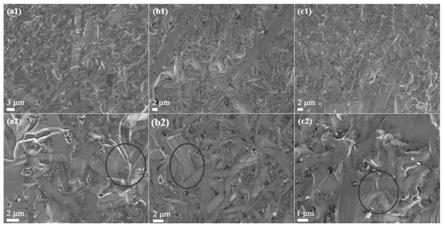
自蔓延燃烧合成
β-sic粉无压烧结制备高密度陶瓷的方法
技术领域
1.本发明涉及β-sic烧结制备陶瓷技术领域,具体地,涉及一种自蔓延燃 烧合成β-sic粉无压烧结制备高密度陶瓷的方法。
背景技术:
2.碳化硅(sic)陶瓷材料是一种重要的结构陶瓷材料,因其耐高温、耐 磨损、热膨胀系数小、热导率大,同时具备优良的抗氧化性和耐腐蚀性, 可广泛应用于航空航天,发动机部件、核反应堆和磨具。例如,在石油化 工中被用于各种耐腐蚀管道;在汽车工业中用作密封环零部件;在机械工 业中制作各种耐磨、耐高温、耐腐蚀器件等。并且由于碳化硅在中子辐射 下的低活性,被科学家认为是核燃料的理想包壳材料。
3.sic是一种仅次于金刚石的强共价键化合物,其硅碳键共价性:离子性 为7.3:1。sic分子构型为si-c四面体,si原子位于中心,四个c原子分 别围绕着si原子。sic的基本结构单元是共价键结合[sic4]和[csi4]配位四 面体,这些[sic4]和[csi4]的底部是以互相平行或反平行结合堆积的,这些 四面体共边形成平面层,并以顶点与下一叠层四面体相连形成三维结构。 sic有β和α两种晶体结构,在温度低于1600℃时,以β-sic的形式存在, 为面心立方晶系闪锌矿结构,密度为3.215g/cm3。当温度高于1600℃时, β-sic开始往α-sic转化,温度高于2100℃时完全转变为α-sic,有2h、4h、 6h、15r等多型体,α-sic的多型体密度大致为3.217g/cm,其中6h多型 体在工业中得到广泛应用。
[0004]
β-sic的制备方法总体可分为三种,即固相法、液相法和气相法,其中 固相法又包含碳热还原法(即acheson法)、硅碳直接反应法、机械合金 化法和自蔓延燃烧合成法;液相法包含溶胶凝胶法和聚合物分解法;气相 法包括化学气相沉积法(cvd法)、激光诱导化学气相沉积法(licvd法) 和等离子体法。其中,液相法和气相法受实验条件和产量的限制不可能应 用于工业上大量生产,而固相法中的碳热还原法耗能高、污染大,机械合 金化法会引入杂质,硅碳直接反应法也需要高温和长时间来反应合成β-sic, 自蔓延燃烧合成(shs),在传统的shs方案中,将固态粉末的反应混合 物一端点燃,然后将其全部点燃。高温燃烧波阵面在介质中传播,从而将 前驱体转化为所需的产物。shs法的一些特征包括:1)反应时间短;2) 能源效率高;3)简单的技术设备;4)高反应速率和相对较快的冷却速度。 由于极高的燃烧温度“燃烧”了大部分杂质,产生了自净化效果。因此, 自蔓延燃烧合成β-sic粉技术是一种可以推向大规模工业化生产高品质、超 细β-sic粉体的一种低成本、节能环保的生产技术。
[0005]
截止目前,用ahceson法工艺生产的β-sic粉,以prochazka提出的固 相烧结sic的理论为基础,添加少量b、c为烧结助剂,无压烧结sic陶瓷 的致密度可达97%以上,然而用自蔓延燃烧合成的β-sic粉烧结的sic陶 瓷致密度仅达到86%。究其原因,一是sic陶瓷的烧结驱动力来自于粉体 的表面能,自蔓延燃烧合成的β-sic粉体平均粒径大,比表面积小,阻碍了 sic陶瓷的致密化,所以需要进一步的机械激活使得自蔓延燃烧合成的 β-sic粉的粒径下降,增加其表面能;二是自蔓延燃烧合成的β-sic粉的初 始纯度只有90%左右,即使
经过酸洗纯化也只能提升到94%左右,所以需 要研究针对自蔓延燃烧合成β-sic粉的酸洗纯化工艺,使得自蔓延燃烧合成 β-sic粉的纯度达到98%以上;三是以β-sic粉为原料,由于在高温下(》1950 (c)sic粉体发生β相
→
α相的晶型转变,并伴有沿一维方向优先取向的 晶粒的异常长大,阻碍了试样的致密化,造成密度下降,所以要严格控制 烧结温度和保温时间,抑制晶粒过分长大,使其致密化。
[0006]
综上来说,与传统的α-sic相比,自蔓延燃烧合成的β-sic微粉具有反 应时间短、纯度高等优点。但是,自蔓延燃烧合成法所制备出来的β-sic微 粉,粒径大、比表面积小、表面活性低,不满足无压固相烧结要求,很难 制备出高质量的陶瓷,因此需要对β-sic微粉进行活化等处理,提高表面活 化能,同时对烧结工艺进行研究,以拓展自蔓延燃烧合成的β-sic微粉在碳 化硅陶瓷材料领域的应用。
技术实现要素:
[0007]
本发明要解决的技术问题在于,提供一种自蔓延燃烧合成β-sic粉无压 烧结制备高密度陶瓷的方法,通过机械激活和酸洗纯化,提高表面活化能、 提高纯度,再通过控制烧结助剂c、b及控制烧结工艺,以期利用自蔓延燃 烧合成β-sic粉作为原料,制备获得致密的、力学性能优异的sic陶瓷材料。
[0008]
本发明提供了一种自蔓延燃烧合成β-sic粉无压烧结制备高密度陶瓷 的方法,包括以下步骤:
[0009]
(1)机械激活:将β-sic原粉放入搅拌磨中,然后加入去离子水,并 加入四甲基氢氧化铵作为分散助剂,再加入氧化锆球作为研磨介质,研磨 24~72h进行机械激活,得到活性β-sic亚微米粉体;
[0010]
(2)酸洗纯化:将机械激活后的β-sic亚微米粉体,放入容器中,用 沸腾的蒸馏水将β-sic粉体打湿,在80
±
5℃下进行水浴至恒温,然后分一 次或两次加入酸液搅拌均匀,每次反应30~90min,加入的酸液为浓硫酸、 氢氟酸或浓盐酸中的一种或几种组成的混合酸,反应结束后冷却并排酸处 理,然后进行干燥,得到纯度大于98%的β-sic微粉;
[0011]
(3)球磨制浆:按照一定重量比例称取固态原料活性β-sic微粉,加 入b源b4c和c源酚醛树脂,并加入zro2球磨介质,共同加入球磨机中球 磨混合10~20min,再加入5~15wt%的分散剂,继续球磨混合30~60min得 到浆料;
[0012]
(4)干压成型:将浆料烘干并过筛,将过筛后的混合粉体置于液压成 型机中,在50~150mpa压力下干压成型形成初坯,然后再置于冷等静压机 中在150~250mpa压力下压制成坯体;
[0013]
(5)无压烧结:将坯体置于烧结炉中,抽真空、充入保护气体,然后 以6℃/min的速率升温至700~900℃,保温预烧30min;再以8℃/min的速 率升温至1950℃~2130℃,保温烧结30~120min后自然冷却至室温。
[0014]
优选的,所述步骤(1)中的β-sic原粉初始平均粒径为5.471μm,比 表面积为6.34m2/g,纯度为90.4%,氧含量为2wt%的自蔓延燃烧合成的 β-sic粉体。
[0015]
优选的,所述步骤(1)中加水后固体重量比为60%。
[0016]
优选的,所述步骤(1)中氧化锆球磨介质的粒径为0.4~2mm。
[0017]
优选的,所述步骤(1)中球磨时间为72h,先加入2mm氧化锆球, 研磨36h,再更换
0.4mm氧化锆球,继续研磨36h。
[0018]
优选的,所述步骤(2)中混合酸中浓硫酸溶液与氢氟酸溶液的质量比 为1:1,其中浓硫酸的质量浓度不低于90%,氢氟酸溶液的浓度不低于40%。
[0019]
优选的,所述步骤(2)中的排酸步骤为:向混合料中加入自来水然后 静置分层,排出上层清液,重复操作至ph=5,再加入去离子水自然静置分 层,再排出上层清液,再重复上述操作至ph=7,将清液全部排出。
[0020]
优选的,所述步骤(2)中沸腾蒸馏水的加入质量为β-sic粉体的1~3 倍。
[0021]
优选的,所述步骤(3)中的b的添加量为0.7wt%,c的添加量为4wt%, 分散剂的加入量为10wt%;所述分散剂包括以下重量份组分:乙醇6~8份、 油酸0.3~2份、聚乙烯醇0.4~1份、四甲基氢氧化铵0.1~1份。
[0022]
优选的,所述步骤(5)中烧结温度为2100℃,保温烧结时间为90min。
[0023]
本发明的有益效果:本发明采用自蔓延燃烧合成的β-sic粉,通过机械 激活、酸洗纯化,提高表面活化能、提高纯度,制备了适合烧结的高性能 亚微米级粉体。再通过控制烧结助剂c、b及控制烧结工艺,以期利用自蔓 延燃烧合成β-sic粉作为原料,制备获得致密的、力学性能优异的β-sic陶 瓷材料。具体地:
[0024]
(1)采用初始平均粒径为5.471μm,比表面积为6.34m2/g,纯度为 90.4%,氧含量为2wt%的自蔓延燃烧合成的β-sic粉体,使用搅拌磨研磨 进行机械激活,使其达到可烧结的亚微米级,制备了d
50
=0.418μm的β-sic 微粉,最佳的机械激活方式为先加入2mm氧化锆球,研磨36h,再更换 0.4mm氧化锆球,继续研磨36h;通过机械激活对物料进行冲击、碰撞、 剪切、分散、研磨等手段的实现来达到所需产品的颗粒的大小和粒度,同 时机械力作用所产生的能量施加在颗粒表面时,会使得颗粒发生晶格缺陷、 无定形化和晶格缺陷等,同时还会伴随着表面游离基形成,通过科学的机 械激活处理,提高激活效率。
[0025]
(2)经过机械激活后的β-sic粉中含有zro2等杂质,β-sic微粉经过 浓h2so4:hf=1:1的混合酸酸洗纯化得到适合无压烧结、纯度较高的β-sic 微粉,其纯度大于98%,氧含量为0.89wt%,比表面积为18.46m2/g,烧结 活性较好,利于烧结,在经济成本和时间效率的综合考量下,浓h2so4和 hf的组合相比于其他三组最优。
[0026]
(3)选用烧结活性好的自蔓延燃烧合成的β-sic微粉,加入b4c和酚 醛树脂作为烧结助剂,采用平均粒径d
50
=0.22μm的b4c作为硼源,采用酚 醛树脂作为有机碳源,其为有机物,分子式为(c8h8o2)n,又俗称电木, 酚醛树脂在其中起到粘结剂的作用,可以提高素坯的强度,其在高温惰性 气氛下酚醛树脂会将h和o以h2o的比例脱去,从而剩下c。这是因为在 烧结sic陶瓷的过程中,高温裂解的c与sio2结合生成sic和co,从而 增加粉体的表面能(eb),降低晶界能(es),增加了β-sic粉的烧结活 性。
[0027]
(4)通过控制b、c的添加量及烧结温度和保温时间,提高无压烧结 自蔓延燃烧合成的β-sic的致密度和力学性能。当b(b4c换算)添加量为 0.7wt%,c(酚醛树脂换算)添加量为4wt%时,在烧结温度为2100℃,保 温时间90min的条件下,制备的sic陶瓷的致密度和力学性能最佳,其烧 失率为7.9%、收缩率为15.6%、密度为3.14g/m3,硬度为25.62
±
0.92gpa, 断裂韧性为4.84
±
0.84mpa
·m1/2
,三点抗弯强度为401.74
±
8.66gpa。
附图说明
[0028]
图1为β-sic粉机械活化前后粒径分布图,其中:(a)机械激活前β-sic 微粉的粒径分布;(b)实施例1;(c)实施例2;(d)实施例3;(e) 实施例4;
[0029]
图2为β-sic粉机械活化过程中的d10、d50和d90随机械激活时间 变化关系图,其中:(a)实施例1;(b)实施例2;(c)实施例3;(d) 实施例4;
[0030]
图3为β-sic粉机械活化前后的sem对比图,其中:(a)-(d)为β-sic 原粉的主要形貌;(e)-(h)为采用实施例4获得的d
50
=0.418μm的β-sic 粉的主要形貌;
[0031]
图4为原粉、粉碎细化以及纯化后的β-sic粉的xrd图;
[0032]
图5为β-sic粉的eds元素面扫,其中:(a)β-sic原粉;(b)实施 例4机械激活后的β-sic粉;(c)实施例4酸洗纯化后的β-sic粉;
[0033]
图6为不同添加量下陶瓷表面sem分析,其中:(a)实施例1;(b) 实施例2;(c)实施例3;(d)实施例4;
[0034]
图7为不同添加量下陶瓷的断口形貌,其中:(a)实施例2;(b)实 施例3;(c)实施例4。图8为抗弯强度测试的三点弯曲示意图,其中,1-试样条,2-辊棒,3
‑ꢀ
加载压头,样条尺寸长a≥35mm,宽b=4
±
0.2mm,高c=3
±
0.2mm;图9 为硬度和断裂韧性测试的压痕示意图,其中:1-压痕,2-裂纹。
具体实施方式
[0035]
为了使本发明技术方案更容易理解,现结合附图采用具体实施例的方 式,对本发明的技术方案进行清晰、完整的描述。
[0036]
一、具体实施例
[0037]
实施例1:
[0038]
本实施例的自蔓延燃烧合成β-sic粉无压烧结制备高密度陶瓷的方法, 包括以下步骤:
[0039]
(1)机械激活:将β-sic原粉放入搅拌磨中,然后加入去离子水,并 加入四甲基氢氧化铵作为分散助剂,再加入2mm的氧化锆球作为研磨介质, 研磨72h进行机械激活,得到活性β-sic亚微米粉体。其中:β-sic原粉初 始平均粒径为5.471μm,比表面积为6.34m2/g,纯度为90.4%,氧含量为 2wt%的自蔓延燃烧合成的β-sic粉体;加水后固体重量比为60%;
[0040]
(2)酸洗纯化:将机械激活后的β-sic亚微米粉体,放入容器中,用 沸腾的蒸馏水将β-sic粉体打湿,在80
±
5℃下进行水浴至恒温,然后先加 入浓硫酸反应0.5h,再倒出浓硫酸加入氢氟酸反应0.5后,冷却并排酸处 理,然后进行干燥,得到纯度大于98%的β-sic微粉。其中:浓硫酸的质 量浓度不低于90%,氢氟酸溶液的浓度不低于40%;排酸步骤为:向混合 料中加入自来水然后静置分层,排出上层清液,重复操作至ph=5,再加入 去离子水自然静置分层,再排出上层清液,再重复上述操作至ph=7,将清 液全部排出;沸腾蒸馏水的加入质量为β-sic粉体的1~3倍。
[0041]
(3)球磨制浆:按照一定重量比例称取固态原料活性β-sic微粉,加 入b源b4c和c源酚醛树脂,并加入zro2球磨介质,共同加入球磨机中球 磨混合10~20min,再加入10wt%
的分散剂,继续球磨混合30~60min得到 浆料;所述b的添加量为0.7wt%,c的添加量为4wt%;所述分散剂包括 以下重量份组分:乙醇7份、油酸1.5份、聚乙烯醇0.6份、四甲基氢氧化 铵0.3份。
[0042]
(4)干压成型:将浆料烘干并过筛,将过筛后的混合粉体置于液压成 型机中,在60~120mpa压力下干压成型形成初坯,然后再置于冷等静压机 中在180~240mpa压力下压制成坯体。
[0043]
(5)无压烧结:将坯体置于烧结炉中,抽真空、充入保护气体,然后 以6℃/min的速率升温至700℃,保温预烧30min;再以8℃/min的速率升 温至1950℃,保温烧结30min后自然冷却至室温。
[0044]
实施例2:
[0045]
本实施例的自蔓延燃烧合成β-sic粉无压烧结制备高密度陶瓷的方法, 包括以下步骤:
[0046]
(1)机械激活:将β-sic原粉放入搅拌磨中,然后加入去离子水,并 加入四甲基氢氧化铵作为分散助剂,再加入0.4mm的氧化锆球作为研磨介 质,研磨72h进行机械激活,得到活性β-sic亚微米粉体。其中:β-sic原 粉初始平均粒径为5.471μm,比表面积为6.34m2/g,纯度为90.4%,氧含 量为2wt%的自蔓延燃烧合成的β-sic粉体;加水后固体重量比为60%。
[0047]
(2)酸洗纯化:将机械激活后的β-sic亚微米粉体,放入容器中,用 沸腾的蒸馏水将β-sic粉体打湿,在80
±
5℃下进行水浴至恒温,然后先加 入浓硫酸反应0.5h,再倒出浓硫酸加入浓盐酸与氢氟酸混合液反应0.5后, 冷却并排酸处理,然后进行干燥,得到纯度大于98%β-sic微粉。其中:浓 硫酸的质量浓度不低于90%,氢氟酸溶液的浓度不低于40%;排酸步骤为: 向混合料中加入自来水然后静置分层,排出上层清液,重复操作至ph=5, 再加入去离子水自然静置分层,再排出上层清液,再重复上述操作至ph=7, 将清液全部排出;沸腾蒸馏水的加入质量为β-sic粉体的1~3倍。
[0048]
(3)球磨制浆:按照一定重量比例称取固态原料活性β-sic微粉,加 入b源b4c和c源酚醛树脂,并加入zro2球磨介质,共同加入球磨机中球 磨混合10~20min,再加入5~15wt%的分散剂,继续球磨混合30~60min得 到浆料;所述b的添加量为0.5~1.0wt%,c的添加量为3~5wt%;所述分散 剂包括以下重量份组分:乙醇6份、油酸2份、聚乙烯醇0.4份、四甲基氢 氧化铵1份。
[0049]
(4)干压成型:将浆料烘干并过筛,将过筛后的混合粉体置于液压成 型机中,在50~100mpa压力下干压成型形成初坯,然后再置于冷等静压机 中在150~200mpa压力下压制成坯体。
[0050]
(5)无压烧结:将坯体置于烧结炉中,抽真空、充入保护气体,然后 以6℃/min的速率升温至800℃,保温预烧30min;再以8℃/min的速率升 温至2000℃,保温烧结60min后自然冷却至室温。
[0051]
实施例3:
[0052]
本实施例的自蔓延燃烧合成β-sic粉无压烧结制备高密度陶瓷的方法, 包括以下步骤:
[0053]
(1)机械激活:将β-sic原粉放入搅拌磨中,然后加入去离子水,并 加入四甲基氢
氧化铵作为分散助剂,再按照1:1的比例加入0.4mm和2mm 的氧化锆球作为研磨介质,研磨72h进行机械激活,得到活性β-sic亚微米 粉体。其中:β-sic原粉初始平均粒径为5.471μm,比表面积为6.34m2/g, 纯度为90.4%,氧含量为2wt%的自蔓延燃烧合成的β-sic粉体;加水后固 体重量比为60%。
[0054]
(2)酸洗纯化:将机械激活后的β-sic亚微米粉体,放入容器中,用 沸腾的蒸馏水将β-sic粉体打湿,在80
±
5℃下进行水浴至恒温,然后先加 入浓硫酸与氢氟酸混合液反应0.5h,再倒出混合酸并加入浓盐酸反应0.5后, 冷却并排酸处理,然后进行干燥,得到纯度大于98%的β-sic微粉。其中: 浓硫酸的质量浓度不低于90%,氢氟酸溶液的浓度不低于40%;排酸步骤 为:向混合料中加入自来水然后静置分层,排出上层清液,重复操作至ph=5, 再加入去离子水自然静置分层,再排出上层清液,再重复上述操作至ph=7, 将清液全部排出;沸腾蒸馏水的加入质量为β-sic粉体的1~3倍。
[0055]
(3)球磨制浆:按照一定重量比例称取固态原料活性β-sic微粉,加 入b源b4c和c源酚醛树脂,并加入zro2球磨介质,共同加入球磨机中球 磨混合10~20min,再加入5~15wt%的分散剂,继续球磨混合30~60min得 到浆料;所述b的添加量为0.5~1.0wt%,c的添加量为3~5wt%;所述分散 剂包括以下重量份组分:乙醇8份、油酸0.3份、聚乙烯醇1份、四甲基氢 氧化铵0.1份。
[0056]
(4)干压成型:将浆料烘干并过筛,将过筛后的混合粉体置于液压成 型机中,在100~150mpa压力下干压成型形成初坯,然后再置于冷等静压 机中在200~250mpa压力下压制成坯体。
[0057]
(5)无压烧结:将坯体置于烧结炉中,抽真空、充入保护气体,然后 以6℃/min的速率升温至900℃,保温预烧30min;再以8℃/min的速率升 温至2130℃,保温烧结120min后自然冷却至室温。
[0058]
实施例4:
[0059]
本实施例的自蔓延燃烧合成β-sic粉无压烧结制备高密度陶瓷的方法, 包括以下步骤:
[0060]
(1)机械激活:将β-sic原粉放入搅拌磨中,然后加入去离子水,并 加入四甲基氢氧化铵作为分散助剂,先加入2mm的zro2球磨介质研磨36h, 再将球磨介质更换成0.4mm的zro2球磨介质研磨36h,进行机械激活,得 到活性β-sic亚微米粉体。其中:β-sic原粉初始平均粒径为5.471μm,比 表面积为6.34m2/g,纯度为90.4%,氧含量为2wt%的自蔓延燃烧合成的 β-sic粉体;加水后固体重量比为60%。
[0061]
(2)酸洗纯化:将机械激活后的β-sic亚微米粉体,放入容器中,用 沸腾的蒸馏水将β-sic粉体打湿,在80
±
5℃下进行水浴至恒温,然后加入 浓硫酸溶液与氢氟酸溶液的质量比为1:1组成的混合酸反应1h,冷却并排 酸处理,然后进行干燥,得到纯度大于98%的β-sic微粉。其中:混合酸 中,其中浓硫酸的质量浓度不低于90%,氢氟酸溶液的浓度不低于40%; 排酸步骤为:向混合料中加入自来水然后静置分层,排出上层清液,重复 操作至ph=5,再加入去离子水自然静置分层,再排出上层清液,再重复上 述操作至ph=7,将清液全部排出;沸腾蒸馏水的加入质量为β-sic粉体的 1~3倍。
[0062]
(3)球磨制浆:按照一定重量比例称取固态原料活性β-sic微粉,加 入b源b4c和c源酚醛树脂,并加入zro2球磨介质,共同加入球磨机中球 磨混合10~20min,再加入5~
15wt%的分散剂,继续球磨混合30~60min得 到浆料;所述b的添加量为0.5~1.0wt%,c的添加量为3~5wt%;所述分散 剂包括以下重量份组分:乙醇7份、油酸1份、聚乙烯醇0.8份、四甲基氢 氧化铵0.7份。
[0063]
(4)干压成型:将浆料烘干并过筛,将过筛后的混合粉体置于液压成 型机中,在80~120mpa压力下干压成型形成初坯,然后再置于冷等静压机 中在180~230mpa压力下压制成坯体。
[0064]
(5)无压烧结:将坯体置于烧结炉中,抽真空、充入保护气体,然后 以6℃/min的速率升温至800℃,保温预烧30min;再以8℃/min的速率升 温至2100℃,保温烧结90min后自然冷却至室温。
[0065]
二、材料的性能测试
[0066]
1.致密度测试
[0067]
采用阿基米德排水法检测sic陶瓷密度,首先称试样干重(m1),样 品经沸水煮0.5-1h后达到饱和称试样湿重(m2)和浮重(m3)。实测密度 按公式(2-1)计算:
[0068]
ρ=[m1/(m
3-m2)]
×
100%
ꢀꢀꢀꢀꢀꢀꢀꢀꢀꢀꢀꢀꢀꢀꢀꢀꢀꢀꢀꢀꢀ
(2-1)
[0069]
式中:m1—sic干重;
[0070]
m2—sic湿重;
[0071]
m3—sic浮重。
[0072]
2.抗弯强度测试
[0073]
将sic陶瓷加工成40mm
×
4mm
×
3mm的样条,依据gb/t 6569-2006 《精细陶瓷弯曲强度试验方法》进行三点抗弯测试,压头的加载速度为0.5 mm/min,跨距30mm。
[0074][0075]
figure 2.3schematic diagram of three-point bending
[0076]
三点弯曲的抗弯强度按公式(2-2)计算:
[0077][0078]
式中:
[0079]
σf——三点弯曲强度(mpa);
[0080]
f——最大载荷(n);
[0081]
l——夹具的下跨距(mm);
[0082]
b——试样的宽度(mm);
[0083]
d——平行于加载方向的试样高度(厚度)(mm)。
[0084]
3.硬度和断裂韧性测试
[0085]
硬度测试采用维氏硬度计,载荷为5kgf,保压时间为10s,取7个点平 均值计算硬度并计算其标准差。
[0086]
断裂韧性采用压痕法,利用维氏硬度计的锥形金刚石压头产生压痕,测 量压痕的对角线和裂纹的长度如图2.4所示,每个样品测量10次,求其平 均值和标准差,计算公式如式(2-3)所示:
[0087]
[0088]
式中:
[0089]
a——压痕对角线一半长度;
[0090]
e——弹性模量(gpa);
[0091]
h——硬度(gpa);
[0092]
c——径向裂纹长度(从压痕中心测量)。
[0093][0094]
4.物相和显微结构(sem)分析
[0095]
采用日本岛津公司xrd-6000对β-sic粉体及烧结后的sic陶瓷进行物 相分析,并采用了eds能谱分析仪,表征了β-sic粉体中各物相分布。
[0096]
采用sem电镜观察了β-sic粉体的颗粒大小及sic烧结制品的平面形 貌、断口形貌和晶粒尺寸等。
[0097]
5.粉体粒度及氧含量分析
[0098]
采用激光粒度仪测试β-sic粉的粒径分布,用(ch3)4noh作分散剂, 将少量粉体加入水去离子水中配制成水基悬浮液,经超声波分散5min后测 定其粒度分布。
[0099]
采用氧含量分析仪测试β-sic粉体的含氧量,充ar气氛作为保护气体, 再用锡囊包裹β-sic样品,在2000-3000℃的高温下,将β-sic中的o与石 墨反应得到co2的含量进一步确定sic中o的含量。
[0100]
三、实施例的技术方案及数据
[0101]
表1:机械激活技术方案对照表
[0102][0103]
表2:酸洗纯化技术方案对照表
[0104][0105]
表3:无压烧结方案对照表
[0106][0107][0108]
四、结果表征与分析:
[0109]
1.机械激活前后粒度分析和显微结构分析
[0110]
1-1.粒度分析
[0111]
对超声分散后的β-sic粉料作粒度分析,如图1(a)-(e)所示。其中, 图1(a)为机械激活前的β-sic微粉粒径分布;图1(b)为实施例1的β-sic 微粉粒径分布;图1(c)为实施例2的β-sic微粉粒径分布;图1(d)为 实施例3的β-sic微粉粒径分布;图1(e)为实施例4β-sic微粉的粒径分 布。
[0112]
图2(a)-(d)为实施例1、实施例2、实施例3和实施例4的β-sic 粉d
10
、d
50
和d
90
随机械激活时间变化关系图。由图2(a)-(d)可知, 机械激活效果最好的是实施例4即先使用2mm的zro2进行机械激活36h, 再用0.4mm的zro2球进行机械激活相同的时间后,其d
50
达到0.418μm, d
90
达到0.733μm,即90%的β-sic微粉粒径都达到了亚微米级,且其粒径 分布范围较窄,如图1(e)所示。且由图1和图2可知,研磨介质(zro2球)的尺寸对β-sic的机械激活效率有着很大的影响,当zro2球越小时, 体积越小,zro2和β-sic的接触面越大,机械激活效率越高。
[0113]
实施例1的β-sic粒径随机械激活变化如图2(a),其最终粒径分布 如图1(b),直径2mm的zro2球在研磨12h后β-sic粉的d
50
达到了0.741 μm,继续研磨发现,sic粉末粒径呈现小幅度的减小,到了72h后,β-sic 粉d
50
达到了0.523μm,d
90
达到了0.867μm;实施例2的β-sic粉体粒径 随机械激活变化如图2(b)所示,在用直径0.4mm的zro2球研磨12h后sic粉体d
50
减小至0.891μm,d
90
减小至1.892μm,初始12h内其机械激 活效率并没有实施例1高,延长机械激活的时间发现,β-sic粉粒径呈现小 幅度减小,直至72h后β-sic粉d
50
达到了0.554μm,d
90
达到了0.748μm; 实施例3的β-sic粒径随机械激活变化如图2(c)所示,当2mm和0.4mm 的zro2球混合使用后,β-sic粉体粒径在机械激活12h后d
50
达到了0.834 μm,d
90
达到了1.494μm,72h后β-sic粉d
50
达到0.564μm,d
90
达到了 0.82μm,其机械激活效果较其他方案相比最差;实施例4的β-sic粒径随 机械激活变化如图2(d)所示,先由2mm的zro2球机械激活12h后,β-sic 粉d
50
达到了0.793μm,36h时sic粉末d
50
达到了0.548μm,更换0.4mm 的zro2球,再机械激活36h后,此时的β-sic粉d
50
达到了0.418μm,d
90
达到了0.733μm,其机械激活效率最高。四种方案对β-sic粉d
10
的机械激 活效率几乎相同,说明机械激活主要针对β-sic其中的较大颗粒,对其较小 颗粒的机械激活并不明显。
[0114]
由实施例1至4四种方案比较可得,zro2球的直径越小,球磨得到了 β-sic粒径越小,且机械激活效率越高。在搅拌磨中,机械激活初期时,β-sic 颗粒所受的zro2球的冲击力大,颗粒粒径减小的较为明显,粒径减小相对 较快,因此,活化初期选择直径较大的球磨介质能更充分地对sic颗粒进 行机械激活。随着机械激活时间的增加,颗粒粒径减小达到了极限尺寸, 此时,大尺寸(2mm)的zro2球不能使β-sic颗粒粒径继续减小,作用在 颗粒表面的机械挤压、冲击能减小,球磨效果减弱,β-sic颗粒的机械激活 方式主要为摩擦破碎,此时更换小尺寸(0.4mm)的zro2球,增加了与β-sic 的接触面,机械激活效率提高。
[0115]
实施例1中,只选择了大尺寸(2mm)的zro2球,在研磨初期时表现 优越,但后期乏力,不能更有效的对β-sic颗粒进行研磨,使得最终结果达 不到所需的0.500μm;实施例2中,只选择了小尺寸(0.4mm)的zro2球, 在研磨初期时的表现,没有大尺寸(2mm)球表现好,至于后期研磨中d
50
没有达到0.4μm,可能是因为初期的颗粒粒径减小的不够,不能顺利的开 启摩擦粉碎;在实施例3中,大尺寸(2mm)的zro2球混合小尺寸(0.4mm) 的zro2球,由图2(c)可知,研磨初期时β-sic颗粒粒径达到了0.834μm, 初期效果没有实施例1中只选择2mm的zro2球研磨效果好,是因为两球 之间形成的空隙过大,研磨介质与物料的接触面积减小,活化效率越不明 显;实施例4中,先用大尺寸(2mm)的zro2球对β-sic颗粒进行研磨, 使β-sic大颗粒粒径快速减小,再更换小尺寸(0.4mm)的zro2球,使其 对β-sic颗粒继续球磨粉碎至极限粒径。由于减小zro2球的直径,可以增 加磨介与物料颗粒接触面,更有利于提高研磨效率,使得β-sic颗粒更加细 化,表面活性更高。
[0116]
1-2.显微结构分析
[0117]
图3是自蔓延燃烧合成β-sic原粉(d
50
=5.471μm)和实施例4机械激 活后的β-sic粉(d
50
=0.418μm)的sem图,其中图3(a)-(d)为β-sic 原粉的四种主要形貌,图3(a)为多个小颗粒团聚而成的大颗粒,图3(b) 为长条树根状,图3(c)为圆柱状超大硬团聚体,宽约10μm左右,图3 (d)为细丝状态,团聚颗粒粒径大部分为5μm以上,且颗粒形貌复杂, 由于烧结sic陶瓷的驱动力来自于sic粉体的表面能,粉体越细,球形度 越好,粉体颗粒的表面能就越大,烧结活性越高。图3(e)-(h)即为采 用实施例4获得的d
50
=0.418μm的β-sic粉,由图3(e)-(h)可以明显 看出,经研磨活化后,颗粒粒径达到了亚微米级,且颗粒球形度增大,颗 粒呈等轴状不规则多边形,粒径分布均匀,这为无压烧结致密化β-sic陶瓷 打下了良好的基础。
[0118]
2.酸洗纯化前后β-sic粉体的相组成、氧含量及显微组织结构分析
[0119]
2-1.相组成分析
[0120]
图4是β-sic原粉及机械激活以及酸洗纯化后的β-sic粉的xrd图, 由图4可知,β-sic粉为3c-sic,粉体的x射线衍射图在2θ=33.7处显示出 一个附加峰。究其原因是由于粉体中的层错,而不是由于其他多型(α-sic) 的存在。而且从图中可以看到研磨后的β-sic粉的衍射峰强度变低,峰宽变 宽,是因为研磨后的β-sic晶粒变细所导致的,由scherrer公式(1)可知。
[0121][0122]
scherrer公式可求出平均晶粒尺寸d,对于不同晶粒大小的同种物质, 当k、γ、θ不变时,平均晶粒尺寸d与样品衍射峰半高宽度b成反比,即 b越大,d越小,由图4可知,经研
磨后的β-sic衍射峰半高宽度要大于原 始粉,证明了机械激活后的晶粒尺寸要小于初始粉体的晶粒尺寸。
[0123]
根据β-sic的研磨前后的纯度对比来看,初始粉的纯度为90.4%,而研 磨细化后的β-sic粉的纯度降低至78%,这是由于zro2陶瓷的硬度比sic 陶瓷低,研磨过程中zro2杂质的引入,致使原物料纯度降低,但在研磨后 的物相分析中没有发现zro2衍射峰,是因为zro2球没有β-sic颗粒的硬度 高,当机械激活时间较长时,损耗了zro2球,使其表面的zro2研磨进了β-sic 浆料中,再经过研磨,摩擦,剪切等作用,可能造成了β-sic颗粒对zro2颗粒晶体结构的破坏,衍射能力减弱,并且zro2的杂质含量较小,于是造 成衍射峰消失。
[0124]
图5(a)-(c)是自蔓延燃烧合成β-sic原粉、亚微米β-sic粉和酸洗 纯化的β-sic粉的元素面扫,由图5(a)可以看出,自蔓延原粉是有si、c、 o三种元素存在,即含有β-sic和部分被氧化的sio2,图5(b)实施例4 机械激活后的β-sic粉,图中有si、c、zr、o四种元素存在,除了β-sic 和sio2的存在,还发现了zro2,且zr均匀分布在sic粉中,进一步证明 了较长时间的研磨破坏了zro2的晶体结构,图5(c)是实施例4经酸洗纯 化纯度达到98%以上的sic粉,可以看出只有β-sic和sio2,酸洗的效果 非常明显,eds能谱中已经没有zr元素的存在,zro2已经被混酸除去,即 成功得到了亚微米级纯度大于98%的无压烧结β-sic粉体。
[0125]
2-2.氧含量及比表面积分析
[0126]
使用氧含量分析仪和比表面积分析仪测试了自蔓延燃烧合成的β-sic 原粉及研磨酸洗纯化后的β-sic粉体的氧含量和比表面积,原粉的氧含量为 2.0wt%,比表面积为6.34m2/g;由表2可已看出,经过实施例4酸洗纯化 的β-sic微粉的氧含量为0.89wt%,比表面积为18.46m2/g。结果表明,酸 洗除去了机械激活引入的zro2杂质和β-sic表面sio2氧化层,提高了β-sic 粉的烧结活性。
[0127]
3.无压烧结方案效果分析
[0128]
3-1.烧结助剂及工艺对sic陶瓷密度及力学性能的影响分析
[0129]
使用活化与纯化处理后的β-sic微粉作为原料,加入b4c和酚醛树脂 作为烧结助剂,研究了b、c的添加量及烧结温度和保温时间对无压烧结自 蔓延燃烧合成的β-sic的致密化和力学性能的影响。通过实施例1至4对比 分析b和c添加量对自蔓延燃烧合成sic陶瓷密度的影响,结果如表3所 示。
[0130]
(1)c添加量:c添加量在1~5wt%范围内,随着c添加量的增加, sic陶瓷的密度也随之增加,当c添加量达到4wt%时sic密度达到最大值 3.14g/cm3;当c继续增加时,密度反而下降,原因是在烧结sic陶瓷的过 程中,c与sio2结合生成sic和co,从而增加粉体的表面能,降低晶界能, 增加了β-sic粉的烧结活性,且sic在高于1880℃时会发生分解-升华反应,c的存在可以阻碍sic的升华,引入碳是为了与sic的氧化层反应。当碳 添加量高于4wt%时,氧化层不再被消除,并在烧结样品中形成碳夹杂物。
[0131]
sic陶瓷的硬度随c添加量增加为先增加后减小的趋势,在c添加量 为4wt%时sic陶瓷硬度为25.62
±
0.92gpa;在c添加量为5wt%时,其硬 度有下降,这与c添加含量和sic陶瓷密度的趋势相似,这可能是因为在 烧结sic时的c将sic表面的sio2还原之后还有残余c留在sic陶瓷中所 导致的硬度降低。
[0132]
sic陶瓷的断裂韧性随c添加量增加为先增加后减小的趋势,c添加量 为4%时sic陶瓷断裂韧性值达到最大为4.84
±
0.89mpa
·m1/2
,但实际上其 断裂韧性值波动较小,平均
断裂韧性值都在4-5mpa
·m1/2
之间,相比于固相 烧结的α-sic的断裂韧性在3-4.5mpa
·m1/2
来说,其数值要稍大一些,这可 能是因为β-sic的晶粒呈现长柱状结构,相比于α-sic的等轴状晶粒有更好 的韧性,在有裂纹扩展的时候,遇到β-sic的长柱状晶粒会发生裂纹延长、 偏转、桥接等作用,从而提高sic的断裂韧性。
[0133]
sic陶瓷的三点弯曲强度随c含量的增加呈现出先增加后减小的趋势, 当c添加量为4wt%时sic陶瓷的三点弯曲强度达到最大值为401.79
±
8.66 mpa,但随着c的继续增加,其sic的三点弯曲强度下降,这可能是因为c 在sic中的残留富集引起的sic强度的降低。
[0134]
(2)b添加量:b添加量在0.2~1.0wt%的范围内,随着b含量的增加, sic陶瓷的密度也随之增加,当b添加量为0.7wt%时,sic陶瓷的密度达 到最大值3.14g/cm3;继续增加b含量时,sic陶瓷的密度反而下降。b在 烧结sic中起到了降低晶界能的作用,即在本身共价性强以及sic本身难 扩散情况下,少量的b即可改变这一现象,当b含量达到1wt%时,sic陶 瓷的密度反而下降,原因是由于b的过量添加导致sic陶瓷的晶粒过于长 大,从而使得晶粒间结合不紧密,结果使sic陶瓷的密度有所下降。
[0135]
sic陶瓷硬度随b添加量增加呈上升趋势,直至b含量至0.7wt%时sic 陶瓷硬度达到最大值25.62
±
0.92gpa,当继续添加b至1wt%时。其硬度反 而下降,这可能是因为b的过量引入使得sic陶瓷的晶粒发生异常长大引 起晶粒间结合不紧密所导致的,这与b添加量和sic陶瓷密度的趋势大致 相同。
[0136]
sic陶瓷的断裂韧性随b添加量增加呈增加趋势,在0.7wt%时sic陶 瓷的断裂韧性值达到最大,为4.84
±
0.84mpa
·m1/2
,当b继续添加至1wt% 时,sic陶瓷的断裂韧性值反而下降,是因为晶粒异常长大引起的。
[0137]
sic陶瓷的三点弯曲强度随b添加量的增加呈而增加,在b添加量为 0.7wt%时有最大的三点弯曲强度,其数值为401.79
±
8.66mpa,但随着b的 继续增加,其sic的三点弯曲强度下大幅度降低,这可能是因为过量b的 引入导致了sic晶粒的异常长大,使得sic晶粒之间结合不紧密引起sic 三点弯曲强度大幅下降。
[0138]
(3)烧结温度:由表3可以看出,当烧结温度为2000℃时,sic陶瓷 的致密度较低,气孔较多,导致sic陶瓷的硬度偏低;当烧结温度为2100℃ 时,sic陶瓷的硬度提高到25.62
±
0.95gpa;烧结温度继续升高至2130℃ 时,晶粒间结合不够紧密,密度降低,硬度也随之下降为21.43
±
0.7gpa。 在烧结温度为2100℃时,sic陶瓷的硬度随时间变化的趋势与密度、收缩 率、烧失率变化趋势相同。
[0139]
首先因2000℃的密度太低导致其中存在大量,用压痕法测量断裂韧性 是其裂纹不明显,故舍弃2000℃时的断裂韧性值,在烧结温度为2050℃、 2100℃、2130℃呈现出先升高后下降的趋势,其原因也与其中晶粒大小和 其晶间结合是否紧密有关,当2100℃时断裂韧性达到4.84
±
0.89mpa
·m1/2
, 在这里值得注意的是普通α-sic的断裂韧性普遍在3-4mpa
·m1/2
,而因为 β-sic的晶粒形貌为棒状,在有裂纹扩展的时候,遇到sic的长柱状晶粒会 发生裂纹延长、偏转、桥接等作用,从而提高了断裂韧性;
[0140]
(4)烧结时间:由表3可以看出,当保温时间为30min时,陶瓷表面 的晶粒细小,但结合不紧密,导致其硬度仅有21.16
±
0.66gpa;当延长保温 时间至60min时,sic陶瓷晶粒逐渐长大,并结合紧密,孔隙减少,致密 度提高,硬度也随之增加,直至90min时硬度达到最大值,为25.62
±
0.62gpa; 继续延长保温时间至120min时,sic晶粒异常长大,导致晶粒之
间结构疏 松,硬度下降。
[0141]
在保温时间为90min时sic断裂韧性达到最大值4.84
±
0.89mpa
·m1/2
。 这是因为60min时,sic晶粒之间结合不够紧密,且120min时sic晶粒粗 大且晶间结合不紧密导致其断裂韧性低。
[0142]
3-2.烧结助剂及工艺对sic陶瓷显微结构的影响分析
[0143]
(1)图6(a)-(d)不同添加量下陶瓷表面sem分析:
[0144]
如图6(a)所示,当烧结助剂c的添加量为1wt%、b含量为0.2wt% 时时,sic陶瓷组织极为疏松。因为c添加量不足,氧化硅层不能被完全 除掉,氧的存在,使得si和c向颈部的扩散受到阻碍,且c添加量不足, 会导致sic的升华,故sic内部组织疏松。b的少量添加便可以引起sic 陶瓷的致密化,这是因为少量的b固溶进sic晶粒中,降低了sic的晶界 能。
[0145]
如图6(b)所示,当c添加量为3wt%、当b添加为0.5wt%时,sic 陶瓷基本致密,致密度达到97.2%,仅1wt.%c的差距,致密度却相差14%, 这是因为均匀分散在sic的c阻碍了sic的升华,使其稳定下来,其晶粒 间结合紧密,但有部分晶粒异常长大,这可能是因为使用酚醛树脂作为有 机碳源时,碳分布在sic晶粒内部,在晶界处的钉扎作用不强,导致部分 的sic晶粒发生过分长大。
[0146]
如图6(c)所示,当c添加量增加到4wt%、当b添加为1.0wt%时,sic陶瓷密度达到了3.14g/cm3,合适的c含量使sic陶瓷密度提升不大但 晶粒生长更均匀,其过分长大晶粒较少,这也是其致密度达到最高的原因。
[0147]
如图6(d)所示,当c含量增加到5wt%、当b添加为0.7wt%时,sic 表面出现较多的大晶粒,此时sic密度为3.12g/cm3,略有下降,这是因为 c的过剩富集导致了密度下降。此外,当b增加到1wt%碳化硅密度反而有 所下降,部分sic为长径比小的板状晶粒,是因为过量b引起了sic晶粒 的异常长大所导致的。
[0148]
(2)不同添加量下sic陶瓷断口的显微结构分析:
[0149]
如图7(a)-(c)为实施例2至4sic陶瓷断面的显微结构,由图可知 红圈出呈现出河流样花纹,由此可得其断裂方式为穿晶断裂,但在图中也 可以看出较为完整且表面平滑的长柱状或棒状的sic晶粒,由此可得其断 裂方式为沿晶断裂,所以其断裂方式为穿晶断裂和沿晶断裂的混合断裂模 式。由三点弯曲强度数据与断裂面结构作比较可得出,由于c添加量为4wt/% 时,sic陶瓷密度最高,晶粒之间结合较为紧密,故其强度最高。在c添 加量为3wt/%和5wt/%时sic陶瓷密度虽然接近,但其强度相差较远的原因 可能是当c添加量增加到5wt%时,sic陶瓷中富碳量也随之增加,因为c 的密度及强度较sic低,导致sic陶瓷密度及强度下降。
[0150]
此外,b添加量为1wt%时,为穿晶断裂和沿晶断裂的混合断裂模式, 断裂面中由于存在异常长大的晶粒,且形成了长径比小的板状晶粒,所以b 添加量为1wt%时的抗弯强度最低。
[0151]
以上结果表明:如实施例4中,当b(b4c换算)添加量为0.7wt%,c (酚醛树脂换算)添加量为4wt%时,在烧结温度为2100℃,保温时间90min 的条件下,制备的sic陶瓷的致密度和力学性能最佳,其烧失率为7.9%、 收缩率为15.6%、密度为3.14g/m3(即致密度为97.8%),硬度为25.62
±
0.92 gpa,断裂韧性为4.84
±
0.84mpa
·m1/2
,三点抗弯强度为401.74
±
8.66gpa。 过量硼和碳的添加都会引起sic晶粒的异常长大,并导致其密度和力学
性 能下降。
[0152]
应当注意,在此所述的实施例仅为本发明的部分实施例,而非本发明 的全部实现方式,所述实施例只有示例性,其作用只在于提供理解本发明 内容更为直观明了的方式,而不是对本发明所述技术方案的限制。在不脱 离本发明构思的前提下,所有本领域普通技术人员没有做出创造性劳动就 能想到的其它实施方式,及其它对本发明技术方案的简单替换和各种变化, 都属于本发明的保护范围。