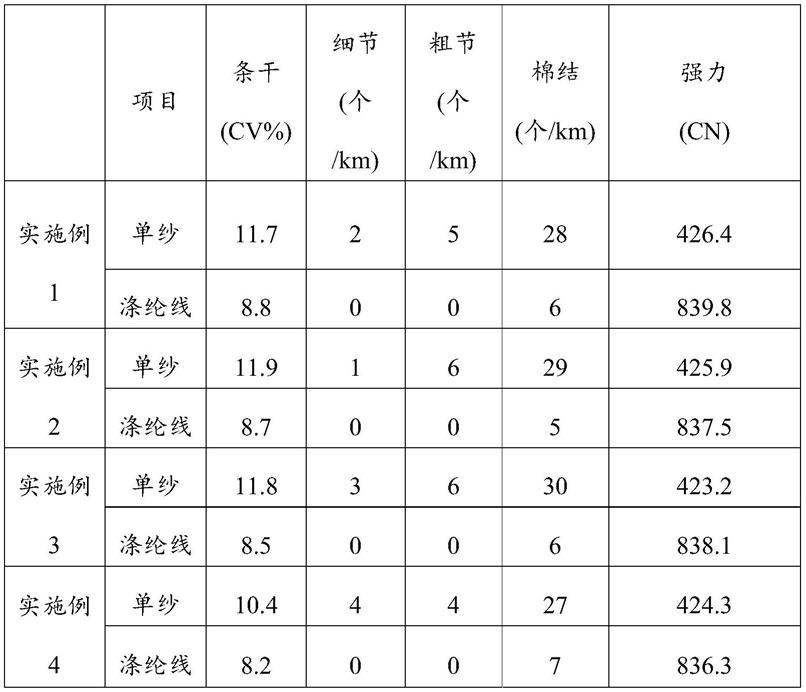
1.本发明涉及纺织技术领域,具体涉及一种涤纶线及其生产方法。
背景技术:
2.涤纶纤维是一种品质优良的合成纤维,用以制得的缝线强力高,在各类缝线中仅次于尼龙线,居第二位,而且湿态时不会降低其强度。它的缩水率很小,经过适当定型后收缩小于1%,因此缝制的线迹能始终保持平挺美观,无皱缩。耐磨性仅次于锦纶。回潮率低,有良好的耐高温、耐低温、耐光性和耐水性。所以,涤纶线是使用极为广泛的品种,在不少场合,取代了棉缝纫线。涤纶线用途广泛,可用于棉织物、化纤织物与混纺织物的服装缝制,也可用于缝针织外衣。特制的涤纶线还是鞋帽皮革行业的优良用线。
3.但涤纶纤维吸湿性低、导电性差,原料蓬松,纺纱过程中易产生静电和搓绕,使得棉结增加,影响成纱质量。
技术实现要素:
4.本发明的目的在于克服上述技术不足,提供一种涤纶线的生产方法,解决现有技术中涤纶线的生产过程中棉结数量多的技术问题。
5.为达到上述技术目的,本发明的技术方案提供一种涤纶线的生产方法,包括以下步骤:
6.将涤纶纤维作为原料依次经清梳工序、并条工序、粗砂工序、细纱工序、络筒工序和倍捻工序加工;
7.其中,所述清梳工序中,给棉板与刺辊隔距14-15英丝,锡林与盖板5点隔距为8英丝
×
7英丝
×
7英丝
×
7英丝
×
8英丝,刺辊与小漏底入口隔距10-12mm,出口隔距2-3mm,梳棉干重定量为18.2-18.5g/5m;
8.所述细纱工序中,捻度为84-85捻/10cm,捻向为s捻;
9.所述倍捻工序中,单纱经2股成线,捻度为80-82捻/10cm,捻向为z捻。
10.进一步地,所述涤纶纤维的比强为5.8-6.1cn/dtex、断裂伸长率为21.8-22.5%、线密度为1.33-1.5dtex、长度为38-40mm。
11.进一步地,所述粗纱工序中,粗纱捻度为2.1-2.2捻/10cm。
12.进一步地,所述粗纱工序中,罗拉隔距采用12mm
×
26mm
×
45mm,后区牵伸为1.2-1.3倍。
13.进一步地,所述粗纱工序中,钳口隔距为9-9.5mm,粗纱干重定量为4.73-4.8克/10米,机械牵伸为7.18-7.2倍。
14.进一步地,所述粗纱工序中,锭速为550-560r/min。
15.进一步地,所述细纱工序中,机械牵伸倍数32-34倍,罗拉隔距为17mm
×
38mm。
16.进一步地,所述细纱工序中,后区牵伸倍数为1.2-1.4倍,钳口隔距2.5-2.8mm,前罗拉直径27-28mm,前罗拉转速为190-200r/min。
17.进一步地,所述并条工序中,经过二道并和,一并8根并合,干重定量17.2g/5米,罗拉隔距10mm
×
14mm
×
26mm,喇叭口直径为3-3.2mm;二并8根并合,干重定量17g/5米,罗拉隔距12mm
×
20mm,喇叭口直径3.2-3.4mm。
18.此外,本发明还提出一种涤纶线,由上述制备方法制备得到。
19.与现有技术相比,本发明的有益效果包括:将涤纶纤维作为原料依次经清梳工序、并条工序、粗砂工序、细纱工序、络筒工序和倍捻工序加工;其中,所述清梳工序中,给棉板与刺辊隔距14-15英丝,锡林与盖板5点隔距为8英丝
×
7英丝
×
7英丝
×
7英丝
×
8英丝,刺辊与小漏底入口隔距10-12mm,出口隔距2-3mm,梳棉干重定量为18.2-18.5g/5m;所述细纱工序中,捻度为84-85捻/10cm,捻向为s捻;所述倍捻工序中,单纱经2股成线,捻度为80-82捻/10cm,捻向为z捻,得到支数为40支的高强涤纶线,且棉结少。
20.所得的涤纶线强度高、耐磨性好、缩水率低、吸湿性及耐热性好,耐腐蚀、不易霉烂、不会虫蛀,色牢度好、不褪色、不变色,可广泛地应用于棉织品、化纤和混纺织物的服装缝制中。
具体实施方式
21.为了使本发明的目的、技术方案及优点更加清楚明白,以下结合实施例,对本发明进行进一步详细说明。应当理解,此处所描述的具体实施例仅仅用以解释本发明,并不用于限定本发明。
22.本具体实施方式提供了一种涤纶线的生产方法,包括以下步骤:
23.将涤纶纤维作为原料依次经清梳工序、并条工序、粗砂工序、细纱工序、络筒工序和倍捻工序加工;所述涤纶纤维的比强为5.8-6.1cn/dtex、断裂伸长率为21.8-22.5%、线密度为1.33-1.5dtex、长度为38-40mm;
24.其中,所述清梳工序中,给棉板与刺辊隔距14-15英丝,锡林与盖板5点隔距为8英丝
×
7英丝
×
7英丝
×
7英丝
×
8英丝,刺辊与小漏底入口隔距10-12mm,出口隔距2-3mm,梳棉干重定量为18.2-18.5g/5m;
25.所述并条工序中,经过二道并和,一并8根并合,干重定量17.2g/5米,罗拉隔距10mm
×
14mm
×
26mm,喇叭口直径为3-3.2mm;二并8根并合,干重定量17g/5米,罗拉隔距12mm
×
20mm,喇叭口直径3.2-3.4mm;
26.所述粗纱工序中,粗纱捻度为2.1-2.2捻/10cm,罗拉隔距采用12mm
×
26mm
×
45mm,后区牵伸为1.2-1.3倍,钳口隔距为9-9.5mm,粗纱干重定量为4.73-4.8克/10米,机械牵伸为7.18-7.2倍,锭速为550-560r/min;
27.所述细纱工序中,捻度为84-85捻/10cm,捻向为s捻,钢领的型号为pg1-4254,所用钢丝圈的型号为w321 38#;机械牵伸倍数32-34倍,罗拉隔距为17mm
×
38mm;后区牵伸倍数为1.2-1.4倍,钳口隔距2.5-2.8mm,前罗拉直径27-28mm,前罗拉转速为190-200r/min;
28.所述倍捻工序中,单纱经2股成线,捻度为80-82捻/10cm,捻向为z捻。
29.本具体实施方式还包括一种涤纶线,由上述制备方法制备得到。
30.实施例1
31.本实施例提出一种涤纶线,由以下方法生产得到:
32.将涤纶纤维作为原料依次经清梳工序、并条工序、粗砂工序、细纱工序、络筒工序
和倍捻工序加工;所述涤纶纤维的比强为6.1cn/dtex、断裂伸长率为21.8%、线密度为1.33dtex、长度为38mm;
33.具体地,所述清梳工序中,涤纶纤维在抓棉圆台上成卷,棉卷干重定量为375g/m;原料蓬松,纺纱过程中易产生静电和搓绕,使得棉结增加。梳棉工序中合理设置梳棉隔距,给棉板与刺辊隔距14英丝,锡林与盖板5点隔距为8英丝
×
7英丝
×
7英丝
×
7英丝
×
8英丝,刺辊与小漏底入口隔距10mm,出口隔距2mm,梳棉干重定量为18.2g/5m;
34.所述并条工序中,经过二道并和,一并8根并合,干重定量17.2g/5米,罗拉隔距10mm
×
14mm
×
26mm,喇叭口直径为3mm;二并8根并合,干重定量17g/5米,罗拉隔距12mm
×
20mm,喇叭口直径3.2mm;
35.所述粗纱工序中,粗纱捻度为2.1捻/10cm,罗拉隔距采用12mm
×
26mm
×
45mm,后区牵伸为1.2倍,钳口隔距为9mm,粗纱干重定量为4.73克/10米,机械牵伸为7.18倍,锭速为550r/min;
36.所述细纱工序中,捻度为84捻/10cm,捻向为s捻,钢领的型号为pg1-4254,所用钢丝圈的型号为w321 38#;机械牵伸倍数32倍,罗拉隔距为17mm
×
38mm;后区牵伸倍数为1.2倍,钳口隔距2.5mm,前罗拉直径27mm,前罗拉转速为190r/min;
37.所述络筒工序中,单纱络筒在日本村田的自动络筒机上生产,棉结n:350%
×
0.5cm、短粗s:200%
×
2.1cm、长粗l:50%
×
32cm、细节t:-35%
×
30cm;
38.所述倍捻工序中,单纱经2股成线,捻度为80捻/10cm,捻向为z捻。
39.实施例2
40.本实施例提出一种涤纶线,由以下方法生产得到:
41.将涤纶纤维作为原料依次经清梳工序、并条工序、粗砂工序、细纱工序、络筒工序和倍捻工序加工;所述涤纶纤维的比强为6.1cn/dtex、断裂伸长率为21.8%、线密度为1.33dtex、长度为38mm;
42.具体地,所述清梳工序中,涤纶纤维在抓棉圆台上成卷,棉卷干重定量为375g/m;原料蓬松,纺纱过程中易产生静电和搓绕,使得棉结增加。梳棉工序中合理设置梳棉隔距,给棉板与刺辊隔距15英丝,锡林与盖板5点隔距为8英丝
×
7英丝
×
7英丝
×
7英丝
×
8英丝,刺辊与小漏底入口隔距12mm,出口隔距3mm,梳棉干重定量为18.3g/5m;
43.所述并条工序中,经过二道并和,一并8根并合,干重定量17.2g/5米,罗拉隔距10mm
×
14mm
×
26mm,喇叭口直径为3.2mm;二并8根并合,干重定量17g/5米,罗拉隔距12mm
×
20mm,喇叭口直径3.3mm;
44.所述粗纱工序中,粗纱捻度为2.2捻/10cm,罗拉隔距采用12mm
×
26mm
×
45mm,后区牵伸为1.3倍,钳口隔距为9.5mm,粗纱干重定量为4.75克/10米,机械牵伸为7.2倍,锭速为560r/min;
45.所述细纱工序中,捻度为85捻/10cm,捻向为s捻,钢领的型号为pg1-4254,所用钢丝圈的型号为w321 38#;机械牵伸倍数33倍,罗拉隔距为17mm
×
38mm;后区牵伸倍数为1.3倍,钳口隔距2.6mm,前罗拉直径28mm,前罗拉转速为200r/min;
46.所述络筒工序中,单纱络筒在日本村田的自动络筒机上生产,棉结n:350%
×
0.5cm、短粗s:200%
×
2.1cm、长粗l:50%
×
32cm、细节t:-35%
×
30cm;
47.所述倍捻工序中,单纱经2股成线,捻度为81捻/10cm,捻向为z捻。
48.实施例3
49.本实施例提出一种涤纶线,由以下方法生产得到:
50.将涤纶纤维作为原料依次经清梳工序、并条工序、粗砂工序、细纱工序、络筒工序和倍捻工序加工;所述涤纶纤维的比强为6.1cn/dtex、断裂伸长率为21.8%、线密度为1.33dtex、长度为38mm;
51.具体地,所述清梳工序中,涤纶纤维在抓棉圆台上成卷,棉卷干重定量为375g/m;原料蓬松,纺纱过程中易产生静电和搓绕,使得棉结增加。梳棉工序中合理设置梳棉隔距,给棉板与刺辊隔距15英丝,锡林与盖板5点隔距为8英丝
×
7英丝
×
7英丝
×
7英丝
×
8英丝,刺辊与小漏底入口隔距11mm,出口隔距2mm,梳棉干重定量为18.5g/5m;
52.所述并条工序中,经过二道并和,一并8根并合,干重定量17.2g/5米,罗拉隔距10mm
×
14mm
×
26mm,喇叭口直径为3.1mm;二并8根并合,干重定量17g/5米,罗拉隔距12mm
×
20mm,喇叭口直径3.4mm;
53.所述粗纱工序中,粗纱捻度为2.1捻/10cm,罗拉隔距采用12mm
×
26mm
×
45mm,后区牵伸为1.2倍,钳口隔距为9.2mm,粗纱干重定量为4.8克/10米,机械牵伸为7.19倍,锭速为550r/min;
54.所述细纱工序中,捻度为84捻/10cm,捻向为s捻,钢领的型号为pg1-4254,所用钢丝圈的型号为w321 38#;机械牵伸倍数34倍,罗拉隔距为17mm
×
38mm;后区牵伸倍数为1.4倍,钳口隔距2.8mm,前罗拉直径27mm,前罗拉转速为195r/min;
55.所述络筒工序中,单纱络筒在日本村田的自动络筒机上生产,棉结n:350%
×
0.5cm、短粗s:200%
×
2.1cm、长粗l:50%
×
32cm、细节t:-35%
×
30cm;
56.所述倍捻工序中,单纱经2股成线,捻度为80捻/10cm,捻向为z捻。
57.实施例4
58.本实施例提出一种涤纶线,由以下方法生产得到:
59.将涤纶纤维作为原料依次经清梳工序、并条工序、粗砂工序、细纱工序、络筒工序和倍捻工序加工;所述涤纶纤维的比强为6.1cn/dtex、断裂伸长率为21.8%、线密度为1.33dtex、长度为38mm;
60.具体地,所述清梳工序中,涤纶纤维在抓棉圆台上成卷,棉卷干重定量为375g/m;原料蓬松,纺纱过程中易产生静电和搓绕,使得棉结增加。梳棉工序中合理设置梳棉隔距,给棉板与刺辊隔距14英丝,锡林与盖板5点隔距为8英丝
×
7英丝
×
7英丝
×
7英丝
×
8英丝,刺辊与小漏底入口隔距10mm,出口隔距3mm,梳棉干重定量为18.4g/5m;
61.所述并条工序中,经过二道并和,一并8根并合,干重定量17.2g/5米,罗拉隔距10mm
×
14mm
×
26mm,喇叭口直径为3mm;二并8根并合,干重定量17g/5米,罗拉隔距12mm
×
20mm,喇叭口直径3.3mm;
62.所述粗纱工序中,粗纱捻度为2.1捻/10cm,罗拉隔距采用12mm
×
26mm
×
45mm,后区牵伸为1.3倍,钳口隔距为9.3mm,粗纱干重定量为4.77克/10米,机械牵伸为7.18倍,锭速为550r/min;
63.所述细纱工序中,捻度为85捻/10cm,捻向为s捻,钢领的型号为pg1-4254,所用钢丝圈的型号为w321 38#;机械牵伸倍数32倍,罗拉隔距为17mm
×
38mm;后区牵伸倍数为1.2倍,钳口隔距2.7mm,前罗拉直径28mm,前罗拉转速为190r/min;
64.所述络筒工序中,单纱络筒在日本村田的自动络筒机上生产,棉结n:350%
×
0.5cm、短粗s:200%
×
2.1cm、长粗l:50%
×
32cm、细节t:-35%
×
30cm;
65.所述倍捻工序中,单纱经2股成线,捻度为82捻/10cm,捻向为z捻。
66.性能测试
67.根据纺织领域的常规方法或国家标准对实施例1生产出的高强涤纶线进行相关性能的测试,测试结果见表1。需要说明的是,本发明中,纱线截面小于平均截面的50%为细纱细节、纱线截面大于或等于平均截面的50%细纱粗节。
68.表1实施例1-4生产出的单纱及涤纶线的性能测试结果
[0069][0070]
从表1可以看出,各实施例得到的单纱和涤纶线都具有较好的强力,而且细节和粗节少,特别是涤纶线没有细节和粗节,另外涤纶线的棉结数量也较少,可低至5个棉结。
[0071]
以上所述本发明的具体实施方式,并不构成对本发明保护范围的限定。任何根据本发明的技术构思所做出的各种其他相应的改变与变形,均应包含在本发明权利要求的保护范围内。