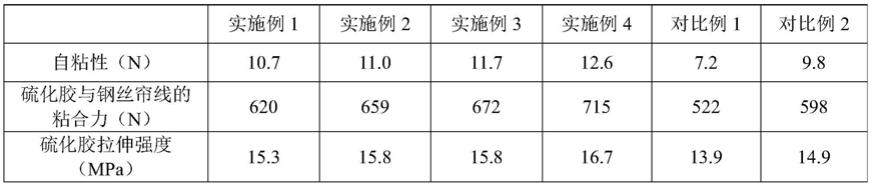
1.本发明涉及固废橡胶再生技术领域,尤其是涉及一种源于固废橡胶轮胎的返原橡胶的制备方法。
背景技术:
2.我国是全球最大的橡胶轮胎生产国与橡胶轮胎消耗大国,我国每年产生的固废橡胶轮胎超过4亿条,如果这些固废橡胶轮胎随意废弃,不仅造成资源的大量浪费,由于硫化橡胶在自然环境中极难降解分解,废弃的轮胎会造成严重的环境污染。因此,利用技术手段,循环利用固废橡胶轮胎与橡胶制品,对资源利用与碳中和具有十分重要的意义。
3.中国专利cn102977404a,公开了一种双螺杆挤出机连续制备再生胶的方法,该技术采用双螺杆挤出机高温、高剪切工作原理,连续脱硫生产再生橡胶,该发明利用传统的橡胶再生机理,即借助挤出机的机械剪切力和较高的温度,利用硫化胶粉中的多硫键“―s―s―”比碳-碳键“―c―c―”容易断裂的特性,将硫化橡胶中的双硫键或多硫键断开,实现硫化橡胶脱硫的一种方法,该发明在再生过程中,需额外加入软化剂与脱硫剂,同时,在最终产品分子结构中也没有引入功能化基团,其生产的再生胶性能不足,加上设备投入成本高,致推广应用受到影响。中国专利202010412712.x提出了一种低温等离子体脱硫再生废橡胶方法与装置,公开一种利用低温等离子体发生装置产生的等离子体对固废橡胶进行脱硫再生的技术,但该技术在产品稳定性方面与用户的期望值存在差距,难以实现工业化生产。
技术实现要素:
4.本发明是为了克服现有技术中的返原橡胶性能不足,不利于资源化利用的问题,提供一种源于固废橡胶轮胎的返原橡胶的制备方法,将复合改性剂中的功能性组分接枝到产物的分子链上,得到一种与通用橡胶相溶性佳、材料力学性能好、并具有良好化学与物理粘合力的返原橡胶。
5.为了实现上述目的,本发明采用以下技术方案:一种源于固废橡胶轮胎的返原橡胶的制备方法,包括如下步骤:(1)将固废橡胶轮胎粉碎得到固废橡胶粉;(2)去除固废橡胶粉中的杂质;(3)以重量份计,将100份固废橡胶粉与1~20份复合型官能化改性剂混合后搅拌均匀;(4)将搅拌均匀后的原料送入脱硫挤出机中挤出,初步冷却后得到粒状的脱硫橡胶;(5)将粒状的脱硫橡胶转入精炼挤出机中连续捏炼;(6)将捏炼后的橡胶进行压型出片,得到所述返原橡胶。
6.本发明的技术原理是基于:固废橡胶轮胎的硫化橡胶在高温及高机械剪切作用下,橡胶分子链上的—c—c—共价键会异裂,产生超高活性的正碳离子与负碳离子,利用此
超高活性的正碳离子与负碳离子无需催化剂就能接枝功能性基团的特性,将本发明的复合型官能化改性剂接枝到返原橡胶分子链上,从而提升返原橡胶与通用橡胶互溶性,使本发明的返原橡胶的使用性能更接近于通用橡胶,同时也提升返原橡胶的力学性能与工艺性能。
7.本发明利用挤出机工作时的机械剪切力产生的机械力化学作用及挤出机各加热区段高温产生的能量,使立体网状交联结构的硫化橡胶分子按预期的要求产生部分断裂,使立体网状交联结构的硫化橡胶返原为以线状结构为主的返原橡胶;同时,在高温及机械力的化学效应下,复合型官能化改性剂与返原橡胶发生化学反应,进而将功能型的活性基团接枝到返原橡胶分子链上,得到一种与通用橡胶相溶性佳、材料力学性能好、并具有良好化学与物理粘合力的返原橡胶。
8.作为优选,步骤(3)中所述的复合型官能化改性剂包括3-羟基环戊烯、己二烯酸、环辛二烯、双环戊二烯酸酯、c9~c22二烯酸中的二种或二种以上的复配物。
9.本发明的复合型官能化改性剂中包括含—c=c—及—cooh、—oh等官能团的化合物,—c=c—可以与固废橡胶粉裂解产生的—sh基发生点击反应,将复合型官能化改性剂接枝到产物的分子链上,从而使产物上带有—c=c—、—cooh、—oh等功能型基团,在各功能型基团的共同作用下,得到一种与通用橡胶相溶性佳、材料力学性能好、并具有良好化学与物理粘合力的返原橡胶。
10.作为优选,所述的复合型官能化改性剂还包括二苯基二硫化物、c12~c22多烯酸中的一种或两种。在复合型官能化改性剂中加入二苯基二硫化物及c12~c22多烯酸,可以催化—c=c—及—sh的反应,使功能型基团更易接枝在返原液体橡胶的分子链上,提升返原液体橡胶的性能。
11.作为优选,步骤(1)中所述的固废橡胶粉的粒径为10~80目。
12.作为优选,步骤(1)中所述的固废橡胶轮胎选自全钢载重轮胎、轿车轮胎、斜交载重轮胎及轻卡轮胎中的一种或多种。
13.作为优选,步骤(2)中用物理方法去除固废橡胶粉中的钢丝帘线、纤维帘线、金属杂质及无机杂质。
14.作为优选,步骤(3)中搅拌时先在50~150℃温度下高速搅拌5~20min,然后再在50~150℃温度下低速搅拌10~25min,高速搅拌的转速50~600转/分,低速搅拌的转速1~50转/分。
15.作为优选,步骤(4)中所述的脱硫挤出机为单螺杆、双螺杆或三螺杆挤出机;所述脱硫挤出机的加热区段不少于4区,各加热区段的温度分别控制为100~350℃;脱硫挤出机转速为10~120转/分。
16.作为优选,步骤(5)中的捏炼温度为100~165℃。
17.作为优选,制备过程中各装置上均设有vocs气体收集与处理装置。本发明在各装置上设置vocs气体收集与处理装置,可以避免返原橡胶制备过程中vocs挥发对环境造成的污染,实现了生产过程绿色环保的要求。
18.因此,本发明具有如下有益效果:利用复合型官能化改性剂分子中的双键与返原橡胶分子中的巯基发生点击化学反应,进而将功能型的活性基团接枝到返原橡胶分子链上,使其最终产物成为一种与通用橡胶相溶性佳、材料力学性能好、并具有良好化学与物理
粘合力的返原橡胶。
具体实施方式
19.下面结合、具体实施方式对本发明做进一步的描述。
20.在本发明中,若非特指,所有设备和原料均可从市场购得或是本行业常用的,下述实施例中的方法,如无特别说明,均为本领域常规方法。
21.总实施例:一种源于固废橡胶轮胎的返原橡胶的制备方法,包括如下步骤:(1)将固废橡胶轮胎粉碎至10~80目,得到固废橡胶粉;(2)用物理方法去除干净步骤(1)固废橡胶粉中的钢丝帘线、纤维帘线、金属杂质及无机杂质;(3)以重量份计,将100份固废橡胶粉与1~20份复合型官能化改性剂混合;所述的复合型官能化改性剂包括3-羟基环戊烯、己二烯酸、环辛二烯、双环戊二烯酸酯、c9~c22二烯酸中的二种或二种以上的复配物,还可能包括二苯基二硫化物、c12~c22多烯酸中的一种或两种;(4)将步骤(3)中的混合物料输送到高速搅拌器中,于50~150℃温度下,高速搅拌5~20min,高速搅拌器转速:50~600转/分;(5)将步骤(4)中的物料输送到储存鑵中,保持50~150℃温度,并低速搅拌10~25min,转速1~50转/分;(6)将步骤(5)储存罐内的物料连续不断地送入脱硫挤出机的进料口内挤出,得到高温状态的脱硫橡胶,脱硫挤出机各加热区段的温度分别控制为100~350℃;脱硫挤出机转速为5~100转/分;(7)将步骤(6)中挤出后的高温状态的脱硫橡胶在冷却机中初步冷却,得到粒状的脱硫橡胶;(8)将步骤(7)中的粒状的脱硫橡胶送入精炼挤出机中进行连续捏炼,捏炼温度为100~165℃;(9)将步骤(8)中捏炼后的橡胶送入挤出机中进行压型出片,得到返原橡胶;(10)将步骤(9)中出片后的返原橡胶送入冷却水水槽及挂链式冷却风干机中冷却,然后收皮、称量;(11)检测合格者入库,不合格者单独存放进行技术处理。
22.实施例1:一种源于固废橡胶轮胎的返原橡胶的制备方法,包括如下步骤:(1)将固废全钢载重子午线轮胎粉碎至20~60目,得到固废橡胶粉;(2)用物理方法去除干净步骤(1)固废橡胶粉中的钢丝帘线、纤维帘线、金属杂质及无机杂质;(3)以重量份计,将100份固废橡胶粉、3份己二烯酸、4份1,5-环辛二烯及1份二苯基二硫化物混合;(4)将步骤(3)中的混合物料输送到高速搅拌器中,于100℃温度下,高速搅拌25min,高速搅拌器转速:150转/分;
(5)将步骤(4)中的物料输送到储存鑵中,保持100℃温度,并低速搅拌25min,转速20转/分;(6)将步骤(5)储存罐内的物料连续不断地送入双螺杆脱硫挤出机的进料口内挤出,得到高温状态的脱硫橡胶;双螺杆脱硫挤出机9个加热区段的温度分别为100~150℃、150~200℃、200~250℃、250~300℃、250~300℃、250~300℃、250~300℃、200~250℃、150~200℃;双螺杆脱硫挤出机转速为80转/分;(7)将步骤(6)中挤出后的高温状态的脱硫橡胶转入至冷却机中初步冷却,得到粒状的脱硫橡胶;(8)将步骤(7)中的粒状的脱硫橡胶送入双螺杆精炼挤出机中进行连续捏炼,捏炼温度为100~165℃;(9)将步骤(8)中捏炼后的橡胶送入挤出机中进行压型出片,得到返原橡胶;(10)将步骤(9)中出片后的返原橡胶送入冷却水水槽及挂链式冷却风干机中冷却,然后收皮、称量;(11)检测合格者入库,不合格者单独存放进行技术处理。
23.实施例2:一种源于固废橡胶轮胎的返原橡胶的制备方法,包括如下步骤:(1)将固废轿车轮胎及全钢载重子午线轮胎粉碎至20~40目,得到固废橡胶粉;(2)用物理方法去除干净固废橡胶粉中的钢丝帘线、纤维帘线、金属杂质及无机杂质;(3)以重量份计,将100份固废橡胶粉、3份3-羟基环戊烯、3份己二烯酸、1份1,5环辛二烯及3份二十二碳二烯酸混合;(4)将步骤(3)中的混合物料输送到高速搅拌器中,于50℃温度下,高速搅拌15min,高速搅拌器转速:300转/分;(5)将步骤(4)中的物料输送到储存鑵中,保持50℃温度,并低速搅拌25min,转速50转/分;(6)将步骤(5)储存罐内的物料连续不断地送入双螺杆脱硫挤出机的进料口内挤出,得到高温状态的脱硫橡胶;双螺杆脱硫挤出机9个加热区段的温度分别为100~150℃、150~200℃、200~260℃、260~300℃、260~300℃、260~300℃、260~300℃、200~250℃、150~200℃;双螺杆脱硫挤出机转速为95转/分;(7)将步骤(6)中挤出后的高温状态的脱硫橡胶转入至冷却机中初步冷却,得到粒状的脱硫橡胶;(8)将步骤(7)中的粒状的脱硫橡胶送入双螺杆精炼挤出机中进行连续捏炼,捏炼温度为130~165℃;(9)将步骤(8)中捏炼后的橡胶送入挤出机中进行压型出片,得到返原橡胶;(10)将步骤(9)中出片后的返原橡胶送入冷却水水槽及挂链式冷却风干机中冷却,然后收皮、称量;(11)检测合格者入库,不合格者单独存放进行技术处理。
24.实施例3:一种源于固废橡胶轮胎的返原橡胶的制备方法,包括如下步骤:
(1)将固废全钢载重子午线轮胎粉碎至60目,得到固废橡胶粉;(2)用物理方法去除干净步骤(1)固废橡胶粉中的钢丝帘线、纤维帘线、金属杂质及无机杂质;(3)以重量份计,将100份固废橡胶粉、3份己二烯酸、3份环戊二烯酸及5份二十二碳六烯酸混合;(4)将步骤(3)中的混合物料输送到高速搅拌器中,于120℃温度下,高速搅拌20min,高速搅拌器转速:200转/分;(5)将步骤(4)中的物料输送到储存鑵中,保持120℃温度,并低速搅拌25min,转速50转/分;(6)将步骤(5)储存罐内的物料连续不断地送入双螺杆脱硫挤出机的进料口内挤出,得到高温状态的脱硫橡胶;双螺杆脱硫挤出机9个加热区段的温度分别为120~160℃、160~220℃、220~250℃、250~300℃、250~300℃、250~300℃、250~300℃、200~250℃、150~200℃;双螺杆脱硫挤出机转速为100转/分;(7)将步骤(6)中挤出后的高温状态的脱硫橡胶转入至冷却机中初步冷却,得到粒状的脱硫橡胶;(8)将步骤(7)中的粒状的脱硫橡胶送入双螺杆精炼挤出机中进行连续捏炼,捏炼温度为130~165℃;(9)将步骤(8)中捏炼后的橡胶送入挤出机中进行压型出片,得到返原橡胶;(10)将步骤(9)中出片后的返原橡胶送入冷却水水槽及挂链式冷却风干机中冷却,然后收皮、称量;(11)检测合格者入库,不合格者单独存放进行技术处理。
25.实施例4:一种源于固废橡胶轮胎的返原橡胶的制备方法,包括如下步骤:(1)将固废全钢载重子午线轮胎粉碎至20~60目,得到固废橡胶粉;(2)用物理方法去除干净步骤(1)固废橡胶粉中的钢丝帘线、纤维帘线、金属杂质及无机杂质;(3)以重量份计,将100份固废橡胶粉、5份己二烯酸、5份环戊二烯酸及5份二十二碳六烯酸混合;(4)将步骤(3)中的混合物料输送到高速搅拌器中,于100℃温度下,高速搅拌25min,高速搅拌器转速:150转/分;(5)将步骤(4)中的物料输送到储存鑵中,保持100℃温度,并低速搅拌25min,转速20转/分;(6)将步骤(5)储存罐内的物料连续不断地送入双螺杆脱硫挤出机的进料口内挤出,得到高温状态的脱硫橡胶;双螺杆脱硫挤出机9个加热区段的温度分别为100~150℃、150~200℃、200~250℃、250~300℃、250~300℃、250~300℃、250~300℃、200~250℃、150~200℃;双螺杆脱硫挤出机转速为80转/分;(7)将步骤(6)中挤出后的高温状态的脱硫橡胶转入至冷却机中初步冷却,得到粒状的脱硫橡胶;(8)将步骤(7)中的粒状的脱硫橡胶送入双螺杆精炼挤出机中进行连续捏炼,捏炼
温度为100~165℃;(9)将步骤(8)中捏炼后的橡胶送入挤出机中进行压型出片,得到返原橡胶;(10)将步骤(9)中出片后的返原橡胶送入冷却水水槽及挂链式冷却风干机中冷却,然后收皮、称量;(11)检测合格者入库,不合格者单独存放进行技术处理。
26.对比例1:一种源于固废橡胶轮胎的返原橡胶的制备方法,包括如下步骤:(1)将固废全钢载重子午线轮胎粉碎至20~60目,得到固废橡胶粉;(2)用物理方法去除干净步骤(1)固废橡胶粉中的钢丝帘线、纤维帘线、金属杂质及无机杂质;(3)以重量份计,将100份固废橡胶粉及15份妥尔油混合;(4)将步骤(3)中的混合物料输送到高速搅拌器中,于100℃温度下,高速搅拌25min,高速搅拌器转速:150转/分;(5)将步骤(4)中的物料输送到储存鑵中,保持100℃温度,并低速搅拌25min,转速20转/分;(6)将步骤(5)储存罐内的物料连续不断地送入双螺杆脱硫挤出机的进料口内挤出,得到高温状态的脱硫橡胶;双螺杆脱硫挤出机9个加热区段的温度分别为100~150℃、150~200℃、200~250℃、250~300℃、250~300℃、250~300℃、250~300℃、200~250℃、150~200℃;双螺杆脱硫挤出机转速为80转/分;(7)将步骤(6)中挤出后的高温状态的脱硫橡胶转入至冷却机中初步冷却,得到粒状的脱硫橡胶;(8)将步骤(7)中的粒状的脱硫橡胶送入双螺杆精炼挤出机中进行连续捏炼,捏炼温度为100~165℃;(9)将步骤(8)中捏炼后的橡胶送入挤出机中进行压型出片,得到返原橡胶;(10)将步骤(9)中出片后的返原橡胶送入冷却水水槽及挂链式冷却风干机中冷却,然后收皮、称量;(11)检测合格者入库,不合格者单独存放进行技术处理。
27.对比例2:一种源于固废橡胶轮胎的返原橡胶的制备方法,包括如下步骤:(1)将固废全钢载重子午线轮胎粉碎至20~60目,得到固废橡胶粉;(2)用物理方法去除干净步骤(1)固废橡胶粉中的钢丝帘线、纤维帘线、金属杂质及无机杂质;(3)以重量份计,将100份固废橡胶粉、10份1,5-环辛二烯及1份二苯基二硫化物混合;(4)将步骤(3)中的混合物料输送到高速搅拌器中,于100℃温度下,高速搅拌25min,高速搅拌器转速:150转/分;(5)将步骤(4)中的物料输送到储存鑵中,保持100℃温度,并低速搅拌25min,转速20转/分;(6)将步骤(5)储存罐内的物料连续不断地送入双螺杆脱硫挤出机的进料口内挤
出,得到高温状态的脱硫橡胶;双螺杆脱硫挤出机9个加热区段的温度分别为100~150℃、150~200℃、200~250℃、250~300℃、250~300℃、250~300℃、250~300℃、200~250℃、150~200℃;双螺杆脱硫挤出机转速为80转/分;(7)将步骤(6)中挤出后的高温状态的脱硫橡胶转入至冷却机中初步冷却,得到粒状的脱硫橡胶;(8)将步骤(7)中的粒状的脱硫橡胶送入双螺杆精炼挤出机中进行连续捏炼,捏炼温度为100~165℃;(9)将步骤(8)中捏炼后的橡胶送入挤出机中进行压型出片,得到返原橡胶;(10)将步骤(9)中出片后的返原橡胶送入冷却水水槽及挂链式冷却风干机中冷却,然后收皮、称量;(11)检测合格者入库,不合格者单独存放进行技术处理。
28.在轮胎胎体配方中,将上述实施例和对比例中的返原橡胶与天然橡胶按质量比1:2比例混合进行混炼,对混炼后的橡胶的性能进行测试,结果如表1中所示。
29.表1:混炼橡胶的性能测试结果。
30.从表1中可以看出,实施例1~4中采用本发明中的方法制得的返原橡胶与天然橡胶混炼后具有良好的自粘性和化学粘合性能,随着复合改性剂用量的增加,混炼胶的自粘性与化学粘合力均有相对应的提高。对比例1中的返原橡胶在加工过程中不添加复合型官能化改性剂,制得的返原橡胶的粘合性及与橡胶基体的相容性不佳,导致最终制得的橡胶制品的自粘性与化学粘合力与实施例1中相比显著下降;对比例2中的复合型官能化改性剂中仅采用1,5-环辛二烯,不与己二烯酸进行复配,返原液体橡胶的分子链中不引入-cooh,导致其与天然橡胶基体的相容性下降,与实施例相比较,混炼胶的自粘性与硫化胶的化学粘合力有一定程度的下降。