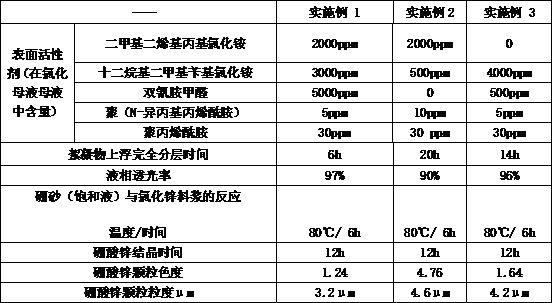
1.本发明涉及阴树脂母液回收处理领域,具体涉及一种利用阴树脂氯化母液中氯化锌制备硼酸锌的方法。
背景技术:
2.随着科学技术日新月异的进步,在各种领域里不断地开发和利用离子交换树脂的功能性,解决并简化了许多化学分离和载体效果的难题,尤其是对阴离子交换树脂功能新的应用和开发,使各类阴离子交换树脂在常规骨架的基础上,进一步针对其应用对象的特性和目标进行特殊性优化和改造,衍生出了各种不同用途的交换、吸附、萃淋、络合、螯合、酯化等特种树脂,也是近几年我国阴离子交换树脂制造总量突跃为全球制造总量的前列,增涨势头不减的一个重要因素。但是因为其产量的增加,尤其是树脂制备氯化反应阶段产生氯化母液量增加,接踵带来了母液后处理的环保难题。
3.阴离子交换树脂的制造中, 由白球在氯化锌的催化作用下与氯甲醚进行 friedel-crafts 反应(氯甲基化)得到氯球,再与相应的胺进行(胺化)反应,转化后制得阴离子交换树脂。用氯甲醚作氯甲基化试剂 , 它既是良好的氯甲基化试剂,又是良好的树脂骨架(高分子共聚体)膨胀试剂,可极其方便地将二乙烯苯-苯乙烯等共聚物(白球)进行氯甲基化反应。阴树脂氯化母液是阴树脂生产中氯甲基化反应过程中产生的。主要是反应成为氯球(固体)移出后去胺化工序,所剩母液(液相)是由氯甲醚、氯化锌组成的。
4.氯化母液中的氯化锌是宝贵的可再生资源,它与其可衍生物在许多工业领域用途广泛,例如;
①
将其再加工成为无水氯化锌做为氯甲基化的催化剂和生产活性碳的活化剂。
②
将其加工成氯化锌,是抗菌化妆品、纺织、橡胶工业、陶瓷、压电材料、涂料工业、玻璃、高效催化剂、吸波材料、电磁学、压敏电阻、医药等多个领域被广泛应用的材料。
③
将其加工成硼酸锌,被广泛应用于各种纤维、树脂、橡胶制品、电 器绝缘材料、电子制品外壳、汽车零件壁材、电线、电 缆、防锈漆等方面的阻燃 、抑烟剂 。
5.因氯化锌在此“白球—氯甲基化反应”中充当催化剂使用,在反应中几乎不消耗,在氯甲醚中的溶解度小,理论上会以沉淀状形态混存于氯化母液中、很容易与氯甲醚分离而被回收。但实际上,在树脂制造的氯化反应中,因氯甲醚既是极强氯甲基化反应试剂,对白球而言又是较好的膨胀剂,它能将白球(高分子聚合物)体内的共聚体、小分子聚合物和聚合反应后残留单体等聚合反应残留物在反应过程中从聚合珠体中不断地抽提出来,游离出至酸液中,这些聚合反应残留物微粒表面因自体被氯甲基化基团化的电性作用,呈溶胶体状微粒,本身的显色致使整个母液体系颜色呈深色。由于胶体微粒间分子的布朗运动和静电的排斥力作用,趋使其中大部分吸附于母液中氯化锌晶体的表面,与氯化锌混溶成为鼻涕状粘稠物状态。回收时要先将母液蒸馏或是离心分离回收大部分氯甲醚。然后对氯化锌(鼻涕状粘稠物)沉淀进行进一步的处理。若将此时的母液直接釆用蒸发、结晶的常规工艺回收其中的氯化锌,会因为聚合反应残留物的存在与氯化锌结焦产生粘釜,氯化锌结晶色泽也会呈柏油色无法直接利用,因此上述直接从母液中分离回收氯化锌的工艺不可行。
通常的做法是;一是不对其进行处理,直接由活性碳生产厂用作生产活性碳时是活化剂,但受生产条件因素的制约,其使用量有限。二是向氯化锌沉淀物(鼻涕状粘稠物)中加碱和水,使氯化锌沉淀转化为氢氧化锌沉淀,再用甲缩醛、丙酮或乙丙醇等溶剂反复洗涤所得的氢氧化锌沉淀,萃取除去其中所含的聚合反应残留物,所获得的氢氧化锌可再进一步加工成各种锌盐或锌材料衍生物。但因为锌离子是两性元素,在酸性液体向碱性转化过程中不仅分离困难,而且流失过多。而且,有机杂质的萃取去除受到溶剂成本与萃取效率的限制而不能取到较好的结果,进一步影响后续产品的质量(色泽深、颗粒不均等)。因需要去除氯化母液中的共聚体、小分子聚合物和聚合反应后残留单体等聚合反应残留物,使对氯化锌的回收工艺繁杂,回收率低、成本高,致生产厂家对其进行回收和使用的积极性不高,所以大部分都当作危废处理了,不仅浪费宝贵的资源,也增加了环保负担,是阴树脂生产过程中很棘手的难题。所以,必须要给阴树脂氯化母液寻找到合适的综合利用出路。
技术实现要素:
6.为了解决上述问题,本发明提供了一种利用阴树脂氯化母液中氯化锌制备硼酸锌的方法。本发明的技术方案如下:一种利用阴树脂氯化母液中氯化锌制备硼酸锌的方法,其特征在于,包括以下步骤:步骤1:将白球、氯甲醚和氯化锌加入反应釜中反应制得氯球;过滤掉反应体系中的氯球,得到的滤液为氯化母液;步骤2:向氯化母液中加入定量的复合阳离子表面活性剂,搅拌一定时间后静置,氯化母液中形成絮凝物并不断上浮,氯化母液的下层形成沉淀物;待氯化母液完全分层后,将其表层的絮凝物去除,然后过滤或离心分离出沉淀物,所得沉淀物即氯化锌料浆。
7.步骤3:将氯化锌料浆称重计量后置于反应釜内,向反应釜中加入适量水,搅拌,升温,然后滴加过饱和硼砂溶液,反应一段时间后降温,静置,生成硼酸锌结晶,对硼酸锌结晶过滤、洗涤、脱水、烘干处理后得到硼酸锌粉体。
8.优选的,步骤1中将白球与氯甲醚按照体积比1:3-5投入反应釜中,并加入占白球重量5%-10%的无水氯化锌,在搅拌状态下,缓慢升温至43
±
1℃,反应15小时,取样测球体氯含量,球体氯含量》14%时釜温降至35℃以下,自滤母液1小时,真空抽滤0.5小时得到氯化母液。
9.优选的,步骤2中所述复合阳离子表面活性剂包含二甲基二烯基丙基氯化铵、十二烷基二甲基苄基氯化铵、双氰胺甲醛中的至少一种,以及聚(n-异丙基丙烯酰胺)和聚丙烯酰胺。
10.优选的,聚(n-异丙基丙烯酰胺)在氯化母液中的添加量为3-20ppm,聚丙烯酰胺在氯化母液中的添加量为5-30ppm。
11.优选的,所述复合阳离子表面活性剂包含二甲基二烯基丙基氯化铵时,二甲基二烯基丙基氯化铵在氯化母液中的添加量为5-3000ppm;所述复合阳离子表面活性剂包含十二烷基二甲基苄基氯化铵时,十二烷基二甲基苄基氯化铵在氯化母液中的添加量为4-3000ppm;所述复合阳离子表面活性剂包含双氰胺甲醛时,双氰胺甲醛在氯化母液中的添加量为5-5000ppm。
12.优选的,步骤2中向氯化母液向中加入定量的复合阳离子表面活性剂后搅拌1.5~2个小时,然后静置4~20个小时。
13.优选的,步骤3中水的加入量为氯化锌料浆重量的三分之一。
14.优选的,步骤3中升温至40℃~80℃后滴加过饱和硼砂溶液。
15.优选的,步骤3中滴加饱和硼砂溶液后反应1~8 小时再将反应釜的温度降至室温,然后静置6~12小时。
16.优选的,步骤3中所述烘干采用的工艺条件为:50~ 90℃温度下烘干4~10h。
17.该方法直接以氯化母液为原料,不改变母液的ph值,通过加入表面活性剂直接回收母液内氯化锌,复合阳离子表面活性剂对有机杂质起到絮凝的作用,而在强酸环境中表面活性剂一般是不会有絮凝效果的,是因为聚合反应残留物微粒表面因自体被氯甲基化基团的电性作用,在母液中呈胶体微粒状态(真溶液状态),很难凝聚分离。而本发明主要是恰好利用母液中存在其锌离子的
‘
两性’特性,能与所选择的阳离子表面活性剂,原位复合成“带正电的锌基无机-有机杂化絮凝剂”,其电荷密度大,所以,即使在强酸性母液中,也能聚集在这些胶体微粒的表面。因聚合反应残留物也就是胶体微粒被氯甲基化后所带的氯甲基基团电性作用,当复合阳离子表面活性剂加入后,其因内含“表面活性成分”的作用增加母液中胶体微粒的反离子数量,根据所形成新增的胶体微粒反离子与使母液中的低聚物等胶体微粒扩散层内原有反离子之间的静电斥力,使其胶体微粒表面的双电层被压缩,以中和电性,降低微粒的电动电位ζ,从而影响溶胶颗粒间的排斥位能,使胶团扩散层厚度压缩,破坏溶胶体系的稳定性,原体系胶核微粒失去稳定性,胶粒之间的排斥作用减弱、吸引力增加,从而聚集沉降。这些细小的胶体微粒互相团簇聚结。带正电的锌基无机-有机杂化表面活性剂中的高分子物质对胶体粒子还有强烈的吸附作用,其高分子长链的一端可吸附在一个胶体粒子表面上,而另一端又被其它胶粒吸附,形成一个高分子链状物,同时吸附在两个以上的胶粒表面上,在各胶粒之间起到架桥作用,像各胶粒间的桥梁,将胶粒联结在一起,胶体微粒与其形成的絮状体,在自身沉降过程中,能集卷、网捕母液中的其他微粒,粘结成较大颗粒,通过这种架桥卷扫作用使胶体细小的微粒再絮凝成较大的颗粒形成絮凝体,通过以上所述综合作用,最终使母液中的胶体微粒即聚合反应残留物絮凝团聚,形成团聚絮凝物,通过静止使之上浮完全与母液分层,就可方便地将其从液体母液表层分离去除,不仅脱除了母液的颜色,而且下层就可得到较为纯净的氯化锌沉淀,经过滤或离心母液回收大部分氯甲醚后可获得去除了聚合反应残留物且分散性较好的氯化锌沉淀。
18.可见,本发明能在强酸性氯化母液中直加入复合的阳离子表面活性剂,与其中氯化锌原位聚合无机-有机杂化表面活性剂,促使氯化母液中所含聚合反应残留物链团簇的形成絮凝分层除去。再通过蒸馏甚或过滤简单工艺回收氯甲其甲醚和较纯的分散性好的氯化锌沉淀。大大的简化了对氯化母液中锌的回收工艺条件。
19.利用硼砂与氯化锌能在酸性条件下反应生成硼酸锌的特性,取上项所得氯化锌沉淀,向其中加入定量的水并搅拌,不用调节体系的ph值,在溶液呈酸性条件下,直接滴加过饱和硼砂溶液,搅拌状态下使硼砂与氯化锌反应完全,然后静止生成硼酸锌结晶。在整个过程中随氯化锌沉淀带来残留于其中的未反应无机-有机杂化表面活性剂(主要成份是复合表面活性剂),对母液又能起到微乳化作用,表面活性剂官能团取代硼酸锌粒子表面部分非架桥羟基,并起到一定的空间位阻作用,能消除结晶的硬团聚,有助于制备得细颗粒硼酸
锌,克服因硼酸锌结晶颗粒偏大,使用时存在分散性不好,添加量大等缺点,所得反应产物、水洗、干燥得到具有阻燃、抑烟性能的硼酸锌成品,并适合在阴树脂生产线上增加少量必要设备就可方便地实现工业化生产。
20.生产时可直接将硼砂配成过饱和溶液,加入所得氯化锌沉淀液中,加热反应成硼酸锌,并在其中还利用了残留在沉淀中因过量未反应的杂化表面活性剂,起到对溶液体系微乳化作用,制备得细颗粒硼酸锌。硼酸晶体过滤、洗涤液体均做为加入和配制硼砂溶液工艺水循环使用。
21.综上所述,本发明的有益效果是:本发明创造性的将复合阳离子表面活性剂作为絮凝剂加入到酸性体系中,使呈胶体状态的难以分离的聚合反应残留物和氯化锌分别转变成漂浮的絮凝物和沉淀物得以分离出来,分离出的氯化锌可直接用作合成反应的原料,得到的清液(氯甲醚)也可以方便的通过蒸馏回收,大大的简化了阴树脂氯化母液的处理工艺,对阴树脂氯化母液的有效成分(氯甲醚、氯化锌)能实现充分地回收利用,取得了意想不到的效果;进一步的,本发明用氯化锌料浆直接生产硼酸锌,巧妙的利用了氯化锌料浆中携带的复合阳离子表面活性剂,改善了硼酸锌产品的晶型。复合阳离子表面活性剂在硼酸锌的结晶过程,与前述工序中所起的絮凝作用相反的、起到分散的作用,明显改善了硼酸锌的颗粒度,制得的硼酸锌分散性更好、具有优良的理化性质。
22.本发明的工艺可操作性强、系统设备简单,克服氯化母液处理困难的难题,能方便的与阴树脂生产工艺及生产设备相融合,有效的实现生产设备、资源的循环利用,从而降低阴离子交换树脂生产与环保成本,提高了经济效益。
具体实施方式
23.下面对本发明进行详细说明,所举实施例只用于解释本发明,并非用于限定本发明的范围。
24.正如本技术背景技术所分析的,现有技术从阴树脂氯化母液中回收氯化锌的工艺复杂,回收率低、成本高,致使生产厂家对其回收和使用的的积极性不高,大部分氯化母液都被当作危废处理,不仅浪费宝贵的资源,而且增加了环保负担。为了解决该问题,本发明提供了一种利用阴树脂氯化母液中氯化锌制备硼酸锌的方法,该方法包括以下步骤:步骤1:将白球、氯甲醚和氯化锌加入反应釜中反应制得氯球;过滤掉反应体系中的氯球,得到的滤液为氯化母液;作为一种优选的实施方式,步骤1中将白球与氯甲醚按照体积比1:3-5投入反应釜中,并加入占白球重量5%-10%的无水氯化锌,在搅拌状态下,缓慢升温至43
±
1℃,反应15小时,取样测球体氯含量,球体氯含量》14%时釜温降至35℃以下,自滤母液1小时,真空抽滤0.5小时得到氯化母液。
25.步骤2:向氯化母液中加入定量的复合阳离子表面活性剂,搅拌一定时间后静置,氯化母液中形成絮凝物并不断上浮,氯化母液的下层形成沉淀物;待氯化母液完全分层后,将其表层的絮凝物去除,然后过滤或离心分离出沉淀物,所得沉淀物即氯化锌料浆。具体的,步骤2中所述复合阳离子表面活性剂包含二甲基二烯基丙基氯化铵、十二烷基二甲基苄基氯化铵、双氰胺甲醛中的至少一种,以及聚(n-异丙基丙烯酰胺)和聚丙烯酰胺。优选的,聚(n-异丙基丙烯酰胺)在氯化母液中的添加量为3-20ppm,聚丙烯酰胺在氯化母液中的添
加量为5-30ppm。所述复合阳离子表面活性剂包含二甲基二烯基丙基氯化铵时,二甲基二烯基丙基氯化铵在氯化母液中的添加量为5-3000ppm;所述复合阳离子表面活性剂包含十二烷基二甲基苄基氯化铵时,十二烷基二甲基苄基氯化铵在氯化母液中的添加量为4-3000ppm;所述复合阳离子表面活性剂包含双氰胺甲醛时,双氰胺甲醛在氯化母液中的添加量为5-5000ppm。
26.优选的,步骤2中向氯化母液向中加入定量的复合阳离子表面活性剂后搅拌1.5~2个小时,然后静置4~20个小时。优选的,步骤2中利用真空抽吸管将氯化母液表层的絮凝物去除。
27.步骤3:将氯化锌料浆称重计量后置于反应釜内,向反应釜中加入适量水,搅拌,升温,然后滴加过饱和硼砂溶液,反应一段时间后降温,静置,生成硼酸锌结晶,对硼酸锌结晶过滤、洗涤、脱水、烘干处理后得到硼酸锌粉体。优选的,步骤3中水的加入量为氯化锌料浆重量的三分之一。优选的,步骤3中升温至40℃~80℃后滴加过饱和硼砂溶液。优选的,步骤3中滴加饱和硼砂溶液后反应1~8 小时再将反应釜的温度降至室温,然后静置6~12小时。优选的,步骤3中所述烘干采用的工艺条件为:50~ 90℃温度下烘干4~10h。
28.本发明中过饱和硼砂溶液的制备方法是:在一定量热水中(》70℃)搅拌釜中,将硼砂(na2b4o5(oh)4
·
8h2o无色透明的晶体)不断地加入,搅拌直到不再溶解为止,然后再将溶液冷却到室温过滤析出的晶体,得到饱和溶液。
29.下面将结合实施例,进一步地说明本技术的有益效果。
30.以下实施例均采用依照步骤1的优选实施方式操作获得的氯化母液进行操作。
31.实施例1a. 配制复合阳离子表面活性剂,然后加入到氯化母液中。本实施例的复合阳离子表面活性剂由二甲基二烯基丙基氯化铵、十二烷基二甲基苄基氯化铵、双氰胺甲醛、聚(n-异丙基丙烯酰胺)和聚丙烯酰胺组成,各组分在氯化母液中的浓度为:二甲基二烯基丙基氯化铵 2000ppm、十二烷基二甲基苄基氯化铵 3000ppm、双氰胺甲醛 5000ppm、聚(n-异丙基丙烯酰胺) 5ppm、聚丙烯酰胺 30ppm。
32.氯化母液中加入复合阳离子表面活性剂后搅拌1.5小时,然后静置。氯化母液中的聚合反应残留物逐渐絮凝、团聚并上浮。静置6小时后用分光光度计测定母液透光率(此时母液透光率》95%),用真空管抽吸去上层的除絮凝物。再从釜底分离下层氯化锌沉淀至另一反应釜内。留在釜内的清液(氯甲醚)进入液相回收系统,回收釜升温70℃蒸馏,使挥发的氯甲醚经冷凝器冷凝回收回用。
33.b.将分离出的下层氯化锌沉淀料浆称重计量,然后置于反应釜内,料浆在反应釜内填充度至不超过50%,向釜中加入料浆重量三分之一的水并搅拌,此时溶液呈酸性,不调ph值,升温至70℃并滴加过饱和硼砂溶液,然后反应8小时后釜温降至室温静止12小时生成硼酸锌结晶(白色沉淀物),取上层液体样测定溶液中锌含量低于0.5%,即可将所述沉淀物依次过滤、洗涤,然后在 80℃温度下烘干6h,即得硼酸锌粉体。收集过滤、洗涤液体可做为向氯化锌沉淀加入水和配制硼砂溶液水循环使用。
34.实施例2a.配制复合阳离子表面活性剂,然后加入到氯化母液中。本实施例的复合阳离子表面活性剂由二甲基二烯基丙基氯化铵、十二烷基二甲基苄基氯化铵、聚(n-异丙基丙烯酰
胺)和聚丙烯酰胺组成,各组分在氯化母液中的浓度为:二甲基二烯基丙基氯化铵 2000ppm、十二烷基二甲基苄基氯化铵 500ppm、聚(n-异丙基丙烯酰胺) 10ppm、聚丙烯酰胺 30ppm。
35.氯化母液中加入复合阳离子表面活性剂后搅拌1.5小时,然后静置。氯化母液中的聚合反应残留物逐渐絮凝、团聚并上浮。静置20小时后用分光光度计测定母液透光率(此时母液透光率》90%),用真空管抽吸去上层的除絮凝物。再从釜底分离下层氯化锌沉淀至另一反应釜内。留在釜内的清液(氯甲醚)进入液相回收系统,回收釜升温70℃蒸馏,使挥发的氯甲醚经冷凝器冷凝回收回用。
36.b.与实例1中的b项相同方法实施。
37.实施例3a. 配制复合阳离子表面活性剂,然后加入到氯化母液中。本实施例的复合阳离子表面活性剂由十二烷基二甲基苄基氯化铵、双氰胺甲醛、聚(n-异丙基丙烯酰胺)和聚丙烯酰胺组成,各组分在氯化母液中的浓度为:十二烷基二甲基苄基氯化铵 4000ppm、双氰胺甲醛 500ppm、聚(n-异丙基丙烯酰胺) 5ppm、聚丙烯酰胺 30ppm。
38.氯化母液中加入复合阳离子表面活性剂后搅拌1.5小时,然后静置。氯化母液中的聚合反应残留物逐渐絮凝、团聚并上浮。静置14小时后用分光光度计测定母液透光率(此时母液透光率》95%),用真空管抽吸去除上浮低聚物。再从釜底分离出的下层氯化锌沉淀到另一反应釜内。留在釜内的清液(氯甲醚)进入液相回收系统,回收釜升温70℃蒸馏,使挥发的氯甲醚经冷凝器冷凝回收回用。
39.b.与实例1中的b项相同方法实施。
40.各实施例的工艺参数和制得的硼酸锌的质量对比见表1。
41.表1由表1可以看出,本发明各实施例制得的硼酸锌均具有优良的理化性质,硼酸锌颗粒细小均匀,颗粒大小在3-5μm之间;硼酸锌颗粒色度也非常浅,证明本发明的有效的去除了氯化锌沉淀中的聚合反应残留物等影响产品色度的杂质。
42.本发明创造性的将复合阳离子表面活性剂作为絮凝剂加入到酸性体系中,使呈胶
体状态的难以分离的聚合反应残留物和氯化锌分别转变成漂浮的絮凝物和沉淀物得以分离出来,分离出的氯化锌可直接用作合成反应的原料,得到的清液(氯甲醚)也可以方便的通过蒸馏回收,取得了意想不到的效果;进一步的,本发明用氯化锌料浆直接生产硼酸锌,巧妙的利用了氯化锌料浆中携带的复合阳离子表面活性剂,改善了硼酸锌产品的晶型。复合阳离子表面活性剂在硼酸锌的结晶过程,与前述工序中所起的絮凝作用相反的、起到分散的作用,明显改善了硼酸锌的颗粒度,制得的硼酸锌分散性更好、具有优良的理化性质。
43.本发明大大的简化了阴树脂氯化母液的处理工艺,对阴树脂氯化母液的有效成分(氯甲醚、氯化锌)能实现充分地回收利用。本发明的工艺可操作性强、系统设备简单,克服氯化母液处理困难的难题,能方便的与阴树脂生产工艺及生产设备相融合,有效的实现生产设备、资源的循环利用,从而降低阴离子交换树脂生产与环保成本,提高了经济效益。
44.以上所述仅为本发明的优选实施例而已,并不用于限制本发明,对于本领域的技术人员来说,本发明可以有各种更改和变化。凡在本发明的精神和原则之内,所作的任何修改、等同替换、改进等,均应包含在本发明的保护范围之内。