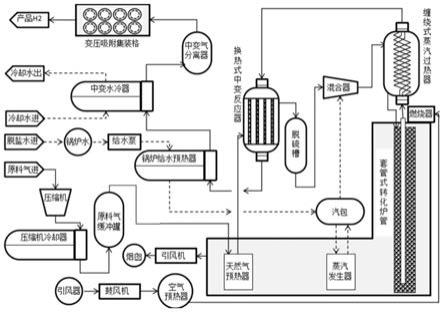
1.本发明属于气体净化与分离领域,用于制氢工艺中提纯氢气,具体涉及一种模块化天然气重整制氢机及其制氢的方法。
背景技术:
2.氢气是传统的生产原料,并作为冷却剂、还原剂等,得到大量的使用。化工上,天然气制氢的比例日渐增加,其规模较大,多在1000~20000m3/h的范围。随绿色能源的战略提出,零排放的氢气日益得到全球国家的重视。我国能源局日前发布的《中华人民共和国能源法(征求意见稿)》在能源术语中正式列入氢能,当前氢能的主要范围是氢燃料电池,加氢站作为燃料电池汽车的燃料补给站,是燃料电池汽车实现商业化的关键因素之一,其建设是发展重点,并使氢的需求呈现分布式发展的趋势。据市场反馈,加氢站适宜的需求量500~1000kg/d(200~500nm3/h左右)。
3.目前,加氢站的氢气来源在国内主要依靠运输,高压长管拖车储运氢气是行业主流。“用氢地区不产氢,氢气储运成本又居高不下,氢气储运正是当前制约我国氢能发展
‘
卡脖子’的地方。”而管道运输方面,因初始投资较大,当前国内相关标准体系尚不完善,管道环焊缝临氢环境下的安全技术问题仍在研究之中,氢气管道运输尚未规模化发展。
4.天然气重整制氢面临小型化的趋势,鉴于此,本技术提供一种模块化天然气重整制氢机及其制氢的方法。
技术实现要素:
5.本发明的目的在于:针对上述现象小规模需氢需要采用高压长管拖车储运氢气,导致的氢气储运成本居高不下的问题,本发明提供一种模块化天然气重整制氢机及其制氢的方法,缩小工程装置体积,降低工程占地面积,将天然气制氢装置高度集成模块化,专门针对加氢站配套提供氢源。
6.本发明采用的技术方案如下:
7.一种模块化天然气重整制氢机,包括依次设置的配料模块、造气模块、净化模块,所述配料模块包括套管式转化炉,脱硫槽,换热式中变换反应器,缠绕式蒸汽过热器,锅炉给水预热器,中变水冷器,及中变气分离器;所述套管式转化炉的对流段内由高温段至低温段设置有蒸汽发生器和天然气预热盘管;天然气预热盘管的出口通过管道和换热式中变换反应器的进口连通,换热式中变换反应器的顶部出口通过管道与脱硫槽连通,脱硫槽通过管道与混合器连通,混合器通过管道与缠绕式蒸汽过热器的顶部进口连通,缠绕式蒸汽过热器底部出口依次通过上集气总管及上猪尾管与套管式转化炉的进口连通;套管式转化炉的出口通过管道与缠绕式蒸汽过热器的底部进口连通,缠绕式蒸汽过热器顶部出口与换热式中变换反应器的顶部进口连通,换热式中变换反应器的底部出口与锅炉给水预热器连通,锅炉给水预热器通过管道与中变水冷器连通,中变水冷器通过管道与中变气分离器连通;蒸汽发生器的出口通过管道与汽包连通,汽包通过管道与混合器连通;蒸汽发生器的进
口通过管道与锅炉给水预热器连通;套管式转化炉上固定设置有加热装置。
8.优选地,所述加热装置包括固定设置在套管式转化炉上燃烧器,引风机与烟囱;燃烧器依次连接有空气预热器、鼓风机及引风机。
9.优选地,所述套管式转化炉上设置有放空管。
10.优选地,所述造气模块包括缓冲罐,压缩机,预脱硫器及锅炉;缓冲罐的出口与原料压缩机通过管道连通,原料压缩机通过管道与预脱硫器连通,预脱硫器通过管道与天然气预热盘管连通;锅炉连接有给水泵,给水泵的出水端与锅炉给水预热器连接;压缩机连接有压缩机冷却器。
11.优选地,所述净化模块包括变压吸附集装格,变压吸附集装格通过阀门与中变气分离器连接。
12.一种模块化天然气重整制氢机的制氢的方法,包括如下步骤:
13.步骤1:预热脱硫:天然气经压缩机升压后进入缓冲罐,经过流量调节器调量后进入套管式转化炉对流段的天然气预热盘管预热至200
±
5℃,再通过换热式中变换反应器换热到400
±
5℃进入脱硫槽,使天然气中的硫含量脱至0.1ppm以下;
14.步骤2:混合后再加热:工艺蒸汽与天然气按h2o/∑c=3.5
±
0.5混合得到混合气,混合气进入缠绕式蒸汽过热器与780
±
5℃的转化气换热,过热到590
±
5℃,经上集气总管及上猪尾管,进入套管式转化炉管中;
15.步骤3:转化炉催化转化:温度为780
±
5℃条件下,混合气在套管式转化炉管的催化剂层中,混合气反应生产co和h2,至残余甲烷含量为3.0
±
0.5%,得到转化气;
16.步骤4:一次降温:转化气出套管式转化炉,进入缠绕式蒸汽过热器与混合气换热,出缠绕式蒸汽过热器的转化气温度降至380
±
5℃;
17.步骤5:再催化转化:380
±
5℃的转化气进入换热式中变换反应器,将co与水蒸气转化为co2和氢气,得到变换气;
18.步骤6:二次降温:出换热式中变换反应器的变换气进入锅炉给水预热器,进一步降至150
±
5℃;
19.步骤7:三次降温:经中变水冷器后被冷却至40
±
5℃,进入中变气分离器分离出工艺冷凝液排出界外,中变气分离器出口的工艺气体压力为1.4mpa,送至变压吸附集装格;
20.步骤8:净化提纯:在经过变压吸附集装格进行净化,得到纯氢气。
21.优选地,燃烧器通过套管式转化炉通过天然气和来自变压吸附集装格的尾气提供热量。
22.优选地,所述工艺蒸汽通过蒸汽发生单元生成,所述蒸汽发生单元包括脱盐水、锅炉、给水泵、锅炉给水预热器、蒸汽发生器及汽包。
23.本发明的采用的套管式转化炉结构,在专利名称为一种套管式多程转化复合式制氢转化炉,专利号为2020228086606有详细说明,不再展开说明;本发明的采用的绕管式蒸汽发生器,在专利名称为一种用于小型天然气制氢转化的绕管式蒸汽发生器,专利号为2020228106065有详细说明,不再展开说明;本发明的采用的换热式变换反应器,在专利名称为一种转化气换热式变换反应器,专利号为2020228081119有详细说明,不再展开说明;本发明的采用的变压吸附集装格,在专利名称为一种用于变压吸附的集装格,专利号为2020229002716有详细说明,不再展开说明。
24.相较于现有技术,本发明的有益效果是:
25.(1)本发明通过采用配料模块、造气模块、净化模块,解决小规模需氢的难题,且实现能源的更好梯级应用,提高效率,即通过预热脱硫、混合后再加热、转化炉催化转化、一次降温、二次降温制氢的工艺步骤,采用转化气对原料气的工艺蒸汽生成及对天然气的加热,实现了转化气中热量的梯级应用。
26.(2)本发明在结合已获授权的四项针对传统天然气制氢集成化部件基础上,将配料模块、造气模块、净化模块中的各部件有机统合,再次有效缩小工程装置体积,降低工程占地面积,将传统天然气制氢装置高度集成模块化,专门针对为加氢站配套提供氢源,从而实现模块化制造、运输,到达现场后,经简单组装即可实现投产。
27.(3)本发明将蒸汽发生器高度集成在炉体内,有效降低了装置的体积及占地面积,从而降低了配套设备及管线投资,同时各个分模块可在装备车间组装,提高装备精度和速度。
附图说明
28.图1为本发明的模块化天然气制氢的流程示意图;
29.图2为本发明的传统的天然气制氢的流程示意图;
30.图3为本发明的造气模块侧视图;
31.图4为本发明的造气模块和净化模块侧视图;
32.图5为本发明的造气模块和净化模块顶视图。
33.图中标记为:1-套管式转化炉,2-脱硫槽,3-换热式中变换反应器,4-缠绕式蒸汽过热器,5-锅炉给水预热器,6-中变水冷器,7-中变气分离器,8-蒸汽发生器,9-天然气预热盘管,10-汽包,11-燃烧器,12-空气预热器,13-鼓风机,14-引风器,15-引风机,16-烟囱,17-放空管,18-缓冲罐,19-压缩机,20-预脱硫器,21-锅炉,22-给水泵,23-变压吸附集装格,24-阀门,25-压缩机冷却器。
具体实施方式
34.为了使本发明的目的、技术方案及优点更加清楚明白,对本发明进行进一步详细说明。应当理解,此处所描述的具体实施例仅用以解释本发明,并不用于限定本发明,即所描述的实施例仅是本发明一部分实施例,而不是全部的实施例。
35.实施例1
36.如图1及3-5所示,一种模块化天然气重整制氢机,包括依次设置的配料模块、造气模块、净化模块,所述配料模块包括套管式转化炉,脱硫槽,换热式中变换反应器,缠绕式蒸汽过热器,锅炉给水预热器,中变水冷器,及中变气分离器;所述套管式转化炉的对流段内由高温段至低温段设置有蒸汽发生器和天然气预热盘管;天然气预热盘管的出口通过管道和换热式中变换反应器的进口连通,换热式中变换反应器的顶部出口通过管道与脱硫槽连通,脱硫槽通过管道与混合器连通,混合器通过管道与缠绕式蒸汽过热器的顶部进口连通,缠绕式蒸汽过热器底部出口依次通过上集气总管及上猪尾管与套管式转化炉的进口连通;套管式转化炉的出口通过管道与缠绕式蒸汽过热器的底部进口连通,缠绕式蒸汽过热器顶部出口与换热式中变换反应器的顶部进口连通,换热式中变换反应器的底部出口与锅炉给
水预热器连通,锅炉给水预热器通过管道与中变水冷器连通,中变水冷器通过管道与中变气分离器连通;蒸汽发生器的出口通过管道与汽包连通,汽包通过管道与混合器连通;蒸汽发生器的进口通过管道与锅炉给水预热器连通;套管式转化炉上固定设置有加热装置。
37.其中,所述加热装置包括固定设置在套管式转化炉上燃烧器,引风机与烟囱;燃烧器依次连接有空气预热器、鼓风机及引风机。所述套管式转化炉上设置有放空管。
38.所述造气模块包括缓冲罐,压缩机,预脱硫器及锅炉;缓冲罐的出口与原料压缩机通过管道连通,原料压缩机通过管道与预脱硫器连通,预脱硫器通过管道与天然气预热盘管连通;锅炉连接有给水泵,给水泵的出水端与锅炉给水预热器连接;压缩机连接有压缩机冷却器。
39.所述净化模块包括变压吸附集装格,变压吸附集装格通过阀门与中变气分离器连接。
40.本发明在结合已获授权的四项针对传统天然气制氢集成化部件基础上,将配料模块、造气模块、净化模块中的各部件有机统合,再次有效缩小工程装置体积,降低工程占地面积,将传统天然气制氢装置高度集成模块化,专门针对为加氢站配套提供氢源,从而实现模块化制造、运输,到达现场后,经简单组装即可实现投产。
41.实施例2
42.本发明的一种模块化天然气重整制氢机的制氢的方法,如图1所示,包括如下步骤:
43.步骤1:预热脱硫:天然气经压缩机升压后进入缓冲罐,经过流量调节器调量后进入套管式转化炉对流段的天然气预热盘管预热至200℃,再通过换热式中变换反应器换热到400℃进入脱硫槽,使天然气中的硫含量脱至0.1ppm以下;
44.步骤2:混合后再加热:工艺蒸汽与天然气按h2o/∑c=3.5混合得到混合气,混合气进入缠绕式蒸汽过热器与780℃的转化气换热,过热到590℃,经上集气总管及上猪尾管,进入套管式转化炉管中;
45.步骤3:转化炉催化转化:温度为780℃条件下,混合气在套管式转化炉管的催化剂层中,混合气反应生产co和h2,至残余甲烷含量为3.0%,得到转化气;
46.步骤4:一次降温:转化气出套管式转化炉,进入缠绕式蒸汽过热器与混合气换热,出缠绕式蒸汽过热器的转化气温度降至380℃;
47.步骤5:再催化转化:380℃的转化气进入换热式中变换反应器,将co与水蒸气转化为co2和氢气,得到变换气;
48.步骤6:二次降温:出换热式中变换反应器的变换气进入锅炉给水预热器,进一步降至150℃;
49.步骤7:三次降温:经中变水冷器后被冷却至40℃,进入中变气分离器分离出工艺冷凝液排出界外,中变气分离器出口的工艺气体压力为1.4mpa,送至变压吸附集装格;
50.步骤8:净化提纯:在经过变压吸附集装格进行净化,得到纯氢气。
51.其中,燃烧器通过套管式转化炉通过天然气和来自变压吸附集装格的尾气提供热量。所述工艺蒸汽通过蒸汽发生单元生成,所述蒸汽发生单元包括脱盐水、锅炉、给水泵、锅炉给水预热器、蒸汽发生器及汽包。
52.空气预热采用成型空气预热器。
53.本发明通过采用配料模块、造气模块、净化模块,解决小规模需氢的难题,且实现能源的更好梯级应用,提高效率,即通过预热脱硫、混合后再加热、转化炉催化转化、一次降温、二次降温制氢的工艺步骤,采用转化气对原料气的工艺蒸汽生成及对天然气的加热,实现了转化气中热量的梯级应用。
54.实施例3
55.传统天然气典型流程为:如图2所示,天然气经压缩机升压后进入原料气缓冲罐,经过流量调节器调量后进入转化炉对流段的原料气预热盘管预热至400℃左右,进入脱硫槽,使原料气中的硫含量脱至0.1ppm以下。脱硫后的原料气与工艺蒸汽按h2o/∑c=3.5(进行自动比值调节)混合后进入混合气预热盘管,进一步预热到590℃,经上集气总管及上猪尾管,均匀地进入转化炉内转化管中,在催化剂层中,甲烷与水蒸汽反应生产co和h2。甲烷转化所需热量由顶部烧嘴燃烧燃料混合气提供。转化气出转化炉的温度约780℃,残余甲烷含量约3.0%(干基),进入余热锅炉的高温端管程。余热锅炉产生2.0mpa(g)的饱和蒸汽,出余热锅炉的转化气温度降至380℃,进入中变反应器,将co与水蒸气转化为co2和氢气。出中变反应器的转化气进入废热锅炉的低温端管程换热后,再进入锅炉给水预热器,进一步降至150℃,经中变水冷器后被冷却至40℃,进入中变气分离器分离出工艺冷凝液排出界外。中变气分离器出口的工艺气体压力约为1.4mpa(g),送至变压吸附装置。
56.为回收烟气热量,在转化炉对流段内设有六组换热盘管:(由高温段至低温段)
57.a、蒸汽-原料混合气预热盘管
58.b、天然气预热盘管ⅱ59.c、蒸汽过热器
60.d、烟气蒸汽发生器
61.e、天然气预热盘管ⅰ62.f、空气预热盘管
63.来自界区的脱盐水,送至加药装置和脱盐水缓冲罐,再由锅炉给水泵升压送至锅炉给水预热器预热至180℃后进入汽包,液相一部份经过转化炉对流段烟气蒸汽发生器与对流段的烟气进行换热,另一部份与转化气余热锅炉换热,换热采用自然循环,锅炉水部分被气化后再送至蒸汽分离器。将送至加药装置的脱盐水加入磷酸盐,由加药装置的往复泵送至锅炉给水泵出口管道上,以减少余热锅炉的结垢情况。热量回收后产生的蒸汽经过蒸汽过热器计量后与天然气按比例混合进入转化炉混合气预热器。
64.以上所述实施例仅表达了本技术的具体实施方式,其描述较为具体和详细,但并不能因此而理解为对本技术保护范围的限制。应当指出的是,对于本领域的普通技术人员来说,在不脱离本技术技术方案构思的前提下,还可以做出若干变形和改进,这些都属于本技术的保护范围。