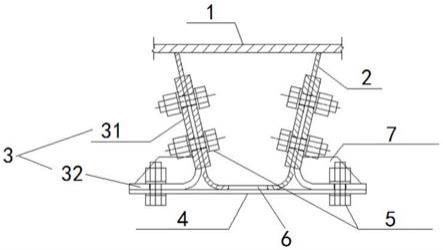
一种顶板u肋连接结构及其施工方法
技术领域
1.本发明涉及桥梁工程技术领域,具体涉及一种顶板u肋连接结构及其施工方法。
背景技术:
2.正交异性钢桥面板是由相互垂直的顶板、纵肋和横隔板通过焊缝连接组成一体而共同工作的结构形式,具有自重轻、承载能力大、使用范围广、施工速度快、造型美观等特点。正交异性钢桥面板的纵肋通常采用u型加劲肋结构。
3.随着钢桥的大规模应用,正交异性钢桥面板的疲劳开裂问题越来越得到重视,尤其是节段拼接处顶板u肋的工地连接构造,往往是疲劳问题的集中点。目前采用的顶板u肋连接构造形式主要有两种:一是利用u肋嵌补段和衬板,通过焊接的形式,将两节段的u肋进行连接;此连接构造的优点为构造简单,刚度没有削弱,缺点为u肋对接处易出现疲劳病害。二是采用u肋腹板加设拼接板,利用高强螺栓连接取代焊缝连接,但这一构造为解决高强螺栓的操作,需要在u肋连接处的底板开手孔;此连接构造的优点为利用高强螺栓连接u肋,避免了疲劳病害,缺点为u肋底板开设了手孔,对u肋刚度有较大削弱。
技术实现要素:
4.本发明的目的是提供一种顶板u肋连接结构及其施工方法,缓解对接处的u肋刚度削弱问题。
5.本发明的目的可以通过以下技术方案来实现:一种顶板u肋连接结构,包括顶板以及焊接于顶板上的u肋,所述的u肋在节段拼接处设置有腹板连接板和底板连接板,所述的腹板连接板包括u肋连接部和底板连接部,u肋连接部连接u肋,底板连接部连接底板连接板。
6.优选地,所述的腹板连接板设置在u肋外侧,底板连接板设置在u肋底部。
7.优选地,所述的u肋连接部和底板连接部呈夹角设置,u肋连接部紧贴u肋的外壁,底板连接部紧贴u肋的底面。
8.进一步优选地,所述的u肋连接部和底板连接部一体成型,连接处呈弧形。
9.优选地,所述的u肋连接部与u肋可拆卸连接,底板连接部与底板连接板可拆卸连接。
10.进一步优选地,所述的u肋连接部通过高强螺栓连接u肋,底板连接部通过高强螺栓连接底板连接板。
11.优选地,所述的u肋在节段拼接处开设有手孔。
12.进一步优选地,所述的手孔设置在u肋的底面。
13.优选地,所述的腹板连接板上设置有加劲肋。
14.进一步优选地,多个所述的加劲肋平行设置在底板连接部上。
15.一种上述顶板u肋连接结构的施工方法,包括以下步骤:
16.s1:利用腹板连接板和高强螺栓,通过手孔将两节段的u肋螺栓连接;
17.s2:利用底板连接板和高强螺栓,将两节段的u肋的底面螺栓连接。
18.与现有技术相比,本发明具有以下优点:
19.1.本发明可解决正交异性钢桥面板顶板u肋连接薄弱的问题;
20.2.本发明在u肋腹板栓接的基础上,对拼接板进行改造,增设底板连接板及高强螺栓,实现全螺栓对接,不仅避免了疲劳病害问题,也解决了对接处的u肋刚度削弱;
21.3.本发明可解决接缝处的疲劳问题,也可弥补u肋刚度削弱的不足,可在既有螺栓连接构造基础上进行改造,不仅适用于新建正交异性钢桥面板,也适用于既有正交异形钢桥面板的加固;
22.4.本发明通过u肋腹板连接板的改造,将封闭内部螺栓连接构造转换为外部螺栓连接构造,从而达到最后一道工序无需开手孔,削弱刚度;
23.5.本发明通过腹板连接板的l型结构设计,使内部连接外延,提供底板连接外部基座,解决了u肋对接处手孔刚度削弱的问题;
24.6.本发明通过腹板连接板、u肋和底板连接板的配合,将u肋底板对接力通过高强螺栓传递给底板连接部及底板连接板,u肋腹板的剪切力通过高强螺栓传递给u肋连接部。
附图说明
25.图1为本发明顶板u肋连接结构的主视图;
26.图2为本发明顶板u肋连接结构的侧视图;
27.图3为本发明顶板u肋连接结构的局部俯视图;
28.图4为本发明腹板连接板的结构示意图;
29.图5为对比例1全焊接形式的连接构造的侧视图;
30.图6为对比例1全焊接形式的连接构造的主视图;
31.图7为对比例2顶板u肋腹板栓接构造的侧视图;
32.图8为对比例2顶板u肋腹板栓接构造的主视图;
33.图9为对比例2顶板u肋腹板栓接构造的局部俯视图;
34.图中:1-顶板,2-u肋,3-腹板连接板,31-u肋连接部,32-底板连接部,33-螺栓孔,4-底板连接板,5-高强螺栓,6-手孔,7-加劲肋,8-衬板,9-u肋嵌补段,10-拼接板,11-u肋封头板。
具体实施方式
35.下面结合附图和具体实施例对本发明进行详细说明。以下实施例在以本发明技术方案为前提下进行实施,给出了详细的实施方式和具体的操作过程,但本发明的保护范围不限于下述的实施例。
36.实施例1
37.一种顶板u肋连接结构,如图1~3所示,包括顶板1、u肋2、腹板连接板3、底板连接板4、高强螺栓5和手孔6。u肋2焊接在顶板1下表面上,腹板连接板3和底板连接板4均通过高强螺栓5可拆卸设置在u肋2的节段拼接处。其中,腹板连接板3设置在u肋2的外侧,结构如图4所示,包括呈夹角设置的u肋连接部31和底板连接部32,u肋连接部31和底板连接部32连接处呈弧形结构,在u肋连接部31和底板连接部32上均开设有螺栓孔33,u肋2底面开设有手孔
6,如图1所示,u肋连接部31通过高强螺栓5固定于u肋2的侧壁,底板连接部32通过高强螺栓5固定于底板连接板4上,使底板连接板4固定与u肋2的底面,弥补u肋2底面手孔6刚度削弱问题。
38.实施例2
39.一种顶板u肋连接结构,在底板连接部32上设置有加劲肋7以加强结构强度,其余结构与实施例1相同。
40.本实施例顶板u肋连接结构的制备和施工方法如下:
41.第一步:在工厂下料加工腹板连接板3,将原矩形连接平板,改造为l形连接板,并设置加劲肋7与其焊接进行加强;
42.第二步:在工厂节段预拼,在u肋2、腹板连接板3、底板连接板4上定位高强螺栓孔位,并精确制孔,在两侧节段端部的u肋2底部开设手孔6,便于施拧高强螺栓5;
43.第三步:拼接现场先利用腹板连接板3及高强螺栓5,通过手孔6将两节段的u肋腹板栓接连接;
44.第四步:将底板连接板4对孔定位,将两侧u肋的底板利用高强螺栓5连接,弥补手孔刚度削弱问题。
45.对比例1
46.一种全焊接形式的连接构造,如图5~6所示,利用u肋嵌补段9和钢衬板8,通过现场围焊的方式进行顶板u肋的工地连接。此连接构造的优点为构造简单,刚度没有削弱,缺点为u肋对接处易出现疲劳病害。
47.对比例2
48.一种顶板u肋腹板栓接构造,如图7~9所示,采用u肋腹板加设拼接板10,利用高强螺栓5连接,u肋底板开设手孔6,以便于高强螺栓5的操作。此方案的优点为:利用高强螺栓连接u肋,避免了疲劳病害,缺点为u肋底板开设了手孔,对u肋刚度有较大削弱。
49.上述的对实施例的描述是为便于该技术领域的普通技术人员能理解和使用本发明。熟悉本领域技术的人员显然可以容易地对这些实施例做出各种修改,并把在此说明的一般原理应用到其他实施例中而不必经过创造性的劳动。因此,本发明不限于上述实施例,本领域技术人员根据本发明的揭示,不脱离本发明范畴所做出的改进和修改都应该在本发明的保护范围之内。