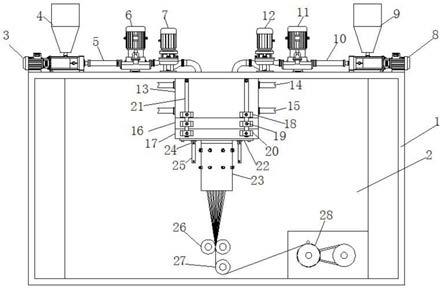
1.本发明涉及化纤制备技术领域,具体为一种再生并列复合仿羽绒聚酯纤维的制备方法及设备。
背景技术:
2.天然的羽绒具有蓬松保暖、光滑柔软的特性,但它不是一种纤维,而是具有纤维团簇结构,且有着相同使用目的的羽毛团,每个大小的羽毛枝都具有独立的柔韧性、回弹性,羽绒正是由这些羽毛单元组成的多个结构的集合体。近年来,禽流感的大规模出现导致家禽的大规模扑杀,使羽绒制品的原材料供应紧张,原材料价格也有所上涨,特别是禽流感之后,人们对羽绒原料和真菌的含量要求越来越严格,这为开发类似羽绒产品的复合纤维提供了商机。
3.目前,国内外已开发出羽绒状纤维,主要有超细旦纤维和添加硅油后处理的三维卷曲中空纤维,市场上的羽绒类产品基本上有两种,一种是2~8d三维中空和1.0d高硅二维中空短纤维,2~8d三维中空羽绒类纤维,虽然这些纤维因具有空腔,具有一定保温性能,但由于纤密度大,触感依然还是比较差的,和真正的羽绒依旧有着较大差异,1.0d高硅二维中空短纤维,虽然具有接近羽绒的手感,但缺乏保暖性和柔软性。
4.随着资源可持续发展理念和生态环境保护理念的逐步完善,循环系统的概念已经成为当今时代的基调,我国很多纺织行业都在逐步利用循环系统对纤维进行再生,再生纤维是以废瓶片、废旧纤维、聚酯下脚料、服装面料等为原料,根据有机化学、物理等现代技术方法,经纺丝生产加工熔合而成,既拓展了新的化纤资源,又整合了节能降耗新技术,又可以满足目前政策法规所要求的碳达峰、碳综合,新工艺提高了产品质量和功能,实现了循环利用、低碳环保、高效的统一。
5.涤纶纺丝用废料的来源主要有两个方面:一是制造生产过程中不可避免地产生的废弃熔体、废丝和边角料;二是贸易后的聚酯包装产品,如pet瓶和塑料薄膜,其中,主要是消费后的pet瓶,因为大部分的聚酯包装产品都是一次性的,现阶段我国再制造涤纶纤维生产工艺分为物理法和化学法,物理法的技术特点是将再生聚酯瓶片根据结晶干燥后送螺杆挤出机挤出,采用多级高精度过滤技术,制成再生聚酯纤维,化学法是将上述原材料回收,利用有机化学品的醇解作用,使其完全恢复到单分子结构水平,经过滤、去除残渣后,再通过聚合生产pet切片,最后制成再生聚酯纤维,物理法应用广泛,机械设备投资少,加工工艺简单,对自然环境的危害比化学法小,化学法就是使用有机化学品的醇解作用来解决问题。根据废涤纶的解聚得到涤纶单体或低聚物,再重新聚合成高聚物,可完成废涤纶的多次循环利用,制得再生涤纶纤维。
6.然而,物理法制成的再生涤纶纤维织物的化学成分与原生涤纶纤维相比,物化指标上具有一定差异,且由于聚酯的降解特性,无法实现多次循环利用,而化学法所使用的化学品可能造成的环境污染的问题。
7.另,现有的纺丝设备使用时,一般需要采用一定量的聚酯片进行冲刷通道,待流出
的纺丝熔体完全无杂质后再开始生产,一旦出现杂质较多就会导致喷丝板堵塞,现有纺丝设备对于喷丝板堵塞后清理均非常不方便。
技术实现要素:
8.(一)解决的技术问题
9.针对现有技术的不足,本发明提供了一种再生并列复合仿羽绒聚酯纤维的制备方法及设备,解决了物理法制成的再生涤纶纤维织物的化学成分与原生涤纶纤维相比,物化指标上具有一定差异,且由于聚酯的降解特性,无法实现多次循环利用的问题以及化学法所使用的化学品可能造成的环境污染的问题和现有纺丝设备对于喷丝板堵塞后清理均非常不方便的问题。
10.(二)技术方案
11.为实现以上目的,本发明通过以下技术方案予以实现:一种再生并列复合仿羽绒聚酯纤维的制备设备,包括机架,所述机架后壁固定连接有背板;固定连接在所述机架上壁且分别位于两端的第一螺杆挤出机、第二螺杆挤出机,所述第一螺杆挤出机、第二螺杆挤出机进进口端分别固定连接有第一料筒、第二料筒;依次固定连接在所述第一螺杆挤出机出口端的第一静态混合器、第一增压泵以及第一计量泵;依次固定连接在所述第二螺杆挤出机出口端的第二静态混合器、第二增压泵以及第二计量泵;固定连接在所述背板前壁且靠近上端的复合纺丝箱;设置在复合纺丝箱内部用于对熔体保温的保温结构;固定连接在所述复合纺丝箱下壁用于分配熔体的并列复合纺丝分配板;固定连接在所述并列复合纺丝分配板下壁的喷丝板,所述喷丝板内壁设置有多组喷丝孔;通过安装法兰固定连接在喷丝板下壁的吹风甬道;设置在复合纺丝箱、并列复合纺丝分配板、喷丝板之间以及喷丝板与安装法兰之间用于方便检修的第一滑动组件和第二滑动组件,所述第一滑动组件、第二滑动组件上均设置有用于防止脱落的限位组件和用于固定位置的锁紧组件;依次设置在所述背板前壁且位于吹风甬道下侧的上油轮、导向轮;固定连接在所述机架内侧下壁且靠近右侧的卷绕机。
12.优选的,所述保温结构包括第一保温内胆、第二保温内胆、保温气体进口管、保温气体出口管以及保温夹层,所述第一保温内胆、第二保温内胆呈左右分布设置在复合纺丝箱内部,所述第一计量泵出口端与第一保温内胆、第二计量泵出口端与第二保温内胆均通过管道贯通,所述保温夹层设置在复合纺丝箱内部且位于第一保温内胆、第二保温内胆外壁,两组保温腔,所述保温夹层与第一保温内胆之间以及保温夹层与第二保温内胆之间均设置有保温腔,所述保温气体进口管、保温气体出口管均固定连接在复合纺丝箱侧壁且分别靠近上壁和下壁,所述保温气体进口管、保温气体出口管外壁均贯穿复合纺丝箱侧壁以及保温夹层至保温腔内侧。
13.优选的,所述第一滑动组件包括第一滑动座、第二滑动座、第三滑动座以及第一滑杆,所述第一滑动座、第二滑动座以及第三滑动座分别固定连接在复合纺丝箱、并列复合纺丝分配板以及喷丝板外壁,所述第一滑杆固定连接在第三滑动座内壁,所述第一滑杆远离第三滑动座的一端外壁依次贯穿第二滑动座、第一滑动座至第一滑动座上侧。
14.优选的,所述第二滑动组件包括第四滑动座、第二滑杆,所述第四滑动座固定连接在安装法兰下壁且位于吹风甬道外侧,所述第二滑杆固定连接在喷丝板下壁,所述第二滑
杆远离喷丝板的一端外壁依次贯穿安装法兰、第四滑动座至第四滑动座下侧。
15.优选的,所述锁紧组件包括多组锁紧螺丝,多组所述锁紧螺丝分别固定连接在第一滑动座、第二滑动座、第三滑动座以及第四滑动座侧壁,所述第一滑动座、第二滑动座、第三滑动座与第一滑杆之间以及第四滑动座与第二滑杆之间分别通过多组锁紧螺丝固定连接。
16.优选的,所述限位组件包括两组限位螺丝,两组所述限位螺丝分别螺纹连接在第一滑杆远离第三滑动座的一端外壁以及第二滑杆远离喷丝板的一端外壁。
17.优选的,所述喷丝孔呈圆周等分阵列形式分布在喷丝板内壁,所述喷丝孔横截面形状接近s型。
18.优选的,所述吹风甬道为全封闭式环吹风冷却形式。
19.一种再生并列复合仿羽绒聚酯纤维的制备方法,所述制备方法包括如下步骤:
20.s1、将高粘度再生聚酯切片和低粘度再生聚酯切片分别投入第一料筒、第二料筒,再分别经过第一螺杆挤出机、第二螺杆挤出机连续干燥熔融挤出,进一步分别通过第一静态混合器、第二静态混合器充分混合;
21.s2、将上述两路熔体分别通过第一增压泵、第二增压泵进行增压,再经过第一计量泵、第二计量泵准确计量后分别送入复合纺丝箱内部的第一保温内胆以及第二保温内胆中;
22.s3、经保温气体进口管通入气相热媒vp-1进入保温腔并从保温气体出口管吹出形成循环为纺丝熔体保温,并保证两种纺丝熔体在维持各自不同的温度情况下进入并列复合纺丝分配板,经并列复合纺丝分配板分配后通过喷丝板上的喷丝孔喷出进行并列复合熔体纺丝,形成并列型丝束;
23.s4、经吹风甬道全密闭式环吹风冷却、上油轮上油后经导向轮导向再经卷绕机卷绕;
24.s5、卷绕后丝束经过往复落丝、集束、导丝、牵伸浴牵伸、蒸汽牵伸、机械卷曲、松弛热定型、切断、打包工序制备得到再生并列复合仿羽绒聚酯纤维。
25.优选的,所述高粘度再生聚酯切片制备方法如下:
26.1)、以废聚酯瓶片为原料,通过分拣、脱标、破碎、碱洗、漂洗生产再生聚酯瓶片;
27.2)、以再生聚酯瓶片为原料,使用硫化床热风连续干燥系统进行干燥,然后通过螺杆熔融送入反应釜,挤出温度为255~268℃,并使用乙二醇钛系降解催化剂为改性剂,进行再生瓶片的破碎和催化剂的熔融混合,然后进行缩聚反应,得到高粘度再生聚酯切片。
28.优选的,所述低粘度再生聚酯切片制备方法如下:
29.1)、以废聚酯纺织品为原料,通过破碎、除油、然后粉碎生产再生聚酯泡料;
30.2)、以再生聚酯泡料为原料,使用硫化床热风连续干燥系统进行干燥,然后采用螺杆挤出法,挤出温度为265~285℃,并使用乙二醇钛系降解催化剂为改性剂,进行再生聚酯泡料的破碎和催化剂的熔融混合,然后进行缩聚反应,得到低粘度再生聚酯切片。
31.优选的,所述第一料筒中的高粘度再生聚酯切片和第二料筒中的低粘度再生聚酯切片质量比为35~65:65~435。
32.优选的,所述高粘度再生聚酯切片中乙二醇钛系降解催化剂的物质含量为400~1800ppm,所述高粘度再生聚酯切片的特性粘度为0.95~1.15dl/g。
33.优选的,所述低粘度再生聚酯切片中乙二醇钛系降解催化剂的物质含量为600~2200ppm,所述低粘度再生聚酯切片的特性粘度为0.50~0.58dl/g。
34.优选的,所述再生聚酯泡料粒径为3-18mm,所述再生聚酯泡料使用硫化床热风连续干燥系统干燥温度控制为110-150℃,干燥时间为10-30分钟,所述再生聚酯泡料缩聚反应温度为265~285℃,真空度控制在60-100pa,缩聚反应时间2~4h。
35.优选的,所述复合纺丝箱中纺丝温度为270~280℃。
36.优选的,所述吹风甬道环吹风截面风速为2~2.6m/mi n且风温为18℃。
37.优选的,所述卷绕机纺织速度为1200~1500m/mi n。
38.优选的,所述牵伸浴牵伸温度为65~75℃且拉伸倍数1.0~1.15倍。
39.优选的,所述蒸汽牵伸温度90~110℃且拉伸倍数2.4~3.0倍。
40.优选的,所述松弛热定型温度为45~65℃。
41.(三)有益效果
42.本发明提供了一种再生并列复合仿羽绒聚酯纤维的制备方法及设备。具备以下有益效果:
43.1、以废聚酯瓶片和废聚酯纺织品为原料,解决了废旧聚酯材料的再生利用问题,同时以瓶片的高粘度通过催化剂进行熔融缩聚过程,利用乙二醇钛系催化剂的聚酯缩聚催化性,提高再生聚酯粘度,从而提高并列复合纺丝全过程的延展性和卷曲性,所制备的再生并列复合仿羽绒聚酯纤维延展性好,回弹率高,蓬松度好,原料成本低,广泛应用于家纺、装饰设计、填充等行业。
44.2、通过第一滑动组件和第二滑动组件,在需要清理维护并列复合纺丝分配板或喷丝板时,仅需松开对应的锁紧螺丝,即可将并列复合纺丝分配板或喷丝板单独分开且又不会脱落,清理结束后回装也非常方便。
附图说明
45.图1为本发明结构示意图;
46.图2为第一滑动组件中清理并列复合纺丝分配板时状态示意图;
47.图3为第一滑动组件中清理喷丝板时状态示意图;
48.图4为复合纺丝箱内部结构剖视图;
49.图5为喷丝板结构俯视图;
50.图6为图5中a处的局部放大图。
51.其中,1、机架;2、背板;3、第一螺杆挤出机;4、第一料筒;5、第一静态混合器;6、第一增压泵;7、第一计量泵;8、第二螺杆挤出机;9、第二料筒;10、第二静态混合器;11、第二增压泵;12、第二计量泵;13、复合纺丝箱;14、保温气体进口管;15、保温气体出口管;16、并列复合纺丝分配板;17、喷丝板;18、第一滑动座;19、第二滑动座;20、第三滑动座;21、第一滑杆;22、安装法兰;23、吹风甬道;24、第四滑动座;25、第二滑杆;26、上油轮;27、导向轮;28、卷绕机;29、限位螺丝;30、锁紧螺丝;31、第一保温内胆;32、第二保温内胆;33、保温腔;34、保温夹层;35、喷丝孔。
具体实施方式
52.下面将结合本发明实施例中的附图,对本发明实施例中的技术方案进行清楚、完整地描述,显然,所描述的实施例仅仅是本发明一部分实施例,而不是全部的实施例。基于本发明中的实施例,本领域普通技术人员在没有做出创造性劳动前提下所获得的所有其他实施例,都属于本发明保护的范围。
53.实施例:
54.如图1-6所示,本发明实施例提供一种再生并列复合仿羽绒聚酯纤维的制备设备,包括机架1,机架1后壁固定连接有背板2;固定连接在机架1上壁且分别位于两端的第一螺杆挤出机3、第二螺杆挤出机8,第一螺杆挤出机3、第二螺杆挤出机8进进口端分别固定连接有第一料筒4、第二料筒9,第一料筒4用于装入高粘度再生聚酯切片,第二料筒9用于装入低粘度再生聚酯切片;依次固定连接在第一螺杆挤出机3出口端的第一静态混合器5、第一增压泵6以及第一计量泵7;依次固定连接在第二螺杆挤出机8出口端的第二静态混合器10、第二增压泵11以及第二计量泵12,第一计量泵7、第二计量泵12可以准确计量熔体用量,使得配比准确;固定连接在背板2前壁且靠近上端的复合纺丝箱13;设置在复合纺丝箱13内部用于对熔体保温的保温结构;固定连接在复合纺丝箱13下壁用于分配熔体的并列复合纺丝分配板16;固定连接在并列复合纺丝分配板16下壁的喷丝板17,喷丝板17内壁设置有多组喷丝孔35,喷丝孔35呈圆周等分阵列形式分布在喷丝板17内壁,喷丝孔35横截面形状接近s型;通过安装法兰22固定连接在喷丝板17下壁的吹风甬道23,吹风甬道23为全封闭式环吹风冷却形式;设置在复合纺丝箱13、并列复合纺丝分配板16、喷丝板17之间以及喷丝板17与安装法兰22之间用于方便检修的第一滑动组件和第二滑动组件,第一滑动组件、第二滑动组件上均设置有用于防止脱落的限位组件和用于固定位置的锁紧组件;依次设置在背板2前壁且位于吹风甬道23下侧的上油轮26、导向轮27;固定连接在机架1内侧下壁且靠近右侧的卷绕机28。
55.保温结构包括第一保温内胆31、第二保温内胆32、保温气体进口管14、保温气体出口管15以及保温夹层34,第一保温内胆31、第二保温内胆32呈左右分布设置在复合纺丝箱13内部,第一计量泵7出口端与第一保温内胆31、第二计量泵12出口端与第二保温内胆32均通过管道贯通,保温夹层34设置在复合纺丝箱13内部且位于第一保温内胆31、第二保温内胆32外壁,两组保温腔33,保温夹层34与第一保温内胆31之间以及保温夹层34与第二保温内胆32之间均设置有保温腔33,保温气体进口管14、保温气体出口管15均固定连接在复合纺丝箱13侧壁且分别靠近上壁和下壁,保温气体进口管14、保温气体出口管15外壁均贯穿复合纺丝箱13侧壁以及保温夹层34至保温腔33内侧,通过保温气体进口管14、保温气体出口管15以及保温腔33,通入气相热媒vp-1后可形成保温循环。
56.第一滑动组件包括第一滑动座18、第二滑动座19、第三滑动座20以及第一滑杆21,第一滑动座18、第二滑动座19以及第三滑动座20分别固定连接在复合纺丝箱13、并列复合纺丝分配板16以及喷丝板17外壁,第一滑杆21固定连接在第三滑动座20内壁,第一滑杆21远离第三滑动座20的一端外壁依次贯穿第二滑动座19、第一滑动座18至第一滑动座18上侧,第二滑动组件包括第四滑动座24、第二滑杆25,第四滑动座24固定连接在安装法兰22下壁且位于吹风甬道23外侧,第二滑杆25固定连接在喷丝板17下壁,第二滑杆25远离喷丝板17的一端外壁依次贯穿安装法兰22、第四滑动座24至第四滑动座24下侧,通过第一滑动组
件、第二滑动组件,可以在需要清理并列复合纺丝分配板16或者喷丝板17时能够进行单独分解,不需要完全拆除,清理非常迅速,且清理结束后回装也非常方便。
57.锁紧组件包括多组锁紧螺丝30,多组锁紧螺丝30分别固定连接在第一滑动座18、第二滑动座19、第三滑动座20以及第四滑动座24侧壁,第一滑动座18、第二滑动座19、第三滑动座20与第一滑杆21之间以及第四滑动座24与第二滑杆25之间分别通过多组锁紧螺丝30固定连接,通过锁紧或松开不同的锁紧螺丝30,可以实现单独打开并列复合纺丝分配板16或者喷丝板17。
58.限位组件包括两组限位螺丝29,两组限位螺丝29分别螺纹连接在第一滑杆21远离第三滑动座20的一端外壁以及第二滑杆25远离喷丝板17的一端外壁,通过限位组件可以确保在清理并列复合纺丝分配板16或者喷丝板17时不会脱落。
59.一种再生并列复合仿羽绒聚酯纤维的制备方法,制备方法包括如下步骤:
60.s1、将高粘度再生聚酯切片和低粘度再生聚酯切片分别投入第一料筒4、第二料筒9,第一料筒4中的高粘度再生聚酯切片和第二料筒9中的低粘度再生聚酯切片质量比为35~65:65~435,再分别经过第一螺杆挤出机3、第二螺杆挤出机8连续干燥熔融挤出,进一步分别通过第一静态混合器5、第二静态混合器10充分混合;
61.s2、将上两路熔体分别通过第一增压泵6、第二增压泵11进行增压,再经过第一计量泵7、第二计量泵12准确计量后分别送入复合纺丝箱13内部的第一保温内胆31以及第二保温内胆32中,复合纺丝箱13中纺丝温度为270~280℃;
62.s3、经保温气体进口管14通入气相热媒vp-1进入保温腔33并从保温气体出口管15吹出形成循环为纺丝熔体保温,并保证两种纺丝熔体在维持各自不同的温度情况下进入并列复合纺丝分配板16,经并列复合纺丝分配板16分配后通过喷丝板17上的喷丝孔35喷出进行并列复合熔体纺丝,形成并列型丝束;
63.s4、经吹风甬道23全密闭式环吹风冷却、上油轮26上油后经导向轮27导向再经卷绕机28卷绕,吹风甬道23环吹风截面风速为2~2.6m/mi n且风温为18℃,卷绕机28纺织速度为1200~1500m/mi n;
64.s5、卷绕后丝束经过往复落丝、集束、导丝、牵伸浴牵伸、蒸汽牵伸、机械卷曲、松弛热定型、切断、打包工序制备得到再生并列复合仿羽绒聚酯纤维,牵伸浴牵伸温度为65~75℃且拉伸倍数1.0~1.15倍,蒸汽牵伸温度90~110℃且拉伸倍数2.4~3.0倍,松弛热定型温度为45~65℃。
65.高粘度再生聚酯切片制备方法如下:
66.1)、以废聚酯瓶片为原料,通过分拣、脱标、破碎、碱洗、漂洗生产再生聚酯瓶片;
67.2)、以再生聚酯瓶片为原料,使用硫化床热风连续干燥系统进行干燥,然后通过螺杆熔融送入反应釜,挤出温度为255~268℃,并使用乙二醇钛系降解催化剂为改性剂,进行再生瓶片的破碎和催化剂的熔融混合,然后进行缩聚反应,得到高粘度再生聚酯切片,高粘度再生聚酯切片中乙二醇钛系降解催化剂的物质含量为400~1800ppm,高粘度再生聚酯切片的特性粘度为0.95~1.15dl/g。
68.低粘度再生聚酯切片制备方法如下:
69.1)、以废聚酯纺织品为原料,通过破碎、除油、然后粉碎生产再生聚酯泡料;
70.2)、以再生聚酯泡料为原料,使用硫化床热风连续干燥系统进行干燥,然后采用螺
杆挤出法,挤出温度为265~285℃,并使用乙二醇钛系降解催化剂为改性剂,进行再生聚酯泡料的破碎和催化剂的熔融混合,然后进行缩聚反应,得到低粘度再生聚酯切片,低粘度再生聚酯切片中乙二醇钛系降解催化剂的物质含量为600~2200ppm,低粘度再生聚酯切片的特性粘度为0.50~0.58dl/g,再生聚酯泡料粒径为3-18mm,再生聚酯泡料使用硫化床热风连续干燥系统干燥温度控制为110-150℃,干燥时间为10-30分钟,再生聚酯泡料缩聚反应温度为265~285℃,真空度控制在60-100pa,缩聚反应时间2~4h。
71.尽管已经示出和描述了本发明的实施例,对于本领域的普通技术人员而言,可以理解在不脱离本发明的原理和精神的情况下可以对这些实施例进行多种变化、修改、替换和变型,本发明的范围由所附权利要求及其等同物限定。