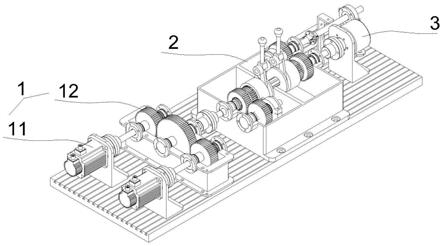
1.本发明涉及实验装置技术领域,尤其涉及一种旋转机械的故障模拟系统。
背景技术:
2.作用一种常用的机械结构,旋转机械被广泛地应用在电力、航空航天、冶金、风力发电、核力发电以及国防等现代化工业领域。随着机械设备向着高速、重载、精密的方向发展,人们对机械设备的安全性、稳定性、可靠性等性能的要求也不断提高。
3.由于旋转机械的运行状态对机械设备能否安全运行有着至关重要的影响,而且大多机械设备的工作环境较为恶劣,工作过程中会受到各种交变载荷、冲击的作用,极易出现故障。故搭建旋转机械故障模拟试验平台,以对旋转机械中关键部件的故障进行研究,是十分必要的。
4.由于现有的旋转机械故障模拟平台的驱动力通常是由单一的旋转驱动件所提供,而单一的旋转驱动件只能输出设定的转速或转矩,因而现有的旋转机械故障模拟平台只能对单一工况下的旋转机械进行模拟,无法很好的复现机械设备运行的实际情况。
5.故亟需一种旋转机械的故障模拟系统,以解决现有的旋转机械故障模拟平台存在的只能对单一工况下的旋转机械进行模拟的问题。
技术实现要素:
6.有鉴于此,有必要提供一种旋转机械的故障模拟系统,以解决现有的旋转机械故障模拟平台存在的只能对单一工况下的旋转机械进行模拟的问题。
7.本发明提供一种旋转机械的故障模拟系统,包括驱动装置、故障模拟平台、负载装置以及控制采集系统;
8.所述驱动装置包括两个驱动件以及齿轮箱,所述齿轮箱具有两个输入端,两个所述驱动件分别与所述齿轮箱的两个输入端固定连接,以分别驱动所述齿轮箱的两个输入端转动,所述齿轮箱的输出端与所述故障模拟平台的输入端固定连接,所述故障模拟平台的输出端与所述负载装置固定连接;
9.所述控制采集系统分别与两个所述驱动件以及负载装置电连接,以分别控制两个所述驱动件的输出转速、输出转矩和控制所述负载装置的输出负载,所述控制采集系统还用于采集所述故障模拟平台的运动状态数据。
10.进一步的,所述故障模拟平台包括壳体、第一转轴、两个传动齿轮、两个齿轮故障模拟模块以及切换机构,所述齿轮箱的输出端与所述第一转轴的输入端固定连接,所述第一转轴与所述壳体转动连接,所述第一转轴的输出端与所述负载装置固定连接;
11.两个所述传动齿轮间隔套设于所述第一转轴上、并分别与所述第一转轴转动连接,所述传动齿轮与所述齿轮故障模拟模块一一对应、并与所述齿轮故障模拟模块啮合;
12.所述切换机构可分别使两个所述传动齿轮处于第一状态或第二状态,当所述传动齿轮处于第一状态时,所述传动齿轮可相对所述第一转轴转动,当所述传动齿轮处于第二
状态时,所述传动齿轮与所述第一转轴限位;
13.所述控制采集系统用于采集两个所述齿轮故障模拟模块的运动状态数据。
14.进一步的,所述切换机构包括两组切换组件,所述切换组件与所述传动齿轮一一对应;
15.所述切换组件包括限位件以及套筒,所述限位件以及套筒间隔套设于所述第一转轴上,所述限位件的侧面与所述传动齿轮的侧面固定连接,所述套筒与所述第一转轴滑动连接、并可随所述第一转轴转动,所述套筒的内部开设有与所述限位件配合的限位槽;
16.可滑动所述套筒,以使所述套筒处于第一位置或第二位置,当所述套筒处于第一位置时,所述套筒与所述限位件分离,当所述套筒处于第二位置时,所述套筒与所述限位件限位。
17.进一步的,所述故障模拟平台还包括轴承故障模拟模块,所述轴承故障模拟模块的输入轴与任一所述齿轮故障模拟模块的输出轴可拆卸连接,所述控制采集系统还用于采集所述轴承故障模拟模块的运动状态数据。
18.进一步的,所述齿轮故障模拟模块包括故障齿轮、第二转轴以及齿轮安装座,所述第二转轴的一端与所述壳体转动连接,所述第二转轴的另一端与所述齿轮安装座转动连接,所述故障齿轮套设于所述第二转轴上、并与所述第二转轴固定连接,所述故障齿轮与所述传动齿轮啮合。
19.进一步的,所述轴承故障模拟模块包括故障轴承、第三转轴以及轴承安装座,所述第三转轴的一端与其中一所述第二转轴的一端可拆卸连接,所述故障轴承套的内圈设于所述第三转轴上、并与所述第三转轴固定连接,所述轴承安装座套设于所述故障轴承的外部、并与所述故障轴承的外圈固定连接。
20.进一步的,所述故障模拟平台还包括对开式联轴器,所述第三转轴的一端与其中一所述第二转轴的一端通过所述对开式联轴器可拆卸连接。
21.进一步的,所述控制采集系统包括工控机、plc模块、运动控制系统以及模拟量采集系统;
22.所述工控机与所述plc模块电连接,所述plc模块与所述运动控制系统以及模拟量采集系统电连接,所述工控机用于通过所述plc模块和运动控制系统来分别控制两个所述驱动件的输出转速、输出转矩以及控制所述负载装置的输出负载;
23.所述工控机还用于通过所述plc模块和模拟量采集系统采集两个所述齿轮故障模拟模块和轴承故障模拟模块的运动状态数据。
24.进一步的,所述运动控制系统包括运动控制模块、两个伺服驱动器以及张力控制器;
25.所述plc模块与所述运动控制模块电连接,所述运动控制模块分别通过两个所述伺服驱动器与两个所述驱动件电连接,以分别控制两个所述驱动件的输出转速、输出转矩,所述运动控制模块还通过所述张力控制器与所述负载装置电连接,以控制所述负载装置的输出负载。
26.进一步的,所述模拟量采集系统包括模拟量采集模块、加速度传感器以及位移传感器;
27.所述plc模块通过所述模拟量采集模块与所述加速度传感器和所述位移传感器电
连接,以通过所述加速度传感器采集两个所述齿轮故障模拟模块以及轴承故障模拟模块的加速度数据,通过所述位移传感器采集所述轴承故障模拟模块的输入轴以及与所述轴承故障模拟模块连接的所述齿轮故障模拟模块的输出轴的位移数据。
28.相较于现有技术,本发明提供了一种旋转机械的故障模拟系统,该故障模拟系统包括故障模拟平台、分别与故障模拟平台的输入端和输出端固定连接的驱动装置和负载装置以及与驱动装置和负载装置电连接的控制采集系统。在实际的使用过程中,工作人员可通过控制采集系统控制驱动装置所输出的转矩、转速以及控制负载装置的输出负载、并通过控制采集系统采集故障模拟平台的运动状态数据,以此来对多种工况下的旋转机械进行模拟。
附图说明
29.图1为本发明提供的旋转机械的故障模拟系统一优选实施例的结构示意图;
30.图2为本发明提供的旋转机械的故障模拟系统中,控制采集系统一优选实施例的结构框图;
31.图3为本发明提供的旋转机械的故障模拟系统中,故障模拟平台一优选实施例的结构示意图;
32.图4为本发明提供的旋转机械的故障模拟系统中,第一转轴、传动齿轮以及切换机构一优选实施例的结构示意图;
33.图5为本发明提供的旋转机械的故障模拟系统中,齿轮故障模拟模块一优选实施例的结构示意图;
34.图6为本发明提供的旋转机械的故障模拟系统中,轴承故障模拟模块一优选实施例的结构示意图;
35.图7为本发明提供的旋转机械的故障模拟系统中,对开式联轴器一优选实施例的爆炸图;
36.图8为本发明提供的旋转机械的故障模拟系统中,运动控制系统一优选实施例的结构框图;
37.图9为本发明提供的旋转机械的故障模拟系统中,模拟量采集系统一优选实施例的结构框图。
38.图中:1、驱动装置,11、驱动件,12、齿轮箱,2、故障模拟平台,21、壳体,22、第一转轴,23、传动齿轮,24、齿轮故障模拟模块,241、故障齿轮,242、第二转轴,243、齿轮安装座,25、切换机构,251、切换组件,2511、限位件,2512、套筒,2513、拨叉,26、轴承故障模拟模块,261、故障轴承,262、第三转轴,263、轴承安装座,27、对开式联轴器,271、半联轴器,272、紧固件,273、限位条,3、负载装置,4、控制采集系统,41、工控机,42、plc模块,43、运动控制系统,431、运动控制模块,432、服驱动器,433、张力控制器,44、模拟量采集系统,441、模拟量采集模块,442、加速度传感器,443、位移传感器,45、控制按钮模块,46、指示模块。
具体实施方式
39.下面结合附图来具体描述本发明的优选实施例,其中,附图构成本技术一部分,并与本发明的实施例一起用于阐释本发明的原理,并非用于限定本发明的范围。
40.请参阅图1和图2,本发明提供了一种旋转机械的故障模拟系统,该故障模拟系统包括驱动装置1、故障模拟平台2、负载装置3以及控制采集系统4。
41.所述驱动装置1包括两个驱动件11以及齿轮箱12,所述齿轮箱12具有两个输入端,两个所述驱动件11分别与所述齿轮箱12的两个输入端固定连接,以分别驱动所述齿轮箱12的两个输入端转动,所述齿轮箱12的输出端与所述故障模拟平台2的输入端固定连接,以向所述故障模拟平台2提供驱动力。所述故障模拟平台2的输出端与所述负载装置3固定连接,以向所述故障模拟平台2提供负载。
42.所述控制采集系统4分别与两个所述驱动件11电连接,以分别控制两个所述驱动件11的输出转速、输出转矩(即控制一个所述驱动件11的输出转速,控制另一所述驱动件11的输出转矩),从而可对所述驱动装置1所输出的驱动力的转速以及转矩进行控制。所述控制采集系统4还与所述负载装置3电连接,以控制所述负载装置3的输出负载。除此之外,所述控制采集系统4还用于采集所述故障模拟平台2的运动状态数据。
43.在实际的使用过程中,工作人员可通过所述控制采集系统4控制所述驱动装置1所输出的转矩、转速以及控制所述负载装置3的输出负载、并通过控制所述采集系统4采集所述故障模拟平台2的运动状态数据,以此来对多种工况下的旋转机械进行模拟,从而使得所述故障模拟平台2能够更好的复现机械设备运行的实际情况。
44.请参阅图1和图3,作为优选的实施例,所述故障模拟平台2包括壳体21、第一转轴22、两个传动齿轮23、两个齿轮故障模拟模块24以及切换机构25,所述齿轮箱12的输出端与所述第一转轴22的输入端固定连接,所述第一转轴22与所述壳体21转动连接,所述第一转轴22的输出端与所述负载装置3固定连接。
45.两个所述传动齿轮23间隔套设于所述第一转轴22上、并分别与所述第一转轴22转动连接,所述齿轮故障模拟模块24具有一可相对其他部分转动的故障齿轮,所述传动齿轮23与所述齿轮故障模拟模块24一一对应、并与所述齿轮故障模拟模块24的故障齿轮啮合。其中,故障齿轮的故障类型可为断齿、裂纹、凹坑等常见的故障类型。在实际的使用过程中,工作人员可通过更换具有不同故障类型的所述齿轮故障模拟模块24,来实现不同故障类型的模拟。
46.所述切换机构25可分别使两个所述传动齿轮23处于第一状态或第二状态,当所述传动齿轮23处于第一状态时,所述传动齿轮23可相对所述第一转轴22转动,此时,在所述第一转轴22转动的过程中,所述传动齿轮23不会跟随所述第一转轴22转动;当所述传动齿轮23处于第二状态时,所述传动齿轮23与所述第一转轴22限位,此时,所述传动齿轮23会跟随所述第一转轴22转动、并带动所述齿轮故障模拟模块24的故障齿轮转动。所述控制采集系统4用于采集两个所述齿轮故障模拟模块24中的故障齿轮的运动状态数据。
47.相较于其他实施例,本实施例中的所述故障模拟平台2不仅可实现故障齿轮的单一模拟、故障齿轮的复合模拟,还可实现两种模拟状态之间的快速切换。
48.不仅如此,将所述齿轮故障模拟模块24进行模块化,还可方便工作人员在任一模拟状态下进行多种模拟类型之间的快速切换。
49.请参阅图4,作为优选的实施例,所述切换机构25包括两组切换组件251,所述切换组件251与所述传动齿轮23一一对应,所述切换组件251包括限位件2511以及套筒2512,所述限位件2511以及套筒2512间隔套设于所述第一转轴22上、并位于所述传动齿轮23的一
侧,所述限位件2511的侧面与所述传动齿轮23的侧面固定连接,所述套筒2512与所述第一转轴22滑动连接、并可随所述第一转轴22转动,在更为具体的实施例中,所述套筒2512通过嵌设于所述第一转轴22上的平键与所述第一转轴22滑动连接。
50.所述套筒2512的内部开设有与所述限位件2511配合的限位槽。工作人员在使用过程中,可驱动所述套筒2512相对于所述第一转轴22滑动,以使所述套筒2512处于第一位置或第二位置。当所述套筒2512处于第一位置时,所述套筒2512与所述限位件2511分离,此时,所述限位件2511不会跟随所述套筒2512转动;当所述套筒2512处于第二位置时,所述套筒2512与所述限位件2511限位,此时,所述限位件2511以及传动齿轮23会跟随所述套筒2512转动。
51.请继续参阅图4,在更为优选的实施例中,所述切换组件251还包括拨叉2513,所述拨叉2513卡设于所述套筒2512的外部、并可相对于所述套筒2512转动。在使用过程中,工作人员可通过所述拨叉2513来驱动所述套筒2512相对所述第一转轴22滑动。相较于其他实施例,当所述传动齿轮23、齿轮故障模拟模块24以及切换机构25全部位于所述壳体21中时,本实施例中的所述拨叉2513,可方便工作人员对所述套筒2512的位置进行调节。
52.请参阅图3,作为优选的实施例,所述故障模拟平台2还包括轴承故障模拟模块26,所述轴承故障模拟模块26的输入轴与任一所述齿轮故障模拟模块24的输出轴可拆卸连接,其中,所述轴承故障模拟模块26的故障类型可为滚动体点缺陷、滚动体裂纹、内圈凹坑、内圈裂纹等常见的故障类型。在实际的使用过程中,工作人员可通过更换具有不同故障类型的所述轴承故障模拟模块26,来实现不同故障类型的模拟。
53.所述控制采集系统4还用于采集所述轴承故障模拟模块26的运动状态数据。
54.相较于其他实施例,本实施例中的所述故障模拟平台2不仅可实现故障齿轮的单一模拟、故障轴承的单一模拟(此时,需要将与所述轴承故障模拟模块26连接的所述齿轮故障模拟模块24中的故障齿轮更换为完好的齿轮)、两个故障齿轮的复合模拟、一个故障齿轮与故障轴承的复合模拟以及两个故障齿轮与故障轴承的复合模拟,还可进行上述五种模拟状态的快速切换。
55.不仅如此,将所述轴承故障模拟模块26进行模块化,还可方便工作人员在任一模拟状态下进行多种模拟类型之间的快速切换。
56.请参阅图5,作为优选的实施例,所述齿轮故障模拟模块24包括故障齿轮241、第二转轴242以及齿轮安装座243,所述第二转轴242的一端与所述壳体21转动连接,所述第二转轴242的另一端与所述齿轮安装座243转动连接,所述故障齿轮241套设于所述第二转轴242上、并与所述第二转轴242固定连接,所述故障齿轮241与所述传动齿轮23啮合,相较于其他的齿轮故障模拟模块,本实施例中的齿轮故障模拟模块结构更加简单,更加实用。
57.请参阅图6,作为优选的实施例,所述轴承故障模拟模块26包括故障轴承261、第三转轴262以及轴承安装座263,所述第三转轴262的一端与其中一所述第二转轴242的一端可拆卸连接,所述故障轴承261套的内圈设于所述第三转轴262上、并与所述第三转轴262固定连接,所述轴承安装座263套设于所述故障轴承261的外部、并与所述故障轴承261的外圈固定连接。相较于其他的轴承故障模拟模块,本实施例中的轴承故障模拟模块结构更加简单,更加实用。
58.请继续参阅图3,作为优选的实施例,所述故障模拟平台2还包括对开式联轴器27,
所述第三转轴262的一端与其中一所述第二转轴242的一端通过所述对开式联轴器27可拆卸连接。相较于其他的联轴器,对开式联轴器在安装、拆卸时,更加方便、快捷。
59.请参阅图7,作为优选的实施例,所述对开式联轴器27包括两组半联轴器271、若干个紧固件272以及若干个限位条273,两组所述半联轴器271通过若干个所述紧固件272可拆卸连接,两组所述半联轴器271在连接时,可形成一圆柱形容纳腔,以容纳所述第三转轴262以及与所述第三转轴262连接的第二转轴242。
60.所述第三转轴262以及与所述第三转轴262连接的第二转轴242均开设有若干个第一限位槽(图中未示出),所述容纳腔的腔壁在对应若干个所述第一容纳槽的位置开设有若干个第二容纳槽(图中未示出)。若干根所述限位条273可分别嵌设于若干个所述第一容纳槽以及若干个所述第二容纳槽中,以在所述第三转轴262以及与所述第三转轴262连接的转动过程中,防止所述对开式联轴器27相对所述第三转轴262以及与所述第三转轴262连接的第二转轴242转动。
61.请参阅图2,作为优选的实施例,所述控制采集系统4包括工控机41、plc模块42、运动控制系统43以及模拟量采集系统44。
62.所述工控机41与所述plc模块42电连接,所述plc模块42与所述运动控制系统43以及模拟量采集系统44电连接,所述工控机41可通过所述plc模块42和运动控制系统43来分别控制两个所述驱动件11的输出转速、输出转矩以及控制所述负载装置3的输出负载。
63.除此之外,所述工控机41还可通过所述plc模块42和模拟量采集系统44采集两个所述齿轮故障模拟模块24和轴承故障模拟模块26的运动状态数据。
64.相较于其他实施例,在本实施例提供的所述控制采集系统4中,工作人员不仅可通过所述工控机41快速调节两个所述驱动件11的输出转速、输出转矩以及调节所述负载装置3的输出负载,还可通过其中的(所述工控机41中的)数据采集软件来实现示波采样、高精度频率计、时域分析、频域分析和自谱分析等操作。
65.请参阅图8,作为优选的实施例,所述运动控制系统43包括运动控制模块431、两个伺服驱动器432以及张力控制器433。
66.所述plc模块42与所述运动控制模块431电连接,所述运动控制模块431分别通过两个所述伺服驱动器432与两个所述驱动件11电连接,以分别控制两个所述驱动件11的输出转速、输出转矩。所述运动控制模块431还通过所述张力控制器433与所述负载装置3电连接,以控制所述负载装置3的输出负载。在更为具体的实施例中,所述驱动件11可为伺服电机,所述负载装置3可为磁粉制动器。
67.相较于其他实施例,本实施中通过所述伺服驱动器432和张力控制器433控制所述驱动件11和负载装置3的方式,控制效果更好,性价比更高。
68.请参阅图9,作为优选的实施例,所述模拟量采集系统44包括模拟量采集模块441、三组加速度传感器442以及两组位移传感器443,三组所述加速度传感器442分别设置于两个所述齿轮故障模拟模块24以及轴承故障模拟模块26的附近,两组位移传感器443分别设置于所述轴承故障模拟模块26的输入轴以及与所述轴承故障模拟模块26的输入轴连接的所述齿轮故障模拟模块24的输出轴附近。在更为具体的实施例,所述位移传感器443为电涡流位移传感器。
69.所述plc模块42通过所述模拟量采集模块441与三组所述加速度传感器442和两组
所述位移传感器443电连接,以通过三组所述加速度传感器442采集两个所述齿轮故障模拟模块24以及轴承故障模拟模块26的加速度数据,以通过两组所述位移传感器443采集所述轴承故障模拟模块26的输入轴以及与所述轴承故障模拟模块26连接的所述齿轮故障模拟模块24的输出轴的位移数据。
70.相较于测量其他数据,测量加速度数据以及位移数据能够能好的得出所述齿轮故障模拟模块24以及轴承故障模拟模块26的运动状态。
71.在更为优选的实施例中,一组所述加速度传感器442包括两个加速度传感器442,两个所述加速度传感器442分别用于对所述齿轮故障模拟模块24或所述轴承故障模拟模块26,在水平方向以及竖直方向的加速度数据进行采集。
72.一组所述位移传感器443包括两个位移传感器443,两个所述位移传感器443分别用于对所述轴承故障模拟模块26的输入轴以及所述轴承故障模拟模块26连接的所述齿轮故障模拟模块24的输出轴,在水平方向以及竖直方向的位移数据进行采集。
73.相较于其他实施例,本实施例中同时采集水平方向以及竖直方向的数据的方式,更加精确。
74.请参阅图2,在更为优选的实施例中,所述控制采集系统4还包括控制按钮模块45,所述控制按钮模块45包括两个所述驱动件11的启动按钮和停止按钮以及急停按钮,所述plc模块42分别与所述启动按钮、停止按钮以及急停按钮电连接,以便于工作人员通过所述启动按钮、停止按钮以及急停按钮直接控制两个所述驱动件11的启动、停止以及急停。除此之外,相较于其他实施例,具有所述急停按钮的所述控制采集系统4具有更高的安全性,即在所述工控机41出现死机或其他故障时,可直接通过所述急停按钮将两个所述驱动件11强制停下。
75.请继续参阅图2,在更为优选的实施例中,所述控制采集系统4还包括指示模块46,所述指示模块46由若干个指示灯组成,所述指示模块46与所述plc模块42电连接,以在所述控制采集系统4的控制过程、数据收集过程中起到提示作用。
76.为了更好地了解本发明,以下结合图1至图7对本发明进行详细说明:
77.在实际的使用过程中,工作人员可先将所述轴承故障模拟模块26与所述齿轮故障模拟模块24连接或断开,再选择将与所述轴承故障模拟模块26连接的所述齿轮故障模拟模块24作为传动部件(此时,需要将与所述轴承故障模拟模块26连接的所述齿轮故障模拟模块24中的故障齿轮241更换为完好的齿轮)或故障模拟模块,再通过两组所述切换组件251切换两个所述传动齿轮23的运动状态,来选择一种想要进行模拟的模拟状态。之后,再更换需要进行模拟的所述齿轮故障模拟模块24以及轴承故障模拟模块26的故障类型,来选择一种想要进行模拟的故障类型。
78.选择完成后,再通过所述工控机41分别控制两个所述驱动件11的输出转矩、输出转矩以及控制所述负载装置3的输出负载,来对多种工况进行模拟。而在模拟的过程中,工作人员可直接通过所述工控机41上所显示的数据,进行记录或分析处理。
79.综上,本发明提供的旋转机械的故障模拟系统在使用过程中,不仅可实现多种模拟状态以及任一模拟状态下的多种模拟类型,还可实现多种模拟状态之间的快速切换以及任一模拟状态下的多种模拟类型之间的快速切换。之后,还可通过驱动装置以及负载装置来对多种工况进行模拟。除此之外,在模拟过程中,工作人员可直接通过工控机上所显示的
数据,进行记录或分析处理。
80.以上所述,仅为本发明较佳的具体实施方式,但本发明的保护范围并不局限于此,任何熟悉本技术领域的技术人员在本发明揭露的技术范围内,可轻易想到的变化或替换,都应涵盖在本发明的保护范围之内。