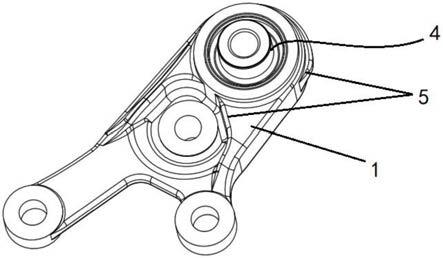
1.本实用新型涉及汽车悬置系统的设计制造领域,更具体的说,它涉及后悬置连接支架。
背景技术:
2.随着汽车行业的发展,3点式悬置系统一直具备优异的成绩,所以对悬置系统的要求越来越高;后悬置连接支架是支撑动力总成的重要组成部分,是动力总成与车身支架连接元件,所以对于动力总成的限位固定和隔振有着非常高的要求;而现有的连接支架一般多铝材,这样在整体强度上就会有缺陷,需要更多的加强筋辅助或者将零件设计的厚重,导致空间占用大,在复杂狭小的后悬置装配位置较难匹配,可能会导致零件间的干涉,各车型间通用性差,需针对车型反复重新设计。
技术实现要素:
3.本实用新型克服了现有技术的不足,提供结构简单、设计合理、强度较高、尺寸较小、便于匹配安装、空间占用小、通用性优秀的后悬置连接支架。
4.为了解决上述技术问题,本实用新型的技术方案如下:
5.后悬置连接支架,包括支架本体,后悬置连接支架的装配孔和定位孔均设置于支架本体上;所述定位孔包括主定位孔和辅助定位孔;所述主定位孔设置于支架本体的中间区域;所述辅助定位孔设置于支架本体的一端;所述装配孔设置于支架本体远离辅助定位孔的一端。
6.进一步的,所述支架本体采用铸铁。
7.进一步的,所述支架本体呈腰型的柱状;装配孔、主定位孔和辅助定位孔均将支架本体的上下表面贯穿,且装配孔、主定位孔和辅助定位孔的中心轴线在垂直方向相互平行。
8.进一步的,所述主定位孔设置于支架本体的中心位置;在支架本体上表面对应主定位孔的区域设置有定位下凹,所述定位下凹环绕主定位孔设置;在支架本体下表面对应主定位孔的区域设置有定位凸起,所述定位凸起环绕主定位孔设置;在定位凸起上设置有主定位孔延伸部,所述主定位孔延伸部的内径与主定位孔的内径对应。
9.进一步的,所述装配孔的长度>支架本体的厚度;在装配孔的两端均设置有辅助装配部,其中位于支架本体下表面的辅助装配部与定位凸起连接。
10.进一步的,还包括衬套,所述衬套设置于装配孔内;所述衬套包括外套、橡胶和内芯,所述外套的外表面与装配孔接触,并将橡胶包裹;所述橡胶将内芯包裹。
11.进一步的,所述内芯采用铁材质;橡胶衬套与支架采用过盈压装。
12.进一步的,所述辅助定位孔包括第一辅助定位孔和第二辅助定位孔;第一辅助定位孔位于主定位孔的一侧,第二辅助定位孔位于主定位孔的另一侧;第一辅助定位孔与主定位孔之间的距离>第二辅助定位孔与主定位孔之间的距离。
13.进一步的,所述支架本体包括支架延伸,第一辅助定位孔设置于支架延伸上;第二
辅助定位孔设置于支架本体远离装配孔的一端,且处于远离支架延伸的一侧。
14.进一步的,还包括加强筋,所述加强筋包括上加强筋和侧加强筋;所述上加强筋设置于支架本体的上表面,其环绕支架本体上表面的辅助装配部和定位下凹;所述侧加强筋设置于支架本体的侧表面。
15.本实用新型的有益效果是:
16.由于车辆后悬置装配环境相对狭小,所以对后悬置支架的尺寸要求比较高;本产品对铁支架进行了新的结构设计,使得本实用新型整体的结构更为紧凑,进而使得本实用新型的结构更小,便于匹配安装;其不仅对装配空间需求更低,还通过加强筋使得本实用新型的强度也得到提升,确保了各车型间的通用性。
17.相较于当前市面上采用铝材制成的连接支架强度低的情况;本产品采用了铸铁材质的支架本体,使其的结构强度得到提升,并且铸铁相对来说成本更低。
18.车身同动力总成件之间采用了衬套连接,保证了强度的情况下提高车辆舒适性;内芯采用铁材质,以保证连接强度;橡胶起到隔振的效果,进而提升车辆舒适性;外套避免了橡胶材料部分直接与支架间距摩擦损伤导致使用寿命降低;橡胶衬套与支架采用过盈压装,使得本实用新型承载能力大、耐冲击性好。
附图说明
19.图1为本实用新型整体结构图。
20.图2为支架本体正面结构图。
21.图3为支架本体反面结构图。
22.图4为衬套结构图。
23.图中标号:
24.1.支架本体;2.装配孔;3.定位孔;4.衬套;5.加强筋;11.定位下凹;12.定位凸起;13.主定位孔延伸部;21.辅助装配部;30.辅助定位孔;31.第一辅助定位孔;32.第二辅助定位孔;33.支架延伸;34.主定位孔;41.外套;42.橡胶件;43.内芯;51.上加强筋;52.侧加强筋。
具体实施方式
25.下面结合附图和具体实施例对本实用新型进一步说明。应当说明的是,实施例只是对本实用新型的具体阐述,其目的是为了让本领域技术人员更好地理解本实用新型的技术方案,不应视为对本实用新型的限定。
26.实施例:
27.如图1-4所示,后悬置连接支架,包括支架本体1,后悬置连接支架的装配孔2和定位孔3均设置于支架本体1上;所述定位孔3包括主定位孔34和辅助定位孔30;所述主定位孔34设置于支架本体1的中间区域;所述辅助定位孔30设置于支架本体1的一端;所述装配孔2设置于支架本体1远离辅助定位孔30的一端;由于车辆后悬置装配环境相对狭小,所以对后悬置支架的尺寸要求比较高;本产品对铁支架进行了新的结构设计,使得本实用新型整体的结构更为紧凑,进而使得本实用新型的结构更小,便于匹配安装;其不仅对装配空间需求更低,还通过加强筋5使得本实用新型的强度也得到提升,确保了各车型间的通用性。
28.在本实施例中,所述支架本体1采用铸铁,使本实用新型的结构强度得到提升,并且铸铁相对来说成本更低,使得本实用新型的制造成本能够更低;在支架本体1的结构强度还需要提升时,也可以采用强度更高的材料。
29.在本实施例中,所述支架本体1呈腰型的柱状;装配孔2、主定位孔34和辅助定位孔30均将支架本体1的上下表面贯穿,且装配孔2、主定位孔34和辅助定位孔30的中心轴线在垂直方向相互平行;使得本实用新型的装配方向一致,进而使得本实用新型在装配后更为牢固稳定;并且可根据实际装配的情况和需求改变装配孔2、主定位孔34和辅助定位孔30的设置朝向,使其能够适应与更多的装配环境和更多型号的车辆。
30.所述主定位孔34设置于支架本体1的中心位置;在支架本体1上表面对应主定位孔34的区域设置有定位下凹11,所述定位下凹11环绕主定位孔34设置;在支架本体1下表面对应主定位孔34的区域设置有定位凸起12,所述定位凸起12环绕主定位孔34设置;在定位凸起12上设置有主定位孔延伸部13,所述主定位孔延伸部13的内径与主定位孔34的内径对应;所述支架本体1在装配时可通过定位下凹11和定位凸起12与对应的装配位置进行贴合,使得本实用新型的装配更为牢固;所述主定位孔延伸部13进一步的稳定本实用新型的装配,主定位孔延伸部13的内径与主定位孔34的内径对应,使得主定位孔延伸部13在进行辅助装配的同时,不会影响主定位孔34本身的装配效果。
31.所述装配孔2的长度>支架本体1的厚度;在装配孔2的两端均设置有辅助装配部21,其中位于支架本体1下表面的辅助装配部21与定位凸起12连接,使得本实用新型整体的结构更为牢固稳定,进而减少加强筋5等辅助加强结构的设置,进而减小本实用新型的体积,降低本实用新型空间占用。
32.在本实施例中,还包括衬套4,所述衬套4设置于装配孔2内;所述衬套4包括外套41、橡胶件42和内芯43,所述外套41的外表面与装配孔2接触,并将橡胶件42包裹;所述橡胶件42将内芯43包裹;车身同动力总成件之间采用了衬套4连接,保证了强度的情况下提高车辆舒适性;内芯43采用铁材质,以保证连接强度;橡胶件42起到隔振的效果,进而提升车辆舒适性;外套41避免了橡胶件42直接与支架间距摩擦损伤导致使用寿命降低;衬套4与支架采用过盈压装,使得本实用新型承载能力大、耐冲击性好。
33.在本实施例中,所述辅助定位孔30包括第一辅助定位孔31和第二辅助定位孔32;第一辅助定位孔31位于主定位孔34的一侧,第二辅助定位孔32位于主定位孔34的另一侧;第一辅助定位孔31与主定位孔34之间的距离>第二辅助定位孔32与主定位孔34之间的距离;通过多个不同位置的定位孔3加强本实用新型完成固定后的整体稳定性;所述支架本体1包括支架延伸33,第一辅助定位孔31设置于支架延伸33上;第二辅助定位孔32设置于支架本体1远离装配孔2的一端,且处于远离支架延伸33的一侧;一般情况下,主定位孔34、第一辅助定位孔31和第二辅助定位孔32呈三角形状分布,通过三角形结构更为牢固稳定的原理,使得本实用新型装配时更为牢固稳定;当然在实际装配中,辅助定位孔30的数量可根据对应的汽车型号以及需求选择增加或者减少;并且支架延伸33的长度可更具实际的装配需求进行调整,避免本实用新型的占用空间过大。
34.在本实用新型中,还包括加强筋5,所述加强筋5包括上加强筋51和侧加强筋52;所述上加强筋51设置于支架本体1的上表面,其环绕支架本体1上表面的辅助装配部21和定位下凹11;所述侧加强筋52设置于支架本体1的侧表面;所述上加强筋51和侧加强筋52用于加
强本实用新型整体结构;并且上加强筋51和侧加强筋52均设置于支架本体1上,避免了加装过多辅助加强结构。
35.值得说明的是,实用新型的其他技术方案均属于现有技术,故不作赘述。
36.以上所述仅是本实用新型优选实施方式,应当指出,对于本技术领域的普通技术人员,在不脱离本实用新型构思的前提下,还可以做出若干改进和润饰,这些改进和润饰也应视为本实用新型保护范围。