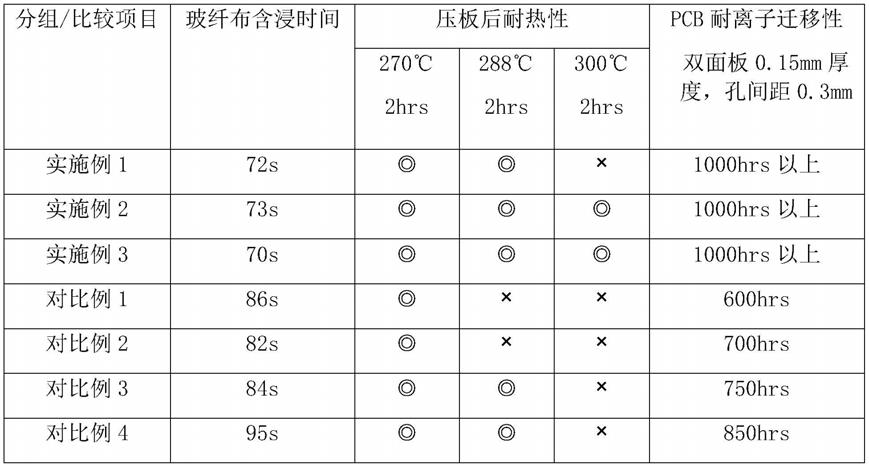
1.本发明属于电子玻璃纤维布处理领域,具体涉及一种用于处理玻璃布的表面处理剂。
背景技术:
2.电子级玻璃纤维布(glass-fibre fabric)是一种用玻璃纤维制成的织物,其具有具有绝缘、绝热、耐腐蚀、不燃烧、耐高温、高强度等性能,主要用作绝缘材料、玻璃钢的增强材料、化学品过滤布、高压蒸汽绝热材料、防火制品、高弹性传动带、建筑材料和贴墙布等。
3.为了使玻璃布本身机械性能更好并且更易于应用到与其他材料的复合过程中,需要在玻璃布的生产过程中对玻璃布进行表面处理。由于玻璃布属于无机纤维,通常使用硅烷偶联剂作为其表面处理剂的关键成分。
4.在化工行业,已知硅烷偶联剂的水解速度取于硅能团si-x,而与有机聚合物的反应活性则取于碳官能团c-y。因此,对于不同基材或处理对象,选择适用的硅烷偶联剂至关重要。由于异种材料间的黏接强度受到一系列因素的影响,诸如润湿、表面能、界面层及极性吸附、酸碱的作用、互穿网络及共价键反应等,因而,光靠试验预选有时还不够精确,还需综合考虑材料的组成及其对硅烷偶联剂反应的敏感度等。
5.5g pcb一个非常明确的方向就是高频高速材料及制板,而树脂、铜箔、玻布的搭配将达成电性能与成本最佳平衡点。此外,高层数和高密度也会带来可靠性的挑战,使得pcb的功能性更强,而此发展要求其增强材料电子级玻璃纤维布的表面处理面向多元化发展,表面处理剂的开发面向客制化,多种树脂领域匹配不同表面处理剂,5g的应用将为高频高速材料、更精密的生产和检测设备,树脂领域进行了重大变革,low df树脂配方应运而生。面临树脂的新型配方,其上游玻纤布的表面处理新工艺必将随之增加新的功能,要求玻纤布表面处理的硅烷偶联剂与树脂具有匹配性。研发新型高效的表面处理剂和表面处理效果(即玻纤布与树脂的浸润性)提升将是电子级玻璃纤维布的一个重要课题。
6.pcb的主要材料覆铜板(ccl)主要由基板和铜箔构成。由于5g需要的低讯号损失应运而生的特殊高分子合成树脂、玻璃纤维布以及光滑平面的铜箔,这三者之间的牢固性,需要硅烷表面处理剂来起作用。硅烷表面处理剂是电子级玻璃纤维布表面处理制程中的重要添加剂,能决定pcb使用中的诸多性能,用量虽小但功效显著。
7.为了满足高频高速pcb产品的可靠性、复杂性、电性能和装配性能等诸多方面的要求,许多pcb基板材料的厂商对特殊树脂进行了不同的改性。
8.在目前高速高频化的趋势下,较为主流的pcb材料包括聚四氟乙烯树脂(ptfe)、环氧树脂(ep)、双马来酰亚胺三嗪树脂(bt)、热固性氰酸脂树脂(ce)、热固性聚苯醚树脂(ppe)和聚酰亚胺树脂(pi),由此衍生出的覆铜板种类超过130种。
9.热固性低介电树脂是一种接近氟树脂、拥有低介电常数和高强度的低弹性树脂。它的高频带(10~80ghz)介电常数低于2.5,消耗因数低于0.00025。这是热固性树脂的最低水平。由于产品的低吸湿性、对低粗度的铜箔也具有很高的粘着力,因此也可用于fccl(软
性铜箔基材)。pcb产业链由上游的铜箔、玻纤、覆铜板,中游的pcb制造以及下游的行业应用构成。覆铜板用电子级玻纤布对pcb直接影响pcb导电、绝缘、支撑等功能,是pcb制造的重要基材。
10.面对当前覆铜板市场low df树脂ppe和热固性氰酸脂树脂(ce)或几种树脂的复配,多层板的需求,传统的硅烷偶联剂配方生产的玻纤布难以达到多层pcb板的耐热、耐湿性要求,以及耐caf性能。
11.中国发明专利cn107119455a公开了一种玻璃纤维布用后处理剂及其制备方法,其玻璃纤维布用后处理剂由以下组分组成,各组分含量以重量百分比计:硅烷偶联剂a,通式y(ch2)six3,含量0.2~1.0%;硅烷偶联剂b,通式y(ch2)six3,含量0.1~0.8%;ph调节剂,含量0.01~0.10%;表面活性剂,含量0.002~0.015%;去离子水余量。该后处理剂储存稳定性好,与树脂结合力强,并且有一定的挺括性,但是其处理后的玻璃纤维布的性能有待进一步改善。
技术实现要素:
12.针对现有技术存在的不足,本发明的目的是提供一种特别适用于玻璃布生产的适用于热固性低介电树脂的硅烷表面处理剂,通过改善表面处理剂的配方和制备方法,可以增强玻纤布表面涂覆偶联剂的均匀性,提高玻纤布偶联剂含量loi%,达到与树脂的结合性改善。
13.本发明的目的是通过以下技术方案实现的:
14.一种用于处理玻璃布的表面处理剂,包括以下重量份数的组分:冰醋酸1-1.5份,含氟硅烷偶联剂0.55-0.80份,含异氰酸酯基硅烷偶联剂0.6
–
1.2份,脂肪胺聚氧乙烯醚0.7
–
0.9份,烷基醇酰胺聚氧乙烯醚1.2-2.0份,消泡剂0.001-0.002份和水90-97份。
15.优选地,所述含氟硅烷偶联剂为1h,1h,2h,2h-全氟癸基三甲氧基硅烷kh-f1013;含异氰酸酯基硅烷偶联剂为3-异氰酸酯基丙基三乙氧基硅烷kh-ic23。
16.优选地,所述含氟硅烷偶联剂与含异氰酸酯基硅烷偶联剂的质量比为1:1.0-1.5。
17.优选地,所述消泡剂包括矿物油、聚醚和二氧化硅。
18.优选地,所述矿物油、聚醚和二氧化硅的质量比为7-10:4-6:2-3。
19.优选地,所述脂肪胺聚氧乙烯醚与烷基醇酰胺聚氧乙烯醚的质量比为1:1.7-2.5。
20.本发明的再一目的是提供上述表面处理剂的制备方法,包括如下步骤:
21.(1)将消泡剂和部分水混合搅拌得消泡剂溶液,再将剩余水和冰醋酸混合,得冰醋酸溶液;
22.(2)向冰醋酸溶液中加入含氟硅烷偶联剂和含异氰酸酯基硅烷偶联剂,混合;
23.(3)向步骤(2)混合制得的液体体系中加入脂肪胺聚氧乙烯醚和烷基醇酰胺聚氧乙烯醚混合搅拌;
24.(4)向步骤(3)制得的混合体系中加入消泡剂溶液,混合搅拌得表面处理剂。
25.优选地,步骤(1)中所述消泡剂和部分水的质量比为1:5-15,所述搅拌的时间为30-40min;所述消泡剂溶液的存放时间≤3h。
26.优选地,步骤(2)或(3)中所述搅拌的时间为30-40min,步骤(4)中所述搅拌的时间为60-100min。
27.本发明还有一个目的是提供上述表面处理剂在制备处理电子级玻璃纤维布表面活性剂中的应用。
28.与现有技术相比,本发明的有益效果:
29.(1)本发明通过选用含氟硅烷偶联剂和含异氰酸酯基硅烷偶联剂的复配,通过各基团的合理配伍,不仅渗透力更强,可以提高玻纤布表面与树脂高分子的粘接性,还可以提高树脂与玻璃纤维的浸润机械强度和电性能,特别是湿态机械强度和电性能,能显著改善玻璃钢的耐候性、耐水性、耐热性,赋予制品较好的电磁波透射性。
30.(2)本发明通过配置的表面活性剂,使得玻璃纤维布在表面处理过程中使玻纤布表面偶联剂涂覆更均匀,提高了玻纤布的含浸性,制得的玻纤布有更优的耐热性、耐离子迁移性和尺寸安定性。
具体实施方式
31.下面结合具体的实施方式对本发明做进一步阐述。
32.本实施例所用的材料均为市售常规材料。其中kh-f1013和kh-ic23购自广州市龙凯化工有限公司;ac-1815、月桂酰胺聚氧乙烯醚(cas:26635-75-6)和聚醚f-38购自江苏省海安石油化工厂。
33.实施例1
34.一种用于处理玻璃布的表面处理剂,原料为:冰醋酸1份,1h,1h,2h,2h-全氟癸基三甲氧基硅烷kh-f1013 0.55份,3-异氰酸酯基丙基三乙氧基硅烷kh-ic23 0.60份,脂肪胺聚氧乙烯醚ac-1815 0.7份,月桂酰胺聚氧乙烯醚1.2份,消泡剂0.001份和水90份。
35.其中消泡剂为质量比为7:6:2煤油、聚醚f-38和二氧化硅组成;
36.制备方法如下:
37.(1)将消泡剂和水按质量比1:5混合,持续搅拌40min,得消泡剂溶液;
38.(2)将剩余水和冰醋酸混合,搅拌均匀,得冰醋酸溶液;
39.(3)向冰醋酸溶液中缓缓加入含氟硅烷偶联剂和含异氰酸酯基硅烷偶联剂,混合均匀;
40.(4)向步骤(3)混合制得的液体体系中缓缓加入脂肪胺聚氧乙烯醚和烷基醇酰胺聚氧乙烯醚混合,并搅拌40分钟至混合均匀;
41.(5)向步骤(4)制得的混合体系中加入消泡剂溶液,混合搅拌60min得表面处理剂。
42.实施例2
43.一种用于处理玻璃布的表面处理剂,原料为:冰醋酸1.5份,1h,1h,2h,2h-全氟癸基三甲氧基硅烷kh-f1013 0.80份,3-异氰酸酯基丙基三乙氧基硅烷kh-ic23 1.2份,脂肪胺聚氧乙烯醚ac-1815 0.90份,月桂酰胺聚氧乙烯醚2.0份,消泡剂0.002份和水97份。
44.其中消泡剂为质量比为10:4:3煤油、聚醚f-38和二氧化硅组成;
45.制备方法如下:
46.(1)将消泡剂和水按质量比1:15混合,持续搅拌30min,得消泡剂溶液;
47.(2)将剩余水和冰醋酸混合,搅拌均匀,得冰醋酸溶液;
48.(3)向冰醋酸溶液中缓缓加入含氟硅烷偶联剂和含异氰酸酯基硅烷偶联剂,混合均匀;
49.(4)向步骤(3)混合制得的液体体系中缓缓加入脂肪胺聚氧乙烯醚和烷基醇酰胺聚氧乙烯醚混合,并搅拌30分钟至混合均匀;
50.(5)向步骤(4)制得的混合体系中加入消泡剂溶液,混合搅拌100min得表面处理剂。
51.实施例3
52.一种用于处理玻璃布的表面处理剂,原料为:冰醋酸1.5份,1h,1h,2h,2h-全氟癸基三甲氧基硅烷kh-f1013 0.65份,3-异氰酸酯基丙基三乙氧基硅烷kh-ic23 0.80份,脂肪胺聚氧乙烯醚ac-1815 0.8份,月桂酰胺聚氧乙烯醚2.0份,消泡剂0.001份和水。
53.其中消泡剂由质量比为8:5:2的煤油、聚醚f-38和二氧化硅组成;
54.制备方法如下:
55.(1)将消泡剂和水按质量比1:10混合,持续搅拌35min,得消泡剂溶液;
56.(2)将剩余水和冰醋酸混合,搅拌均匀,得冰醋酸溶液;
57.(3)向冰醋酸溶液中缓缓加入含氟硅烷偶联剂和含异氰酸酯基硅烷偶联剂,混合均匀;
58.(4)向步骤(3)混合制得的液体体系中缓缓加入脂肪胺聚氧乙烯醚和烷基醇酰胺聚氧乙烯醚混合,并搅拌35分钟至混合均匀;
59.(5)向步骤(4)制得的混合体系中加入消泡剂溶液,混合搅拌80min得表面处理剂。
60.对比例1
61.本对比例与实施例3的区别是将3-异氰酸酯基丙基三乙氧基硅烷kh-ic23去掉,将1h,1h,2h,2h-全氟癸基三甲氧基硅烷kh-f1013增加为1.45份,其余与实施例3保持一致。
62.对比例2
63.本对比例与实施例3的区别是将1h,1h,2h,2h-全氟癸基三甲氧基硅烷kh-f1013去掉,将3-异氰酸酯基丙基三乙氧基硅烷kh-ic23增加为1.45份,其余与实施例3保持一致。
64.对比例3
65.本对比例与实施例3的区别是脂肪胺聚氧乙烯醚ac-1815与月桂酰胺聚氧乙烯醚的质量比不同,具体表面处理剂原料为:冰醋酸1.5份,1h,1h,2h,2h-全氟癸基三甲氧基硅烷kh-f1013 0.65份,3-异氰酸酯基丙基三乙氧基硅烷kh-ic23 0.80份,脂肪胺聚氧乙烯醚ac-1815 2.0份,月桂酰胺聚氧乙烯醚0.8份,消泡剂0.001份和水。
66.其中消泡剂由质量比为8:5:2的煤油、聚醚f-38和二氧化硅组成;
67.制备方法同实施例3一致。
68.对比例4
69.本对比例与实施例3的区别是将月桂酰胺聚氧乙烯醚替换为辛基酚聚氧乙烯醚,其余与实施例3保持一致。
70.对比例5
71.本对比例与实施例3的区别是将1h,1h,2h,2h-全氟癸基三甲氧基硅烷kh-f1013替换为巯基硅烷偶联剂kf580,将3-异氰酸酯基丙基三乙氧基硅烷kh-ic23替换为氨基硅烷偶联剂a-1100,其余与实施例3保持一致。
72.效果例
73.用实施例1-3与对比例1-5制备的表面处理剂对电子级玻璃纤维布(由我司生产的
型号为1080的退浆布,厚度范围为0.03-0.05mm)进行处理,测定电子级玻璃纤维布含浸时间性能,然后与热固性树脂酚醛树脂结合后,压板测定其耐热性,制作成pcb后测试其耐离子迁移性。
74.试验方法:
75.(1)玻纤布含浸时间测试方法如下:
76.在成品布上用取样工具裁取左中右各一块面积为110*160mm(经向长110mm)的试样,并往搪瓷托盘内倒入适量的水杨酸甲酯将样品放入搪瓷托盘,同时开始用秒表记时,样品必须全部浸入水杨酸甲酯内必要时用镊子轻压漂浮的样品使其完全浸入水杨酸甲酯内。在实验过程中,不停的用手电筒成30
°
角分别沿经纬纱方向照射。观察玻璃丝及其结合处,在手电筒光照射下有亮晶晶的白光,样品布仍未完全透明;随含浸时间的增加,要注意纵向和横向玻璃丝的结合处,是否还有闪亮晶晶的白光,样品布是否完全透明。当含浸在水杨酸甲酯中的玻璃布,在手电筒光照射下,所有区域不再闪亮晶晶的白光,玻璃布与试剂完全融为一体,即含浸点到,停止计时.从含浸开始,到含浸停止计时,所花时间就是含浸时间,
77.(3)压板后耐热性测试方法:
78.将已经完成表面处理的玻纤布含浸树脂后得到半固化片ccl,将2张板半固化片压片叠合,双面覆铜箔后进行压板得到0.15mm厚度覆铜板.将覆铜板两面的铜时刻掉,裁切为5cm*5cm大小的样品,磨边后放入高温烘箱中烘烤,设定温度为270℃/288℃/300℃各2h,利用静态热-力分析tma仪器观察是否起泡分层。
79.(3)耐离子迁移性测试
80.参考行业内标准测试方法,将样品制作为双面pcb测试板,孔径为0.35mm,孔间距为0.3mm。先将测试板烘干,烘干条件为105℃/6hrs,在用260℃回流焊6次,将其放置在23℃,适度50%的条件下存放24小时,再进行耐离子迁移性测试,环境条件为温度80℃,湿度85%,施加100v电压,随时间的延长孔间距逐渐绝缘失效,失效判定标准为电阻小于1兆欧姆。
81.试验结果见表1。
82.表1不同表面处理剂对含浸时间性能、耐热性等的影响结果
83.[0084][0085]
◎
:无起泡,无分层;
×
:起泡分层
[0086]
以上所述仅为本发明的较佳实施例,但这些实施例仅是范例性的,并不对本发明的范围构成任何限制。本领域技术人员应该理解的是,在不偏离本发明的精神和范围下可以对本发明技术方案的细节和形式进行修改或替换,但这些修改和替换均落入本发明的保护范围内。