述预存区的高度为7000~9000m;所述环形风道区的内环墙高宽比为2~3;所述冷却区的高径比为0.7~0.9。
8.所述预存区的直段内径为9000~13000mm;所述环形风道区的内环墙厚度为350~600mm,环形风道区的内部通道宽度为1500~2200mm,高度为4000~5200mm;所述冷却区的内径为9500~14000mm。
9.所述斜道区的牛腿数量为24~30个;斜道区设有调节砖或金属调节板。
10.所述干熄炉炉体采用耐火砖或预制块砌筑而成,或者采用浇注料浇铸而成。
11.所述环形风道区的内环墙设有支撑墙结构。
12.所述斜道区由斜道区内墙、牛腿、牛腿环梁及分隔墙组成,所述牛腿沿干熄炉周向均匀分布,将斜道区分隔为多个气道空间;每个气道空间内至少设1层分隔墙,将气道空间分隔为2条以上平行的气流通道。
13.所述气流通道的气体流通截面积自上至下逐渐增大。
14.所述环形风道区的内环墙砌筑时,相邻2层及同层相邻2块砌体之间通过锁扣结构连接。
15.与现有技术相比,本实用新型的有益效果是:
16.1)可满足超大容积焦炉的熄焦需要,解决以往对大型焦炉只能采用两套干熄焦装置来配套的状况,节省建设投资和运行费用。
17.2)实现了超大型干熄焦装置的设计开发,有利于提高焦化行业装备水平,进一步改善环境质量,达到节能减排的目的。
18.3)作为一种大型干熄炉炉体结构,具有强度高、运行稳定的优点,延长了中修、大修间隔时间,在实现干熄炉炉体大型化的同时,实现了长寿化的目的。
附图说明
19.图1是现有干熄炉炉体结构的示意图。
20.图2是本实用新型所述一种处理能力为210~230t/h的干熄炉炉体结构的示意图。
21.图中:1.预存区 2.环形风道区 21.内环墙 22.分隔墙 3.斜道区 4.冷却区
具体实施方式
22.下面结合附图对本实用新型的具体实施方式作进一步说明:
23.如图2所示,本实用新型提供了一种处理能力为210~230t/h的干熄炉炉体结构,所述干熄炉炉体包括预存区1、环形风道区2、斜道区3及冷却区4;所述预存区1的高度为7000~9000mm;所述环形风道区2的内环墙高宽比为2~3;所述冷却区4的高径比为0.7~0.9。
24.所述预存区1的直段内径为9000~13000mm;所述环形风道区2的内环墙21厚度为350~600mm,环形风道区2的内部通道宽度为1500~2200mm,高度为4000~5200mm;所述冷却区4的内径为9500~14000mm。
25.所述斜道区3的牛腿数量为24~30个;斜道区3设有调节砖或金属调节板。
26.所述干熄炉炉体采用耐火砖或预制块砌筑而成,或者采用浇注料浇铸而成。
27.所述环形风道区2的内环墙21设有支撑墙结构。
28.所述斜道区3由斜道区内墙、牛腿、牛腿环梁及分隔墙31组成,所述牛腿沿干熄炉周向均匀分布,将斜道区3分隔为多个气道空间;每个气道空间内至少设1层分隔墙31,将气道空间分隔为2条以上平行的气流通道。
29.所述气流通道的气体流通截面积自上至下逐渐增大。
30.所述环形风道区的内环墙砌筑时,相邻2层及同层相邻2块砌体之间通过锁扣结构连接。
31.本实用新型所述一种处理能力为210
‑
230t/h的干熄炉炉体结构,将传统的“高瘦型”干熄炉炉体结构升级为“矮胖型”炉体结构,主要是对干熄炉的预存区1、环形风道区2、斜道区3及冷却区4的尺寸及各部比例进行了优化。
32.本实用新型通过改进干熄炉各工作区域的结构,在提高处理能力的同时,增加了整体强度,达到了运行稳定、节能降耗的目的,其主要原理如下:
33.①
降低预存区直段高度(如图1、图2所示,h'<h),缩短焦炭在干熄炉预存区的停
留时间,减少焦炭产品烧损;
34.②
降低环形风道区的内环墙高宽比,组成环形风道区内环墙的砌体之间具有相互锁紧的连接结构,防止内环墙“鼓肚”倒塌;
35.③
斜道区部位采用分层结构(详见公开号为cn210595920u的中国实用新型专利公开的“一种新型干熄炉斜道结构”,及公开号为cn210595919u的中国实用新型专利公开的“一种两分格式斜气道”),以降低循环气体流速,减少浮焦,增加牛腿强度;
36.④
降低冷却区的高径比,配合循环气体导入装置,在充分换热的条件下优化冷却气料比,降低能耗。
37.所述环形风道区内可以不设支撑墙,也可以根据需要设置支撑墙,以增加环形风道区内环墙的强度,防止其倒塌。
38.以下实施例在以本实用新型技术方案为前提下进行实施,给出了详细的实施方式和具体的操作过程,但本实用新型的保护范围不限于下述的实施例。下述实施例中所用方法如无特别说明均为常规方法。
39.【实施例】
40.本实施例中,干熄炉炉体包括预存区、环形风道区、斜道区及冷却区;其中:
41.1、预存区的直段内径为10200mm,高度为7980mm。
42.2、环形风道区的内环墙厚度为450mm;内部通道的宽度为1900mm,内部通道的高度为4680mm,高宽比为2.5;
43.3、斜道区的牛腿数量为26个,斜道区的气道空间内设有一层分隔墙,将气道空间分隔为2条平行的气流通道,且上部气流通道的截面积小于下部气流通道的截面积;斜道区设有调节砖;
44.4、冷却区的内径为12000mm,高径比为0.8;
45.本实施例中,干熄炉炉体采用耐火砖砌筑而成。
46.本实施例中,干熄炉的处理能力为220t/h,投产后运行稳定。
47.以上所述,仅为本实用新型较佳的具体实施方式,但本实用新型的保护范围并不局限于此,任何熟悉本技术领域的技术人员在本实用新型揭露的技术范围内,根据本实用新型的技术方案及其实用新型构思加以等同替换或改变,都应涵盖在本实用新型的保护范围之内。