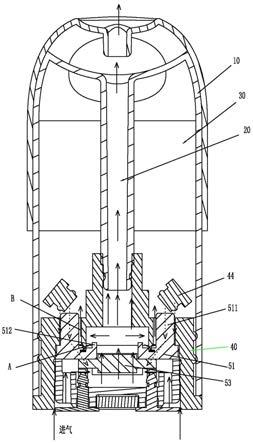
1.本发明涉及雾化器领域技术,尤其是指一种雾化器,其主要但是不局限于电子烟,也可用于医用雾化产品等。
背景技术:
2.目前的雾化器,在仓储和运输途中,储液腔中的液体通过雾化芯和外界空气接触,造成氧化或者吸收空气中的水分,影响保质期和使用效能。由于仓储和运输途中,储液腔中的液体因为和雾化芯接触,不能完全密封,在外界温度和气压发生变化时造成储液腔和外部大气压形成压力差,储液腔内液体在压力作用下向外渗(漏)液。
3.以及,目前的雾化器主要采用棉芯外面绕发热丝,或者微孔陶瓷表面附发热电路(例如:贴发热铁片/网,或者印刷发热电路等)等方式,它们有个共同特点:发热元件和导液元件直接接触,理想状态下,导液元件既需导液、锁液性能良好,又需耐高温且在高温下不能分解出有异味的物质、有毒物质。但是,一般材料难以同时满足以上要求,例如:1、棉花芯外面绕发热丝的方式,由于棉花芯不耐高温,在供液不足的情况下容易烧糊,而供液太充足也会造成漏液;2、陶瓷芯是将发热元件紧贴陶瓷表面或镶嵌于陶瓷内部,发热元件在加热雾化液的时候同时也在加热陶瓷,造成热能的浪费,且,陶瓷发热后也加热陶瓷上部储液腔的雾化液,使雾化液容易变质变味,缩短保持期,同时,微孔陶瓷内部不可避免地存在盲孔和半盲孔,发热元件紧贴陶瓷或者镶嵌在陶瓷内部,使盲孔内的雾化液不能雾化成气体带走热量,盲孔内的雾化液在反复高温下容易产生有毒有害物质。经加热雾化的气体,由于温差,在后段流通过程中容易出现冷凝液,且,过热的雾化气被吸用可能导致用户烫嘴,这些都会影响用户体验感。还有,在微孔陶瓷烧结前把微孔金属发热材料定位在陶瓷模具里,再浇注陶瓷原料再烧结,由于微孔金属材料比较软,定位困难,导致工艺复杂,生产成本高。
4.因此,本发明中,申请人精心研究了一种新的技术方案来解决上述问题。
技术实现要素:
5.有鉴于此,本发明针对现有技术存在之缺失,其主要目的是提供一种雾化器,其通过软胶密封件、导液元件的巧妙结构设计,使得雾化器在仓储和运输状态,雾化液完全和外界空气隔绝,确保仓储和运输过程中不漏液及延长雾化液保质期;而把雾化芯压入正常工作位置后,利用导液元件的导液柱穿过密封孔刺破待刺破部或者顶开密封塞,实现储液腔出液。
6.为实现上述目的,本发明采用如下之技术方案:一种雾化器,包括壳体和设置于壳体内的气嘴通道、储液腔、软胶密封件、雾化芯、供电及控制装置;其中:所述软胶密封件内具有雾化芯安装腔,所述软胶密封件上对应雾化芯安装腔的上端设置有密封孔;所述软胶密封件成型时一体连接有待刺破部封住密封孔,或者,所述密封孔内设置有密封塞以封住密封孔;
所述雾化芯包括导液元件及雾化元件,所述导液元件采用微孔材料,所述导液元件一体向上延伸有用于刺破待刺破部或者顶开密封塞以使储液腔能经导液柱出液至导液元件的导液柱。
7.作为一种优选方案,所述雾化器在正常工作之前,所述雾化芯位于雾化芯安装腔的内部或外部。
8.作为一种优选方案,所述雾化芯安装腔内具有自下而上依次设置的第一安装位和第二安装位;所述雾化芯安装于第一安装位时,所述导液柱位于待刺破部或密封塞的下方,所述待刺破部或密封塞阻隔于储液腔与雾化芯安装腔之间;所述雾化芯自第一安装位向上压入第二安装位时,所述导液柱穿过密封孔刺破待刺破部或者顶开密封塞,所述储液腔经导液柱实现出液。
9.作为一种优选方案,所述软胶密封件上对应雾化芯安装腔的上端设置有供气接头,所述供气接头连通于气嘴通道下端与雾化芯安装腔之间,所述软胶密封件上围绕供气接头下端延伸设置有环形隔离部;在第二安装位时,所述环形隔离部的下端设置有第一通气间隙,所述导液柱与密封孔的内壁面之间形成第二通气间隙;所述储液腔经第一通气间隙、第二通气间隙实现进气。
10.作为一种优选方案,所述第一通气间隙是环形隔离部的下端与导液元件之间形成间隙,或者,所述第一通气间隙是导液元件顶部凹设的通气槽,或者,所述第一通气间隙是利用导液元件自身的微孔作为第一通气间隙。
11.作为一种优选方案,所述导液元件上设置有堵液骨,所述堵液骨高于第一通气间隙以隔设于供气接头下方区域与第一通气间隙所在区域之间。
12.作为一种优选方案,所述导液元件设置有雾化气体冷却孔,所述雾化气体冷却孔上下贯通导液元件,所述雾化气体冷却孔位于供气接头下方,所述堵液骨隔设于雾化气体冷却孔的上端开口与第一通气间隙所在区域之间。
13.作为一种优选方案,所述导液元件具有导液槽,所述导液槽上下贯通导液元件,所述雾化元件伸入导液槽内,所述雾化气体冷却孔位于导液槽的侧旁;常温气体经雾化气体冷却孔向上输送,液体经雾化元件加热成雾化气体后向上输送,雾化气体和常温气体混合冷却。
14.作为一种优选方案,所述雾化元件采用可吸液的多孔电热材料;所述可吸液的多孔电热材料为小直径电阻丝编织片、小直径电阻丝编织管、多孔微孔金属件、蚀刻孔金属件、通槽金属件、冲压孔金属件或金属网;和/或:所述导液元件为微孔陶瓷、微孔纤维或活性炭。
15.作为一种优选方案,所述雾化芯包括有导电片,所述导电片设置于导液元件上或者壳体上,所述雾化元件设置于导电片上或者壳体上。
16.本发明与现有技术相比具有明显的优点和有益效果,具体而言,由上述技术方案可知,其主要是通过软胶密封件、导液元件的巧妙结构设计,使得雾化器在仓储和运输状态,软胶密封件成型时一体连接的待刺破部封住密封孔,以阻隔储液腔与雾化芯安装腔,雾化液完全和外界空气隔绝,确保仓储和运输过程中不漏液及延长雾化液保质期;而把雾化芯压入正常工作位置后,利用导液元件的导液柱穿过密封孔刺破待刺破部或者顶开密封塞,雾化液经过导液柱进入导液元件。
17.其次是,通过增加堵液骨,可以堵住多余渗出来的液体(例如烟油),一方面,避免液体外漏(例如漏入气嘴通道等),另一方面,提升导液元件顶部周围的液体平面高度,使多余渗出来的液体的平面高出第一通气间隙,堵住空气进入储液腔,更利于止住储液腔内液体继续往外渗,更好地达到负气压防漏液的目的。
18.再者是,雾化元件不需随微孔陶瓷烧结埋在微孔陶瓷里面,解决了定位困难、工艺复杂的问题,有利于控制生产成本。
19.为更清楚地阐述本发明的结构特征和功效,下面结合附图与具体实施例来对本发明进行详细说明。
附图说明
20.图1是本发明之实施例一中雾化芯的立体示图;图2是本发明之实施例一中雾化芯的侧视图;图3是本发明之实施例一中雾化芯的截面示图;图4是本发明之实施例一雾化芯安装之前的截面示图;图5是本发明之实施例一雾化芯安装之前的另一截面示图;图6是本发明之实施例一雾化芯处于非正常工作位置的截面示图;图7是本发明之实施例一雾化芯向上压入正常工作位置后的截面示图;图8是图4的局部放大示图;图9是图5的局部放大示图;图10是本发明之实施例一雾化芯向上压入正常工作位置后的截面示图(含供电及控制装置);图11是本发明之实施例二雾化芯处于非正常工作位置的截面示图;图12是本发明之实施例二雾化芯向上压入正常工作位置后的截面示图;图13是本发明之实施例三中雾化芯的立体示图;图14是本发明之实施例三中雾化芯的另一立体示图;图15是本发明之实施例三中雾化芯的截面示图;图16是本发明之实施例四雾化芯向上压入正常工作位置后的截面示图;图17是本发明之实施例四中雾化芯的组装状态截面示图;图18是本发明之实施例四中雾化芯的分解状态截面示图;图19是本发明之实施例五中雾化芯的组装状态截面示图;图20是本发明之实施例五中雾化芯的分解状态截面示图。
21.附图标识说明:壳体10、气嘴通道20、储液腔30、软胶密封件40、雾化芯安装腔41、供气接头42、密封孔43、待刺破部44'、密封塞44、环形隔离部45、雾化芯50、导液元件51、导电片52、雾化元件53、导液柱511、第一通气间隙a、第二通气间隙b、堵液骨512、雾化气体冷却孔513、导液槽514、供电及控制装置60、供电连接座70、雾化元件53’、硅胶件80、侧向进气孔81、雾化元件501、底壳502、导电片503、供电连接座70’、导液元件51’、导油槽511’、雾化元件504、导液元件505、辅助导液元件506、导液槽507。
具体实施方式
22.请参照图1至图20所示,其显示出了本发明之多种实施例的具体结构。
23.一种雾化器,包括壳体10和设置于壳体10内的气嘴通道20、储液腔30、软胶密封件40、雾化芯50、供电及控制装置60;其中:所述软胶密封件40内具有雾化芯安装腔41,所述软胶密封件40上对应雾化芯安装腔41的上端设置有供气接头42、密封孔43,所述软胶密封件40上围绕供气接头42下端延伸设置有环形隔离部45;所述供气接头42连通于气嘴通道20下端与雾化芯安装腔41之间,所述密封孔43内设置有密封塞44以封住密封孔43,以阻隔储液腔30与雾化芯安装腔41,此处,在软胶密封件40成型时一体连接有密封塞44,易于生产制作;当然,若另外制作密封塞装入密封孔43内以封住密封孔43,亦可。如图4、图6及图7所示,其显示了密封孔43内设置有密封塞44以封住密封孔43的情形。如图11和图12所示,其在软胶密封件40成型时一体连接有待刺破部44'封住密封孔43,通常待刺破部44'采用薄壁设计,待刺破部44'的周缘与密封孔43的内壁面一体成型连接呈闭合结构。
24.所述雾化芯50包括导液元件51、导电片52及雾化元件53;所述导液元件51采用微孔材料,所述导电片52连接于雾化元件53,所述导液元件51向上延伸有用于刺破待刺破部44'或者顶开密封塞44以使储液腔30能经导液柱511出液至导液元件51的导液511。
25.所述导液柱511与导液元件51一体成型设置,因此,导液柱511也为微孔材料。所述导电片52设置于导液元件51上,所述雾化元件53设置于导电片52上,不需随微孔陶瓷烧结埋在微孔陶瓷里面,解决了定位困难、工艺复杂的问题,有利于控制生产成本。也可以把导电片52安装设置于壳体10上,雾化元件53也可设置于壳体10上,例如:将导电片52装在壳体10上,再把雾化元件53装在两个导电片52之间,该种安装方式,更方便简捷,有利于推广生产应用。
26.所述雾化器在正常工作之前,所述雾化芯位于雾化芯安装腔的内部或外部。且待刺破部44'或者密封塞44封住密封孔43,以阻隔储液腔30与雾化芯安装腔41,因此,确保在仓储和运输过程中,不漏液;而产品到了终端用户手中后,可以将雾化芯50安装至正常工作位置,在安装雾化芯50的过程中,所述导液柱511穿过密封孔43刺破待刺破部44'或者顶开密封塞44,所述储液腔30经导液柱511实现出液。
27.实施例一中,在所述雾化芯安装腔41内具有自下而上依次设置的第一安装位和第二安装位;所述雾化芯50安装于第一安装位时,所述导液柱511位于待刺破部44'或密封塞44的下方,所述待刺破部44'或密封塞44阻隔于储液腔30与雾化芯安装腔41之间;所述雾化芯50向上压入第二安装位时,所述导液柱511穿过密封孔43刺破待刺破部44'或者顶开密封塞44,所述储液腔30经导液柱511实现出液。由于软胶密封件40具有一定弹性变形能力,因此,雾化芯安装腔41有一定变形能力,可以在雾化芯安装腔41内设计台阶作为第一安装位、第二安装位,将雾化芯50装至第一安装位时以及后续将雾化芯50压入第二安装位时时,可以有明确的档位感。也可不设计台阶,利用雾化芯安装腔41的弹性紧配力即可。
28.通常,在出厂时,所述雾化芯50安装于雾化芯安装腔41内,所述雾化芯50处于非正常工作位置(也指第一安装位),所述导液柱511位于待刺破部44'或密封塞44的下方,所述待刺破部44'或密封塞44阻隔于储液腔30与雾化芯安装腔41之间;因此,在仓储和运输过程中,不漏液;而产品到了终端用户手中后,可以将雾化芯50向上自第一安装位压入正常工作
位置(也指第二安装位),所述导液柱511穿过密封孔43刺破待刺破部44'或者顶开密封塞44,所述储液腔30经导液柱511实现出液。所述导液柱511穿过密封孔43并伸入储液腔30,所述环形隔离部45的下端设置有第一通气间隙a,所述导液柱511与密封孔43的内壁面之间形成第二通气间隙b;所述储液腔30经第一通气间隙a、第二通气间隙b实现进气,所述储液腔30经导液柱511实现出液。在实际设计制作时,所述第一通气间隙a是环形隔离部45的下端与导液元件51之间形成间隙,或者,所述第一通气间隙是导液元件51顶部凹设的通气槽,或者,所述第一通气间隙是利用导液元件51自身的微孔作为第一通气间隙。相较而言,在所述环形隔离部45的下端与导液元件51之间形成第一通气间隙a的设计情形,内外气压更容易达到平衡,液体更容易渗出,避免干烧。对于功率要求不是很高的情形,通过导液元件51自身微孔材料内部的微孔进气,平衡储液腔30内外的气压,也是可行的。
29.所述导液元件51上设置有堵液骨512,所述堵液骨512高于第一通气间隙a以隔设于供气接头42下方区域与第一通气间隙a所在区域之间。所述导液元件51设置有雾化气体冷却孔513,所述雾化气体冷却孔513上下贯通导液元件51,所述雾化气体冷却孔513位于供气接头42下方,所述堵液骨512隔设于雾化气体冷却孔513的上端开口与第一通气间隙a所在区域之间。利用堵液骨512,可以堵住多余渗出来的液体(例如烟油),避免液体外漏(例如漏入气嘴通道20等),也可提升第一通气间隙a周围的液体平面高度,使多余渗出来的液体的平面高出第一通气间隙a,堵住空气进入储液腔30,更利于止住储液腔30内液体继续往外渗,更好地达到负气压防漏液的目的。
30.所述导液元件51具有导液槽514,所述导液槽514上下贯通导液元件51,所述雾化元件53部伸入导液槽514内,所述雾化气体冷却孔513位于导液槽514的侧旁;常温气体经雾化气体冷却孔513向上输送,液体经雾化元件53加热成雾化气体后向上输送,雾化气体和常温气体混合冷却。所述雾化元件53的部分或整体伸入导液槽514内;所述雾化元件53采用可吸液的多孔电热材料,例如:所述雾化元件53为小直径电阻丝编织片、小直径电阻丝编织管、多孔微孔金属件、蚀刻孔金属件、通槽金属件、冲压孔金属件或金属网。所述导液元件51为微孔陶瓷、微孔纤维或活性炭。由于毛细现象,导液槽514内会储有雾化液,雾化元件53不需与导液元件51直接接触,就可吸收到导液元件51内的雾化液,雾化元件53在加热雾化时,导液元件51不会出现高温,不参与雾化,完全避免了现有陶瓷雾化芯50的缺点,充分发挥了雾化元件53采用可吸液的多孔电热材料时的优点,因为没有雾化元件53埋在微孔陶瓷里面,增大了雾化面积,整体温度更加均衡,雾化效率更高,雾化效果更好,口味更纯。同时因为我们的导液元件51在功能上不参与高温雾化,只需满足导液锁液功能,温度接近环境温度,当雾化气体经过导液元件51的雾化气体冷却孔513时,储存在导液元件51内的待雾化液可以吸收部分热量及大雾化气体中的大颗粒,起到给雾化气体降温的作用,避免用户烫嘴,减小了雾化气体在后段流通过程中的冷凝液,提升用户体验感,同时实现热量和大颗粒烟液回收重新利用,节能环保。
31.如图13至图15所示,其显示了实施例三的雾化芯的具体结构。其与实施例一的主要区别在于:实施例三中的雾化元件53’设置于导液元件51的底部。雾化元件53’可以与底部的导电柱直接接触导通,也可以另设置导电片用于连接在雾化元件53’、导电柱之间,相当于导电片与导电柱接触。
32.如图16所示,其显示了实施例四的雾化芯向上压入正常工作位置后的气体走向。
通常在雾化芯的下侧设置有硅胶件80,所述硅胶件80位于侧向进气孔81的内侧。在抽吸时,常温气体(或指冷气)从侧向进气孔81进入,在外部气压的作用下将硅胶件80往内打开。停止抽吸时,硅胶件80在自身回弹力的作用下回弹,堵住侧向进气孔81,避免雾化气体或者导液元件多余渗出的液体外出,影响客户体验感及使用功能。
33.如图17和图18所示,所述雾化元件501安装于底壳502上的两导电片503之间,具体是指导电片503设置于底壳502上形成供电连接座70’上,将导液元件51’组装于供电连接座70’上后,所述雾化元件501插入导液元件51’的导油槽511’内。该种安装方式,更方便简捷,有利于推广生产应用。
34.如图19和图20所示,为了进一步提升口感,也可在雾化元件504和导液元件505之间增加一层辅助导液元件506。实际制作时,可以将雾化元件504平置于两导电片503的顶部之间,再于雾化元件504顶部平贴辅助导液元件506,所述辅助导液元件506优选纯天然导液元件或者能释放特殊味道的导液元件,纯天然导液元件或者能释放特殊味道的导液元件紧贴上方的导液元件505的底部,使上方的导液元件505表面及导液槽507内的液体能顺利送至纯天然导油元件或者能释放特殊味道的导油元件上。
35.本发明的设计重点在于:其主要是通过软胶密封件、导液元件的巧妙结构设计,使得雾化器在仓储和运输状态,软胶密封件成型时一体连接的待刺破部封住密封孔,以阻隔储液腔与雾化芯安装腔,雾化液完全和外界空气隔绝,确保仓储和运输过程中不漏液及延长雾化液保质期;而把雾化芯压入正常工作位置后,利用导液元件的导液柱穿过密封孔刺破待刺破部或者顶开密封塞,雾化液经过导液柱进入导液元件。
36.其次是,通过增加堵液骨,可以堵住多余渗出来的液体(例如烟油),一方面,避免液体外漏(例如漏入气嘴通道等),另一方面,提升导液元件顶部周围的液体平面高度,使多余渗出来的液体的平面高出第一通气间隙,堵住空气进入储液腔,更利于止住储液腔内液体继续往外渗,更好地达到负气压防漏液的目的。
37.再者是,雾化元件不需随微孔陶瓷烧结埋在微孔陶瓷里面,解决了定位困难、工艺复杂的问题,有利于控制生产成本。
38.以上所述,仅是本发明的较佳实施例而已,并非对本发明的技术范围作任何限制,故凡是依据本发明的技术实质对以上实施例所作的任何细微修改、等同变化与修饰,均仍属于本发明技术方案的范围内。