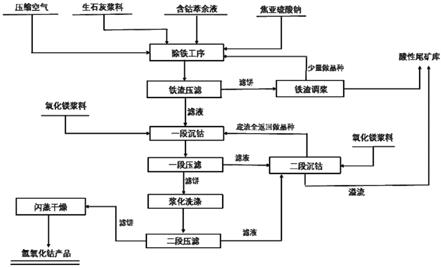
1.本发明属于湿法冶金技术领域,具体涉及一种工业上含钴低铜萃余液生产粗制氢氧化钴的方法。
背景技术:
2.在现有技术中,粗制氢氧化钴制备过程中的除铁、沉钴等工序处理效果仍不是很理想,存在除铁率不高、铁渣沉降慢易跑浑、氧化镁添加易过量、沉钴率不高、辅料单耗高以及产品一次回收率低等一系列相关问题,且制备获得的粗制氢氧化钴产品普遍存在钴含量不高(<33%),fe、mn、mg等杂质含量偏高等问题。
技术实现要素:
3.本发明提供一种工业上含钴低铜萃余液生产粗制氢氧化钴的方法,要解决的技术问题是:解决当前粗制氢氧化钴产品钴含量不高、杂质含量偏高、产品一次回收率低、辅料单耗高等问题。
4.为了解决以上技术问题,本发明提供了一种工业上含钴低铜萃余液生产粗制氢氧化钴的方法,其特征在于,包括以下步骤:
5.s1、除铁:向低铜含钴萃余液中加入一定比例的焦亚硫酸钠浆料与压缩空气,调节反应的氧化还原环境将难水解沉淀的fe
2+
氧化成更易水解沉淀的fe
3+
,同时通入生石灰浆料调节溶液ph;
6.s2、沉钴:加入活性氧化镁浆料,控制反应的ph,使溶液中co离子以co(oh)2沉淀物析出;
7.s3、浆化洗涤:将氢氧化钴滤饼卸入浆化槽进行浆化洗涤,完成后再泵入压滤机进行压滤;
8.s4、闪蒸干燥。
9.有益效果:本发明采用除铁+一段沉钴+二段沉钴+压滤浆化洗涤+闪蒸干燥等相关工艺基本流程,通过优化除铁工艺,采取焦亚硫酸钠溶液作为除铁添加药剂并将部分铁渣返回作为除铁反应晶种,从而大大改善了除铁效果,同时通过工艺改良提升二段沉钴渣品质指标,并将其全部作为一段沉钴反应晶种,有效促进了一段沉钴反应晶核快速形成与长大,改善一段沉钴效率,提高了氧化镁利用效率,且大大提升了氢氧化钴产品总产出量及一次回收率消除了现有技术条件下的除铁效果差、氢氧化钴钴含量不高、产品一次回收率低、辅料单耗高等一系列问题。
附图说明
10.图1本发明工艺流程图。
具体实施方式
11.为使本发明的目的、内容和优点更加清楚,下面对本发明的具体实施方式作进一步详细描述。
12.本发明提出的一种工业上含钴低铜萃余液生产粗制氢氧化钴的方法,含钴低铜萃余液成份:co:2~5g/l,cu:0.2~0.8g/l,fe:1~2g/l,mn:1~1.5g/l,ca:0.3~0.7g/l,h2so4:18~25g/l,包括以下步骤:
13.s1、除铁工序:通过向低铜含钴萃余液中加入一定比例的焦亚硫酸钠浆料与压缩空气,调节反应的氧化还原环境将难水解沉淀的fe
2+
氧化成更易水解沉淀的fe
3+
,同时通入生石灰浆料调节溶液ph实现绝大部分铁离子去除的目的,另外部分cu、mn等杂质离子在除杂过程中也能一并除去。同时通过将少部分外排铁渣重新返回除铁槽作为除铁反应晶种,增大了铁渣晶核粒径,从而改善了铁渣沉降性能,解决了现有技术存在的铁渣沉降易跑浑的难题,从根本上改善了除铁效果。需特别说明的是,上述提到的除铁各项控制工艺参数具体规定为:生石灰浆料浓度为10%~20%;控制调节各槽ph2.5~4.0,终点ph4.0~5.0;焦亚硫酸钠溶液浓度为15%~25%,添加速度为0.5~3m3/h;压缩空气通入量为30~50l/min,除铁氧化还原电位420~580mv;除铁反应时间控制5~8h。
14.s2、沉钴工序:沉钴主要是通过加入活性氧化镁浆料,控制反应的ph,使溶液中co离子以co(oh)2沉淀物析出。为了控制和保证氢氧化钴产品的钴品位,沉钴工序采取了2段沉钴工艺,其工艺控制参数与要求有比较大的区别,其中一段沉钴工艺控制参数为:
①
控制调节各槽ph5.5~7.8,终点ph 7.8~8.2;
②
反应时间控制5~10h;
③
一段沉钴后液含co控制在0.4~0.8g/l;
④
生石灰加料添加速度3~10m3/h。二段沉钴工艺控制要求为:
①
控制调节各槽ph8.5~9.1,终点ph 9.1~9.5;
②
反应时间为3~6h;
③
二段沉钴后液含co控制<0.1g/l;
④
生石灰加料添加速度0.5~5m3/h。另外需特别说明的是,将二段沉钴获得的沉钴渣底流全部泵入一段沉钴槽1号槽,作为一段沉钴反应晶种,更易进行氢氧化钴成核,这样做不但有效使氢氧化钴晶核粒径长得更大便于过滤固液分离,而且能实现一、二段沉钴所有沉淀物均可作为氢氧化钴产品产出,最终使沉钴工序钴损失率控制在2%以内,沉钴工序氢氧化钴产品钴回收率可以达到98%以上。
15.3、压滤浆化洗涤工序:将一段沉钴处理后含氢氧化钴浆料经过压滤机进行压滤实现初步液固分离,滤液打完二段沉钴工序进一步处理,滤饼卸至压滤机正下方的浆化槽加清水进行浆化洗涤除去夹带的mn
2+
、mg
2+
等杂质离子。浆化洗涤洗水量控制10~30m3,浆化时间控制20~50min。
16.4、闪蒸干燥工序:通过在燃烧炉中燃烧柴油加热空气,然后热空气与氢氧化钴湿料在闪蒸主机中进行充分接触热交换,水份被瞬间蒸发,从而达到氢氧化钴湿料被干燥的目的。闪蒸入风控制温度300~400℃,混合温度65~90℃,出风温度55~65℃。
17.实施例1:
18.本实施例采用的含钴低铜萃余液成份为co:3.12g/l,cu:0.315g/l,mn:1.12g/l,fe:1.235g/l,ca:0.6g/l,h2so4:22.1g/l
19.除铁工序:将含钴低铜萃余液以180m3/h的速度通入除铁1号槽中,反应料液利用槽罐高度差依次从一段沉钴1号槽自流至6号槽;分别往除铁1、2、3、4号槽通入质量浓度17.6%的生石灰浆料,控制调节各槽ph2.5~4.5,终点ph5.0;分别往除铁1、2、3号槽通入质
量浓度18%的焦亚硫酸钠溶液;分别往除铁1至6号槽通入压缩空气30l/min,控制各槽氧化还原电位420mv左右;反应时间控制6h;反应温度为常温;将除铁浓密机底流通过压滤机过滤,生成的滤饼进行再浆化外排,同时将少部分铁渣返回除铁槽作为除铁反应晶种。
20.一段沉钴工序:将合格的除铁后液以190m3/h速度通入溶液输送泵泵入一段沉钴1号槽中,反应料液利用槽罐高度差依次从一段沉钴1号槽自流至8号槽;分别往一段沉钴1、2、3、4号槽通入质量浓度10%的氧化镁反应浆料,控制反应终点ph 8.0;反应时间控制8h;反应温度为常温;一段沉钴后液含co控制在0.5g/l。
21.二段沉钴工序:将一段沉钴后液通入二段沉钴1号槽中,反应料液利用槽罐高度差依次从二段沉钴1号槽自流至3号槽;分别往二段沉钴1、2号槽通入质量浓度12%的氧化镁反应浆料,控制终点ph 9.3;反应时间为4h;反应温度为常温;二段沉钴后液含co控制0.05g/l。
22.浆化洗涤工序:浆化槽加入清水25m3,再将氢氧化钴滤饼卸入浆化槽进行浆化洗涤,浆化时间控制30min,完成后再泵入压滤机进行压滤。
23.闪蒸干燥工序:将洗涤好的氢氧化钴湿料通过闪蒸上料皮带进入闪蒸系统进行闪蒸干燥,闪蒸入风控制温度400℃,混合温度80℃,出风温度65℃,最终产出氢氧化钴干料产品。
24.其效果见表2
25.表2实施例1效果一览表
[0026][0027]
实施例2:
[0028]
本实施例采用的含钴低铜萃余液成份为co:2.82g/l,cu:0.217g/l,mn:1.14g/l,fe:1.435g/l,ca:0.5g/l,h2so4:23.5g/l
[0029]
除铁工序:将含钴低铜萃余液以190m3/h的速度通入除铁1号槽中,反应料液利用槽罐高度差依次从一段沉钴1号槽自流至6号槽;分别往除铁1、2、3、4号槽通入质量浓度15%的生石灰浆料,控制调节各槽ph2.5~4.0,终点ph4.5;分别往除铁1、2、3号槽通入质量浓度18%的焦亚硫酸钠溶液;分别往除铁1至6号槽通入压缩空气45l/min,控制各槽氧化还原电位460mv左右;反应时间控制6h;反应温度为常温;将除铁浓密机底流通过压滤机过滤,生成的滤饼进行再浆化外排,同时将少部分铁渣返回除铁槽作为除铁反应晶种。
[0030]
一段沉钴工序:将合格的除铁后液以200m3/h速度通入溶液输送泵泵入一段沉钴1号槽中,反应料液利用槽罐高度差依次从一段沉钴1号槽自流至8号槽;分别往一段沉钴1、2、3、4号槽通入质量浓度15%的氧化镁反应浆料,控制反应终点ph7.8;反应时间控制8h;反应温度为常温;一段沉钴后液含co控制在0.4g/l。
[0031]
二段沉钴工序:将一段沉钴后液通入二段沉钴1号槽中,反应料液利用槽罐高度差依次从二段沉钴1号槽自流至3号槽;分别往二段沉钴1、2号槽通入质量浓度15%的氧化镁反应浆料,控制终点ph 9.1;反应时间为4h;反应温度为常温;二段沉钴后液含co控制0.06g/l。
[0032]
浆化洗涤工序:浆化槽加入清水20m3,再将氢氧化钴滤饼卸入浆化槽进行浆化洗涤,浆化时间控制50min,完成后再泵入压滤机进行压滤。
[0033]
闪蒸干燥工序:将洗涤好的氢氧化钴湿料通过闪蒸上料皮带进入闪蒸系统进行闪蒸干燥,闪蒸入风控制温度350℃,混合温度70℃,出风温度60℃,最终产出氢氧化钴干料产品。
[0034]
其效果见表3
[0035]
表3实施例2效果一览表
[0036][0037]
以上所述仅是本发明的优选实施方式,应当指出,对于本技术领域的普通技术人员来说,在不脱离本发明技术原理的前提下,还可以做出若干改进和变形,这些改进和变形也应视为本发明的保护范围。