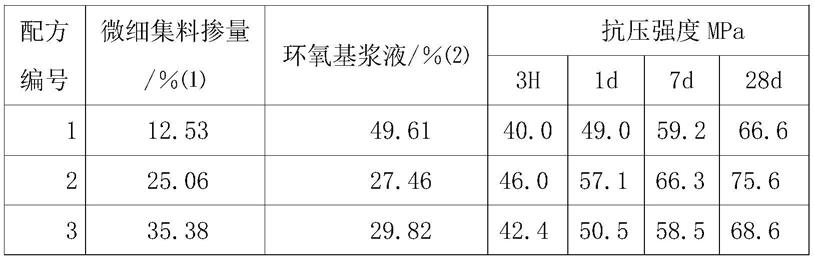
1.本发明涉及公路建设施工技术领域,特别是涉及一种新型水泥路面错台修复方法。
背景技术:
2.水泥路面由于其强度高、稳定性好、无车辙、耐久性好、造价适中、夜间行车可视性好等诸多优点.受到各国道路部门的重视。
3.然而,水泥路面也有一些急需改进的问题。
4.水泥路面在车辆碾压下,往往会出现路面变形,表现为断角、塌落、错台、裂缝、啃边等病害形式,特别是错台病害,是养护部门亟待解决而没有很好解决方案的路面病害之一。现有水泥路面错台修复时根据不同路况采用不同的处理工艺,如果是地基下沉造成的错台,采用压浆法处理;如果由于温差变化,造成水泥砼体积产生缩、涨,导致水泥路面面板的翘曲和拱起等诸多因数致使局部地基不均匀下沉,产生的错台,根据错位程度采用磨平或填补法处理。磨平法即先用人工将高处的错台板基本凿平,再用磨平机磨平,并清缝灌入填缝料。填补法即先在修复表面凿除20至30mm的填补空间,采用沥青砂或水泥混凝土进行错位填补。但这些工艺随着人工成本的逐年提高,修复成本已越来越难以被接受,况且细石子水泥砼或高聚物砂浆与原路面的连接亦不理想;当采用细粒式沥青砼处置时,厚度小于20mm的沥青砼根本承载不了行车重载的冲击,很快就会松散、脱落。
5.因此,亟需一种全新的错台处理新工艺,能够极大的满足水泥砼路面错台养护需求。
技术实现要素:
6.基于此,本发明的目的在于提供一种新型水泥路面错台修复方法,解决现有水泥路面错台修复成本高、连接强度不足,承受行车重载后易松散、脱落的问题。
7.为了达到上述目的,本发明采用这样的技术方案:
8.一种新型水泥路面错台修复方法,至少包括以下步骤:
9.s1:预处理,对待修复错台路面进行平整处理;
10.s2:清洁处理,对待施工区域进行粉尘、杂质、污渍的清理;
11.s3:构设施工区域,根据路面错台程度制定施工坡度及施工面积,在施工区域界限处粘贴胶带,并在错台面及两侧固设隔离板;
12.s4:透层油配制,所述透层油由脂肪醇聚氧乙烯醚(aeo)和环氧基错台修复剂混合搅拌制成;
13.s5:涂刷透层油,将所述透层油均匀涂满施工区域;
14.s6:错台修补材料配制,错台修补材料采用错台修补环氧砼;
15.s7:涂抹错台修补材料,待s5步骤中涂刷的所述透层油干透后,对施工区域涂抹所述错台修补环氧砼;
16.s8:铺设防滑材料,在s7步骤完成后的所述错台修补环氧砼表面均匀铺撒防滑材料;
17.s9:回收防滑材料,待所述错台修补环氧砼初凝后,对于未与所述错台修补环氧砼固定连接的所述防滑材料进行回收,回收后即可开放交通;
18.其中,所述错台修补环氧砼至少由所述环氧基错台修复剂、大颗粒石英砂、中颗粒石英砂、细颗粒石英砂和调色矿粉组成;所述环氧基错台修复剂至少包括环氧树脂、丁晴橡胶、聚氨酯、氧化镁、氧化铝、偶联剂、固化剂、特种稀释剂、调色矿粉。
19.优选的,所述错台修补环氧砼至少由环氧基错台修复剂、大颗粒石英砂、中颗粒石英砂、细颗粒石英砂、调色矿粉按质量份比24:14.5:27:12.4:9.5混合制成。
20.优选的,所述环氧基错台修复剂至少由环氧树脂、丁晴橡胶、聚氨酯、氧化镁、氧化铝、偶联剂、固化剂、特种稀释剂、调色矿粉按质量份比15:15:13:4:10:10:8:7:0.5混合制成。
21.优选的,所述大颗粒石英砂的规格为20目~40目;所述中颗粒石英砂的规格为70目~120目;所述细颗粒石英砂的规格为大于200目。
22.优选的,所述特种稀释剂采用环氧活性稀释剂。
23.优选的,所述环氧活性稀释剂为2,5-呋喃二甲醇(c6h8o3)。
24.优选的,所述透层油由脂肪醇聚氧乙烯醚(aeo)和环氧基错台修复剂按质量份比3:1混合搅拌制成。
25.优选的,所述防滑材料采用1mm~3mm防滑陶瓷颗粒。
26.优选的,所述隔离板采用3mm~10mm的kt板。
27.有益效果
28.相较于现有技术,本发明至少包括以下优点:
29.材料方面:
30.本发明通过采用新型错台修补环氧砼作为错台修补材料,其通过环氧基错台修复剂、石英砂和调色矿粉按一定质量比混合制成,其中环氧基错台修复剂由环氧树脂、丁晴橡胶、聚氨酯、氧化镁、氧化铝、偶联剂、固化剂、特种稀释剂、调色矿粉组成,这种材料与水泥砼路面粘结性能好,在载荷冲击下不易脱落;有足够的强度和韧性,在载荷的冲击下不松散;热胀冷缩的升缩性与水泥砼路面相似,在环境气温变化时不产生裂纹;
31.本发明采用新型透层油进行作业,透层油中的脂肪醇聚氧乙烯醚能和混凝土中的钙、镁离子起化学反应成抗磨、防尘的致密实体,在使用合适的情况下,有助于混凝土变得耐磨和抗化学渗透,通过深入渗透到混凝土内,最大渗透深度可达1mm左右,使反应后的残留物形成硅酸凝体有效填补混凝土毛细成为一个个致密的实体,从而阻止污染物,油脂以及湿气的渗透,长久的避免了混凝土灰尘从表面空隙中析出,同时,透层油中含有环氧基错台修复剂,与环氧基错台修复材料有良好的亲和性,能很好的增加环氧基错台修复材料与水泥路面的联结。
32.施工工艺方面:
33.本发明还公开了一种利用新型错台修补环氧砼的水泥路面错台修复方法,让错台修复工艺操作便捷,劳动强度低,有助于降低人工成本,修复时间短,充分满足水泥路面的养护需求;
34.本发明中隔离板的设置也是现有错台修复工艺所没有的,现有错台修复工艺在错台处理凝固后,错台两侧板块在温度变化时会产生热胀冷缩,导致错台材料与错台高的面板侧面拉裂;另一方面,因为错台处伸缩缝里的填缝材料为柔性材料,在车载载荷冲击下,容易造成错台修复面塌陷;虽然有些施工先将伸缩缝里的填缝材料清理干净,把错台修复材料填满伸缩缝,这样错台修复面塌陷的问题解决了,但伸缩缝的功能也减弱了,本发明中隔离板的设置能够合理解决上述难题;
35.本发明中采用防滑陶瓷颗粒来改善修复面外观,现行的错台修复工艺,防滑处理使用的是级配碎石,和水泥路面会产生色差,修复面会产生麻麻点点的感觉,本发明中采用防滑陶瓷颗粒,可以将陶瓷颗粒烧制得和水泥路面色差相似,使错台修复面和原路面有整体的感觉,有助于提高修复面的美观性。
附图说明
36.图1为140℃下制备工艺对剪切强度影响的折线图。
37.图2为160℃下制备工艺对剪切强度影响的折线图。
38.图3为180℃下制备工艺对剪切强度影响的折线图。
39.图4为200℃下制备工艺对剪切强度影响的折线图。
40.图5为聚氨酯添加量对抗压强度影响的折线图。
41.图6为聚氨酯添加量对拉伸强度影响的折线图。
42.图7为氨酯添加量对断裂伸长率影响的折线图。
具体实施方式
43.为使本发明的目的、技术方案和优点更加清楚,下面结合附图及具体实施方式做详细的说明。在下面的描述中阐述了很多具体细节以便于充分理解本发明。但是本发明能够以很多不同于在此描述的其他方式来实施,本领域技术人员可以在不违背本发明内涵的情况下做类似改进,因此本发明不受下面公开的具体实施的限制。
44.除非另有定义,本文所使用的所有的技术和科学术语与属于本发明的技术领域的技术人员通常理解的含义相同。本文中在本发明的说明书中所使用的术语只是为了描述具体的实施例的目的,不是旨在于限制本发明。本文中所使用的术语“及/或”包括一个或多个相关的所列项目的任意的和所有的组合。
45.本发明公开的一种错台修补环氧砼,由环氧基错台修复剂、大颗粒石英砂、中颗粒石英砂、细颗粒石英砂、灰色调色矿粉按质量份比24:14.5:27:12.4:9.5混合制成。
46.其中,所述大颗粒石英砂、中颗粒石英砂和细颗粒石英砂作为惰性材料,与环氧基错台修复剂不发生化学反应,因此作为填料补充,主要起到降低环氧基错台修复剂用量,降低成本的作用。
47.具体的,所述大颗粒石英砂的规格为20目~40目,sio2含量>98%,颜色为带红色或无色半透明状,莫氏硬度>5,相对密度:2.65,不溶于酸。
48.所述中颗粒石英砂的规格为70目~120目,sio2含量>98%,颜色为带红色或无色半透明状,莫氏硬度>5,相对密度:2.65,不溶于酸。
49.所述细颗粒石英砂的规格为大于200目,sio2含量>98%,颜色为带红色或无色半
透明状,不溶于酸。
50.其中,灰色调色矿粉的规格为200目或以上,主要作为微细集料使用,起到调色作用。
51.通过试验得到各原材料的密度与堆积密度,首先用石英砂的堆积密度计算出所需的石英砂用量,再用砂的表观密度与堆积密度之间的差值计算石英砂堆积之后剩余的空隙,然后采用相同的方法计算微细集料的用量以及环氧基浆液的用量,按此计算后得到单位体积中,当微细集料掺量(与环氧基错台修复材料的质量比)为25.06%时达到最紧密堆积状态。当微细集料的掺量小于该值时,环氧基错台修复材料中未被填满的部分仍需要用环氧基浆液将其填满;而微细集料的掺量大于该值时,则过多的微细集料仍需环氧基浆液将其进行包裹。在本试验条件下,根据最紧密堆积的原则,微细集料的掺量为25.06%时环氧基浆液的用量最少。
52.为了研究微细集料掺量对试样强度的影响,设计了3组试样,浆液的用量按石英砂和微细集料填充后剩余的体积计算。试验结果如表1所示。
53.表1微细集料掺量对试样抗压强度的影响
[0054][0055]
注:
⑴
微细集料与环氧基错台修复材料的质量百分比;
[0056]
⑵
浆液与环氧基错台修复材料的质量百分比;
[0057]
从表1中表格内容可见,配方2即微细集料的掺量为25.06%时试样的抗压强度最大,即当环氧基错台修复材料中的集料为最紧密堆积状态时,环氧基错台修复材料的抗压强度达到最大;配方1的微细集料掺量为12.53%,所用的微细集料未能完全填充砂堆积后剩余的空隙,因此未填完的空隙需要环氧基浆液来填充,整个环氧基错台修复材料所需的环氧基浆液用量为配方2的1.8倍左右,而且浆量足够把石英砂和微细集料充分分散,因而试样的抗压强度主要取决于环氧基浆液硬化后的强度,试样的强度不如配方2的高;微细集料掺量为35.38%时,环氧基错台修复材料中微细集料的用量过多,成型时浆液略有不足,浆液不能将所有的石英砂和微细集料包裹起来,使石英砂和微细集料无法和浆液良好粘结,导致试样的强度也不如配方2的高。
[0058]
从成本来说,添加的微细集料的用量越多则砂浆的成本也越低,因而配方2的成本要比配方1的低,但在实际使用中微细集料的用量有一个最大的限度,即上面计算的最紧密堆积所用的量,微细集料的用量超过了最紧密堆积的用量后,多出的微细集料需要更多的环氧基浆液来包裹,才能得到和易性较好的环氧基错台修复材料,反而使环氧基错台修复材料的成本增大。
[0059]
由于环氧树脂黏度大,环氧基浆液用量较少使得砂浆很难搅拌均匀,因而适当提高浆液用量可以使砂浆的流动性能得到改善,但浆液用量增多提高了环氧基错台修复材料
的成本,也影响环氧基错台修复材料的强度,我们对这方面进行一定的探讨,试验结果见表2。
[0060]
表5浆液用量对试样抗压强度的影响
[0061][0062]
注:(1)浆液用量为浆液填充的比例;
[0063]
(2)试样的集料与微细集料的用量均是最紧密堆积状态下的用量。
[0064]
从表2可见,1d、7d和28d时3个时段的试样强度基本接近,仅在早期(2h)时强度差异比较明显,环氧树脂浆液的用量越多早期强度越低。这是因为在浆液填充完空隙的情况下,随着浆液用量的增多,砂和微细集料在浆液中剥离的距离就越大,那么浆液的硬化强度对砂浆试样的早期强度影响越大,而且当骨料之间的距离足够大时,砂浆试样的强度主要取决于浆液的硬化强度。由于浆液的早期强度并不如骨料的高,因而随着浆液用量的增多,环氧树脂基修补材料的抗压强度反而下降,随着龄期的增长,浆液的强度随反应程度的加大而提高,到后期试样的强度基本接近。
[0065]
经过计算和试验,我们本实施例中错台修补环氧砼的配比。
[0066]
进一步的,本实施例中的所述环氧基错台修复剂由环氧树脂、丁晴橡胶、聚氨酯、氧化镁、氧化铝、偶联剂、固化剂、特种稀释剂、灰色调色矿粉按质量份比15:15:13:4:10:10:8:7:0.5混合制成。
[0067]
其中,聚合物环氧树脂一般含有两个以上环氧基团。常温下将固化剂按比例掺入环氧树脂,会交联形成三维网状结构,因而强度好、粘结性能优异,但交联固化后环氧树脂质脆、易疲劳、耐热性不佳、抗冲击韧性差,因而无法在工程领域推广使用。为此,我们借鉴环氧树脂的相关研究成果,对环氧树脂进行改性,在充分保持环氧树脂强度好、粘结性能优异的同时,提高交联固化后环氧树脂耐疲劳、耐热、抗冲击韧性性能,使之适应工程领域的使用要求。
[0068]
其中,偶联剂选用kh-550;固化剂选用有机胺类固化剂t-31;特种稀释剂选用环氧活性稀释剂(c6h
803
)。
[0069]
其中,端羧基液体丁腈橡胶(ctbn)在高温及催化剂的存在下,都能与环氧基反应,把橡胶柔性链段引入环氧树脂交联结构中,起到增韧作用。在固化过程中形成环氧树脂为连续相,丁腈橡胶为粒子状分散相的两相体系,即所谓的“海岛”式两相结构,获得显著的增韧效果。
[0070]
聚氨酯塑料的主要缺点是在长期高温、高湿下易水解,但是它和环氧树脂交联后就克服了这一缺点。利用聚氨酯改性环氧树脂主要是为了改善其脆性、提高其柔韧性、增加剥离强度。聚氨酯改性环氧树脂反应所得的固化产物具有弹性好,耐冲击、耐热、耐冷热交变等,从而改善环氧树脂胶粘剂的剥离强度低、嵌件易开裂的缺点。
[0071]
聚氨酯中的氨基可以与环氧树脂中的环氧基发生开环反应,异氰酸酯基团可以和环氧树脂中的羟基或开环反应生成的羟基发生反应,而使环氧树脂固化。由于把聚氨酯中醚键引进到环氧树脂交联网络中,所以固化物的韧性较好。聚氨酯增韧剂具有如下优点:1、低温下仍然保持高强度。耐寒可达-196℃;2、可按需要调节加入比例,能获得从坚韧到弹性体不同性能的聚合物,这是环氧树脂很难达到的。改变所用多羧基化合物和二异氰酸酯的种类、配比,可以得到不同程度的弹性体,有的伸长率可达600%以上,能适应水泥路面缝的变形;3、增韧容易,可在较宽的比例范围内与环氧树脂配合;4、耐化学介质性能与环氧树脂相似,耐酸、耐碱。
[0072]
因此,聚氨酯是环氧树脂增韧改性的良好材料。
[0073]
对所述环氧基错台修复剂的制备进行试验,具体如下:
[0074]
1、a组分制备:在烧杯中按配比称取100g环氧树脂(e-44、e-51复配)和增韧剂ctbn加热到设定温度,恒温一定时间。再加入适量聚氨酯,氧化镁、氧化铝(用量为环氧树脂和增韧剂总质量的1%),搅拌,加入偶联剂kh-550(用量为环氧树脂和增韧剂总质量的1%)。
[0075]
2、b组分制备:计算并称取20g的t-31固化剂,加入促进剂(用量为固化剂质量的1%),12g特种稀释剂,搅匀即得。
[0076]
3、a、b组分混匀,固化得到增韧改性的环氧树脂弹性填料。
[0077]
关于丁晴橡胶增韧改性制备工艺对剪切强度的影响试验,固定环氧树脂100g、固化剂20g,仅添加ctbn进行增韧改性,考察ctbn的添加量、反应温度、反应时间对增韧效果的影响,增韧效果,以固化产物的剪切强度为指标,如表3所示,通过正交试验确定最佳的工艺条件。
[0078]
表3试验考察因素
[0079]
序号ctbn/%温度/℃时间/h151401.52101602.03151802.54202003.0
[0080]
图1至图4,中分别为反应温度140℃、160℃、180℃、200℃时,a组分反应时间对试样剪切强度的影响曲线,丁晴橡胶的质量占环氧树脂质量的5%、10%、15%、20%。从四个图整体来看,固化产物的剪切强度是随着环氧树脂中ctbn的质量增大而增大。在环氧树脂体系中,随着ctbn用量的增加,体系中橡胶颗粒的体积分数就加大,剪切强度相应提高。所以环氧树脂与丁晴橡胶的质量分数为5%时,其固化产物的剪切强度较小;而在温度较低,环氧树脂中丁晴橡胶的添加量为20%时,环氧基体中所溶解丁晴橡胶的量增多,而与环氧基反应的比例不大,导致基体软化,因而所得固化产物的剪切强度较低;所以环氧树脂与丁晴橡胶的比例为15%时,所得的结构胶的剪切强度较大。在环氧体系中,随着丁晴橡胶用量的增加,体系中橡胶颗粒的体积分数就加大,剪切强度相应提高;但温度较高时,环氧基体中丁晴橡胶含量过高,会导致丁晴橡胶中端羧基与环氧树脂中环氧基反应过甚,而使甲组分中的橡胶颗粒聚集,呈现出相不确定的情况,使其与b组分固化不充分,所以其固化产物的剪切强度较低。因此,在180℃、200℃时,环氧树脂中丁晴橡胶的添加量为15%。
[0081]
综合以上图,可以看出,环氧树脂与丁晴橡胶反应在180℃及200℃下所得结构胶
的剪切强度较大,这是因为用丁晴橡胶增韧环氧树脂时,丁晴橡胶应先在环氧树脂中溶解,形成均相溶液,此过程吸热,所以较高温度时,丁晴橡胶能更好的溶解在环氧基体中,且丁晴橡胶中端羧基与环氧树脂中环氧基反应较为良好。
[0082]
环氧树脂与丁晴橡胶反应2.5h所得的胶粘剂的剪切强度较大,这是因为随着反应进行到一定程度,体系就会出现相分离,即丁晴橡胶粒子作为分散相而从连续相环氧基体中分离出来,由于析出的橡胶颗粒与环氧树脂间能进行良好的化学键合,故剪切强度提高。然而随着反应时间的继续延长,会导致丁晴橡胶中端羧基与环氧树脂中环氧基反应过甚,而使甲组分中产生交联,使其与乙组分固化不充分,所以其固化产物的剪切强度较低。
[0083]
因此,选择丁晴橡胶增韧改性环氧树脂的最佳工艺条件为添加量为15%,改性温度180℃,改性时间为2.5h,剪切强度相比空白样提高了36%。
[0084]
对丁晴橡胶、聚氨酯增韧剂比例确定的试验。环氧树脂由于其结构的特点,固化物的脆性较大。针对环氧树脂这个缺点,本实验以双酚环氧树脂、固化剂体系为基础,研究端竣基液体丁腈橡胶、聚氨酯对环氧树脂增韧效果的不同,寻找两者之间的最佳匹配,达到既有好的增韧效果,又不影响力学强度的目的。
[0085]
表3实验配方
[0086]
序号环氧树脂/g固化剂/g丁晴橡胶/g聚氨酯树脂/g110020150210020152310020154410020156510020158
[0087]
图5至图7是添加不同量聚氨酯改性剂时对材料抗压强度、拉伸强度、断裂伸长率的影响。随着添加量的增加,断裂伸长率、抗压强度逐渐增大,拉伸强度在添加量大于4g后,强度稍微下降,聚氨酯量添加过大会影响材料的耐热性,因此,添加聚氨酯改性最佳量在4~6g。
[0088]
聚氨酯增韧剂对环氧树脂的增韧效果明显。聚氨酯中氨基与环氧树脂中的环氧基发生开环反应,异氰酸酯基团和环氧树脂中的羟基或开环反应生成的羟基发生反应,把聚氨酯中醚键引进到原环氧树脂交联网络中,生成了弹性固化物,增强了浆材的韧性。随着聚氨酯加入量的增加,抗压、抗拉、抗折强度有不同程度的下降,断裂伸长率随之增大。需要选择适宜的加入量,以同时满足各项力学性能的要求。当聚氨酯的加入量达到20g时,约为环氧树脂量(a组分)的20%时,抗压强度为67mpa,抗拉强度为22.4mpa,抗折粘结强度大于8.4mpa(高于砂浆本体的粘结强度),断裂伸长率达到23%,各项物理力学指标完全满足规范要求,达到配制高韧性环氧基水泥路面错台修补材料的试验目的,是较为理想的高韧性环氧基水泥路面修复材料。
[0089]
本发明公开的一种利用上述错台修补环氧砼的新型水泥路面错台修复方法,包括以下步骤:
[0090]
s1:预处理,对待修复错台路面进行平整处理,清除坑槽、裂缝、污染等病害;
[0091]
s2:清洁处理,采用强力吸尘器或强力风机对待施工区域进行粉尘、杂质的清理或利用清洗剂对污渍进行清除;
[0092]
s3:构设施工区域,根据路面错台程度制定施工坡度及施工面积,在施工区域界限处粘贴胶带,并在错台面及两侧固设隔离板;
[0093]
s4:透层油配制,所述透层油由脂肪醇聚氧乙烯醚(aeo)和环氧基错台修复剂按质量份比3:1混合搅拌制成,其中,脂肪醇聚氧乙烯醚(aeo)又称为聚氧乙烯脂肪醇醚,用以下通式表示:ro(ch2ch2o)nh,其中n是聚合度,因聚乙二醇的聚合度和脂肪醇的种类不同而有不同的品种。具体混合操作:先在容器中加入3份脂肪醇聚氧乙烯醚(aeo),然后在往容器中加入1份环氧基错台修复剂,利用搅拌棒搅拌1至3分钟即可;
[0094]
s5:涂刷透层油,将所述透层油均匀涂满施工区域,涂刷后既能均匀覆盖路面又不存在透层油堆积;
[0095]
s6:错台修补材料配制,错台修补材料采用所述错台修补环氧砼,具体的,首先往搅拌器里加入24份环氧基错台修复剂,启动搅拌器,再依次往搅拌器里加入14.5份大颗粒石英砂(20目~40目)、27份中颗粒石英砂(70目~120目)、12.4份细颗粒石英砂(大于200目)、9.5份灰色调色矿粉(大于200目),添加完毕,继续搅拌,直至完全没有花料;
[0096]
s7:涂抹错台修补材料,待s5步骤中涂刷的所述透层油干透后,对施工区域涂抹所述错台修补环氧砼;
[0097]
s8:铺设防滑材料,在s7步骤完成后的所述错台修补环氧砼表面均匀铺撒防滑陶瓷颗粒;
[0098]
s9:回收防滑材料,待所述错台修补环氧砼初凝后,对于未与所述错台修补环氧砼固定连接的所述防滑陶瓷颗粒进行回收,回收后即可开放交通。
[0099]
以上实施例仅用以说明本发明的技术方案,而非对其限制;尽管参照前述实施例对本发明进行了详细的说明,本领域的普通技术人员应当理解:其依然可以对前述各实施例所记载的技术方案进行修改,或者对其中部分技术特征进行等同替换;而这些修改或者替换,并不使相应技术方案的本质脱离本发明各实施例技术方案的精神和范围。