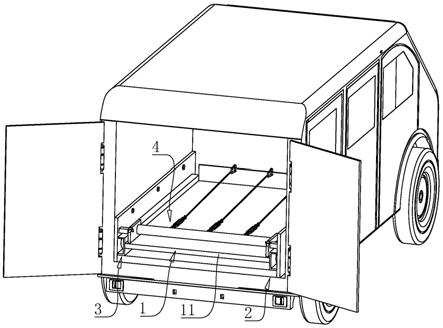
1.本技术涉及货物承运设备技术领域,尤其涉及一种货物装载卸载一体设备及其应用。
背景技术:
2.目前,自重较大的货物会通过诸如飞机、火车、货车等具备封闭式厢体结构的移运设备进行运输。
3.当货物需要从厢体结构内卸载时,卸货人员大多先通过叉车将货物移运至厢体结构外部,再通过行车将货物吊运至指定地点。
4.针对上述中的相关技术,发明人认为存在有以下缺陷:货物从厢体结构内部向外移运时过于繁琐,降低了卸货人员对货物的卸货效率。
技术实现要素:
5.为了改善货物不便从厢体结构内部向外移运的问题,本技术提供了货物装载卸载一体设备及其应用。
6.第一方面,本技术提供的货物装载卸载一体设备采用如下的技术方案:一种货物装载卸载一体设备,包括载物装置和固定装置,所述载物装置用于装载货物,所述固定装置用于安装载物装置;所述固定装置包括底撑板、两块支撑板和多个固定螺栓,两块所述支撑板设置于底撑板相对的两侧,所述固定螺栓用于将底撑板和支撑板固定于安装固定装置的载体上;所述载物装置包括载物板,所述载物板通过滑移机构滑动设置于支撑板上。
7.通过采用上述技术方案,载物板用于承接货物,以保障货物的运输稳定性;当货物需要卸载时,载物板通过滑移机构在支撑板上滑移,使载物板一端位移至载体的车厢外部,进而便于卸货人员调动行车以吊运货物至指定地点;此过程减少了叉车将货车从载体的车厢内搬运至车厢外的步骤,极大地降低了货物的卸载难度,缩短了货物的卸载时间,提高了卸货人员对货物的卸载效率。
8.优选的,所述滑移机构包括两条侧撑条和多个导向轮;所有所述导向轮间隔设置于两块支撑板相互朝向的侧壁上,两条所述侧撑条分别设置于载物板朝向支撑板的侧壁;每条所述侧撑条朝向支撑板的侧壁设置有滑移通道,所述侧撑条通过滑移通道滑动设置于导向轮上。
9.通过采用上述技术方案,侧撑条通过滑移通道套接于导向轮上,使载物板宽度方向侧与支撑板滑动连接,载物板稳定架设于底撑板上方;卸货人员拉动载物板时,载物板可沿支撑板的长度方向快速位移,进而以将载物板的一端快速拉动至载体的车厢外部,以便货物实现快速卸载。
10.优选的,所述侧撑条上插设有卡位螺栓,所述底撑板上设置有供卡位螺栓插接的插接槽。
11.通过采用上述技术方案,卡位螺栓的杆体穿过侧撑条后插接于插接槽内,使得侧撑条快速定位于底撑板上方,限定了侧撑条相对底撑板的位置,进而减少了载物板沿支撑条的长度方向出现自由位移的现象。
12.优选的,所述载物板和底撑板之间设置有限位钢索,所述限位钢索用于限制载物板沿底撑板的长度方向位移。
13.通过采用上述技术方案,当所有导向轮均位于滑移通道内腔时,限位钢索处于自由拉伸状态,载物板可沿支撑板的长度方向滑移;当载物板在底撑板上位移一定距离后,限位钢索处于张紧拉直状态,以减少载物板在底撑板上进一步位移的现象,进而减少了载物板完全脱离底撑板上方的现象。
14.优选的,所述载物板上设置有卡接机构,所述卡接机构包括限位轴、对拉钩和连接钢索;所述限位轴设置于载物板的顶壁上,所述对拉钩设置于限位轴的外缘壁上;所述连接钢索长度方向的一端与对拉钩固定连接,所述连接钢索长度方向的另一端固定设置于载物板上。
15.通过采用上述技术方案,连接钢索抵接于货物远离载物的一侧,连接钢索长度方向的一端与限位轴上的对拉钩固定,另一端与载物板固定,进而使得货物稳定绑扎于载物板上,保障了货物在载物板上的位置稳定性及运输稳定性。
16.优选的,所述连接钢索与载物板之间设置有安装组件,所述安装组件包括连接板和卡固件;所述连接板设置于载物板上,且所述连接板与限位轴分别位于载物板长度方向的两端;所述卡固件用于将连接钢索靠近连接板的一端固定于连接板上。
17.通过采用上述技术方案,卡固件同时套接连接板和连接钢索,以实现连接钢索在底撑板上的快速固定;同时,卡固件便于卸载人员快速拆除连接钢索与连接板之间的连接结构,以对长时间使用的连接钢索保养、换新。
18.优选的,所述连接钢索与对拉钩之间设置有调节组件,所述调节组件为花篮螺栓;所述花篮螺栓用于将连接钢索靠近对拉钩的一端固定于对拉钩上。
19.通过采用上述技术方案,操作人员通过顺时针旋拧花篮螺栓,以缩短连接钢索与对拉钩之间的距离,使得连接钢索快速张紧于对拉钩与连接板之间,进而通过连接钢索将货物稳定固定于载物板上;操作人员逆时针旋拧花篮螺栓,以增大连接钢索与对拉钩之间的距离,进而便于卸货人员拆除连接钢索与对拉钩之间的连接结构,以便货物从载物板上卸载。
20.优选的,所述限位轴与载物板之间设置有定位组件,所述定位组件包括两块卡位板和定位螺栓;两块所述卡位板相对设置于载物板上,所述限位轴抵接设置于两块卡位板之间;所述定位螺栓螺纹连接于每块卡位板上,所述限位轴长度方向的端壁设置有与定位螺栓螺纹配合的锁止槽。
21.通过采用上述技术方案,限位轴抵接于两块卡位板之间,定位螺栓的杆体穿过卡位板后螺纹拧紧于锁止槽内,使得限位轴固定于两块卡位板之间,进而以实现限位轴在载物板上的快速安装;同时,便于限位轴在载物板上拆卸,以便卸货人员将货物从载物板上卸载下来。
22.优选的,所述卡位板与支撑板之间设置有抵紧组件,所述抵紧组件包括抵接块、异形条和抵触块;所述抵接块设置于支撑板朝向卡位板的侧壁,所述异形条一端同时穿设于
卡位板和抵接块,所述抵触块设置于异形条另一端的外缘壁上;所述卡位板上设置有让位平面,所述抵触块上设置有导向槽,所述抵触块通过导向槽卡接于卡位板的让位平面上。
23.通过采用上述技术方案,异形条通过同时穿设于卡位板和抵接块,以限定卡位板相对支撑板的位置;抵触块通过导向槽卡接于卡位板的让位平面上,以保障异形条在卡位板上的定位稳定性,进而通过卡位板不易相对支撑板位移,减少了载物板相对底撑板位移的现象,提高了货物在载物板上的装载稳定性及运输稳定性。
24.第二方面,本技术提供的货物装载卸载一体设备的应用采用如下的技术方案:一种货物装载卸载一体设备的应用,所述货物装载卸载一体设备用于货物在飞机或火车或货车上的装载和卸载。
25.通过采用上述技术方案,货物可在货物装载卸载一体设备上稳定装载、运输,同时便于卸货人员快速将货物从货物装载卸载一体设备上卸载下来,提高了卸货人员对货物的卸载效率。
26.综上所述,本技术具有以下有益技术效果:1.当货物需要卸载时,载物板通过滑移机构在支撑板上滑移,使载物板一端位移至载体的车厢外部,进而便于卸货人员调动行车以吊运货物至指定地点;此过程减少了叉车将货车从载体的车厢内搬运至车厢外的步骤,极大地降低了货物的卸载难度,缩短了货物的卸载时间,提高了卸货人员对货物的卸载效率;2.异形条通过同时穿设于卡位板和抵接块,以限定卡位板相对支撑板的位置;抵触块通过导向槽卡接于卡位板的让位平面上,以保障异形条在卡位板上的定位稳定性,进而通过卡位板不易相对支撑板位移,减少了载物板相对底撑板位移的现象,提高了货物在载物板上的装载稳定性及运输稳定性。
附图说明
27.图1是本技术实施例中一种货物装载卸载一体设备的结构示意图;图2是本技术实施例中用于体现载物板和固定装置位置关系的示意图;图3是本技术实施例中载物板和支撑板、底撑板连接关系的示意图;图4是本技术实施例中限位轴和卡位板连接关系的爆炸示意图;图5是图4中a部分的放大示意图。
28.附图标记说明:1、载物装置;11、载物板;111、限位钢索;2、固定装置;21、底撑板;211、插接槽;22、支撑板;23、固定螺栓;3、滑移机构;31、侧撑条;311、滑移通道;312、卡位螺栓;32、导向轮;4、卡接机构;41、限位轴;411、锁止槽;42、对拉钩;43、连接钢索;5、定位组件;51、卡位板;511、让位平面;52、定位螺栓;6、抵紧组件;61、抵接块;62、异形条;621、水平杆;622、纵向杆;63、抵触块;631、导向槽;7、安装组件;71、连接板;711、通孔;72、卡固件;8、调节组件;81、花篮螺栓。
具体实施方式
29.本技术实施例公开了一种货物装载卸载一体设备。货物装载卸载一体设备用于在飞机或火车或货车的车厢内进行货物的装载和卸载。
30.以下结合附图1-5对本技术作进一步详细说明。
31.参照图1,货物装载卸载一体设备包括载物装置1和固定装置2。在本实施例中,载物装置1包括载物板11,载物板11为实心钢板,载物板11用于承接、装载货物。固定装置2安装于面包车上,载物板11通过滑移机构3滑动设置于固定装置2上。当面包车将货物运抵至指定地点时,载物板11通过在固定装置2上滑移,以将货物移运至面包车的车厢外部。此过程减少了叉车的应用,卸货人员可通过行车直接将载物板11上的货物移运至指定地点,提高了卸货人员对货物的卸货效率。
32.参照图2和图3,固定装置2包括底撑板21、两块支撑板22和多个固定螺栓23。底撑板21沿水平方向放置于面包车的车厢内底壁,底撑板21沿面包车的车厢的长度方向延伸,固定螺栓23将底撑板21固定于面包车的车厢内。两块支撑板22分别焊接于底撑板21宽度方向的两侧,支撑板22沿底撑板21的长度方向延伸,且每块支撑板22远离底撑板21的侧壁均抵紧于面包车的车厢内侧壁,固定螺栓23固定连接支撑板22与面包车的车厢。
33.参照图2和图3,滑移机构3包括两条侧撑条31和多个导向轮32。多个导向轮32分别通过螺栓转动设置于两块支撑板22相互朝向的侧壁上,相邻的所有导向轮32沿支撑板22的延伸方向等距分布,且导向轮32位于底撑板21上方。两条侧撑条31分别焊接于载物板11宽度方向的两侧,每条侧撑条31均沿载物板11的长度方向延伸。
34.参照图2和图3,每条侧撑条31朝向支撑板22的侧壁设置有滑移通道311,滑移通道311沿侧撑条31的长度方向设置,且于侧撑条31长度方向的两端均为开口设置。侧撑条31通过滑移通道311套接于导向轮32上,当所有导向轮32均位于滑移通道311内腔时,载物板11稳定定位于底撑板21上方。卸货人员可将载物板11沿支撑板22的长度方向滑移,使载物板11滑移至面包车的车厢外部,以便货物快速卸载。需要说明的是,滑移机构3亦可以为电驱动结构。操作人员可在底撑板21的顶壁上安装电动缸,通过电动缸的输出端与载物板11的底壁固定连接,实现载物板11在底撑板21上的自动化位移,以节省人力,提高卸货人员对货物的卸载效率。
35.参照图2和图3,侧撑条31上沿竖直方向插设有卡位螺栓312,底撑板21上设置有插接槽211,插接槽211对应卡位螺栓312的杆体设置。当所有导向轮32均位于滑移通道311内腔时,载物板11位于面包车的车厢内,卡位螺栓312的杆体穿过侧撑条31后抵接于插接槽211内,使得侧撑条31定位于底撑板21上方,进而以减少载物板11在固定装置2上出现自由位移的现象。
36.参照图2和图3,载物板11与底撑板21之间还共同设置有限位钢索111,在本实施例中,限位钢索111由不锈钢链条制得,限位钢索111的数量可以为三根,所有限位钢索111的长度尺寸等同,且均小于载物板11和底撑板21的长度尺寸。限位钢索111长度方向的一端焊接于底撑板21的顶壁上,限位钢索111长度方向的另一端焊接于载物板11朝向面包车的端壁上。当载物板11沿支撑板22的长度方向滑移,使载物板11远离限位钢索111的一端位于面包车外部一定尺寸后,限位钢索111处于拉直张紧状态,进而以减少载物板11完全脱离底撑板21上方的现象。
37.参照图2和图3,载物板11上设置有卡接机构4,卡接机构4包括限位轴41。
38.参照图3和图4,限位轴41通过定位组件5固定于载物板11上,且限位轴41位于载物板11长度方向的一端。定位组件5包括两块卡位板51和定位螺栓52,两块卡位板51相对焊接
于载物板11的顶壁上,且两块卡位板51分别位于载物板11宽度方向的两侧。在本实施例中,限位轴41位于两块卡位板51之间,且限位轴41长度方向的端壁与卡位板51的侧壁相抵。
39.参照图4,限位轴41长度方向的两端分别设置有锁止槽411,锁止槽411为螺纹槽。定位螺栓52螺纹连接于每块卡位板51上,且定位螺栓52的杆体可螺纹拧紧于锁止槽411内,使限位轴41固定于两块卡位板51之间。此时,限位轴41悬空架设于载物板11上方。
40.参照图4和图5,卡位板51与支撑板22之间还共同设置有抵紧组件6,在本实施例中,抵紧组件6包括抵接块61、异形条62和抵触块63。抵接块61焊接于支撑板22朝向卡位板51的侧壁,以减少支撑板22与卡位板51之间的空隙。在本实施例中,异形条62为l型条,异形条62长度方向的一端为水平杆621,另一端为纵向杆622,水平杆621与纵向杆622相互垂直且一体成型。水平杆621可同时穿设于卡位板51和抵接块61,使纵向杆622抵接于卡位板51远离支撑板22的侧壁。
41.参照图5,抵触块63一体成型于纵向杆622上,且抵触块63上设置有导向槽631。卡位板51上倾斜设置有让位平面511,操作人员将水平杆621同时穿设于卡位板51和抵接块61后,纵向杆622可沿竖直方向抵接于卡位板51远离支撑板22的侧壁,此时,抵触块63位于卡位板51上方。操作人员转动纵向杆622,使抵触块63通过导向槽631抵接于卡位板51的让位平面511上,限定了卡位板51相对支撑板22的位置,减少了载物板11在底撑板21上方出现自由位移的现象。
42.参照图3和图4,卡接机构4还包括对拉钩42和连接钢索43,对拉钩42焊接于限位轴41的外缘壁上。在本实施例中,限位轴41上的对拉钩42数量可以为三个,三个对拉钩42沿限位轴41的长度方向等距分布。连接钢索43的数量等同于对拉钩42的数量,连接钢索43沿载物板11的长度方向延伸。连接钢索43长度方向的一端通过安装组件7与载物板11固定连接,安装组件7位于载物板11远离限位轴41方向的一端。
43.参照图2和图3,安装组件7包括连接板71和卡固件72,连接板71垂直焊接于载物板11的顶壁上,在本实施例中,连接板71与限位轴41分别位于载物板11长度方向的两端。卡固件72为不锈钢制得的可按压式卡扣,连接板71上贯穿设置有供卡固件72套接的通孔711,卡固件72穿过连接钢索43后通过通孔711套接于连接板71上,进而使得连接钢索43长度方向的一端固定于载物板11上。
44.参照图2和图3,连接钢索43长度方向的另一端通过调节组件8与对拉钩42固定连接,在本实施例中,调节组件8包括花篮螺栓81。当货物装载于载物板11上时,操作人员先将花篮螺栓81长度方向的一端与连接钢索43相连,再将连接钢索43抵接于货物远离载物板11的侧壁,最后通过花篮螺栓81将连接钢索43长度方向的另一端固定连接于对拉钩42上,使得连接钢索43将货物稳定定位于载物板11上,保障了货物在运输过程中的稳定性。
45.本技术实施例一种货物装载卸载一体设备的实施原理为:当货物装载于载物板11的顶壁上时,操作人员将连接钢索43穿过货物远离载物板11的侧壁,通过花篮螺栓81将连接钢索43紧密连接于对拉钩42上,进而通过连接钢索43将货物绑扎于载物板11上,保障了货物在载物板11上的位置稳定性及运输稳定性。
46.当面包车将货物运抵至指定地点时,卸货人员可向上提拉卡位螺栓312,以拆除侧撑条31与底撑板21之间的限位结构。接着,转动纵向杆622,使抵触块63位于至卡位板51上方,以便卸货人员将水平杆621从抵接块61和卡位板51上抽离出来。接着,卸货人员拉动载
物板11沿支撑板22的长度方向滑移,使载物板11一端位移至面包车的车厢外部,此时,卸货人员旋拧花篮螺栓81,使连接钢索43脱离对拉钩42,进而便于连接钢索43从货物上脱离。卸货人员通过操作人员行车,以将货物吊运至指定地点。
47.以上均为本技术的较佳实施例,并非依此限制本技术的保护范围,故:凡依本技术的结构、形状、原理所做的等效变化,均应涵盖于本技术的保护范围之内。