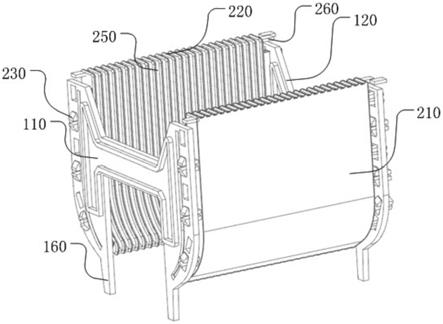
1.本实用新型涉及半导体集成技术领域,尤其涉及一种可拆卸式晶片承载盒。
背景技术:
2.随着半导体技术领域的发展,对高清洁度的衬底晶片需求日益上升,衬底的清洗通常采用rca、超声、二流体与刷片等方式,上述清洗方式可去除晶片表面绝大部分小于1um的颗粒,但晶片清洗后的二次污染较难避免;二次污染即来自于其存放环境以及运输运送过程中装载的载具等。承载盒作为直接与晶片接触的载具,其内部的洁净度直接影响衬底的表面洁净度;因而为了确保晶片的清洁度,对晶片承载盒的品质要求也越来越高。
3.目前常见的晶片承载盒是采用塑料一体成型的方式加工而成,成型后会以超声清洗、药剂浸泡等方法进行清洗,对于未使用过的晶片承载盒其清洁度一般能达到需求,但对于回收循环使用的晶片承载盒由于其已与机台、外部环境接触造成污染,因而在使用前一般需极力清洗;而对于循环使用的晶片承载盒的清洗效果受限于承载盒的污损程度,对于与晶片边缘直接接触的狭窄部位,使用过程中易产生细小划痕,导致颗粒堆积不易去除;为改善承载盒清洗效果,一般需采用多种清洗方式结合对晶片承载盒进行清洗,例如首先通过清洗剂配合超声去除颗粒,再采用鼓泡或喷淋的方式去除药剂残留;采用上述方式进行清洗不仅使清洗工艺较复杂,但即便采用多道清洗工序,清洗后的晶片承载盒的清洁度也难以满足需求。
4.另外,传统的晶片承载盒清洗效率还受限于承载盒的空间结构与自身重量,其较轻的自身重量以及较大的空间占用量使得晶片承载盒无法大批量且有序的固定于清洗槽内,导致实际清洗困难;且由于其自身结构,不仅导致运输困难,而且在重复使用及清洗过程中,由于不同程度的磕碰会造成承载盒局部破损或变形,从而降低了晶片承载盒的使用寿命,导致二次回收的报废率高达30~40%,因而提高了成本以及产生了资源浪费。因此,如何使晶片承载盒便于清洗及运输,以及降低晶片承载盒在循环回收利用过程中的报废率是亟待解决的技术问题。
技术实现要素:
5.有鉴于此,本实用新型提供了一种可拆卸式晶片承载盒,以解决现有的承载盒清洗运输困难、报废率高以及成本损耗较高的问题。
6.根据本实用新型的一方面,公开了一种可拆卸式晶片承载盒,所述晶片承载盒包括第一端部挡板、第二端部挡板、第一侧板以及第二侧板,
7.所述第一端部挡板与第二端部挡板相对设置;
8.所述第一侧板位于所述第一端部挡板与第二端部挡板之间,所述第一侧板的两端分别与所述第一端部挡板和第二端部挡板通过可拆卸连接结构连接;
9.所述第二侧板与所述第一侧板相对且间隔设置,所述第二侧板的两端分别与所述第一端部挡板和第二端部挡板通过可拆卸连接结构连接,且所述第一侧板的面向于所述第
二侧板的一侧和/或第二侧板的面向于所述第一侧板的一侧具有晶片安装槽。
10.在本实用新型的一些实施例中,所述可拆卸连接结构包括卡扣和卡槽,所述卡扣位于所述第一侧板和第二侧板的端部,所述卡槽位于所述第一端部挡板和第二端部挡板的与所述卡扣相对应的位置处。
11.在本实用新型的一些实施例中,所述可拆卸连接结构包括凸起部和槽孔,所述凸起部位于所述第一侧板和第二侧板的端部,所述槽孔位于所述第一端部挡板和第二端部挡板的与所述凸起部相对应的位置处。
12.在本实用新型的一些实施例中,所述第一端部挡板的远离所述第二端部挡板的一侧具有朝外凸起的凸沿,所述凸沿的深度大于或等于位于所述第一端部挡板外侧的卡扣的高度。
13.在本实用新型的一些实施例中,所述第一侧板与第二侧板之间的间距至少一部分为从上至下逐渐减小。
14.在本实用新型的一些实施例中,所述第一侧板和第二侧板的靠近于所述第一端部挡板的一端顶部具有朝向所述第一端部挡板外侧延伸的限位柱,所述第一侧板和第二侧板的靠近于第二端部挡板的一端顶部具有朝向所述第二端部挡板外侧延伸的限位柱。
15.在本实用新型的一些实施例中,所述第一端部挡板和第二端部挡板的底部均具有底部脚柱。
16.在本实用新型的一些实施例中,所述第一侧板的面向于所述第二侧板的一侧具有多个第一晶片安装槽,所述第二侧板的面向于所述第一侧板的一侧具有多个与所述第一晶片安装槽相对应的第二晶片安装槽。
17.在本实用新型的一些实施例中,所述第一侧板和第二侧板的数量均为多个,且多个所述第一侧板以及多个第二侧板分别水平排布,相邻两个所述第一侧板之间以及相邻两个所述第二侧板之间均通过可拆卸连接方式连接。
18.在本实用新型的一些实施例中,所述第一端部挡板的数量为多个,相邻两个所述第一侧板的相邻端部均与所述第一端部挡板可拆卸连接,相邻两个第二侧板的相邻端部均与所述第一端部挡板可拆卸连接。
19.通过利用本实用新型实施例中的可拆卸式晶片承载盒,可以获得的有益效果至少在与:
20.该可拆卸式晶片承载盒的各个端部挡板与各个侧板之间均通过可拆卸连接方式进行连接,在循环使用过程中,拆卸后的晶片承载盒不仅便于摆放及清洗,还便于运输。另外,在清洗过程中,可基于各部件的污损情况选择合适的清洗方式,例如,对于较难清洗的晶片安装槽所处的侧板采用超声或二流体喷淋清洗,对于较易清洗的挡板采用简易浸泡方式清洗,上述方式不仅简化了清洗的工艺流程,还提高了清洗效率。另外,随着循环使用次数的增加,可通过仅更换污损严重的部件的方式降低晶片承载盒的报废率,从而降低了损耗成本。
21.本实用新型的附加优点、目的,以及特征将在下面的描述中将部分地加以阐述,且将对于本领域普通技术人员在研究下文后部分地变得明显,或者可以根据本实用新型的实践而获知。本实用新型的目的和其它优点可以通过在书面说明及其权利要求书以及附图中具体指出的结构实现到并获得。
22.本领域技术人员将会理解的是,能够用本实用新型实现的目的和优点不限于以上具体所述,并且根据以下详细说明将更清楚地理解本实用新型能够实现的上述和其他目的。
附图说明
23.此处所说明的附图用来提供对本实用新型的进一步理解,构成本技术的一部分,并不构成对本实用新型的限定。附图中的部件不是成比例绘制的,而只是为了示出本实用新型的原理。为了便于示出和描述本实用新型的一些部分,附图中对应部分可能被放大,即,相对于依据本实用新型实际制造的示例性装置中的其它部件可能变得更大。在附图中:
24.图1为本实用新型一实施例的可拆卸式晶片承载盒的立体图。
25.图2为图1所示可拆卸式晶片承载盒的拆去第一侧板后的主视图。
26.图3为图1所示可拆卸式晶片承载盒的左视图。
27.图4为图1所示可拆卸式晶片承载盒的俯视图。
28.图5为本实用新型一实施例的第一端部挡板的结构示意图。
29.图6为本实用新型一实施例的第二端部挡板的结构示意图。
30.图7为本实用新型一实施例的第一侧板的结构示意图。
31.图8为本实用新型另一实施例的可拆卸式晶片承载盒的结构示意图。
具体实施方式
32.为使本实用新型实施例的目的、技术方案和优点更加清楚明白,下面结合附图对本实用新型实施例做进一步详细说明。在此,本实用新型的示意性实施例及其说明用于解释本实用新型,但并不作为对本实用新型的限定。
33.在此,需要说明的是,为了避免因不必要的细节而模糊了本实用新型,在附图中仅仅示出了与根据本实用新型的方案密切相关的结构和/或处理步骤,而省略了与本实用新型关系不大的其他细节。
34.应该强调,术语“包括/包含/具有”在本文使用时指特征、要素、步骤或组件的存在,但并不排除一个或更多个其它特征、要素、步骤或组件的存在或附加。
35.在此,还需要说明的是,本说明书内容中所出现的方位名词是相对于附图所示的位置方向;如果没有特殊说明,术语“连接”在本文不仅可以指直接连接,也可以表示存在中间物的间接连接。直接连接为两个零部件之间不借助中间部件进行连接,间接连接为两个零部件之间借助其他零部件进行连接。
36.在下文中,将参考附图描述本发明的实施例。在附图中,相同的附图标记代表相同或类似的部件。
37.图1为本实用新型一实施例的可拆卸式晶片承载盒的立体图,如图1所示,该晶片承载盒包括第一端部挡板110、第二端部挡板120、第一侧板210以及第二侧板220。其中,第一端部挡板110与第二端部挡板120相对且间隔设置,第一侧板210和第二侧板220均位于第一端部挡板110与第二端部挡板120之间;由上可知,第一端部挡板110与第二端部挡板120之间的间隔距离可为第一侧板210或第二侧板220的长度。其中,第一侧板210与第二侧板220相对且间隔设置,且第一侧板210的两端分别与第一端部挡板110和第二端部挡板120通
过可拆卸连接结构连接,而第二侧板220的两端也分别与第一端部挡板110和第二端部挡板120通过可拆卸连接结构连接;另外,由于晶片被放置在第一侧板210与第二侧板220之间,因而第一侧板210和/或第二侧板220上还具有晶片安装槽250。
38.从图1和图4中可以看出,该晶片承载盒的顶部以及底部均为敞口结构,晶片可从晶片承载盒的顶部敞口位置处装载至位于第一侧板210与第二侧板220之间的晶片安装槽250内。另外,为了防止晶片从晶片承载盒的底部敞口位置处掉落,则晶片承载盒的底部敞口的宽度尺寸可小于晶片的直径尺寸,换句话说,即第一侧板210与第二侧板220的底部间距可小于晶片的直径尺寸;其中宽度尺寸是指图3中的横向尺寸;另外,为了确保晶片便于从晶片承载盒的顶部敞口位置处安装至晶片安装槽250内,则还应保证顶部敞口的宽度尺寸稍大于晶片的直径尺寸,也即在该实施例中,晶片承载盒的顶部敞口宽度尺寸大于底部敞口宽度尺寸。应当理解的是,将晶片承载盒的底部敞口的宽度尺寸限定为小于晶片直径尺寸是为了防止晶片从晶片承载盒的底部敞口掉落,因而也可以通过加装挡板的方式对晶片进行限位。另外,晶片承载盒的顶部敞口以及底部敞口的尺寸可根据该晶片承载盒所承载的晶片的尺寸进行限定,因而可通过调整第一侧板210与第二侧板220之间的间距使晶片承载盒可装载不同尺寸的晶片。
39.进一步的,第一侧板210的面向于第二侧板220的一侧具有多个第一晶片安装槽250,第二侧板220的面向于第一侧板210的一侧具有多个与第一晶片安装槽250相对应的第二晶片安装槽250。示例性的,第一晶片安装槽250和第二晶片安装槽250的数量可为25个,此时可对应的在第一侧板210和第二侧板220上分别设置24条挡条,且相邻两条挡条之间间隔预定距离,即形成晶片安装槽250。在第一侧板210和第二侧板220上设置晶片安装槽250可将晶片限制且稳定在晶片安装槽250内,从而防止相邻晶片互相碰撞及互相干扰。
40.在上述实施例中,晶片承载盒通过四个单独的部件进行组装,且各部件之间通过可拆卸连接方式进行连接。因而在晶片承载盒的循环利用过程中,可进一步的将晶片承载盒的各个部件进行拆卸之后进行清洗及运输,其相对于一体成型的晶片承载盒不仅减少了所占用的空间,还使得单个部件的重量较轻,从而便于运输及清洗。另外,当随着循环使用次数的增加,晶片承载盒的各个部件的磨损程度不同,可通过仅更换磨损严重的第一侧板210或第二侧板220的方式降低晶片承载盒的报废率,进而则降低了成本。
41.在一实施例中,第一侧板210与第二侧板220之间的间距至少一部分为从上至下逐渐减小。参考图1,第一侧板210和第二侧板220具体的可包括上部的矩形板和下部的弧形板,此时弧形板的顶部边沿与矩形板的底部边沿相接,且弧形板自矩形板的底部边沿逐渐向内收缩。即在该实施例中,自弧形板顶部边沿至底部敞口第一侧板210与第二侧板220之间的间距逐渐减小。在该实施例中,第一侧板210与第二侧板220的结构相同,均包括矩形板和弧形板;在其他实施例中,也可将第一侧板210和第二侧板220中的其中一个设置为矩形板与弧形板相接的形式。另外,与矩形板相接的弧形板是为了使晶片承载盒的底部敞口宽度尺寸小于其顶部敞口宽度尺寸,因而其也可替换成朝内倾斜的矩形板。
42.在本实用新型一实施例中,第一侧板210、第二侧板220与第一端部挡板110和第二端部挡板120之间可均通过卡扣230卡槽130的连接方式进行连接,也即此时第一侧板210与各端部挡板之间、第二侧板220与各端部挡板之间的可拆卸连接结构包括卡扣230和卡槽130。示例性的,卡扣230可位于第一侧板210和第二侧板220的端部,此时卡槽130则位于用
于与第一侧板210和第二侧板220连接的第一端部挡板110和第二端部挡板120上,且为了确保卡扣230卡槽130的有效配合,第一端部挡板110与第二端部挡板120上的卡槽130的位置与其相配合的卡扣230的位置相对应。
43.进一步的,卡扣230为斜角卡扣230,而卡槽130为矩形卡槽130。如图7所示,卡扣230包括呈对称结构的上下两个子卡扣230,且各子卡扣230包括矩形柱和位于矩形柱末端的斜角凸起部,相对应的,此时位于第一端部挡板110和第二端部挡板120上的卡槽130为矩形卡槽130。在将斜角卡扣230安装至矩形卡槽130内时,基于斜角卡扣230的弹性及韧性特性,两个子卡扣230向中间合并;进一步的两个子卡扣230的斜角凸起部通过矩形卡槽130后被释放,即两个子卡扣230的斜角凸起部被抵靠在矩形卡槽130的外侧,此时也即实现了斜角卡扣230与矩形卡槽130的连接。另外,如图1所示,第一侧板210端部的卡扣230的数量为多个,相应的,与第一侧板210连接的第一端部挡板110和第二端部挡板120上的卡槽130的数量也为多个,且各卡扣230与各卡槽130的位置一一相对应。
44.进一步的,可拆卸连接结构还包括凸起部240和槽孔140,凸起部240位于第一侧板210和第二侧板220的端部,槽孔140位于第一端部挡板110和第二端部挡板120的与凸起部240相对应的位置处。如图7所示,第一侧板210的斜角卡扣230的内侧具有长方体形状的凸起部240,相对应的,与第一侧板210相连接的第一端部挡板110和第二端部挡板120上具有矩形槽孔140,该矩形槽孔140的位置与凸起部240的位置相对应,且在第一侧板210与端部挡板的连接状态下,凸起部240与矩形槽孔140间隙配合,使得凸起部240位于矩形槽孔140内。应当理解的是,当第一侧板210、第二侧板220、第一端部挡板110、第二端部挡板120之间仅通过凸起部240与槽孔140进行连接时,此时第一端部挡板110以及第二端部挡板120除了水平方向之外的其他方向均通过凸起部240进行限位。而进一步的为了实现第一端部挡板110以及第二端部挡板120在水平方向上的限位,则可进一步的通过卡扣230及卡槽130对第一端部挡板110和第二端部挡板120进一步固定。
45.在本实用新型一实施例中,第一端部挡板110的远离第二端部挡板120的一侧具有朝外凸起的凸沿150,凸沿150的深度大于或等于位于第一端部挡板110外侧的卡扣230的高度。其中,第一端部挡板110的远离第二端部挡板120的一侧即为第一端部挡板110的左侧(或外侧),而凸沿150的深度则是指图2所示附图的横向方向。如图5所示,凸沿150的结构形状大致可呈“工”字形;在第一端部挡板110的左侧设置凸沿150,是为了确保晶片承载盒竖立放置时(第一端部挡板110位于底部)保持平衡,即在晶片承载盒竖直放置时避免卡扣230与支撑面接触。应当理解的是,除了在第一端部挡板110的外侧设置凸沿150之外,还可以采用凸块代替凸沿150。
46.进一步的,所述第一侧板210和第二侧板220的两端顶部还均具有限位柱260。具体的,第一侧板210和第二侧板220的靠近于第一端部挡板110的一端顶部具有朝向第一端部挡板110外侧延伸的限位柱260,而第一侧板210和第二侧板220的靠近于第二端部挡板120的一端顶部具有朝向第二端部挡板120外侧延伸的限位柱260。如图7所示,限位柱260具体的可呈长方形结构,该限位柱260的作用是为了使晶片承载盒在竖立放置时实现限位。
47.另外,当晶片承载盒水平放置时,为了确保晶片承载盒内的晶片处于悬空状态,及增加整个晶片承载盒的高度,即第一端部挡板110和第二端部挡板120的底部还可均设有底部脚柱160。参考图5和图6,各端部挡板的底部具有两个底部脚柱160,且各底部脚柱160的
高度均相等。除上述之外,底部脚柱160也可被设置在第一侧板210和第二侧板220的底部,即第一侧板210和第二侧板220的底部可分别设置两个等高的底部脚柱160。
48.图8为本实用新型另一实施例的可拆卸式晶片承载盒的结构示意图,如图8所示,该晶片承载盒的第一侧板210和第二侧板220的数量均为两个,其中,两个第一侧板210水平排布在第一端部挡板110和第二端部挡板120之间,而两个第二侧板220类似的也水平排布在第一端部挡板110和第二端部挡板120之间。另外,两个第一侧板210之间以及两个第二侧板220之间均通过可拆卸连接方式连接。在该实施例中,位于晶片承载盒的第一端部挡板110和第二端部挡板120之间的第一侧板210和第二侧板220的数量可根据实际要承载的晶片的数量进行设定,即一个晶片承载盒内,第一侧板210、第二侧板220的数量可为两个或多个。由于该晶片承载盒便于拆装,因而可通过加装第一侧板210和第二侧板220的方式方便的提高晶片的装载容量。
49.当第一侧板210和第二侧板220的数量均为多个时,进一步的,第一端部挡板110的数量也为多个。且相邻两个第一侧板210的相邻端部均与第一端部挡板110可拆卸连接,相邻两个第二侧板220的相邻端部均也与第一端部挡板110可拆卸连接。示例性的,相邻两个第一侧板210的相邻端部的卡扣230可交错设置,相邻两个第一侧板210的端部均与位于两个第一侧板210之间的第一端部挡板110进行连接即实现了两个第一侧板210的可拆卸链接;类似的,相邻两个第二侧板220的相邻端部的卡扣230也可交错设置,进而相邻的两个第二侧板220也通过第一端部挡板110实现了可拆卸连接。
50.进一步的,晶片承载盒的材质可根据实际应用环境进行选择,示例性的,作业环境为强酸碱环境时,可选用耐腐蚀性强的ptfe材质;作业环境为高温时,可选用聚苯硫醚、聚苯酯与peek等热变形稳定较高的材质;而普通环境加工点周转重复使用时,则可选用聚酰胺、聚甲醛、聚丙烯与聚碳酸酯等能承受一定外力作用、具有良好的机械性能和耐磨性及尺寸稳定性良好的材质。
51.通过上述实施例可以发现,该晶片承载盒的第一端部挡板、第二端部挡板、第一侧板、第二侧板之间进行可拆卸连接,实现了各部件的自由拆卸及组合;且拆卸后的承载盒占地空间小,可降低2/3的占地空间,利于运输与摆放;另,将晶片承载盒拆卸后进行清洗,不仅减少了清洗工艺步骤,还提高了清洗效率。除上述之外,通过增加第一侧板以及第二侧板的方式还可扩大晶片承载盒的容量。
52.本实用新型中,针对一个实施方式描述和/或例示的特征,可以在一个或更多个其它实施方式中以相同方式或以类似方式使用,和/或与其他实施方式的特征相结合或代替其他实施方式的特征。
53.上述所列实施例,显示和描述了本实用新型的基本原理与主要特征,但本实用新型不受上述实施例的限制,本领域技术人员在没有做出创造性劳动的前提下对本实用新型做出的修改、等同变化及修饰,均应落在本实用新型技术方案保护的范围内。