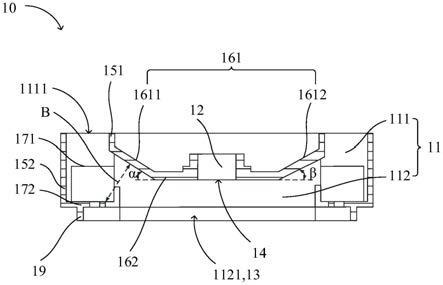
1.本实用新型涉及一种燃烧器以及炊具。
背景技术:
2.现有技术中,分体式燃烧器一般包括底座和内环火盖、外环火盖,并由底座和内环火盖围设形成内环混气室,底座和外环火盖围设形成外环混气室。如图1所示,底座10’通常沿外环送气路径依次包括外环进气口11’、外环传气通道12’和环形的混气腔13’。但是,由于外环传气通道是一个通道结构,因此,在制作时不能采用压铸工艺成形,而只能采用浇筑工艺成形。浇筑工艺需要通过人工制作砂芯,造成制造成本高,形成的成品较为粗糙,而且成品的质量不稳定,容易出现砂眼等而影响燃烧器性能。
技术实现要素:
3.本实用新型要解决的技术问题是为了克服现有技术不能采用压铸工艺制作而造成制造成本高、成品的质量不稳定的缺陷,提供一种燃烧器以及炊具。
4.本实用新型是通过下述技术方案来解决上述技术问题:
5.一种燃烧器,所述燃烧器包括底座、以及覆盖在所述底座上的外环火盖,所述底座与所述外环火盖围合形成外环混气室,所述外环混气室包括设置于所述底座内的外环混气腔,其特点在于,
6.所述外环混气腔包括具有顶部敞口的由上至下凹进的第一混气腔、以及位于所述第一混气腔的下方的具有底部敞口的由下至上凹进的第二混气腔,所述第一混气腔为环状,所述第二混气腔沿所述第一混气腔的径向延伸,且相对的两端均与所述第一混气腔直接连通,所述第二混气腔的底部敞口为外环进气口,且部分及另一部分的所述第一混气腔分别位于所述外环进气口沿所述第一混气腔的径向延伸的相对的两端的正上方。
7.在本技术方案中,采用上述结构设置,使底座为上下对冲结构,不再需要设置外环传气通道结构,从而能够采用压铸工艺形成底座,降低了制造成本,提高了成品的质量;并且,由于减少了气体在外环传气通道传输过程中的动力损失,还具有提高燃烧器的性能的有益效果。相较于现有技术中,传气路径需要经过外环传气通道,而导致传气路径的截面积的减少,而造成传气的节流;在本技术方案中,由于不再设置外环传气通道,外环进气口直接连通外环混气腔,从而能够避免造成传气的节流,并且增加二次空气流动范围的有益技术效果。
8.可选地,所述底座包括:内环壁和外环壁、顶壁、底壁以及相对设置的第一侧壁和第二侧壁,所述内环壁和外环壁呈环形并且同心间隔设置;
9.所述第一侧壁和第二侧壁均沿所述第一混气腔的径向设置,所述第一侧壁和所述第一侧壁的两端均分别连接于所述外环壁的不同位置;
10.所述顶壁沿所述第一混气腔的径向设置,且所述顶壁的两端分别连接于所述内环壁的不同位置,所述顶壁位于所述第一侧壁和所述第二侧壁的上方,所述顶壁相对的两侧
分别与所述第一侧壁和所述第二侧壁连接;
11.所述底壁包括第一部分和第二部分,所述第一部分位于所述第一侧壁和第二侧壁的上方,所述第二部分位于所述第一侧壁与所述第二侧壁的下方;所述第一部分连接于所述内环壁和外环壁之间;所述第二部分沿所述第一混气腔的径向设置,所述第二部分的两端分别与所述外环壁连接,且所述第二部分的相对的两侧分别与第一侧壁和第二侧壁连接,所述外环进气口开设于所述第二部分。
12.在本技术方案中,采用上述结构设置,提供底座的具体结构以形成上下对冲结构。
13.可选地,所述内环壁、所述外环壁、所述底壁的第一部分围合形成所述第一混气腔;
14.所述顶壁、所述第一侧壁、所述第二侧壁和所述底壁的第二部分围合形成所述第二混气腔。
15.在本技术方案中,采用上述结构设置,提供一种形成第一混气腔和第二混气腔的具体结构。
16.可选地,所述燃烧器还包括内环火盖,所述底座与所述内环火盖围合形成内环混气室,所述内环混气室包括设置于所述底座内的内环混气腔,所述内环混气腔的内环进气口内置于所述外环进气口中。
17.在本技术方案中,采用上述结构设置,提供内环混气腔以及内环进气口的设置方式,使底座的结构更为紧凑。
18.可选地,所述内环进气口开设于所述顶壁上,且所述内环混气腔位于与所述顶壁的上方。
19.在本技术方案中,采用上述结构设置,提供内环混气腔以及内环进气口的具体设置位置,使底座的结构更为紧凑。
20.可选地,所述顶壁靠近所述内环壁的一端沿所述第一混气腔的径向逐渐向上延伸以形成一倾斜壁。
21.在本技术方案中,通过设置倾斜壁,扩大了进入第一混气腔的进气路径的最小截面的面积,有助于燃烧器的性能提升;并且倾斜壁可以充当内环聚能圈使用。
22.可选地,所述倾斜壁所在的平面与水平面的夹角为45度-60度。
23.在本技术方案中,通过进一步限定倾斜壁所在的平面与水平面的夹角的度数范围,以最大化进入第一混气腔的进气路径的最小截面的面积。
24.可选地,所述顶壁包括靠近所述内环壁设置的第一倾斜壁和第二倾斜壁、以及连接于第一倾斜壁和第二倾斜壁之间的连接部,所述连接部沿水平方向设置。
25.在本技术方案中,采用上述结构设置,使第二混气腔与第一混气腔连通的两端均具有倾斜壁,扩大了进入第一混气腔的进气路径的最小截面的面积,有助于燃烧器的性能提升;通过在中间位置沿水平方向设置连接部,以避免第一倾斜壁和第二倾斜壁太靠近内环火焰。
26.可选地,所述第一倾斜壁和第二倾斜壁对称设置。
27.在本技术方案中,采用上述结构设置,使第二混气腔与第一混气腔连通的两端的进气更为均匀。
28.可选地,所述底座还包括密封台阶,所述密封台阶设于所述底壁的第二部分的下
表面,且沿所述外环进气口的外周缘设置。
29.在本技术方案中,通过设置密封台阶,以实现底座与位于其下方的基座之间的密封,避免漏火现象的产生。
30.可选地,所述底座一体压铸成型。
31.在本技术方案中,底座通过一体压铸成型,能够达到降低制造成本,提高成品的质量的有益技术效果。
32.一种炊具,其特点在于,所述炊具包括如上所述的燃烧器。
33.本实用新型的积极进步效果在于:
34.本实用新型的燃烧器以及炊具,通过设置底座为上下对冲结构,不再需要设置外环传气通道结构,从而能够采用压铸工艺形成底座,降低了制造成本,提高了成品的质量;并且,由于减少了气体在外环传气通道传输过程中的动力损失,还具有提高燃烧器的性能的有益效果。相较于现有技术中,传气路径需要经过外环传气通道,而导致传气路径的截面积的减少,而造成传气的节流;在本技术方案中,由于不再设置外环传气通道,外环进气口直接连通外环混气腔,从而能够避免造成传气的节流,并且增加二次空气流动范围的有益技术效果。
附图说明
35.图1为现有技术中的底座的立体剖视结构示意图。
36.图2为本实用新型一实施例的燃烧器的立体结构示意图。
37.图3为本实用新型一实施例的燃烧器的剖视结构示意图。
38.图4为本实用新型一实施例的底座的立体结构示意图。
39.图5为本实用新型一实施例的另一角度的底座的立体结构示意图。
40.图6为本实用新型一实施例的底座的俯视结构示意图。
41.图7为图6中沿a-a方向的剖视结构示意图。
42.图8为本实用新型一实施例的底座的仰视结构示意图。
具体实施方式
43.下面举个较佳实施例,并结合附图来更清楚完整地说明本实用新型。
44.如图2和图3所示,本实施例提供一种燃烧器1,燃烧器1包括底座10、以及覆盖在底座10上的外环火盖20、以及内环火盖30。
45.底座10与外环火盖20围合形成外环混气室40,外环混气室40包括设置于底座10内的外环混气腔。底座10与内环火盖30围合形成内环混气室50,内环混气室50包括设置于底座10内的内环混气腔。
46.如图4至图8所示,具体地,外环混气腔11包括具有顶部敞口1111的由上至下凹进的第一混气腔111、以及位于第一混气腔111的下方的具有底部敞口1121的由下至上凹进的第二混气腔112。第一混气腔111为环状,第二混气腔112沿第一混气腔111的径向p延伸,且相对的两端(即指第二混气腔112的沿第一混气腔111的径向p相对的两端)均与第一混气腔111直接连通。第二混气腔112的底部敞口1121为外环进气口13。且部分及另一部分的第一混气腔111分别位于外环进气口13沿第一混气腔111的径向p延伸的相对的两端的正上方,
也就是说,外环进气口13沿第一混气腔111的径向p延伸的相对的两端在竖直方向h的正投影均位于第一混气腔111在竖直方向h的正投影中,即通过扩大外环进气口13沿第一混气腔111的径向p的相对两端至环形的第一混气腔111的正下方,而使底座的整体结构不会有沿径向设置的环形闭合的通道结构。
47.这样,使底座10为上下对冲结构,不再需要设置外环传气通道结构,从而能够采用压铸工艺制作底座10,降低了制造成本,提高了成品的质量;并且,由于减少了气体在外环传气通道传输过程中的动力损失,还具有提高燃烧器1的性能的有益效果。相较于现有技术中,传气路径需要经过外环传气通道,而导致传气路径的截面积的减少,而造成传气的节流;在本技术方案中,由于不再设置外环传气通道,外环进气口13直接连通外环混气腔11,从而能够避免造成传气的节流,并且增加二次空气流动范围的有益技术效果。
48.底座10包括:内环壁151和外环壁152、顶壁16、底壁17以及相对设置的第一侧壁181和第二侧壁182,内环壁151和外环壁152呈环形并且同心间隔设置。
49.第一侧壁181和第二侧壁182均沿第一混气腔111的径向p设置,第一侧壁181和第一侧壁181的两端均分别连接于外环壁152的不同位置。
50.顶壁16沿第一混气腔111的径向p设置,且顶壁16的两端分别连接于内环壁151的不同位置,顶壁16位于第一侧壁181和第二侧壁182的上方,顶壁16相对的两侧分别与第一侧壁181和第二侧壁182连接。
51.底壁17包括第一部分171和第二部分172,第一部分171位于第一侧壁181和第二侧壁182的上方,第二部分172位于第一侧壁181与第二侧壁182的下方;第一部分171连接于内环壁151和外环壁152之间;第二部分172沿第一混气腔111的径向p设置,第二部分172的两端分别与外环壁152连接,且第二部分172的相对的两侧分别与第一侧壁181和第二侧壁182连接,外环进气口13开设于第二部分172。
52.其中,内环壁151、外环壁152、底壁17的第一部分171围合形成第一混气腔111。顶壁16、第一侧壁181、第二侧壁182和底壁17的第二部分172围合形成第二混气腔112。
53.内环混气腔12的内环进气口14内置于外环进气口13中。这样,通过提供内环混气腔12以及内环进气口14的设置方式,使底座10的结构更为紧凑。具体地,内环进气口14开设于顶壁16上,且内环混气腔12位于顶壁16的上方。
54.顶壁16靠近内环壁151的一端沿第一混气腔111的径向p逐渐向上延伸以形成一倾斜壁161。这样,通过设置倾斜壁161,扩大了进入第一混气腔111的进气路径的最小截面b的面积,有助于燃烧器1的性能提升;并且倾斜壁161可以充当内环聚能圈使用。
55.在本实施例中,倾斜壁161的数量为两个,即顶壁16包括靠近内环壁151设置的第一倾斜壁1611和第二倾斜壁1612、以及连接于第一倾斜壁1611和第二倾斜壁1612之间的连接部162,连接部162沿水平方向设置。这样,使第二混气腔112与第一混气腔111连通的两端均具有倾斜壁161,扩大了进入第一混气腔111的进气路径的最小截面b的面积,有助于燃烧器1的性能提升;通过在中间位置沿水平方向设置连接部162,以避免第一倾斜壁1611和第二倾斜壁1612太靠近内环火焰。
56.较佳地,第一倾斜壁1611和第二倾斜壁1612对称设置,以使第二混气腔112与第一混气腔111连通的两端的进气更为均匀。
57.较佳地,倾斜壁161所在的平面与水平面的夹角为45度-60度。即,第一倾斜壁1611
所在的平面与水平面的第一夹角α为45度-60度,以及第二倾斜壁1612所在的平面与水平面的第二夹角β亦为45度-60度。这样,通过进一步限定倾斜壁161所在的平面与水平面的夹角的度数范围,以最大化进入第一混气腔111的进气路径的最小截面的面积。第一夹角α与第二夹角β相等,或者不相同,可以根据设计需要进行调整。
58.但不限于此,在其他实施例中,也可以仅设置第一倾斜壁1611或者仅设置第二倾斜壁1612。
59.内环进气口14的内壁卡套于位于底座10下方的基座的上端的第二出气口的外周缘,以实现底座10的内环进气口14与基座的第二出气口之间的密封,避免漏火现象的产生。
60.在本实施例中,底座10还包括密封台阶19,密封台阶19设于底壁17的第二部分172的下表面,且沿外环进气口13的外周缘设置。这样,通过设置密封台阶19,密封台阶19卡套于位于底座10下方的基座的上端的外周缘,以实现底座10的外环进气口13与位于其下方基座上的第一出气口之间的密封,避免漏火现象的产生。
61.本实施例中的底座10一体压铸成型。这样,底座10通过一体压铸成型,能够达到降低制造成本,提高成品的质量的有益技术效果。
62.本实施例还提供一种炊具,炊具包括如上的燃烧器1。
63.本实施例的燃烧器1以及炊具,通过设置底座10为上下对冲结构,不在设置外环传气通道结构,从而能够采用压铸工艺制作底座10,降低了制造成本,提高了成品的质量;并且,由于减少了气体在外环传气通道传输过程中的动力损失,还具有提高燃烧器1的性能的有益效果。相较于现有技术中,传气路径需要经过外环传气通道,而导致传气路径的截面积的减少,而造成传气的节流;在本技术方案中,由于不再设置外环传气通道,外环进气口13直接连通外环混气腔11,从而能够避免造成传气的节流,并且增加二次空气流动范围的有益技术效果。
64.虽然以上描述了本实用新型的具体实施方式,但是本领域的技术人员应当理解,这仅是举例说明,本实用新型的保护范围是由所附权利要求书限定的。本领域的技术人员在不背离本实用新型的原理和实质的前提下,可以对这些实施方式做出多种变更或修改,但这些变更和修改均落入本实用新型的保护范围。