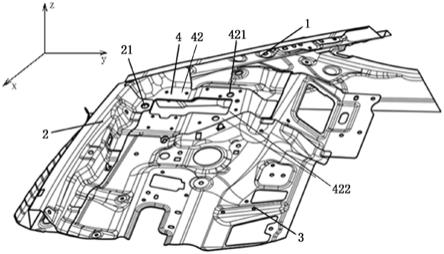
1.本实用新型属于汽车技术领域,具体提供一种汽车后尾门区域车身结构。
背景技术:
2.汽车后尾门作为重要的车身部件,起着密闭行李箱、美化车身外观的重要作用。同时后尾门作为一个功能部件,还需要具有开闭功能来保证行李的放入或取出。而后尾门开闭功能则需要铰链来实现,铰链总成将车体与后尾门连接起来构成后尾门开闭机构,从而实现后尾门的开闭功能。现有的后尾门铰链固定在汽车后方的衣帽架上,由于汽车后方的衣帽架的刚度较差,并且衣帽架用于放置物品,本身已经承受了较大的压力,铰链设置在衣帽架上,使其承受的压力又大大增加,为保证整体结构的稳定,往往需要对铰链安装位置进行局部加强,不仅增加了汽车的成本,侵占了行李箱的空间,也增加了多次使用后变形的风险,变形后尾门和车身配合不均,易导致关门力变大,尾门区域漏水,行驶中异响等常见问题。
3.相应的,本领域需要一种新的汽车后尾门区域车身结构来解决现有汽车后尾门铰链安装位置强度较差,铰链占用行李箱空间较多的问题。
技术实现要素:
4.为了解决现有技术中的上述问题,即为了解决现有汽车尾门铰链安装位置强度较差,铰链占用行李箱空间较多的问题,本实用新型提供了一种汽车后尾门区域车身结构,包括侧围总成、后挡风玻璃安装横梁、后排座椅安装横梁、铰链总成、铰链安装板总成,所述侧围总成两侧与所述后挡风玻璃安装横梁、后排座椅安装横梁依次固定成环形结构,所述铰链安装板总成设置在所述环形结构内,并且所述铰链安装板总成与所述侧围总成、后挡风玻璃安装横梁均固定连接,所述铰链总成与所述铰链安装板总成固定连接。
5.在上述汽车后尾门区域车身结构的优选技术方案中,所述汽车后尾门区域车身结构包括衣帽架总成,所述衣帽架总成设置在所述环形结构内,所述衣帽架总成与所述后挡风玻璃安装横梁、铰链安装板总成、后排座椅安装横梁依次固定连接。
6.在上述汽车后尾门区域车身结构的优选技术方案中,所述铰链安装板总成包括铰链安装板,所述铰链安装板与所述侧围总成、后挡风玻璃安装横梁均固定连接,所述铰链总成固定连接在所述铰链安装板上。
7.在上述汽车后尾门区域车身结构的优选技术方案中,所述铰链安装板总成包括铰链安装加强板,所述铰链安装板下方固定连接所述铰链安装加强板,所述铰链安装加强板分别与所述侧围总成、后挡风玻璃安装横梁固定连接。
8.在上述汽车后尾门区域车身结构的优选技术方案中,所述铰链安装板设置有两个第一安装孔。
9.在上述汽车后尾门区域车身结构的优选技术方案中,所述铰链安装板中部设置有槽状过孔。
10.在上述汽车后尾门区域车身结构的优选技术方案中,所述后挡风玻璃安装横梁设置有第二安装孔。
11.在上述汽车后尾门区域车身结构的优选技术方案中,所述铰链总成包括铰链本体和铰链支座,所述铰链支座固定在所述铰链本体的一端,所述铰链支座与所述铰链安装板总成固定连接。
12.在上述汽车后尾门区域车身结构的优选技术方案中,所述侧围总成距离所述铰链本体的中心轴线最小距离为10mm。
13.在上述汽车后尾门区域车身结构的优选技术方案中,所述后挡风玻璃安装横梁、衣帽架总成、侧围总成、后排座椅安装横梁分别设置有空腔结构,并依次固定连接形成空腔环形结构。
14.本领域人员能够理解的是,在本实用新型的技术方案中,一种汽车后尾门区域车身结构,包括侧围总成、后挡风玻璃安装横梁、后排座椅安装横梁、铰链总成、铰链安装板总成,侧围总成两侧与后挡风玻璃安装横梁、后排座椅安装横梁依次固定成环形结构,铰链安装板总成设置在环形结构内,并且铰链安装板总成与侧围总成、后挡风玻璃安装横梁均固定连接,铰链总成与铰链安装板总成固定连接。
15.通过上述设置方式,本实用新型的汽车后尾门区域车身结构包括依次固定连接成环形的侧围总成、后挡风玻璃安装横梁、后排座椅安装横梁,铰链安装板总成设置在环形结构内,并且与侧围总成、后挡风玻璃安装横梁均固定连接。通过侧围总成、后挡风玻璃安装横梁、后排座椅安装横梁固定连接后形成的环形结构,提高了该区域整体的结构强度,使侧围总成、后挡风玻璃安装横梁、后排座椅安装横梁提升了自身的强度。铰链总成与铰链安装板总成固定连接,使设置在环形内的铰链总成获得更高的支撑强度,相较于将铰链总成单独设置在单薄的衣帽架上的结构,本结构为铰链安装提供了较好的结构支撑,大大降低了铰链多次使用后变形的风险,解决了变形后尾门和车身配合不均,易导致关门力变大,后尾门区域漏水,行驶中异响等常见问题。使铰链不需要额外的加强,保证了铰链的属性和功能的要求,又达到了减重降本的目的。避免了传统车型设计在衣帽架总成上,多次累积公差,有利于后尾门的装配以及和车身之间的间隙公差配合调整,同时车身上的环形结构,帮助车身整体提升弯曲刚度和扭转刚度,有利于车辆的操控性和nvh。铰链安装区域的强度和刚度都有提升,相应的可减小铰链的尺寸,并且安装位置更靠近车身结构两侧的侧围,相应的增大了行李箱的门洞尺寸,门洞尺寸增大有利于乘客视野,铰链外移,防止铰链弯管占用行李箱空间,扩大了行李箱容积。
附图说明
16.下面参照附图来描述本汽车后尾门区域车身结构。附图中:
17.图1为本实用新型的汽车后尾门区域车身结构的侧围总成、后挡风玻璃安装横梁、铰链安装板总成的连接结构图;
18.图2为本实用新型的汽车后尾门区域车身结构的铰链安装板总成的结构示意图;
19.图3为本实用新型的汽车后尾门区域车身结构的铰链总成的安装结构示意图;
20.图4为本实用新型的汽车后尾门区域车身结构的铰链总成的位置示意图。
21.附图标记列表:
22.1-侧围总成,2-后挡风玻璃安装横梁,21-第二安装孔,3-后排座椅安装横梁,4-铰链安装板总成,42-铰链安装板,41-铰链安装加强板,421-第一安装孔,422-槽状过孔,5-铰链总成,51-铰链本体,52-铰链支座,6-衣帽架总成。
具体实施方式
23.下面参照附图来描述本实用新型的优选实施方式。本领域技术人员应当理解的是,这些实施方式仅仅用于解释本实用新型的技术原理,并非旨在限制本实用新型的保护范围。本领域技术人员可以根据需要对其作出调整,以便适应具体的应用场合。例如,尽管说明书中铰链安装板42是以板状结构进行描述的,但是,本实用新型的铰链安装板42显然并不局限于板状结构,也可以是支架、底座或者也可以是铰链总成5周围的侧围总成1、后挡风玻璃安装横梁2等部件的一部分,只要能将铰链总成5固定在其上即可,这些都不偏离本实用新型的原理,因此都将落入本实用新型的保护范围之内。
24.需要说明的是,在本实用新型的描述中,术语“中心”、“上”、“下”、“左”、“右”、“竖直”、“水平”、“内”、“外”等指示的方向或位置关系的术语是基于附图所示的方向或位置关系,这仅仅是为了便于描述,而不是指示或暗示所述装置或元件必须具有特定的方位、以特定的方位构造和操作,因此不能理解为对本实用新型的限制。此外,术语“第一”、“第二”、“第三”仅用于描述目的,而不能理解为指示或暗示相对重要性。
25.此外,还需要说明的是,在本实用新型的描述中,除非另有明确的规定和限定,术语“安装”、“相连”、“连接”应做广义理解,例如,可以是固定连接,也可以是可拆卸连接,或一体地连接;可以是机械连接,也可以是电连接;可以是直接相连,也可以通过中间媒介间接相连,可以是两个元件内部的连通。对于本领域技术人员而言,可根据具体情况理解上述术语在本实用新型中的具体含义。
26.如图1、图3所示,为解决现有的解决现有的汽车尾门铰链安装位置强度较差,铰链占用行李箱空间较多的问题。本实用新型的汽车后尾门区域车身结构包括侧围总成1、后挡风玻璃安装横梁2、后排座椅安装横梁3、铰链总成5、铰链安装板总成4,侧围总成1两侧与后挡风玻璃安装横梁2、后排座椅安装横梁3依次固定成环形结构,铰链安装板总成4设置在环形结构内,并且铰链安装板总成4与侧围总成1、后挡风玻璃安装横梁2、后排座椅安装横梁3均固定连接,铰链总成5与铰链安装板总成4固定连接。
27.上述设置方式的优点在于:本实用新型的汽车后尾门区域车身结构包括依次固定连接成环形的侧围总成1、后挡风玻璃安装横梁2、后排座椅安装横梁3,铰链安装板总成4设置在环形结构内,并且与侧围总成1、后挡风玻璃安装横梁2均固定连接。通过侧围总成1两侧、后挡风玻璃安装横梁2、后排座椅安装横梁3固定连接后形成的环形结构,提高了该区域整体的结构强度,使侧围总成1、后挡风玻璃安装横梁2、后排座椅安装横梁3提升了自身的强度。铰链总成5与铰链安装板总成4固定连接,使设置在环形内的铰链总成5获得更高的支撑强度,相较于将铰链总成5单独设置在单薄的衣帽架上的结构,本结构为铰链安装提供了较好的结构支撑,大大降低了铰链多次使用后变形的风险,解决了变形后尾门和车身配合不均,易导致关门力变大,后尾门区域漏水,行驶中异响等常见问题。使铰链不需要额外的加强,保证了铰链的属性和功能的要求,又达到了减重降本的目的。避免了传统车型将铰链设计在衣帽架上,多次累积公差,有利于后尾门的装配以及和车身之间的间隙公差配合调
整,同时车身上的环形结构,帮助车身整体提升弯曲刚度和扭转刚度,有利于车辆的操控性和nvh。铰链安装区域的强度和刚度都有提升,相应的可减小铰链的尺寸,并且安装位置更靠近车身结构两侧的侧围,相应的增大了行李箱的门洞尺寸,门洞尺寸增大有利于乘客视野,铰链向车身两侧移动,防止铰链弯管占用行李箱空间,扩大了行李箱容积。nvh的含义为噪声、振动与声振粗糙度(noise、vibration、harshness)的英文缩写,用来衡量汽车的制造质量和舒适度。
28.如图3所示,在一种可能的实施方式中,汽车后尾门区域车身结构包括衣帽架总成6,衣帽架总成6设置在环形结构内,衣帽架总成6与后挡风玻璃安装横梁2、铰链安装板总成4、后排座椅安装横梁3依次固定连接。
29.上述设置方式的优点在于:后排座椅安装横梁3与侧围总成1两侧焊接,同时后挡风玻璃安装横梁2与侧围总成1两侧焊接,使得三者之间形成环形结构,增强了整体结构的刚度,衣帽架总成6设置在环形结构内,衣帽架总成6与后挡风玻璃安装横梁2、铰链安装板总成4、后排座椅安装横梁3依次固定连接,使衣帽架总成6的支撑强度更高,同时使铰链安装板总成4通过与衣帽架总成6焊接,又进一步增强了铰链总成5安装位置的稳定性,同时又使车身整体的结构更稳定,提升了车身的整体扭转。
30.如图1、图3所示,在一种可能的实施方式中,铰链安装板总成4包括铰链安装板42,铰链安装板42与侧围总成1、后挡风玻璃安装横梁2均固定连接,铰链总成5固定连接在铰链安装板42上。铰链安装板42设置有两个第一安装孔421,铰链安装板42中部设置有槽状过孔422,后挡风玻璃安装横梁2设置有第二安装孔21。铰链总成5包括铰链本体51和铰链支座52,铰链支座52固定在所述铰链本体51的一端,铰链支座52与铰链安装板42固定连接。
31.上述设置方式的优点在于:后挡风玻璃安装横梁2上设置第二安装孔21,铰链支座52穿过槽状过孔,铰链支座52上设置的安装孔与铰链安装板42上设置的第一安装孔421、后挡风玻璃安装横梁2上设置的第二安装孔21通过螺栓螺母固定连接。铰链安装板42设置在侧围总成1、后挡风玻璃安装横梁2、后排座椅安装横梁3焊接形成的环形结构内,铰链安装板42与侧围总成1、后挡风玻璃安装横梁2、后排座椅安装横梁3分别焊接,使铰链安装板42的安装结构强度更高,铰链安装板42上设置的第一安装孔421与后挡风玻璃安装横梁2上设置的第二安装孔21同时与铰链支座52固定连接的结构,增加了安装点的强度,同时铰链安装板42与侧围总成1通过设计z向滑贴面,保证焊接时z向可调,在焊接过程中可通过夹具调节定位铰链z向装配位置,保证了车尾门和车身之间的匹配,有利于关门力和防水。
32.铰链安装板42的两个安装点在车身上均设计为过孔,相较于传统车型直接提供螺母孔的装配方案,给予了装配时铰链总成5在x向和y向的调整空间。铰链安装板42与后挡风玻璃安装横梁2上设置的安装孔形成的三点安装结构相较于现有的铰链安装板的四点安装结构节约了材料成本,在满足铰链总成5的强度的同时,减小了铰链安装板42的面积,节省了安装空间,减重降本的同时,使铰链安装板42更靠近侧围总成1,进而使铰链总成5更靠近侧围总成1,从而使铰链总成5在行李箱的位置更靠近车体两侧,使铰链总成占用的行李箱的可用空间减少,相应的增大了行李箱的容量。
33.如图2所示,在一种可能的实施方式中,铰链安装板总成4包括铰链安装加强板41,铰链安装板42下方固定连接铰链安装加强板41,铰链安装加强板41分别与侧围总成1、后挡风玻璃安装横梁2固定连接。
34.上述设置方式的优点在于:铰链安装板42下方焊接有铰链安装加强板41,铰链安装加强板41与侧围总成1、后挡风玻璃安装横梁2焊接,使铰链安装板42的强度进一步增大,增强铰链安装板总成4的安装位置的支撑强度。
35.在一种可能的实施方式中,后挡风玻璃安装横梁2、衣帽架总成6、侧围总成1、后排座椅安装横梁3分别设置有空腔结构,并依次固定连接成空腔环形结构。
36.上述设置方式的优点在于:在后挡风玻璃安装横梁2、衣帽架总成、侧围总成1上分别设置空腔结构,各部件固定连接形成空腔环形的结构,增强各部件的刚度,也进一步增强了铰链安装位置的强度,同时环状结构和车身主传力路径进行了串联,有利于车身整体的刚度和模态,提高车辆整体的稳定性。
37.如图4所示,在一种可能的实施方式中,侧围总成1距离铰链本体51的中心轴线最小距离为10mm。
38.上述设置方式的优点在于:通过加强铰链总成5安装位置的强度,从而使铰链安装板42的面积减小,使得铰链总成5可以尽可能的靠近侧围总成1,从而使铰链总成5距离侧围总成1的距离比现有的距离更小,本方案使得铰链本体51的中心轴线距离侧围总成1的最小距离为10mm,从而通过铰链总成5向两侧靠拢,使行李箱的开口可以更大,从而使行李箱的容量得到了大大的提升,提升用户的使用体验,同时在不改变车身整体的尺寸的情况下,通过缩小铰链总成5的体积,减重降本的同时,使行李箱的容量得到了提升,并且有利于用户对行李箱的可视性。
39.综上所述,本方案的汽车后尾门区域车身结构通过将侧围总成1、后挡风玻璃安装横梁2、后排座椅安装横梁3固定连接成环形结构,使得整体结构的刚度得到加强,将铰链安装板总成4安装在环形结构内,使铰链总成5的安装位置的强度大大提高。进一步的铰链总成5安装在铰链安装板42上,通过铰链安装板42与侧围总成1、后挡风玻璃安装横梁2、后排座椅安装横梁3固定连接,使得铰链安装板42的整体支撑强度增大,从而相应的缩小铰链安装板42的面积,从而使铰链总成5可以尽可能的靠近侧围总成1,从而使行李箱内铰链本体51的位置更靠两侧,从而可将行李箱的开口增大,从而加大行李箱的容量。通过增强铰链安装板42的强度,在满足铰链总成的各项功能和属性要求情况下,使铰链的四点安装结构简化成三点安装,使铰链的安装更便捷,成本更低,更容易避开安装受限的区域。衣帽架总成6与后挡风玻璃安装横梁2、铰链安装板总成4、后排座椅安装横梁3依次固定连接,又进一步的增强了铰链总成5安装区域的强度,并且在侧围总成1、后挡风玻璃安装横梁2、衣帽架总成6、后排座椅安装横梁3上设置空腔结构,并固定形成空腔环形结构,使整体的结构刚度增加,铰链总成5通过与铰链安装板42、铰链安装加强板41、后挡风玻璃安装横梁2多个部件的固定连接,使安装点的强度更大,从而使铰链的安装位置的结构更稳定,解决了现有的铰链安装位置强度差的问题。
40.需要说明的是,上述实施方式仅仅用来阐述本实用新型的原理,并非旨在与限制本实用新型的保护范围,在不偏离本实用新型原理的条件下,本领域技术人员能够对上述结构进行调整,以便本实用新型能够应用于更加具体的应用场景。
41.例如,在另一种可替换的实施方式中,铰链除了三点安装结构也可以是四点或者五点安装结构等,铰链安装板42可以通过螺接、铆接、卡接、胶粘、焊接等方式和车身其他部件固定,铰链安装板42的材质可以根据需求变换为铸造结构或辊压结构件,局部区域也可
依据具体需求采用结构膨胀胶进行局部增强,这些都不偏离本实用新型的原理,因此都将落入本实用新型的保护范围之内。
42.例如,在另一种可替换的实施方式中,铰链安装板42与后挡风玻璃安装横梁2设置第一安装孔421和第二安装孔21,用于铰链总成的安装,使铰链总成5的安装点具有两个部件强度的叠加,或者也可以通过在侧围总成1或者后排座椅安装横梁3等其他的部件上设置安装孔,用于铰链总成5的安装,只要能使铰链总成5的安装点的强度增加即可,这些都不偏离本实用新型的原理,因此都将落入本实用新型的保护范围之内。
43.例如,在另一种可替换的实施方式中,铰链安装板42中部设置的槽状过孔422用于铰链支座52穿过槽状过孔422,但不局限于槽状结构,随铰链支座52的结构变化而变化,也可以是圆形、三角形或者多边形等其他形状,这些都不偏离本实用新型的原理,因此都将落入本实用新型的保护范围之内。
44.例如,在另一种可替换的实施方式中,铰链总成5可以为鹅颈式铰链,也可以是琴式铰链或四连杆式铰链等。只要能将后尾门与车体连接在一起并实现后尾门的开合即可,这些都不偏离本实用新型的原理,因此都将落入本实用新型的保护范围之内。
45.最后需要说明的是,尽管本实用新型是以汽车为例进行描述的,但是本实用新型的汽车后尾门区域车身结构显然还可以应用于其他的设备。例如,火车、飞机等交通运输设备,还可以应用于其他各种需要铰链局部加强的设备或结构。
46.至此,已经结合附图所示的优选实施方式描述了本实用新型的技术方案,但是,本领域技术人员容易理解的是,本实用新型的保护范围显然不局限于这些具体实施方式。在不偏离本实用新型的原理的前提下,本领域技术人员可以对相关技术特征作出等同的更改或替换,这些更改或替换之后的技术方案都将落入本实用新型的保护范围之内。