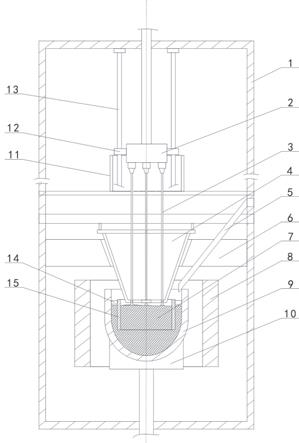
1.本实用新型涉及人工晶体制备领域,尤其涉及一种同时拉制多根硅芯的装置,具体涉及一种使用碎硅料同时拉制多根硅芯的装置。
背景技术:
2.已知的,随着信息技术和光伏产业的飞速发展及相关政策的利好,全球对多/单晶硅的需求增长迅猛,市场供不应求。受此影响,作为太阳能电池主要原料的多/单晶硅价格快速上涨,国内很多企业均在扩产。
3.多/单晶硅在整个生产过程中,硅芯的使用量非常大,现有的硅芯大多是通过区熔的方式制备获得的(主要通过高频线圈、籽晶夹头来完成拉制过程),其工作原理如下:工作时通过给高频线圈通入高频电流,高频感应加热,使高频线圈产生电流对原料棒产生磁力线,加热后的原料棒上端头形成融化区,然后将籽晶插入融化区,当籽晶的端头与原料棒的融区融为一体后,慢慢提升籽晶,融化后的原料融液就会跟随籽晶上升,形成一个新的柱形晶体,这个新的柱形晶体便是硅芯的制成品。
4.在实际生产过程中,发现硅芯制备过程中出现的余料,不小心折断的硅芯,多/单晶硅生产企业在还原、切割、磨抛等工艺阶段产生的碎料等处理非常繁琐,很多企业为了图省事,直接将上述碎料丢弃或者长期堆放在仓库中,还有一些企业将上述碎料进行回收,通过直拉炉拉制成硅棒,然后使用硅棒再拉制成硅芯,这样不仅增加了硅芯拉制的成本,还造成了较大的资源浪费等,那么如何将碎硅料进行再利用就成了本领域技术人员的长期技术诉求。
5.发明人通过检索发现,中国发明专利,专利号为200910064106.7,申请日为2009年1月20日,专利名称为一种晶体碎料拉制硅芯及实施该方法的一种装置,该专利中给出了一种使用晶体碎料拉制硅芯的装置及方法,该专利虽说可以利用碎硅料拉制硅芯,但拉制出硅芯的椭圆度稍大,即良率稍低等。
技术实现要素:
6.为了克服背景技术中的不足,本实用新型提供了一种使用碎硅料同时拉制多根硅芯的装置,本实用新型通过在坩埚的上方设置硅芯成型机构,在硅芯成型机构的上方设置籽晶夹头,硅芯成型机构使温度形成下高上低的温度梯度,降低硅芯成型机构底面硅料融液的温度,增加硅料融液的粘稠度,利于硅料融液跟随籽晶结晶等,进而实现多根硅芯的同时拉制。
7.为实现上述发明目的,本实用新型采用如下技术方案:
8.一种使用碎硅料同时拉制多根硅芯的装置,包括炉室、籽晶夹头、硅芯成型机构、加热器和坩埚,在所述炉室的下部设有坩埚,在所述坩埚的外围设置加热器,或在坩埚的底部设置板状加热器,或在坩埚的外围及底部分别设置加热器和板状加热器,在坩埚开口端的上方设有硅芯成型机构,所述硅芯成型机构的下端面处于坩埚开口端的上部且靠近坩埚
内的硅料融液,在所述硅芯成型机构的上方设有籽晶夹头,所述籽晶夹头中的夹持件上夹持有籽晶形成所述的使用碎硅料同时拉制多根硅芯的装置。
9.所述的使用碎硅料同时拉制多根硅芯的装置,所述硅芯成型机构的下端面距离硅料融液液面的距离为1~50mm。
10.所述的使用碎硅料同时拉制多根硅芯的装置,所述硅芯成型机构的第一结构为硅芯成型机构包括冷却介质出管a、冷却介质入管a和冷却块,所述冷却介质出管a和冷却介质入管a至少设置一组,在每组冷却介质出管a与冷却介质入管a的下端头分别连接冷却块,所述冷却块的上面设有贯通至冷却块下面的拉制孔,在拉制孔外围的冷却块上设有密闭的介质通道,所述介质通道的进口和出口分别连接冷却介质入管a和冷却介质出管a。
11.所述的使用碎硅料同时拉制多根硅芯的装置,所述硅芯成型机构的第二结构为硅芯成型机构包括冷却屏主体、冷却介质出管b、空腔盘和冷却介质入管b,在所述冷却屏主体的下端设有空腔盘,所述冷却屏主体上的腔体与空腔盘上的冷却介质通道连通形成冷却介质通路,所述冷却介质通路分别连接冷却介质出管b和冷却介质入管b,在空腔盘的中部设有观察孔或拉制孔,在观察孔或拉制孔的外围设置至少一个拉制孔,所述拉制孔设置为多个时,多个拉制孔环绕观察孔设置,或多个拉制孔为中间设置一个,另外几个环绕设置。
12.所述的使用碎硅料同时拉制多根硅芯的装置,所述硅芯成型机构的第三结构为硅芯成型机构包括冷却介质出管a、冷却介质入管a和空腔盘,所述冷却介质出管a与冷却介质入管a的下端头连接空腔盘,所述空腔盘上的冷却介质通道与冷却介质出管a和冷却介质入管a连通组成冷却介质通路,在空腔盘的中部设有观察孔或拉制孔,在观察孔或拉制孔的外围设置至少一个拉制孔,所述拉制孔设置为多个时,多个拉制孔环绕观察孔设置,或多个拉制孔为中间设置一个,另外几个环绕设置。
13.所述的使用碎硅料同时拉制多根硅芯的装置,所述空腔盘包括上板、连接柱和下板,在所述下板的上方设有上板,在上板上面的中部设有贯通至下板下面的观察孔,由下板、上板和观察孔形成的空腔为冷却介质通道,在冷却介质通道内设有复数个连接柱,每个连接柱的上端和下端分别连接上板和下板,在每个连接柱的中部分别设有拉制孔,在上板上分别设有至少一组贯通至冷却介质通道的冷却介质下入口和冷却介质下出口。
14.所述的使用碎硅料同时拉制多根硅芯的装置,所述硅芯成型机构的第四结构为硅芯成型机构包括进气管、吹气环主体、连接管、下吹气环和吹气孔,所述吹气环主体为中空结构,吹气环主体的外缘面上分别设有至少两个进气管,在吹气环主体的下面间隔设有复数个连接管,在每个连接管的下端头分别设有下吹气环,在每个下吹气环的内缘面上分别设有复数个吹气孔。
15.所述的使用碎硅料同时拉制多根硅芯的装置,所述籽晶夹头为旋转式籽晶夹头或固定式籽晶夹头。
16.所述的使用碎硅料同时拉制多根硅芯的装置,所述旋转式籽晶夹头包括电机、连接盘、夹持件和旋转机构,在连接盘上设有旋转机构,所述旋转机构的输入端连接电机或旋转机构的输入端连接硬轴,硬轴的另一端延伸至炉室外后连接电机,在连接盘的下部设有至少两个夹持件,所述每个夹持件连接旋转机构使夹持件旋转,所述连接盘的上部连接上提拉机构中的软轴。
17.所述的使用碎硅料同时拉制多根硅芯的装置,所述旋转式籽晶夹头的外部设有上
冷却屏。
18.所述的使用碎硅料同时拉制多根硅芯的装置,所述坩埚内设有隔离环。
19.所述的使用碎硅料同时拉制多根硅芯的装置,所述坩埚的上方设有自动加料管,所述自动加料管的下端头对应坩埚的开口端,自动加料管的上端头外接自动上料机构。
20.所述的使用碎硅料同时拉制多根硅芯的装置,所述坩埚的上方设有液面红外测距仪。
21.由于采用如上所述的技术方案,本实用新型具有如下有益效果:
22.本实用新型通过在坩埚的上方设置硅芯成型机构,在硅芯成型机构的上方设置籽晶夹头,通过在硅芯成型机构上设置多个拉制孔,并通过冷却介质对硅芯成型机构底面以上的空间冷却形成低温区,即形成下高上低的温度梯度,同时还可以实现降低硅芯成型机构底面硅料融液的温度,增加硅料融液的粘稠度,利于硅料融液跟随籽晶结晶,最主要的是还可以对硅芯进行冷却,进而提高硅芯的拉制速度及降低拉制硅芯的椭圆度,本实用新型在实现多根硅芯同时拉制的同时还可以提高硅芯的拉制速度,有效的避免了碎硅料的资源浪费等,适合大范围的推广和应用。
附图说明
23.图1是本实用新型的结构示意图;
24.图2是本实用新型的另一结构示意图;
25.图3是本实用新型中籽晶旋转机构的立体爆炸结构示意图;
26.图4是本实用新型中硅芯成型机构的第一实施例立体结构示意图;
27.图5是本实用新型中硅芯成型机构的第二实施例立体结构示意图;
28.图6是本实用新型中硅芯成型机构的第三实施例立体结构示意图;
29.图7是图6的主视局部剖视结构示意图;
30.图8是本实用新型中硅芯成型机构的第四实施例立体结构示意图;
31.在图中:1、炉室;2、籽晶夹头;201、电机;202、旋拧孔;203、联轴器;204、连接架固定孔;205、连接盘盖体;206、主动力轴;207、从动轴;208、从动齿轮;209、主动齿轮;210、连接盘;211、夹持件;3、硅芯;4、硅芯成型机构;401、冷却介质出管a;402、冷却介质入管a;403、固定环;404、定位环;405、导向孔;406、拉制孔;407、冷却块;408、冷却介质出口;409、冷却介质入口;410、上气管;411、上法兰;412、冷却屏主体;413、冷却介质出管b;414、下气管;415、进气口;416、空腔盘;417、观察孔;418、冷却介质入管b;419、冷却介质通道;420、下板;421、连接柱;422、上板;423、进气管;424、吹气环主体;425、连接管;426、下吹气环;427、吹气孔;5、自动加料管;6、保温层;7、硅料融液;8、加热器;9、坩埚;10、坩埚支座;11、上冷却屏;12、导向块;13、导向钢丝;14、固定块;15、隔离环;16、板状加热器。
具体实施方式
32.通过下面的实施例可以更详细的解释本实用新型,公开本实用新型的发明目的旨在保护本实用新型范围内的一切变化和改进,本实用新型并不局限于下面的实施例;
33.在本实用新型的描述中,需要理解的是,术语“中心”、“侧向”、“长度”、“宽度”、“高度”、“上”、“下”、“前”、“后”、“左”、“右”、“竖直”、“水平”、“顶”、“底”、“内”、“外”、“侧”等指
示的方位或位置关系为基于附图1所示的方位或位置关系,仅是为了便于描述本实用新型和简化描述,而不是指示或暗示所指的设备或元件必须具有特定的方位、以特定的方位构造和操作,因此不能理解为对本实用新型的限制。
34.在本实用新型的描述中,还需要说明的是,除非另有明确的规定和限定,术语“设置”、“安装”、“相连”、“连接”应做广义理解,例如,可以是固定连接,也可以是可拆卸连接,或一体地连接;可以是机械连接,也可以是电连接;可以是直接相连,也可以通过中间媒介间接相连,可以是两个元件内部的连通。对于本领域的普通技术人员而言,可以具体情况理解上述术语在本实用新型中的具体含义。
35.结合附图1~8所述的一种使用碎硅料同时拉制多根硅芯的装置,包括炉室1、籽晶夹头2、硅芯成型机构4、加热器8和坩埚9,如图1、2所示,在所述炉室1的下部设有坩埚9,如图1、2所示,所述坩埚9的底部形状为弧形或平底型,坩埚9设置在坩埚支座10上,在坩埚9的上方或外围设置用于保温的保温层6,在所述坩埚9的外围设置加热器8,或在坩埚9的底部设置板状加热器16,或在坩埚9的外围及底部分别设置加热器8和板状加热器16,在坩埚9开口端的上方设有硅芯成型机构4,所述硅芯成型机构4的下端面处于坩埚9开口端的上部且靠近坩埚9内的硅料融液7,实施时,所述硅芯成型机构4的下端面距离硅料融液7液面的距离为1~50mm,在所述硅芯成型机构4的上方设有籽晶夹头2,所述籽晶夹头2的外缘面上设有两个导向块12,两导向块12上的导向孔围绕导向钢丝13做上下移动,所述籽晶夹头2中的夹持件211上夹持有籽晶,具体实施时,为了实现连续加料功能,保证在硅芯拉制的同时不间断的向坩埚9内加入硅料,确保加料时硅料融液7的液面不发生波动影响硅芯的拉制,在坩埚9内通过固定块14设置用于隔离拉制区的隔离环15,即隔离环15的作用就是使坩埚9内形成两个区域,一个是由隔离环15内部形成的硅芯拉制区,另一个是由隔离环15外壁与坩埚9内壁形成的添加硅料的加料区,形成两个区域的目的就是为了确保在加料时避免拉制区内的硅料融液7液面发生波动,然后在坩埚9的上方设置自动加料管5,所述自动加料管5的下端头对应坩埚9的加料区,自动加料管5的上端头外接自动上料机构,由于自动上料机构不是本实用新型保护的重点,因此再此不对其具体结构做累述,进一步,为了时刻掌握坩埚9内硅料融液7液面的高度,在坩埚9的上方设有液面红外测距仪形成所述的使用碎硅料同时拉制多根硅芯的装置。
36.进一步,在具体实施时,如图2所示,所述硅芯成型机构4的第一结构为硅芯成型机构4包括冷却介质出管a401、冷却介质入管a402和冷却块407,所述冷却介质出管a401和冷却介质入管a402至少设置一组,在每组冷却介质出管a401与冷却介质入管a402的下端头分别连接冷却块407,所述冷却块407的上面设有贯通至冷却块407下面的拉制孔406,在拉制孔406外围的冷却块407上设有密闭的介质通道,所述介质通道的进口和出口分别连接冷却介质入管a402和冷却介质出管a401,当冷却块407设置为多个时,多个冷却块407呈圆形设置。
37.进一步,所述冷却块407的上方设有定位环404,所述定位环404上设有复数组管道穿孔和复数个导向孔405,每组管道穿孔分别套接在对应的冷却介质出管a401和冷却介质入管a402的外缘面上,每个导向孔405分别对应冷却块407上的拉制孔406,所述导向孔405与拉制孔406同心设置。
38.进一步,所述每个拉制孔406下部的内缘面上设有至少一个吹气口,所述吹气口外
接气源。所述吹气口设置为一个时,吹气口连接设置在冷却块407下部的气体通道,气体通道通过设置在冷却块407外侧壁上的吹气管连通气源。
39.所述吹气口设置为多个时,在冷却块407下部拉制孔406的外围设置气道,所述气道的内缘面设有复数个贯通至拉制孔406的吹气口,气道的外缘面连通设置在冷却块407下部的气体通道,气体通道通过设置在冷却块407外侧壁上的吹气管连通气源。所述吹气管设置在冷却介质出管a401或冷却介质入管a402的内缘面,吹气管的外端头连通气源,吹气管的下端头依次穿过冷却块407上吹气管穿孔及介质通道后连通气道,所述气道的内缘面上设有至少一个贯通至拉制孔406的吹气口。所述吹气管的外端头连接调压阀,所述调压阀通过管道连接气源。所述吹气管的外端头分别连接固定环403上的进气口,所述进气口连接调压阀,所述调压阀通过管道连接气源。
40.进一步,所述冷却介质出管a401和冷却介质入管a402的外端头分别固连在固定环403上的冷却介质出口408与冷却介质入口409,所述冷却介质出口408与冷却介质入口409外接气源。
41.关于硅芯成型机构4的第一结构申请人已另行申报专利,在此不对其具体结构做累述。
42.在具体实施时,如图3所示,所述硅芯成型机构4的第二结构为硅芯成型机构4包括冷却屏主体412、冷却介质出管b413、空腔盘416和冷却介质入管b418,在所述冷却屏主体412的下端设有空腔盘416,所述冷却屏主体412上的腔体与空腔盘416上的冷却介质通道419连通形成冷却介质通路,所述冷却介质通路分别连接冷却介质出管b413和冷却介质入管b418,在空腔盘416的中部设有观察孔417或拉制孔406,在观察孔417或拉制孔406的外围设置至少一个拉制孔406,所述拉制孔406设置为多个时,多个拉制孔406环绕观察孔417设置,或多个拉制孔406为中间设置一个,另外几个环绕设置。
43.进一步,所述冷却屏主体412包括上法兰411、冷却屏外层板和冷却屏内层板,所述冷却屏外层板与冷却屏内层板间隔设置,在冷却屏外层板与冷却屏内层板的上端设有上法兰411,冷却屏外层板与冷却屏内层板之间的空隙形成冷却介质通路。
44.进一步,为了提高硅芯拉制时的拉制速度,降低硅芯的椭圆度,保证同时拉制的每根硅芯3等径,每个拉制孔406下部的内缘面上设有至少一个吹气口,所述吹气口外接气源。
45.进一步,所述吹气口设置为一个时,吹气口连接设置在下板420上的气体通道,气体通道通过设置在下板420上的进气孔b连接下气管414,所述下气管414设置在冷却屏外层板的外侧壁或冷却屏外层板与冷却屏内层板之间的空腔内,下气管414的上端头连通设置在上法兰403上的进气孔a,所述进气孔a连通上气管410,所述上气管410的外端头连通气源。
46.进一步,所述吹气口设置为多个时,在下板420上设置复数个岛柱,在每个岛柱上分别设置拉制孔406,在拉制孔406的外围设置环形气道,所述环形气道的内缘面设有复数个贯通至拉制孔406的吹气口,环形气道的外缘面连通设置在岛柱上的气体通道,气体通道通过设置在下板420上的进气孔b连接下气管414,所述下气管414设置在冷却屏外层板的外侧壁或冷却屏外层板与冷却屏内层板之间的空腔内,下气管414的上端头连通设置在上法兰403上的进气孔a,所述进气孔a连通上气管410,所述上气管410的外端头连通气源。
47.进一步,所述下气管414设置在冷却屏外层板的外侧壁时,在下气管414的外缘面
包覆气体冷却管,在气体冷却管覆盖内的冷却屏外层板的外侧壁上设有至少一组冷却介质通孔。
48.进一步,所述上气管410的外端头连接调压阀,所述调压阀通过管道连接气源。
49.进一步,所述上气管410的外端头分别连接固定环403上的进气口415,所述进气口415连接调压阀,所述调压阀通过管道连接气源。
50.关于硅芯成型机构4的第二结构申请人已另行申报专利,在此不对其具体结构做累述。
51.进一步,具体实施时,如图6、7所示,所述硅芯成型机构4的第三结构为硅芯成型机构4包括冷却介质出管a401、冷却介质入管a402和空腔盘416,所述冷却介质出管a401与冷却介质入管a402的上端头连接固定环403上的冷却介质出入口,冷却介质出管a401与冷却介质入管a402的下端头连接空腔盘416,所述空腔盘416上的冷却介质通道419与冷却介质出管a401和冷却介质入管a402连通组成冷却介质通路,在空腔盘416的中部设有观察孔417或拉制孔406,在观察孔417或拉制孔406的外围设置至少一个拉制孔406,所述拉制孔406设置为多个时,多个拉制孔406环绕观察孔417设置,或多个拉制孔406为中间设置一个,另外几个环绕设置。
52.进一步,所述空腔盘416包括上板422、连接柱421和下板420,在所述下板420的上方设有上板422,在上板422上面的中部设有贯通至下板420下面的观察孔417,由下板420、上板422和观察孔417形成的空腔为冷却介质通道419,在冷却介质通道419内设有复数个连接柱421,每个连接柱421的上端和下端分别连接上板422和下板420,在每个连接柱421的中部分别设有拉制孔406,在上板422上分别设有至少一组贯通至冷却介质通道419的冷却介质下入口和冷却介质下出口。
53.进一步,为了提高硅芯拉制时的拉制速度,降低硅芯的椭圆度,保证同时拉制的每根硅芯3等径,每个拉制孔406下部的内缘面上设有至少一个吹气口,所述吹气口外接气源。实施时,吹气口的设置形式及其结构等同硅芯成型机构4的第二结构,因此,在此不做累述。
54.进一步,具体实施时,如图8所示,所述硅芯成型机构4的第四结构为硅芯成型机构4包括进气管423、吹气环主体424、连接管425、下吹气环426和吹气孔427,所述吹气环主体424为中空结构,吹气环主体424的外缘面上分别设有至少两个进气管423,在吹气环主体424的下面间隔设有复数个连接管425,在每个连接管425的下端头分别设有下吹气环426,在每个下吹气环426的内缘面上分别设有复数个吹气孔427。
55.具体实施时,每个下吹气环426分别环绕一根硅芯3设置,下吹气环426上开设多个吹气孔427,使从吹气孔427吹出的气体沿多个方向均匀吹向每根硅芯3。
56.进一步,在所述下吹气环426的上游设置一个或多个进气通道,通过连接管425将下吹气环426与进气通道相连通,所述的多个进气通道之间通过多个进气孔相互连通,使进入吹气装置的气流在所述的进气通道及下吹气环426内重新分布。
57.进一步,所述的进气通道为多个平行叠置的环形通道,冷却气体经进气管423进入之后,由第一进气通道进入第二进气通道,再经连接管425进入第三进气通道,后由吹气孔427吹向硅芯3。进气管423设置为两个,两个进气管423的外端外接气源。第一进气通道和第二进气通道均设置在圆环形的吹气环主体424内,第一进气通道设置在吹气环主体424的上方,第二进气通道设置在吹气环主体424的下方,通过多个进气孔相互连通。
58.进一步,所述的若干个下吹气环426设置在吹气环主体424下方,第三进气通道位于下吹气环426内部,通过连接管425将其与第二进气通道相连通,吹气孔427设置在下吹气环426上,对准硅芯3的结晶区。
59.实施时,所述籽晶夹头2为旋转式籽晶夹头或固定式籽晶夹头。当籽晶夹头2为固定式籽晶夹头时,在一圆盘上设置复数个固定孔,圆盘的下面设置复数个夹持件211,在圆盘的上面设置连接件连接上轴系统。当籽晶夹头2为旋转式籽晶夹头时,如图3所示,所述旋转式籽晶夹头包括电机201、连接盘210、夹持件211和旋转机构,在连接盘210上设有旋转机构,所述旋转机构包括主动力轴206、从动轴207、从动齿轮208和主动齿轮209,所述主动力轴206和从动轴207分别设置在主动力轴安装孔和从动轴安装孔内,在主动力轴206的外缘面上设有主动齿轮209,在从动轴207的外缘面上设有从动齿轮208,所述主动齿轮209的齿面与从动齿轮208的齿面啮合,所述主动力轴206的上端连接动力源,主动力轴206和从动轴207的下端分别连接夹持件211或从动轴207的下端连接夹持件211;所述旋转机构的输入端连接电机201或旋转机构的输入端连接硬轴,硬轴的另一端延伸至炉室1外后连接电机201,当旋转机构的输入端连接电机201时,电机201通过联轴器203连接主动力轴206的上端。在连接盘210的下部设有至少两个夹持件211,所述每个夹持件211连接旋转机构使夹持件211旋转,所述连接盘210的上部连接上提拉机构中的软轴。
60.实施时,为了保证电机201及旋转机构保持正常的工作温度,旋转式籽晶夹头的外部设有上冷却屏11。
61.所述旋转机构的替换结构为旋转机构包括主动力轴206、从动轴207、从动摩擦轮和主动摩擦轮,所述主动力轴206和从动轴207分别设置在主动力轴安装孔和从动轴安装孔内,在主动力轴206的外缘面上设有主动摩擦轮,在从动轴207的外缘面上设有从动摩擦轮,所述从动摩擦轮与主动摩擦轮接触,所述主动力轴206的上端连接动力源,主动力轴206和从动轴207的下端分别连接夹持件211或从动轴207的下端连接夹持件211。
62.所述连接盘210上部面的中部设有向下凹陷的环形凹槽,在所述凹槽的中部设有主动力轴安装孔,在所述主动力轴安装孔的外围设有至少一个从动轴安装孔,所述从动轴安装孔环绕主动力轴安装孔设置,在凹槽的上部设有连接盘盖体205,所述连接盘盖体205的中部设有内孔,在所述内孔的外围分别设有旋拧孔202和连接架固定孔204,所述连接架固定孔204上设有连接架,所述连接架连接上轴系统。
63.进一步,冷却介质为冷却水或冷却气体,如液氮等。
64.本实用新型在具体应用时,硅芯成型机构4设置在位于炉室1内坩埚9的上方,硅芯成型机构4的下面接近坩埚9内硅料融液7但不能接触,工作时,首先将碎硅料放入坩埚9内,开启加热器对位于坩埚支撑10上的坩埚9进行加热,待坩埚9内的碎硅料融化为硅料融液7后,籽晶夹头2带动籽晶下降,当籽晶穿过硅芯成型机构4上的拉制孔406与硅料融液7接触停止籽晶下降,待籽晶的下端头融化后缓慢提升籽晶,此时由于硅芯成型机构4内通入了冷却介质,使硅芯成型机构4底面的温度形成下高上低的温度梯度,此时,硅料融液7跟随籽晶上升,当硅料融液7接近硅芯成型机构4上的拉制孔406时,由于此处的温度低于坩埚9的温度,硅料融液7逐渐结晶,当结晶的硅料融液7通过拉制孔406进入硅芯成型机构4后温度逐渐降低便形成所需要的硅芯3,应用时,硅芯成型机构4还可以通过吹气口对刚刚结晶后的硅芯3进行强制冷却,拉制时,籽晶夹头2可以旋转,当籽晶夹头2上的夹持件211旋转时带动
拉制出的硅芯3旋转,通过硅芯3的旋转及调节吹气量的大小实现调整硅芯的椭圆度及保证同时拉制出的硅芯等径,大大提高了硅芯3的成品率及拉制效率。
65.本实用新型中涉及到的碎硅料不仅包括硅芯制备过程中出现的余料,不小心折断的硅芯,多/单晶硅生产企业在还原、切割、磨抛等工艺阶段产生的碎料等,同样还包括其它形状的硅料(比如菜花料、长度较小的硅棒等),或直接采购新的硅料使用本实用新型直接拉制硅芯。
66.本实用新型在实际应用时,不仅可以用于硅芯的拉制,同时还可以实现其它晶体材料的拉制。
67.以上内容中未细述部份为现有技术,故未做细述。
68.为了公开本实用新型的目的而在本文中选用的实施例,当前认为是适宜的,但是,应了解的是,本实用新型旨在包括一切属于本构思和发明范围内的实施例的所有变化和改进。