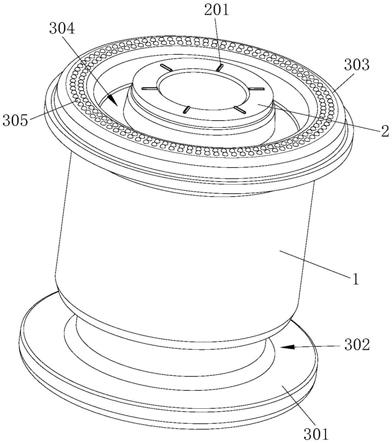
1.本实用新型涉及车辆零部件技术领域,特别涉及一种悬置衬套,同时,本实用新型还涉及一种具有该悬置衬套的车辆。
背景技术:
2.目前,悬置的类型主要有橡胶悬置、液压悬置、半主动悬置、和主动悬置。悬置的作用主要有以下几方面:固定并支撑汽车动力总成;承受动力总成内部因发动机或电机旋转和平移而产生的往复惯性力及力矩;承受汽车行驶过程中作用于动力总成上的一切动态力;隔离由于发动机或电机激励而引起的车架或车身的振动;隔离由于路面不平度以及车轮所受路面冲击而引起的车身振动向动力总成的传递。
3.但是,由于结构设计不合理,现有的悬置衬套在装配于车辆上后,容易在整车运动过程中因悬置衬套扭转而导致内芯转动,以及引起螺栓返松。另外,现有的悬置衬套由于自身结构存在设计缺陷,在向车身上压装时较为困难。
技术实现要素:
4.有鉴于此,本实用新型旨在提出一种悬置衬套,其可在整车运动过程中,有效防止内芯转动。
5.为达到上述目的,本实用新型的技术方案是这样实现的:
6.一种悬置衬套,包括外管、位于所述外管中的内芯,以及连接于所述内芯和所述外管之间的橡胶体,
7.所述内芯的两端分别伸于所述外管外,并于所述内芯至少一端的端面上构造有凸筋;
8.所述橡胶体具有伸于所述外管一端外的外伸部,所述外伸部包裹于所述内芯外;以及,
9.所述外伸部具有径向外凸的第一限位结构,所述第一限位结构的外径大于所述外管的外径;
10.所述第一限位结构中嵌设有骨架,且所述第一限位结构的一侧形成有避让空间;
11.所述避让空间用于在所述悬置衬套压装时,容纳压缩变形的至少部分所述第一限位结构。
12.进一步的,所述凸筋沿所述内芯的径向延伸设置;且所述凸筋为环所述内芯上芯孔的周向间隔布置的多个。
13.进一步的,所述凸筋的一端位于所述芯孔的边缘处。
14.进一步的,所述第一限位结构为沿所述外伸部周向设置的环状;所述骨架为沿所述第一限位结构的周向间隔布置的多段。
15.进一步的,相对于供所述外伸部伸出的一端,所述外管的另一端具有外翻布置的限位翻边;所述橡胶体具有覆盖于所述限位翻边上的第二限位结构。
16.进一步的,所述第一限位结构和/或所述第二限位结构的表面形成有若干凸起。
17.进一步的,所述橡胶体的形成有所述第二限位结构的一端设有凹槽;所述凹槽呈环形,并位于所述内芯和所述第二限位结构之间。
18.进一步的,所述内芯上设有沿自身径向外凸的凸出部。
19.相对于现有技术,本实用新型具有以下优势:
20.本实用新型所述的悬置衬套,通过在内芯至少一端的端面上构造凸筋,可在螺栓打紧时,使凸筋陷入与之配合的钣金件中,从而可有效防止整车运动过程中因悬置衬套扭转,而导致内芯转动及螺栓返松;另外,通过在第一限位结构中嵌设骨架,可有效减小悬置衬套的轴向位移,从而能够提升轴套的使用寿命;同时,设置避让空间,可便于悬置衬套的压装。
21.另外,将凸筋设为沿内芯的径向延伸设置,能够进一步防止因悬置扭转而导致内芯转动。通过将骨架设为沿第一限位结构的周向间隔布置的多段,能够提高对悬置轴套轴向限位的效果。而设置限位翻边,相较于现有限位结构采用粘接设置的方式,可有效避免胶水流淌而降低悬置衬套的外观质量;同时,设置覆盖于限位翻边上的第二限位结构,可有效降低限位翻边因与动力总成接触所导致的异响。
22.此外,通过在第一限位结构和/或第二限位结构的表面形成有若干凸起,可进一步改善异响问题。在内芯上设置沿自身径向外凸的凸出部,能够有效提升悬置轴套的轴向刚度。
23.本实用新型的另一目的在于提出一种车辆,所述车辆上应用有如上所述的悬置衬套。
24.本实用新型所述的车辆,通过应用如上所述的悬置衬套,可有效防止内管芯转动及螺栓返松,从而可提高对动力总成的支撑效果。
附图说明
25.构成本实用新型的一部分的附图用来提供对本实用新型的进一步理解,本实用新型的示意性实施例及其说明用于解释本实用新型,并不构成对本实用新型的不当限定。在附图中:
26.图1为本实用新型实施例一所述的悬置衬套的结构示意图;
27.图2为图1的俯视图;
28.图3为本实用新型实施例一所述的悬置衬套的轴向剖视图;
29.图4为图3中a部分的放大图。
30.附图标记说明:
31.1、外管;2、内芯;3、橡胶体;4、骨架;
32.101、限位翻边;
33.201、凸筋;202、芯孔;203、凸出部;
34.301、第一限位结构;302、避让空间;303、第二限位结构;304、凹槽;305、凸起。
具体实施方式
35.需要说明的是,在不冲突的情况下,本实用新型中的实施例及实施例中的特征可
以相互组合。
36.在本实用新型的描述中,需要说明的是,若出现“上”、“下”、“内”、“背”等指示方位或位置关系的术语,其为基于附图所示的方位或位置关系,仅是为了便于描述本实用新型和简化描述,而不是指示或暗示所指的装置或元件必须具有特定的方位、以特定的方位构造和操作,因此不能理解为对本实用新型的限制。此外,若出现“第一”、“第二”等术语,其也仅用于描述目的,而不能理解为指示或暗示相对重要性。
37.下面将参考附图并结合实施例来详细说明本实用新型。
38.实施例一
39.本实施例涉及一种悬置衬套,在整体构成上,由图1至图3中所示,其包括外管1、位于外管1中的内芯2,以及连接于内芯2和外管1之间的橡胶体3。
40.其中,外管1呈圆筒状,内芯2也为圆筒状,且内芯2的两端分别伸于外管1外,并于内芯2至少一端的端面上构造有凸筋201。另外,为提高悬置衬套的轴向刚度,由图3中所示,在内芯2上设有沿自身径向外凸的凸出部203。而且,该凸出部203可为图3中示出的一个,亦可设为间隔设置的多个。
41.本实施例中,作为一种优选的实施方式,如图3中所示,内芯2的两个端面上均构造有凸筋201,以此可在螺栓打紧时,使两端的凸筋201均陷入与各自配合的钣金件中,从而可有效防止因悬置衬套扭转而导致内芯2转动,以及引起螺栓返松。其中,钣金件具体为用于和悬置衬套连接的部件,例如为动力总成的安装支架。
42.另外,为提高使用效果,结合图1和图2中所示,凸筋201的一端位于芯孔202的边缘处,并为沿内芯2的径向延伸设置的直条状。进一步地,本实施例的凸筋201为环内芯2上芯孔202的周向间隔布置的多个,且具体为图2中示出的六个。
43.在此,需要说明的是,凸筋201除了沿内芯2的径向延伸设置,亦可设为沿内芯2的周向延伸设置的弧形,或者设为不规则形状,但此时,可能会降低使用效果。另外,除了将凸筋201的一端设于芯孔202的边缘处,亦可使凸筋201的一端与芯孔202的边缘之间间距布置。
44.继续参照图1至图3中所示,橡胶体3具有伸于外管1一端的外伸部,且该外伸部包裹于内芯2外。而且,外伸部具有径向外凸的第一限位结构301,且作为一种优选的实施方式,如图1中所示,该第一限位结构301为沿外伸部的周向设置的环状,且其外径大于外管1的外径。可以理解的是,除了将第一限位结构301设为环状,亦可将其设为沿外伸部的周向间隔设置的多段,但此时可能会降低使用效果。
45.本实施例中,为便于悬置衬套于车身上的压装,由图4结合图3中所示,在第一限位结构301靠近外管1的一侧形成有避让空间302,以用于在悬置衬套压装时,容纳压缩变形的至少部分第一限位结构301。其中,作为一种具体的实施方式,本实施例的避让空间302为环外伸部的周向设置的环形槽,且该环形槽槽底位置的橡胶体3的半径小于外管1的半径。
46.此时,为保证悬置轴套的使用效果,仍由图4中所示,在第一限位结构301中嵌设有骨架4,如此设置,可有效减小悬置衬套的轴向位移,从而能够提升轴套的使用寿命。作为一种进一步的实施方式,本实施例的骨架4为沿第一限位结构301的周向间隔布置的多段,并具体可采用金属制成,例如可采用钢制成。另外,为降低异响,结合图1和图2中所示,在第一限位结构301的表面形成有多个凸起305。
47.此外,为提高使用效果,由图1结合图3中所示,相对于供外伸部伸出的一端,外管1的另一端(也即图3中所示的底端)具有外翻布置的限位翻边101,橡胶体3具有覆盖于该限位翻边101上的第二限位结构303。通过设置限位翻边101,相较于现有限位结构采用粘接设置的方式,可有效避免胶水流淌而降低悬置的外观质量;同时,设置覆盖于限位翻边101上的第二限位结构303,可有效降低限位翻边101因与动力总成接触所导致的异响。
48.另外,为进一步改善异响问题,本实施例中,在第二限位结构303的表面也形成有多个凸起305。为提高悬置衬套的使用性能,由图1中所示,在橡胶体3的形成有第二限位结构303的一端设有凹槽304,该凹槽304具体呈环形,并位于内芯2和第二限位结构303之间。
49.本实施例的悬置衬套,通过设置上述结构,可有效防止整车运动过程中因悬置衬套扭转,而导致内芯2转动及螺栓返松;另外,通过在第一限位结构301中嵌设骨架4,可有效减小悬置衬套的轴向位移,从而能够提升轴套的使用寿命;同时,设置避让空间302,可便于悬置衬套的压装,因而可具有较好的使用效果。
50.实施例二
51.本实施例涉及一种车辆,该车辆上应用有实施例一所述的悬置衬套。
52.本实施例的车辆,通过应用实施例一所述的悬置衬套,可有效防止内芯2转动及螺栓返松,从而可提高对动力总成的支撑效果。
53.以上所述仅为本实用新型的较佳实施例而已,并不用以限制本实用新型,凡在本实用新型的精神和原则之内,所作的任何修改、等同替换、改进等,均应包含在本实用新型的保护范围之内。